-
Global
-
Africa
-
Asia Pacific
-
Europe
-
Latin America
-
Middle East
-
North America
- |
- Partners
- |
-
Currency:Localize your Content
You can set your preferred currency for this account.
Choose a Currency
Currency- CHOOSE YOUR CURRENCY
Update Currency
Changing Currency will cause your current cart to be deleted. Click OK to proceed.
To Keep your current cart, click CLOSE and then save your cart before changing currency.
-
Select Account
Switching accounts will update the product catalog available to you. When switching accounts, your current cart will not move to the new account you select. Your current cart will be available if you log back into this account again.
Account# Account Name City Zip/Post Code CANCELPROCEEDMy Account
-
Support
- View All Productivity Solutions
- Warranties
- Patents
- Global Locations
- Technical Support
- Discontinued Products
- Quality Program and Environmental Compliance
- Return Material Authorization (RMA)
- Legal Documents
- Product Certification
- Software Downloads
- Cyber Security Notifications
- Case Studies and Success Stories
- View All Sensing Solutions
- Sales Contact Form
- Technical Support
- Certificates
- eCOM Portal
- Distributor Inventory
- Return Material Authorization (Test & Measurement)
- Return Material Authorization (Citytech)
- Return Material Authorization (EnviteC)
- Legal Documents
- Intelligent Life Care
- Return Material Authorization (ILC)
-
Global
-
Africa
-
Asia Pacific
-
Europe
-
Latin America
-
Middle East
-
North America
- |
- Partners
- |
You are browsing the product catalog for
You are viewing the overview and resources for
- News & Events
- Featured stories
- Maximize Uptime in the DC With a Predictive Maintenance Strategy
Maximize Uptime in the DC With a Predictive Maintenance Strategy
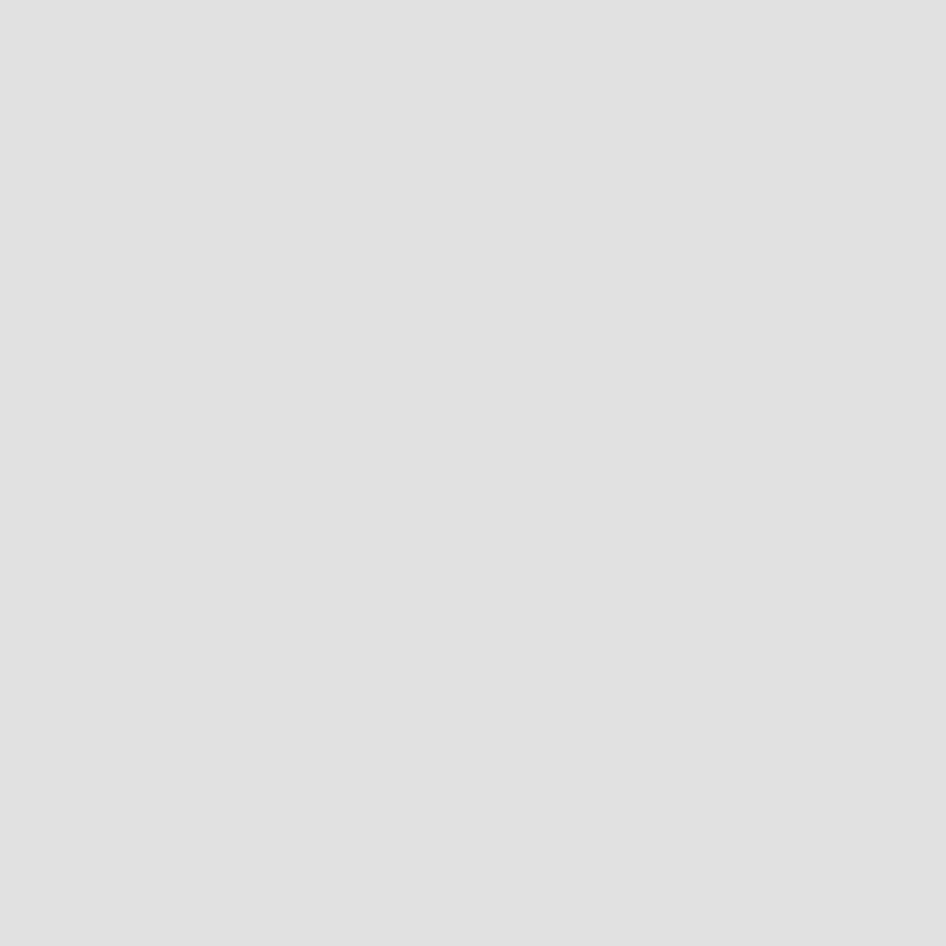
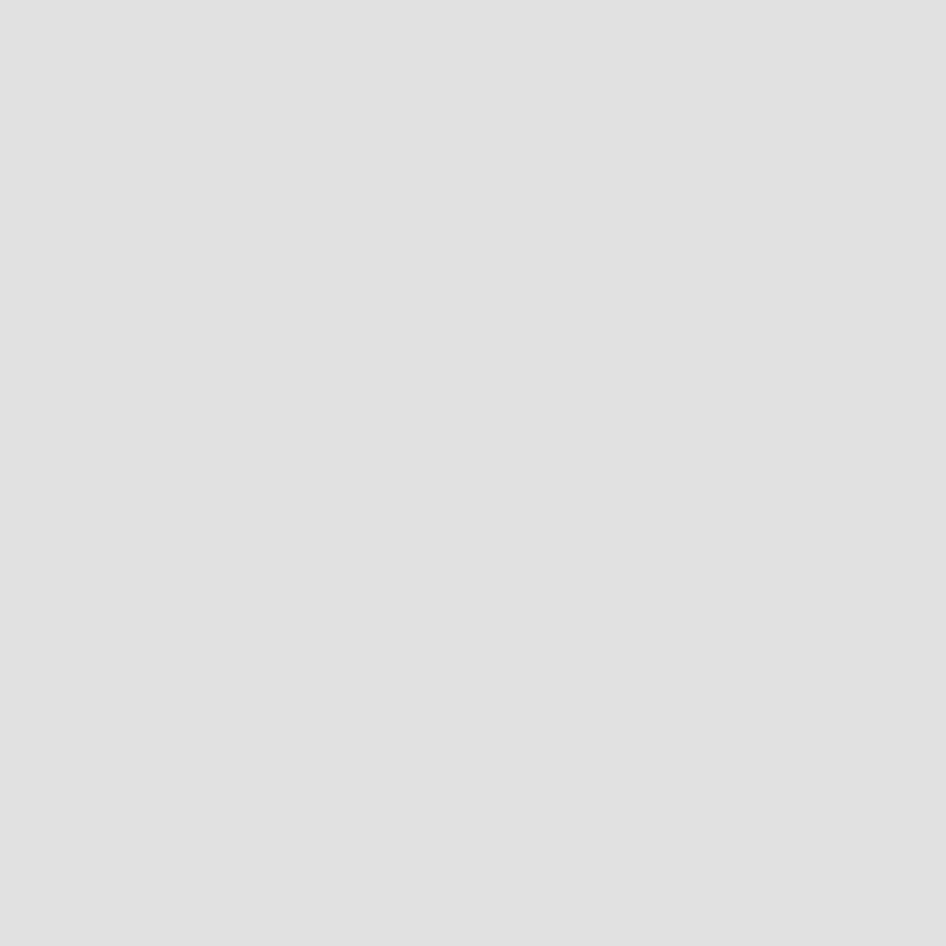
Maximize Uptime in the DC With a Predictive Maintenance Strategy
Eric Rice
August 27, 2018
With 80 percent of distribution centers (DCs) still manually operated, traditional order fulfillment strategies are straining under the weight of e-commerce and omnichannel complexities — most notably rising customer expectations, high order volumes and labor constraints. To overcome these challenges and gain a competitive edge, leading e-commerce retailers are integrating new technologies and making the digital transformation to greater automation within their DC operations.
Chief among these technologies is The Connected Distribution Center by Honeywell Intelligrated — connecting machine-level sensors, workers, material handling equipment, robotics and automated systems to cloud storage and powerful data analytics. With The Connected Distribution Center, retailers can leverage deep operational insights for real-time decision making and can even execute predictive maintenance programs to increase reliability and uptime in their DCs.
We know that downtime for a major e-retailer can cost hundreds of thousands of dollars in lost productivity — and the average outage lasts five hours. We also know that that financial impact is not the only consequence of downtime in today’s competitive retail market. Downtime also means reduced customer service levels and missed deliveries — spelling disappointment for your customers.
It’s estimated that 50 percent of consumers will stop doing business with a retailer after a negative experience, while 73 percent promise repeat business after a positive one.
Increase DC reliability for measurable profitability gains
For an average distribution center, where the cost of downtime is approximately $20,000 per hour, reducing unplanned outages by even 1 percent can potentially result in up to $1 million in annual revenue gains. By connecting machine-level asset sensors within the DC, The Connected Distribution Center can deliver incremental reliability improvements that quickly add up.
Traditional DCs typically rely on calendar-based maintenance programs, where material handling equipment and systems are maintained according to predefined service intervals, regardless of whether assets need servicing or not. Supporting a program like this requires significant budget allocations for service crews and spare parts inventories.
In a connected DC, where assets can be proactively and continually monitored, operators can reap the financial benefits of a predictive, condition-based maintenance model. Consider the key factors in this equation using an average DC as the example:
- Reducing downtime by one-half percentage point = $520,000 annual savings
- Cutting preventive maintenance spending by 20–35 percent = up to $40,000 annual savings
- 30 percent reduction in spare parts and 20 percent drop in inventory = $140,000 annual savings
This example illustrates how a predictive model can produce $700,000 in annual savings through increased uptime and reduced maintenance spending.
Another advantage of DC digitization and connectivity is the ability to remotely receive alerts about underperforming assets or material handling equipment — especially those which indicate issues that could potentially lead to downtime. For example, DC operators typically measure sortation performance using a targeted number of cartons per minute. By utilizing asset connectivity, a database of historic metrics and real-time performance analytics, The Connected Distribution Center sends alerts to DC operators when a mission-critical piece of equipment is not processing the required amount needed to meet the facility’s daily throughput goals. Then, the operator can dispatch the appropriate personnel to diagnose, address and fix the issue.
In a connected DC, as the system accumulates data, the potential for greater insight grows with each passing day. Using advanced machine learning algorithms, this technology can potentially detect patterns of performance at the asset level that indicate the possibility for asset failure well in advance of the actual event. In other words: true predictive maintenance.
These examples are just some of the ways of how The Connected Distribution Center is enabling the digital transformation to take place in the modern DC. Retailers on the leading edge of this movement already have a competitive differentiation using this technology.
To subscribe to our blog and receive exclusive communications and updates from Honeywell Intelligrated, click here.
Let's Connect!
Sign up to receive exclusive communications from Honeywell including product updates, technical information, new offerings, events and news, surveys, special offers, and related topics via telephone, email, and other forms of electronic communication.
Copyright © 2025 Honeywell International Inc
Maximum File Size
Maximum Files Exceeded
Due to inactivity you will be logged out in 000 seconds.
Maximum File Size
Maximum Files Exceeded
You cannot access this page as this product is not available in your country.