-
Global
-
Africa
-
Asia Pacific
-
Europe
-
Latin America
-
Middle East
-
North America
- |
- Partners
- |
-
Currency:Localize your Content
You can set your preferred currency for this account.
Choose a Currency
Currency- CHOOSE YOUR CURRENCY
Update Currency
Changing Currency will cause your current cart to be deleted. Click OK to proceed.
To Keep your current cart, click CLOSE and then save your cart before changing currency.
-
Select Account
Switching accounts will update the product catalog available to you. When switching accounts, your current cart will not move to the new account you select. Your current cart will be available if you log back into this account again.
Account# Account Name City Zip/Post Code CANCELPROCEEDMy Account
-
Support
- View All Productivity Solutions
- Warranties
- Patents
- Global Locations
- Technical Support
- Discontinued Products
- Quality Program and Environmental Compliance
- Return Material Authorization (RMA)
- Legal Documents
- Product Certification
- Software Downloads
- Cyber Security Notifications
- Case Studies and Success Stories
- View All Sensing Solutions
- Sales Contact Form
- Technical Support
- Certificates
- eCOM Portal
- Distributor Inventory
- Return Material Authorization (Test & Measurement)
- Return Material Authorization (Citytech)
- Return Material Authorization (EnviteC)
- Legal Documents
- Intelligent Life Care
- Return Material Authorization (ILC)
-
Global
-
Africa
-
Asia Pacific
-
Europe
-
Latin America
-
Middle East
-
North America
- |
- Partners
- |
You are browsing the product catalog for
You are viewing the overview and resources for
- News & Events
- Featured stories
- Personal Protective Equipment
- The Hands-On Guide to Find the Right Safety Gloves for the Job
The Hands-On Guide to Find the Right Safety Gloves for the Job
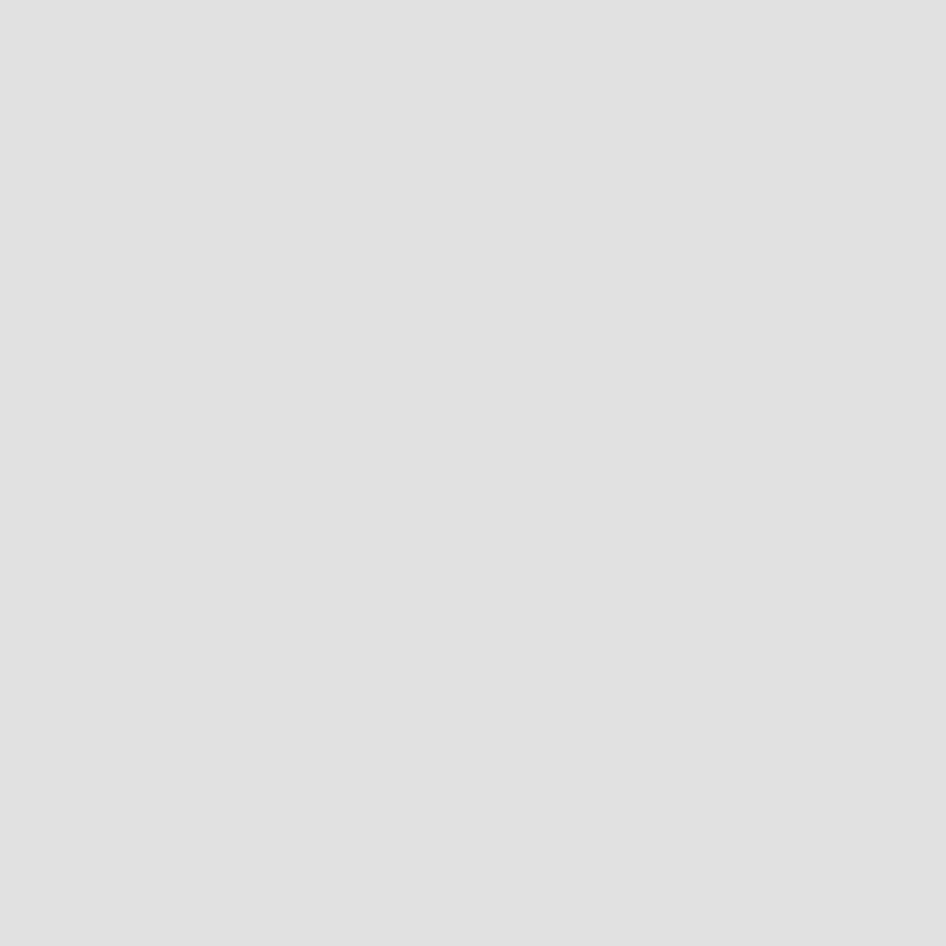
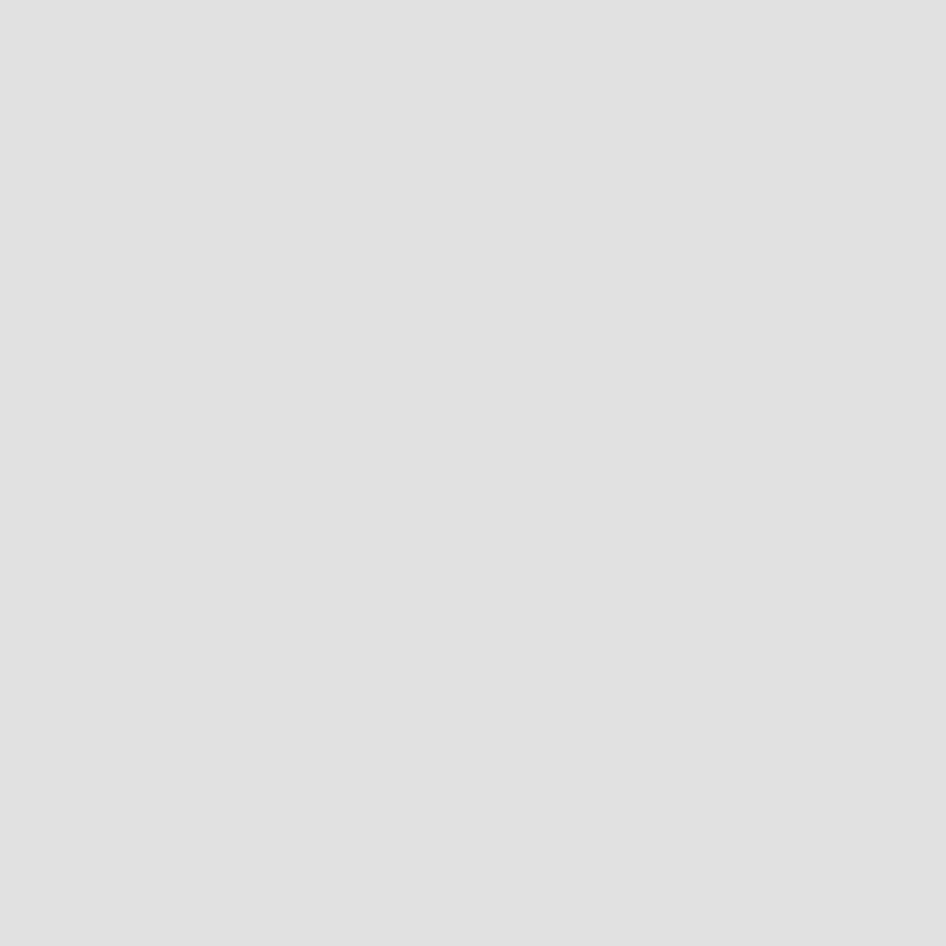
The Hands-On Guide to Find the Right Safety Gloves for the Job
Alexandra Serban
August 30, 2020
Our hand is arguably our most complex tool, helping us perform all sorts of tasks, from intricate painting to operating heavy machinery on a construction site. However, it’s also exposed to a myriad of safety hazards.
Viewed collectively, hand injuries take a toll on people and businesses, in the form of lost wages and lost productivity. The Bureau of Labor Statistics estimates there were 100 million days’ worth of lost work in 2016.
Thus, proper glove selection plays a key role when it comes to creating a safer workplace, to invigorate employee morale and productivity.
If you’re a safety professional in charge of specifying hand protection, you most likely feel overwhelmed by the myriad of products available. The risk of over-specifying is as real as the risk of underspecifying. What’s more, workers won’t wear uncomfortable PPE, right? Plus, there’s always the need to stay cost-effective. This puts even more pressure on the glove selection process.
How do I find the perfect safety hand gloves for me?
In this hand glove selection guide, we’ll discuss how to select the right gloves for the job by looking at these key aspects:
- Hand hazards and safety risks
- The cost of workplace hand injuries
- Hand protection standards
- Size and comfort
Step 1
Know the application and assess the hazard
Each working environment has its own set of hazards.
Oil and gas workers are especially exposed to cuts, pinch and impact injuries when handling oily, wet and sharp objects. Hand and finger injuries top the list of injuries in this industry sector.
Construction work is considered one of the most dangerous professions, as worker fatigue, maneuvering heavy machinery and hand-operated power tools pose serious hand risks. For some workers, chemical substances that irritate or even burn skin are the main problem.
It may seem obvious, but start your assessment by looking closer to:
- Activities, processes and equipment that can cause hand-related injuries. Are you inspecting hand tools before using them? Are tools completely de-energized before cleaning or repairing them?
- Feedback from workers, as they might identify hazards that pass a first at-a-glance inspection.
- Official accident records
- The manufacturer instructions/ data sheets of tools and machinery handled by workers
- Non-routine operations (e.g. maintenance cleaning) that might pose hazards. For instance, work-related skin problems caused by unknown exposure to chemicals such as soaps and detergents.
Step 2
Know your people
Not all workers face the same level of risk.
Where do your people work and what do they do? Are they exposed to a hand hazard? Are they working with unguarded machinery? Are they well-trained and experienced enough to handle equipment? Are they new or contractors?
On this note, it’s important to identify ways to help contractors understand and reinforce your safety expectations for the staff while working on your site.
Placing safety signs in your areas of operations is a great way to remind workers about hand safety.
Step 3
Identify risk levels
Think about each hazard and ask yourself how likely is it that will cause harm and how severe consequences can be. For instance, cut-related injuries fall into three main categories, based on their severity.
- Incisions – resulting from contact with a sharp edge that results in a mild wound. E.g. a paper cut.
- Lacerations – torn, open wounds from contact with a jagged, rough edge.
- Abrasions – skin being scrapped by a rough surface.
Why is this important?
As much as managers select PPE with the best intention in mind, some choices may lead to overprotection. A glove with an ANSI level 4 may be too bulky for an application that requires a good level of dexterity, and the worker finds it difficult to complete the task at hand. This could make him give up the gloves entirely.
Step 4
Know hand safety standards and regulations
March 2019 marked the launch of a new standard for industrial gloves. The International Safety Equipment Association (ISEA) released the American National Standard for Performance and Classification for Impact Resistant Hand Protection — ANSI/ISEA 138-2019.
Build upon its predecessor – ANSI/ISEA 105-2016 -, this standard is the first to address hand impact injuries in North America. Its role is to help safety professionals make better-informed decisions about glove selection by better understanding the classification of gloves. It also covers protection requirements on knuckles and fingers, two areas considered critical.
In Europe, EN 420 is the baseline for hand protection. All gloves must adhere to its testing requirements. EN 420 does not cover the protective properties of gloves, so it must be applied in combination with other relevant standards.
For instance, impact protection gloves need to pass EN 388 or ISEA 138 impact tests. ANSI/ISEA 138 has standardized the method for testing impact-resistant gloves, guiding manufacturers end-to-end on how tests should be performed.
Under the new standard, a typical impact-glove test implies dropping a falling mass (drop striker) on the knuckles and fingers and recording the transferred force in kilonewtons. This is repeated 8 times for the knuckles and ten times for the fingers.
Learn more, in our video.
Step 5
Match gloves with the application
OSHA recommends that "gloves be selected based on the task that will be performed, the chemicals encountered, and the performance and construction characteristics of the glove material.”
For instance, automotive plant workers feeding the stamping presses are exposed to rough edges and need gloves with resistance to cuts and punctures.
Fortunately, a variety of new technologies, designs and materials have surfaced in the past years.
“New materials and processes have improved coatings and seamless knits, and consequently, protection and wearer comfort”, John Sujo, Global Product Manager at Honeywell, says in this article. “When workers are exposed to cut hazards, they want the glove to protect their hand from all injuries that could happen on the job, as well as provide excellent grip and breathability.”
Tech advances together with an increasing consumer awareness for health and hygiene drive the expansion of the impact glove market.
A typical impact glove includes TPR (thermoplastic rubber) with the adequate thickness, softness and hardness to protect the back-of-hand and other sensitive parts of the hand. It may also feature anti-impact padding.
When it comes to materials, it’s a known fact that heavier-gauge gloves provide enhanced hand protection, while thinner rubber, cotton or leather gloves come with greater dexterity and tactile sensitivity. Strong-knit and palm-coated gloves also offer more freedom of movement than leather gloves or fully-coated ones. Yet, bear in mind, high-tactile feel is very subjective.
Rubber properties such as elasticity, resilience, and form-fitting justify the wide applications of rubber in various industrial gloves and its extensive use for various applications in the industrial and medical sectors.
Latex coated gloves offer a high-level of grip on both wet and dry surfaces, most biological materials, and are perfect for jobs that require high-agility. For instance, thin, disposable gloves, are widely used in laboratories. But they offer little protection from commonly used chemicals, and will degrade in a matter of minutes. Moreover, a significant part of the population has developed an allergy to latex products.
Step 6
Find the right hand glove fit
70% of workers who have injured their hands, weren’t wearing gloves at the time of the incident. Most of the time it’s a matter of comfort. Sizing and fit make a big difference in how comfortable gloves are. Here are some things to consider:
- Outside seams are typically more comfortable to wear
- Inside seams are durable, but can cause skin irritations unless carefully selected.
- Old worn-out gloves can lose their protective ability
Step 7
Educate on how to wear hand protection
Using gloves might seem intuitive, but workers also need to be informed on hand-related hazards present at the job site and potential health effects related to glove materials. Other topics to discuss include the importance of wearing gloves that fit. A glove that is too big will slide off, while a small one will rip or tear easily.
Inspecting gloves to make sure they’re still protective, glove replacement and safe hand practices are also key in your hand safety program.
Conclusion
There isn’t one glove to offer protection from all types of hand injuries, yet staying informed on the latest innovations, listening to workers’ needs and continuous training and education significantly diminish the risk of hand injuries.
Let's Connect!
Sign up to receive exclusive communications from Honeywell including product updates, technical information, new offerings, events and news, surveys, special offers, and related topics via telephone, email, and other forms of electronic communication.
Copyright © 2025 Honeywell International Inc
Maximum File Size
Maximum Files Exceeded
Due to inactivity you will be logged out in 000 seconds.
Maximum File Size
Maximum Files Exceeded
You cannot access this page as this product is not available in your country.