-
Global
-
Africa
-
Asia Pacific
-
Europe
-
Latin America
-
Middle East
-
North America
- |
- Partners
- |
-
Currency:Localize your Content
You can set your preferred currency for this account.
Choose a Currency
Currency- CHOOSE YOUR CURRENCY
Update Currency
Changing Currency will cause your current cart to be deleted. Click OK to proceed.
To Keep your current cart, click CLOSE and then save your cart before changing currency.
-
Select Account
Switching accounts will update the product catalog available to you. When switching accounts, your current cart will not move to the new account you select. Your current cart will be available if you log back into this account again.
Account# Account Name City Zip/Post Code CANCELPROCEEDMy Account
-
Support
- View All Productivity Solutions
- Warranties
- Patents
- Global Locations
- Technical Support
- Discontinued Products
- Quality Program and Environmental Compliance
- Return Material Authorization (RMA)
- Legal Documents
- Product Certification
- Software Downloads
- Cyber Security Notifications
- Case Studies and Success Stories
-
Global
-
Africa
-
Asia Pacific
-
Europe
-
Latin America
-
Middle East
-
North America
- |
- Partners
- |
You are browsing the product catalog for
You are viewing the overview and resources for
- News & Events
- Featured stories
- How a WES Delivers Automated Throughput and Workflow Efficiencies in DCs
How a WES Delivers Automated Throughput and Workflow Efficiencies in DCs
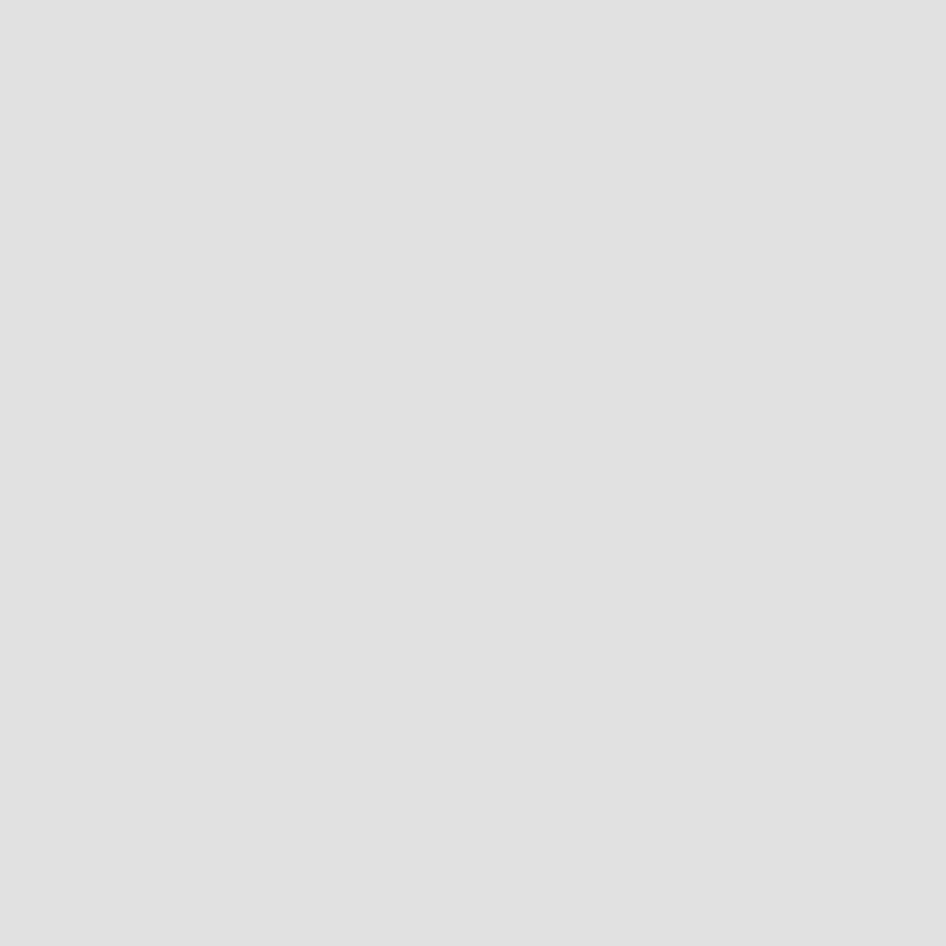
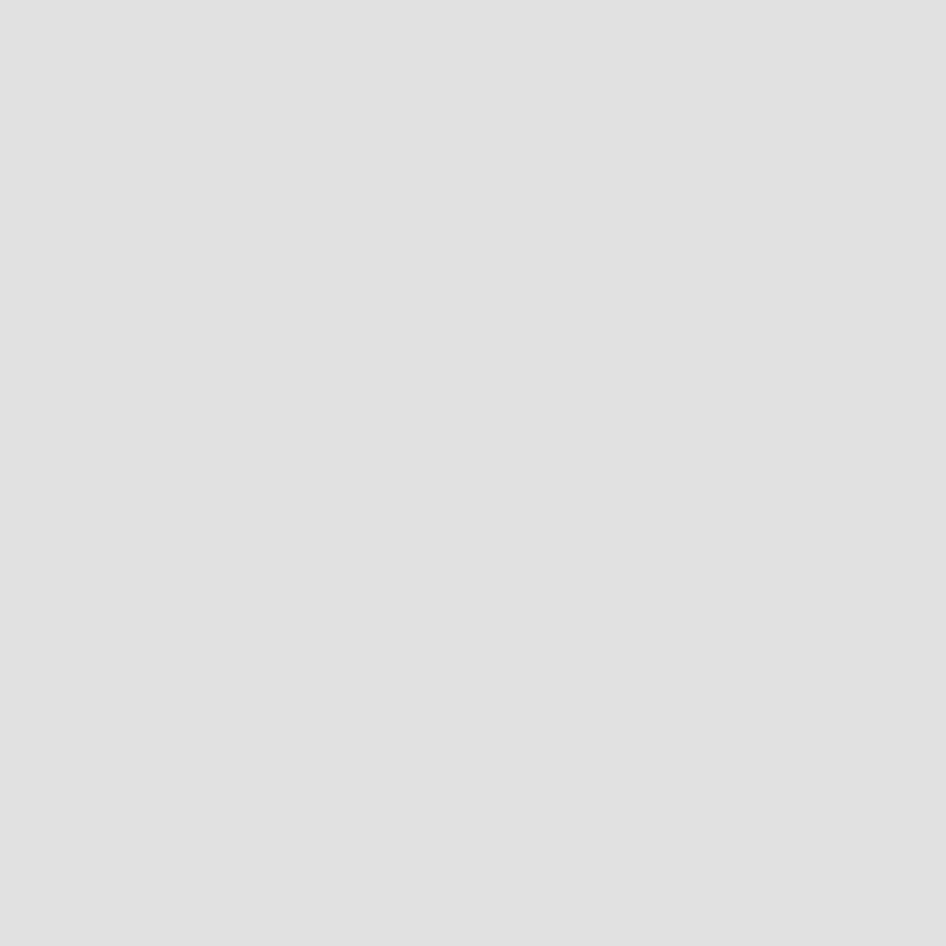
How a WES Delivers Automated Throughput and Workflow Efficiencies in DCs
January 14, 2019
To compete in the fast-paced, high-stakes world of e-commerce, modern distribution and fulfillment center operations are introducing increasing levels of automation. Too often these automated systems operate independently, performing very discrete tasks and processes. In my most recent blog, I explained how warehouse execution systems (WES) are connecting these islands of automation to integrate disparate workflows and enable dynamic, real-time decision making for smart order prioritization and order release execution. In this blog, I’ll discuss how that translates into enhanced throughput and workflow efficiencies.
Today, many retailers are seeking to leverage existing assets while introducing new automation systems. Because each of these assets could potentially be controlled by separate vendors, it can be difficult to integrate them with most warehouse management systems (WMS) out of the box. A WES is designed to address this integration challenge by giving retailers the ability to orchestrate order fulfillment across processes among these disparate systems. This is just one example illustrating why a WES is quickly becoming an essential software component in modern distribution centers (DCs).
In e-commerce operations that have already incorporated a WES — particularly those where the dynamic prioritization of orders is a requirement — we’re seeing the critical roles of order release and execution functions taken over by the WES. It’s here where a WES demonstrates its flexibility and visibility into real-time product flows and order fulfillment lifecycles. Let’s examine a few examples of what this dynamic optimization looks like.
Intelligent order management and release
Instead of pushing out orders in large groups and hoping they get shipped at the correct times, a WES utilizes a pull model for order release, analyzing downstream capacity across various areas of the DC to ensure there is not an area starved or overworked, while considering the most important orders to complete. By doing this, a WES is able to prioritize “hot” orders as they are received and instruct operators to perform the next best tasks as capacity becomes available.
For example, consolidating and shipping orders comprised of products from varying locations is a common DC challenge, especially when some items are perishable or have unique handling requirements. A WES provides intelligent order planning and release to make sure products from various locations arrive at the shipping dock at the same time. By taking all aspects related to discrete order fulfillment into consideration — such as labor and workstation availability, product attributes, value-added services, product travel routes and DC congestion — a WES prioritizes and escalates orders to meet service level agreements (SLA) while reducing congestion, bottlenecks and overloading of resources.
AS/RS system automation
Many companies are introducing automated storage and retrieval systems (AS/RS) to reduce labor requirements, avoid capital expansion, and lay the foundation for greater long-term productivity. When the automated workflows of an AS/RS are integrated into a WES, it opens up a new world of possibilities. For example, the WES can handle cartons of varying sizes and provide maximum utilization by determining the best location to dynamically store the cartons within the AS/RS array, rather than constraining those decisions to fixed locations. Instead of creating locations based on the largest carton size, which leads to wasted space when smaller cartons are stored, a WES can tightly fit cartons based on available space within the array. This dynamic, intelligent decision making makes maximum use of the storage capacity available in the AS/RS.
Another example of AS/RS automation with a WES is the ability to completely automate bulk and active storage for store replenishment. Here, retailers can use an AS/RS crane system for bulk storage and an AS/RS shuttle system for residual inventory. In this scenario, the AS/RS receives a wave of orders from a WMS, and then hands off to a WES for execution. Then, the WES aggregates demand by specific items to determine the best sources of allocation to achieve maximum throughput. Smaller quantities can be fulfilled from residual inventory while an AS/RS crane system pulls full pallets from bulk storage for larger quantities. Pallets are then routed to available automatic depalletizing stations so that cases can be shipped as needed. Finally, a WES gives the depalletizer instructions to de-layer the pallet, and cartons are placed on a conveyor for sorting and routing to individual stores.
AS/RS goods-to-operator robotic each picking to sorter
To improve picking accuracies and reduce labor touches, some e-commerce retailers are automating goods-to-operator (GTO), each-picking stations with the addition of robotic capabilities. By pairing this with an AS/RS, a WES instructs the system to bring a tote of single-SKU items to the robotic picking station based on order demand. Then, it sends pick quantity and placement instructions to the robotic arm, telling it to either place items directly into an order carton or onto a unit sorter for fulfillment. For a fully automated fulfillment workflow, a WES can even pair a shuttle for chute closing at a sorter, which will transfer the completed order to a take-away conveyor and make the chute available for the next demand. This eliminates the manual, labor-intensive chute closing process typically completed within the WMS via an RF hand-held device.
Just-in-time put wall allocation and order consolidation
Put walls have become integral tools for order consolidation in automated DCs, and a WES only enhances their usefulness. A WES takes a real-time view of order prioritization and put wall availability during upstream picking, and then allocates orders to the best-available put wall. Using put walls with a WES combines the benefits of wave picking with just-in-time cubby assignment for increased throughput and decreased put wall congestion.
Whether providing smart workflow allocations based on available capacity or instructing order consolidation processes like put walls or unit sortation, a WES integrates automation technologies to make real-time order fulfillment and execution decisions.
Download our new white paper, Material Handling Automation Driving Wider Adoption of WES to learn how a WES can deliver automated throughput and workflow efficiencies in your DC.
To subscribe to our blog and receive exclusive communications and updates from Honeywell Intelligrated, click here.
Let's Connect!
Sign up to receive exclusive communications from Honeywell including product updates, technical information, new offerings, events and news, surveys, special offers, and related topics via telephone, email, and other forms of electronic communication.
Copyright © 2025 Honeywell International Inc
Maximum File Size
Maximum Files Exceeded
Due to inactivity you will be logged out in 000 seconds.
Maximum File Size
Maximum Files Exceeded
You cannot access this page as this product is not available in your country.