-
Global
-
Africa
-
Asia Pacific
-
Europe
-
Latin America
-
Middle East
-
North America
- |
- Partners
- |
-
Currency:Localize your Content
You can set your preferred currency for this account.
Choose a Currency
Currency- CHOOSE YOUR CURRENCY
Update Currency
Changing Currency will cause your current cart to be deleted. Click OK to proceed.
To Keep your current cart, click CLOSE and then save your cart before changing currency.
-
Select Account
Switching accounts will update the product catalog available to you. When switching accounts, your current cart will not move to the new account you select. Your current cart will be available if you log back into this account again.
Account# Account Name City Zip/Post Code CANCELPROCEEDMy Account
-
Support
- View All Productivity Solutions
- Warranties
- Patents
- Global Locations
- Technical Support
- Discontinued Products
- Quality Program and Environmental Compliance
- Return Material Authorization (RMA)
- Legal Documents
- Product Certification
- Software Downloads
- Cyber Security Notifications
- Case Studies and Success Stories
- View All Sensing Solutions
- Sales Contact Form
- Technical Support
- Certificates
- eCOM Portal
- Distributor Inventory
- Return Material Authorization (Test & Measurement)
- Return Material Authorization (Citytech)
- Return Material Authorization (EnviteC)
- Legal Documents
- Intelligent Life Care
- Return Material Authorization (ILC)
-
Global
-
Africa
-
Asia Pacific
-
Europe
-
Latin America
-
Middle East
-
North America
- |
- Partners
- |
You are browsing the product catalog for
You are viewing the overview and resources for
- News & Events
- Featured stories
- Planning for Production Changes With Automated Palletizer Systems
Planning for Production Changes With Automated Palletizer Systems
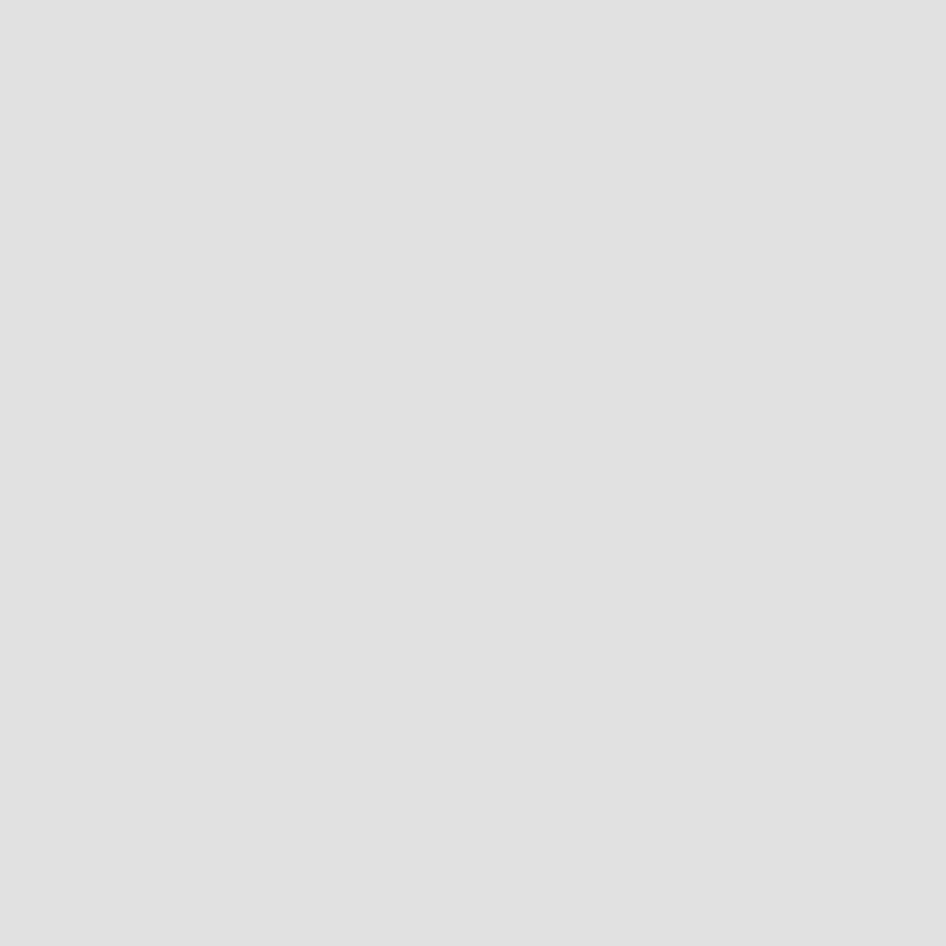
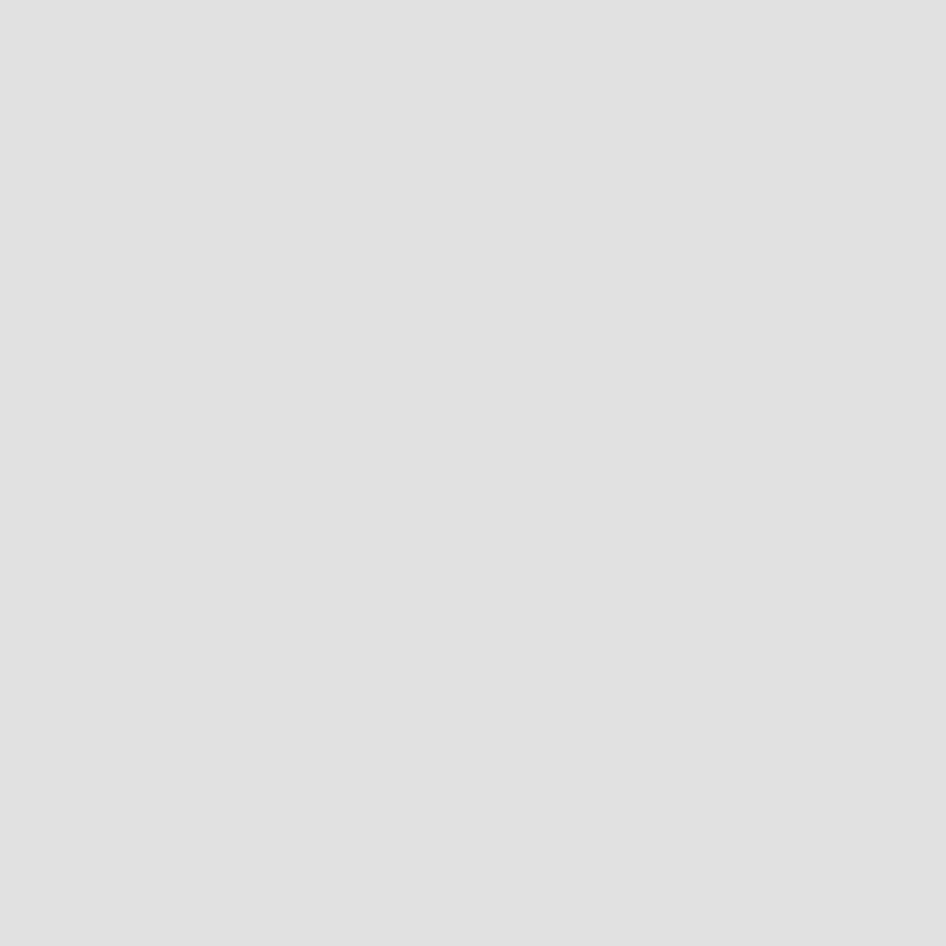
Planning for Production Changes With Automated Palletizer Systems
Matt Wicks
November 4, 2019
Manual palletizing is one of the most challenging tasks in manufacturing and distribution operations. It’s physically demanding, requiring long hours of bending, lifting and twisting. Injuries and high turnover rates are common. When coupled with other labor challenges like a declining availability of qualified workers and the rise in minimum wage expectations, you can see how staffing end-of-line processes like palletizing has become a serious challenge for many operators.
If this is happening in your operation, you may be thinking about incorporating an automated palletizer. When looking toward automated system design, embracing the idea of future changes can be a critical component in equipment selection and overall system design.
Evaluate your current palletizing needs
When considering making the switch from manual to automated palletizing, planning for future changes is a strategic advantage. Working with a system provider to incorporate versatility into your design will help maximize long-term viability and return on investment.
A system design should consider the number of SKUs that will need to run immediately, and at what rate and in which pattern those SKUs will need to move through the system. A good system design doesn’t only look at how many cases a system will run; it looks at each SKU individually. This will provide a clear picture of how the machine will perform your specific needs.
Once you plan for your current production rate, considering future needs for flexibility is also extremely important. Some things to consider include production rate increases, consumer demands, packaging changes and possible fluctuation of product size.
A look at current automated palletizer technologies
Modern automatic palletizing systems are dynamic and flexible, with the ability to handle many SKUs. System providers like Honeywell Intelligrated strive to supply user-friendly, flexible pattern utilities, so you can adapt and change based on your production demands. Each company is different when it comes to system changes; some adjust production runs once a day and others adjust only once a month. A user-friendly system limits downtime and the need for support calls when changes are required.
Today’s palletizing systems have the capability to detect the type of product running through the system and change tuning parameters on the fly when that product changes upstream. This can be an important time saver in operations with a large product mix.
Several of Honeywell Intelligrated’s palletizers are valued for their superior package handling capability as well as their pattern-forming flexibility and reliability. In these palletizing systems, pattern utility software enables quick case pattern creation from an intuitive touch-screen interface, which also provides advanced diagnostics.
Making the switch from manual to automated palletizing is a big decision with various important factors. Having a robust, versatile system can be a great benefit to your business. Download our brochure to learn more about your options for automated palletizing.
To subscribe to our blog and receive exclusive communications and updates from Honeywell Intelligrated, click here.
Let's Connect!
Sign up to receive exclusive communications from Honeywell including product updates, technical information, new offerings, events and news, surveys, special offers, and related topics via telephone, email, and other forms of electronic communication.
Copyright © 2025 Honeywell International Inc
Maximum File Size
Maximum Files Exceeded
Due to inactivity you will be logged out in 000 seconds.
Maximum File Size
Maximum Files Exceeded
You cannot access this page as this product is not available in your country.