-
Global
-
Africa
-
Asia Pacific
-
Europe
-
Latin America
-
Middle East
-
North America
- |
- Partners
- |
-
Currency:Localize your Content
You can set your preferred currency for this account.
Choose a Currency
Currency- CHOOSE YOUR CURRENCY
Update Currency
Changing Currency will cause your current cart to be deleted. Click OK to proceed.
To Keep your current cart, click CLOSE and then save your cart before changing currency.
-
Select Account
Switching accounts will update the product catalog available to you. When switching accounts, your current cart will not move to the new account you select. Your current cart will be available if you log back into this account again.
Account# Account Name City Zip/Post Code CANCELPROCEEDMy Account
-
Support
- View All Productivity Solutions
- Warranties
- Patents
- Global Locations
- Technical Support
- Discontinued Products
- Quality Program and Environmental Compliance
- Return Material Authorization (RMA)
- Legal Documents
- Product Certification
- Software Downloads
- Cyber Security Notifications
- Case Studies and Success Stories
- View All Sensing Solutions
- Sales Contact Form
- Technical Support
- Certificates
- eCOM Portal
- Distributor Inventory
- Return Material Authorization (Test & Measurement)
- Return Material Authorization (Citytech)
- Return Material Authorization (EnviteC)
- Legal Documents
- Intelligent Life Care
- Return Material Authorization (ILC)
-
Global
-
Africa
-
Asia Pacific
-
Europe
-
Latin America
-
Middle East
-
North America
- |
- Partners
- |
You are browsing the product catalog for
You are viewing the overview and resources for
- News & Events
- Featured stories
- Video-Enabled Maintenance Helps to Resolve Issues Even Faster
Video-Enabled Maintenance Helps to Resolve Issues Even Faster
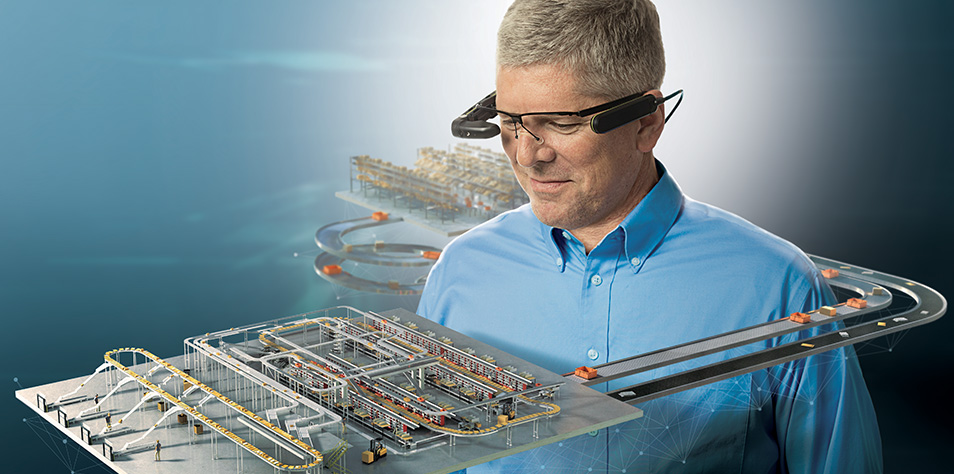
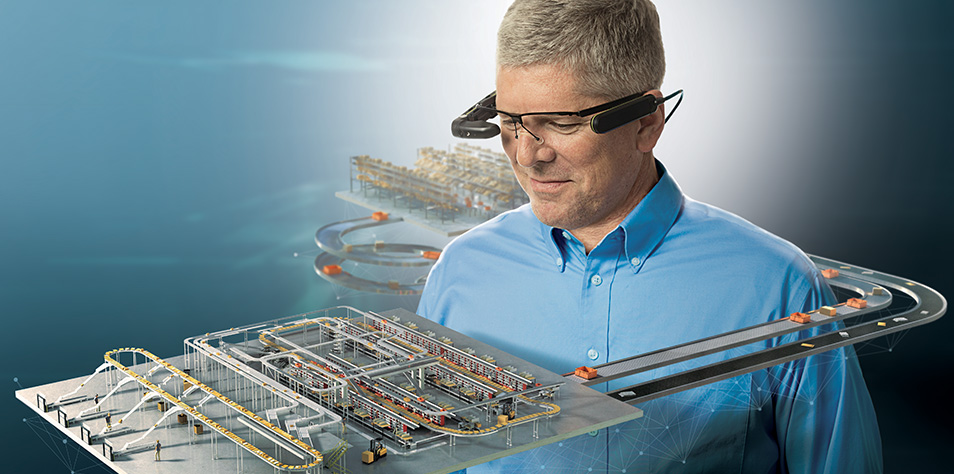
Video-Enabled Maintenance Helps to Resolve Issues Even Faster
Mike Kelton
March 23, 2021
Unplanned downtime is the bane of every operations manager’s existence. For them, perhaps nothing can be more painful than watching productivity plummet as employees sit idly due to equipment failure.
Historically, the only option for solving such an issue was for an experienced in-house maintenance and repair technician to call a remote technical support professional to discuss the problem. If that effort failed, then a field support technician authorized by the original equipment manufacturer (OEM) had to travel to the site to assess — and hopefully fix — the issue. With travel alone potentially taking 24–48 hours, as well as representing an added expense, the costs of unplanned downtime can add up quickly.
Enter video-enabled remote technical support, solutions made possible by advances in wearable technologies developed for industrial applications. These emerging options — such as Honeywell Intelligrated’s TechSight video-enablement solution — combine (optional) smart glasses with augmented reality (AR) capabilities and built-in video cameras to accelerate equipment issue resolution. When these smart glasses are worn by an in-house technician — or someone familiar with the equipment’s operation (although perhaps not trained in repair) — their view of the problem is transmitted to a remote technical support representative.
The solution enables “see what I see” troubleshooting by giving a remote technical support team a clear view of the issue for real-time diagnosis and consultation. Not only can they make more targeted, specific recommendations for the steps to be taken to resolve the problem, but they can also direct the hands-free wearer of the smart glasses to shift their focus or make manual adjustments under direct supervision. Further, they can display schematics, graphics, snapshots, video, messaging and documents into the field of view of the wearer’s smart glasses. This provides a visual illustration of key components to help identify damage or direct repair processes.
All of these capabilities dramatically reduce the time required to achieve a resolution, significantly decreasing unplanned equipment downtime. What’s more, anyone can wear these devices, regardless of their level of maintenance expertise, as their actions will be guided by a remote expert. This solution also eliminates the need for an on-site visit from a technical or service expert, as well as the associated travel costs.
In our most recent On The Move webinar, I explained how leveraging wearable video-enablement devices and AR for remote maintenance brings fast issue resolution into view. It also should be noted that these same technologies can be used to support picking and order fulfillment processes, training, and virtual testing of proposed facility designs and modifications.
Incorporating wearables for technical support into an operation
In the webinar, I explained that the journey to integrating a digitally enabled remote technical support solution that utilizes wearables and AR can be completed in three key steps:
- Develop a strong business case. In a distribution center (DC), the ability to more quickly resolve equipment problems that cause unplanned downtime can have a direct impact on overall operational productivity.
- Start small and clearly define the scope. Select a key operational area for testing and evaluation of the solution.
- Gain internal support. Build a team internally who is excited about utilizing new technologies and applying them in innovative ways to solve problems like unplanned downtime.
To learn more about how video-enabled technical support can address your operation’s maintenance, repair and productivity challenges, please view this webinar.
To register for our upcoming webinars in this series, visit this page for more details.
To subscribe to our blog and receive exclusive communications and updates from Honeywell Intelligrated, click here.
Let's Connect!
Sign up to receive exclusive communications from Honeywell including product updates, technical information, new offerings, events and news, surveys, special offers, and related topics via telephone, email, and other forms of electronic communication.
Copyright © 2025 Honeywell International Inc
Maximum File Size
Maximum Files Exceeded
Due to inactivity you will be logged out in 000 seconds.
Maximum File Size
Maximum Files Exceeded
You cannot access this page as this product is not available in your country.