-
Global
-
Africa
-
Asia Pacific
-
Europe
-
Latin America
-
Middle East
-
North America
- |
- Partners
- |
-
Currency:Localize your Content
You can set your preferred currency for this account.
Choose a Currency
Currency- CHOOSE YOUR CURRENCY
Update Currency
Changing Currency will cause your current cart to be deleted. Click OK to proceed.
To Keep your current cart, click CLOSE and then save your cart before changing currency.
-
Select Account
Switching accounts will update the product catalog available to you. When switching accounts, your current cart will not move to the new account you select. Your current cart will be available if you log back into this account again.
Account# Account Name City Zip/Post Code CANCELPROCEEDMy Account
-
Support
- View All Productivity Solutions
- Warranties
- Patents
- Global Locations
- Technical Support
- Discontinued Products
- Quality Program and Environmental Compliance
- Return Material Authorization (RMA)
- Legal Documents
- Product Certification
- Software Downloads
- Cyber Security Notifications
- Case Studies and Success Stories
- View All Sensing Solutions
- Sales Contact Form
- Technical Support
- Certificates
- eCOM Portal
- Distributor Inventory
- Return Material Authorization (Test & Measurement)
- Return Material Authorization (Citytech)
- Return Material Authorization (EnviteC)
- Legal Documents
- Intelligent Life Care
- Return Material Authorization (ILC)
-
Global
-
Africa
-
Asia Pacific
-
Europe
-
Latin America
-
Middle East
-
North America
- |
- Partners
- |
You are browsing the product catalog for
You are viewing the overview and resources for
- Services
- Warehouse Automation
- Engineering Services
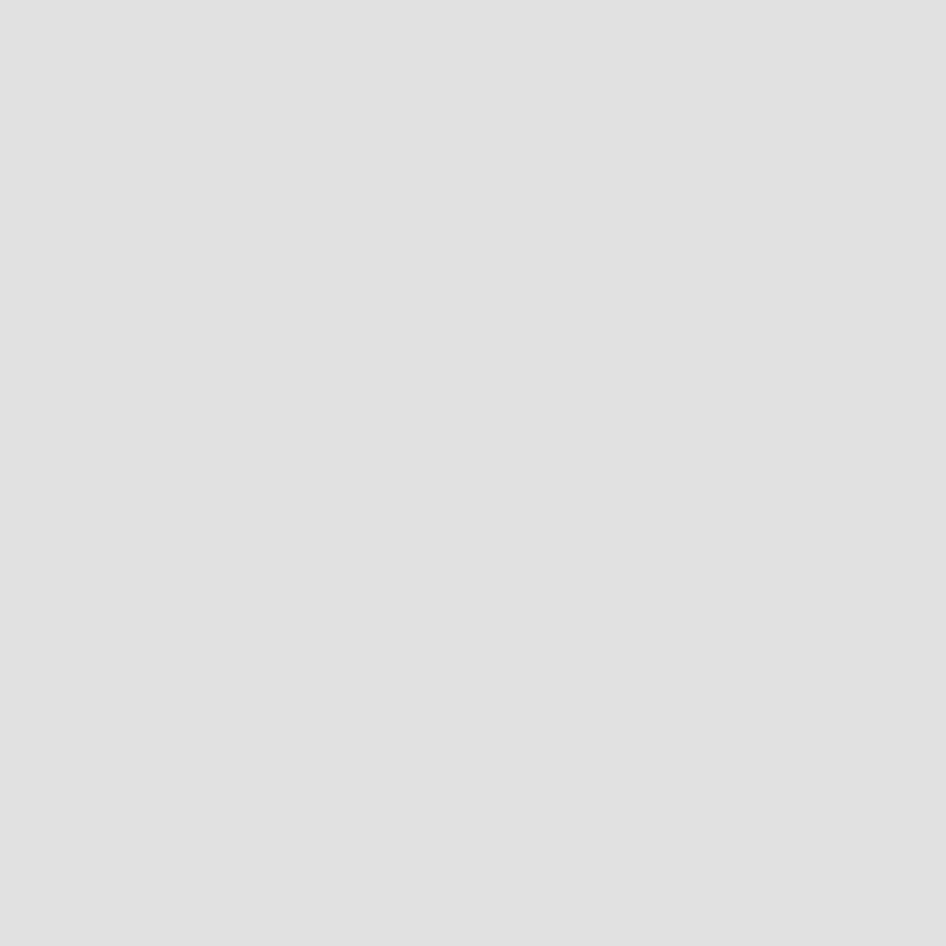
ENGINEERING SERVICES
Custom Warehouse System Layout and Design That Meets Your Operation's Needs
In a world where no two fulfillment operations are alike, standard solutions can’t always address the most challenging or unique business requirements. That’s why we offer Engineered Solutions: a team of material handling, software and control engineers dedicated to creating custom solutions for your biggest challenges.
Engineered Solutions allows you to put the industry’s most experienced and knowledgeable experts to work on your specific fulfillment problem, scenario or upgrade — before you make a big investment in equipment or technology.
Whether you’re trying to meet peak season demand levels, adapt to new product profiles, achieve new levels of overall equipment effectiveness, or meet changing customer requirements, Engineered Solutions provides a wide range of professional services to help you streamline the change management process. This multidisciplinary approach offers you an efficient resource for assessing your business requirements and developing custom, cost-effective solutions to increase the effectiveness of your fulfillment operations.
Maintain Best Practices While Minimizing Downtime
Maintaining the uptime of material handling equipment (MHE) is critical to your operational success, especially when you consider that most downtime is preventable. Audits and assessments can maximize the efficiency of your operation, while identifying asset, maintenance and functional opportunities.
The Honeywell Intelligrated Lifecycle Support Services (LSS) team provides levels of experience and expertise unmatched by any third-party provider. They have a deeper understanding of your system’s design, maintenance and requirements that only an original equipment manufacturer (OEM) can provide, plus robust data to back their claims and recommendations. In addition, all LSS auditors and assessors are subject matter experts (SMEs) who either maintain, have maintained, or have led a technical team in support of real-world operations like yours.
Audits
LSS audits provide you with expert consultation designed to identify process gaps and improve your operation. Whether you’re trying to identify unknown factors that are causing unscheduled downtime, struggling to meet maintenance schedules or key performance indicators (KPIs), or looking for strategies to improve performance, each audit is custom-tailored to meet your specific objectives.
Depending on your operation’s unique needs, LSS audits offer a variety of options. This variable scope can include any combination of the following:
- Uptime, parcel count, preventive maintenance scheduling, parts usage, and other KPIs
- Internal information systems (IRIS, iCampus, Dashboard)
- Technician proficiency and compliance to processes
- Maintenance shop layout and 5S standards
- Timekeeping and general administrative tasks
- Root cause analysis (RCA) and lessons learned tracking
- New technology implementation
Preventive Maintenance Audits
Preventive maintenance audits evaluate your maintenance standards, practices and systems to ensure that those systems are getting the maintenance they need to function at optimum capacity.
Technician Proficiency Audits
Technician proficiency audits assess the aptitude of your technicians to learn how efficiently they’re performing, identify potential expertise gaps, and recommend opportunities for skill improvement.
Field Maintenance Audits
Field maintenance audits provide a general overview of your equipment and maintenance practices.
Assessments
LSS assessments can help your organization to prevent issues and preserve system uptime by proactively evaluating overall system performance and health risks. An expert assessment team deploys a proven, field-tested approach to gauge operational performance and conditions against established benchmarks.
Every assessment includes the following services and deliverables:
- Expert evaluation of major components and an overview report prior to leaving site
- Follow-up, detailed report with a summary of findings, risk level for each major component, and recommendations for improvement
- Inspection certificate containing photos and measurement data (when applicable)
- Recommendations for upgrades or product enhancements
- Parts quote for replacement components
- Discussions to ensure clear understanding of findings and recommendations
Reliability Assessments
Reliability assessments evaluate your equipment’s operational condition and functionality levels. You’ll get a detailed inspection of critical components, plus root cause analysis (RCA) and prioritization of maintenance actions or part replacements. The LSS team will also recommend engineered solutions, if needed, to bring equipment back to designed operating standards or reduce the risk of unplanned downtime.
Optimization Assessments
Optimization assessments review the effectiveness of maintenance programs and seek to optimize operator interactions with MHE. You’ll get recommendations for best-in-class asset management, with a focus on increasing throughput.
Audit or Assessment: Which Is Right for You?
Although LSS audits and assessments provide resources to identify opportunities, mitigate risks, and help your facility to run more effectively, each offering focuses on different aspects of your operation.
Audit
- Consultation to identify process gaps
- Reviews performance of people or processes
- Eliminates “tribal” knowledge loss by documenting procedures to inform training
- Provides actionable insights about your systems and maintenance procedures
Assessment
- Thorough inspection of equipment, including mechanical and electrical components
- Design review against original drawings and bills of material (BOMs)
- Expert recommendations to improve or enhance your equipment’s functionality
Changes to Business Operations
As you confront the challenges of modernizing legacy control systems, Engineered Solutions provides obsolescence planning for critical control system components. These projects help you reconcile obsolescence while providing modern enhancements to deliver increased system capacity, flexibility and longevity. Modifications and upgrades include the following services:
Controls and Software
- Complete control platform upgrade or replacement
- Mid-life system technology refreshes
- PLC and HMI replacement
- Obsolescence- or performance-driven variable frequency and servo drive replacements
- Obsolescence- or performance-driven scanner and vision upgrades
Mechanical and Electrical
- Line, tilt-tray and cross-belt sorter rebuilds and upgrades for maximum efficiency, uptime and accuracy
- ZoneFlex® Advanced increases throughput up to 45%, improves product handling, and reduces side-by-sides on existing conveyor lines
- Palletizer upgrades, retrofits and repurposing to enhance operation, productivity, safety and support product and packaging changes
- Product enhancement updates (PEUs) for scalable, continuous improvement
Related Content
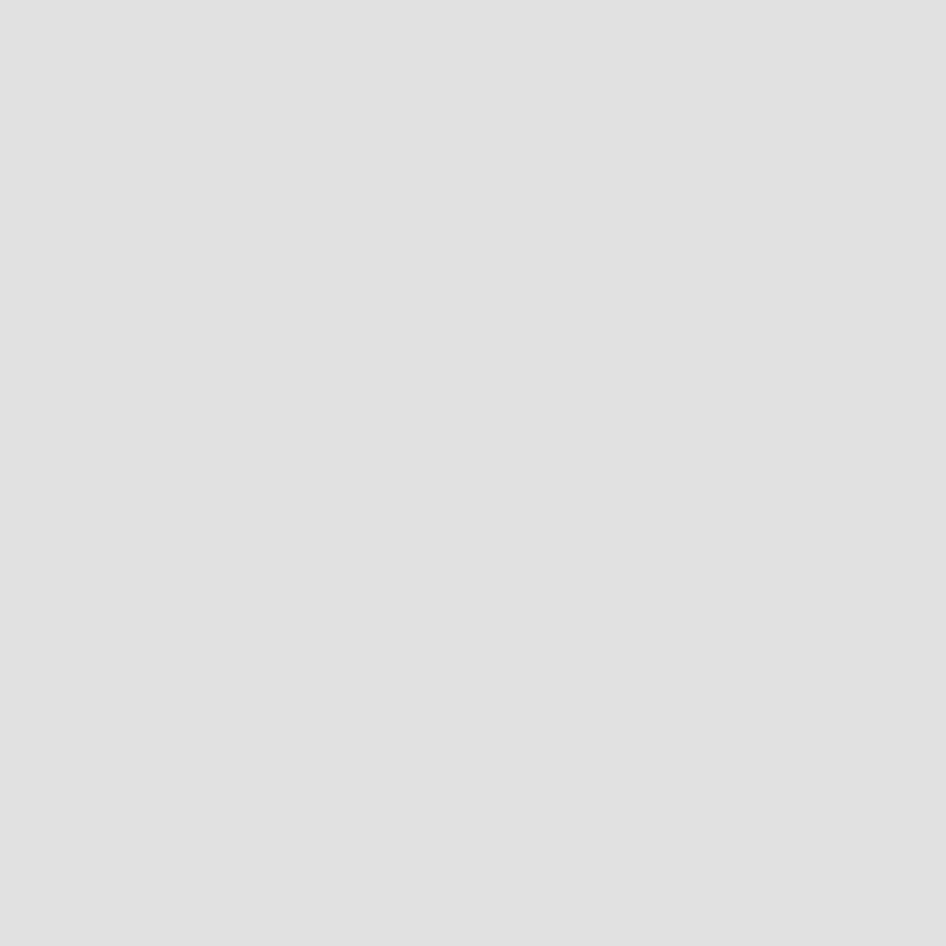
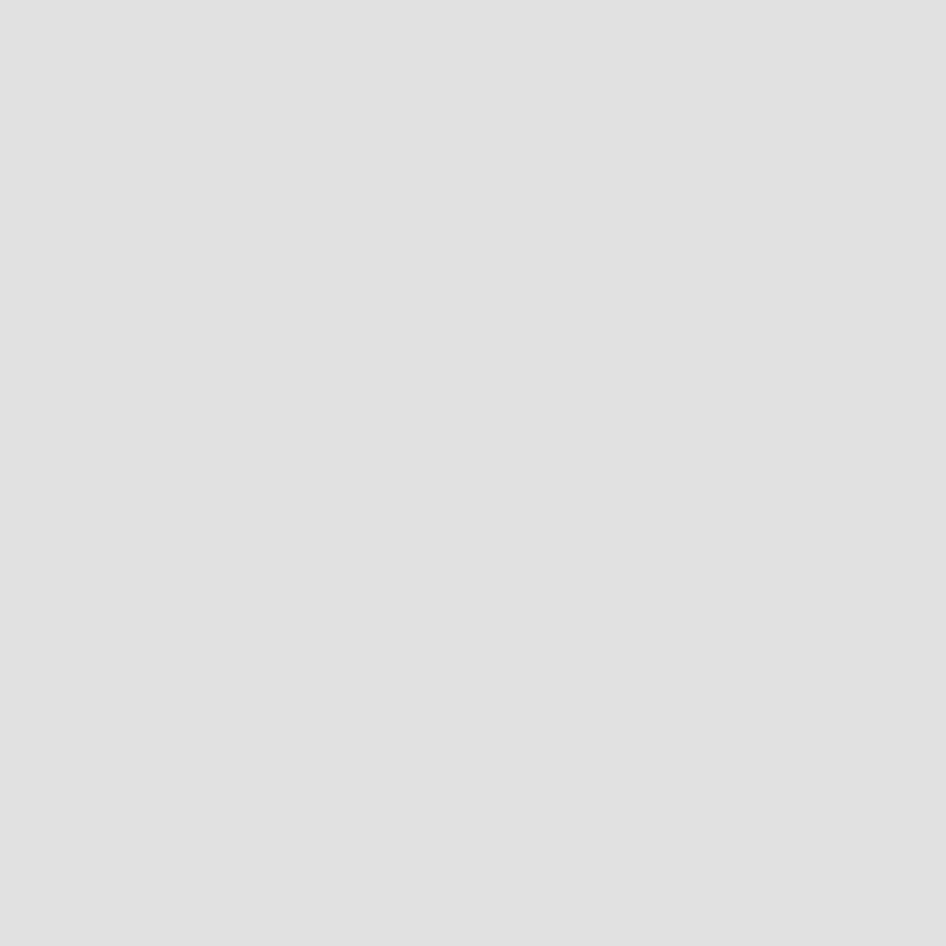
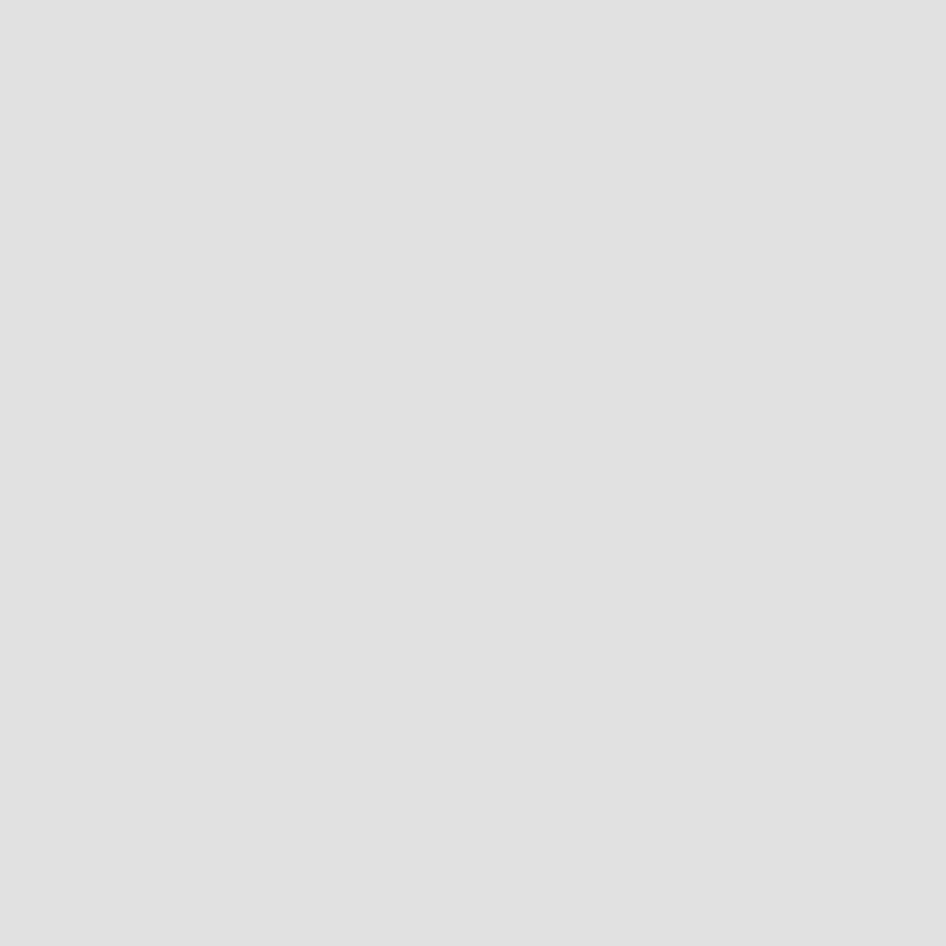
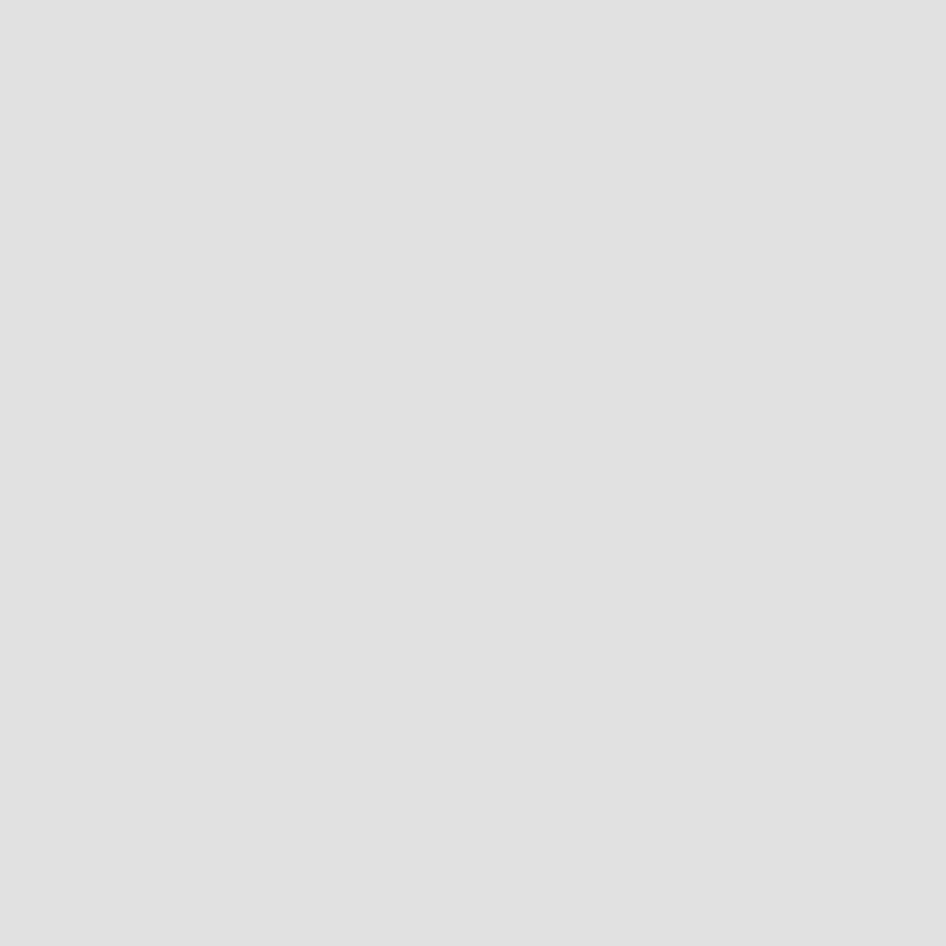
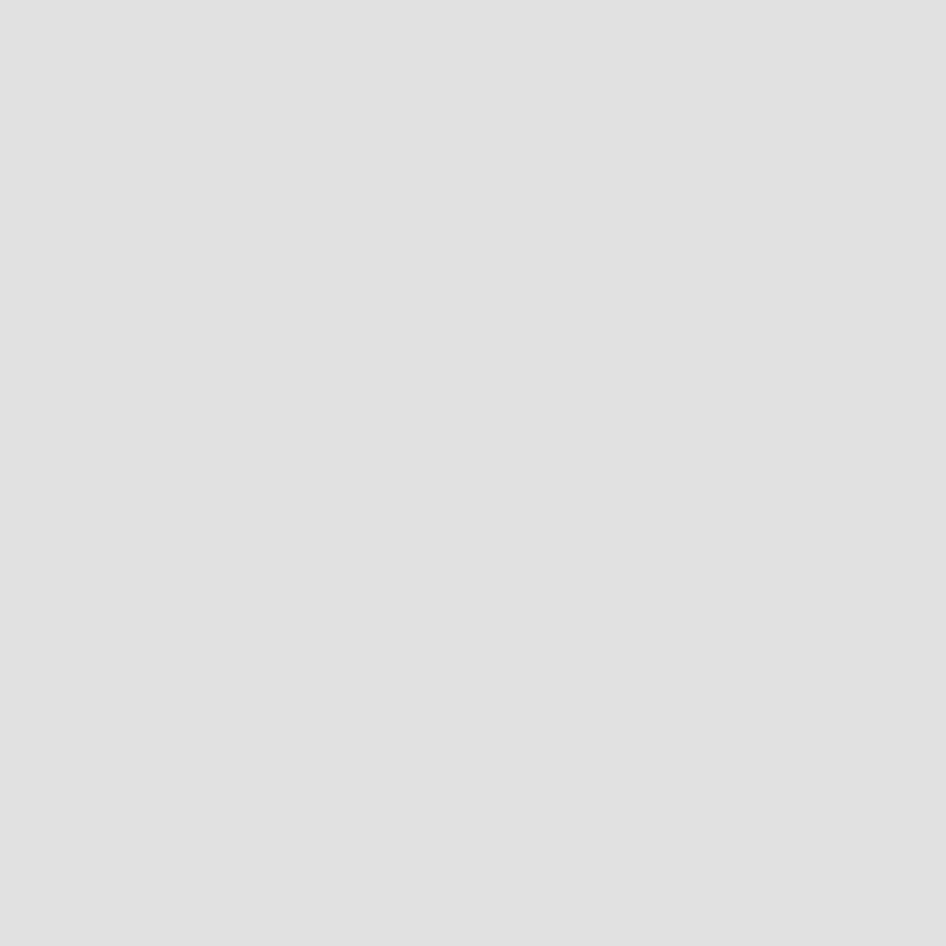
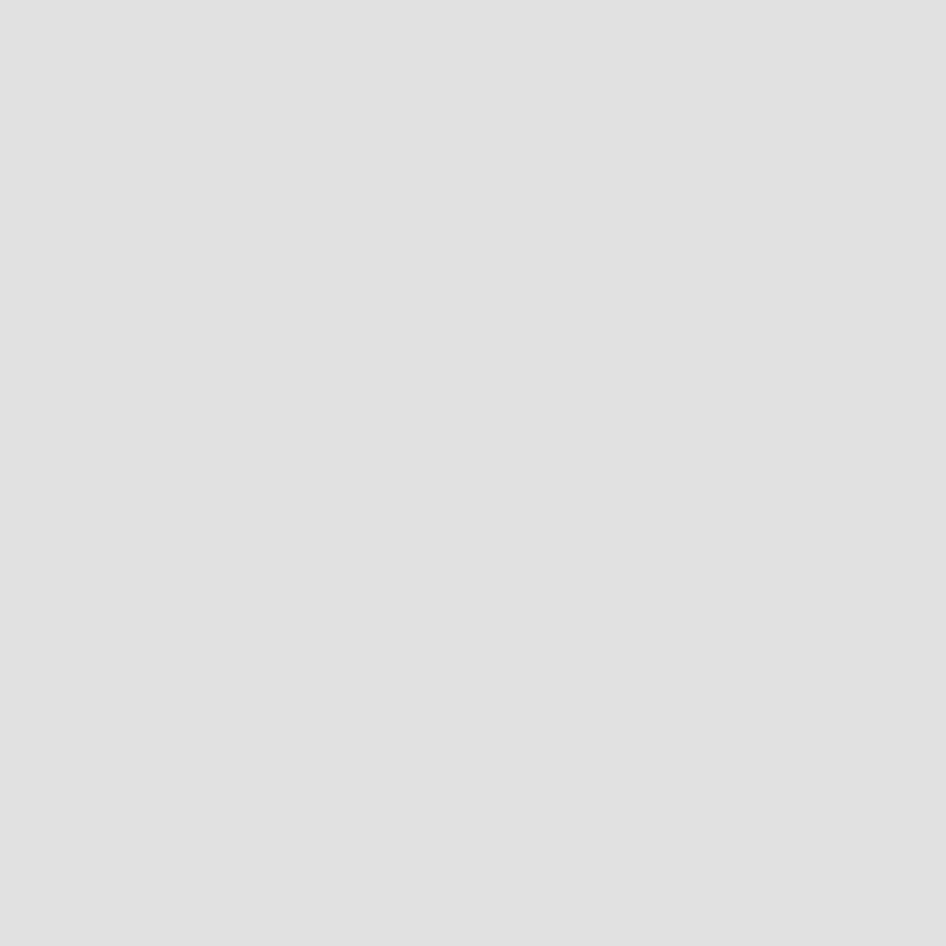
Engineering Services
Let's Connect!
Sign up to receive exclusive communications from Honeywell including product updates, technical information, new offerings, events and news, surveys, special offers, and related topics via telephone, email, and other forms of electronic communication.
Copyright © 2025 Honeywell International Inc
Maximum File Size
Maximum Files Exceeded
Due to inactivity you will be logged out in 000 seconds.
Maximum File Size
Maximum Files Exceeded
You cannot access this page as this product is not available in your country.