-
Global
-
Africa
-
Asia Pacific
-
Europe
-
Latin America
-
Middle East
-
North America
- |
- Partners
- |
-
Currency:Localize your Content
You can set your preferred currency for this account.
Choose a Currency
Currency- CHOOSE YOUR CURRENCY
Update Currency
Changing Currency will cause your current cart to be deleted. Click OK to proceed.
To Keep your current cart, click CLOSE and then save your cart before changing currency.
-
Select Account
Switching accounts will update the product catalog available to you. When switching accounts, your current cart will not move to the new account you select. Your current cart will be available if you log back into this account again.
Account# Account Name City Zip/Post Code CANCELPROCEEDMy Account
-
Support
- View All Productivity Solutions
- Warranties
- Patents
- Global Locations
- Technical Support
- Discontinued Products
- Quality Program and Environmental Compliance
- Return Material Authorization (RMA)
- Legal Documents
- Product Certification
- Software Downloads
- Cyber Security Notifications
- Case Studies and Success Stories
- View All Sensing Solutions
- Sales Contact Form
- Technical Support
- Certificates
- eCOM Portal
- Distributor Inventory
- Return Material Authorization (Test & Measurement)
- Return Material Authorization (Citytech)
- Return Material Authorization (EnviteC)
- Legal Documents
- Intelligent Life Care
- Return Material Authorization (ILC)
-
Global
-
Africa
-
Asia Pacific
-
Europe
-
Latin America
-
Middle East
-
North America
- |
- Partners
- |
You are browsing the product catalog for
You are viewing the overview and resources for
- News & Events
- Featured stories
- Spare Parts Are Critical in Meeting Tighter Fulfillment Demands
Spare Parts Are Critical in Meeting Tighter Fulfillment Demands
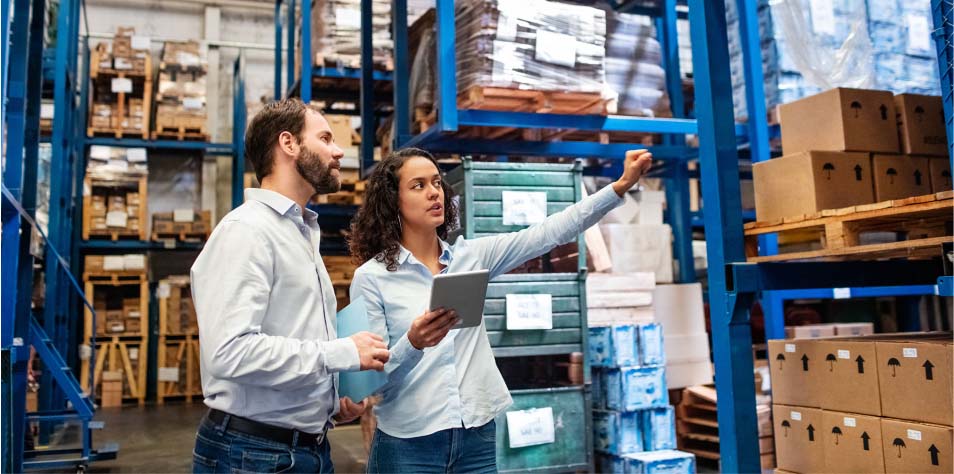
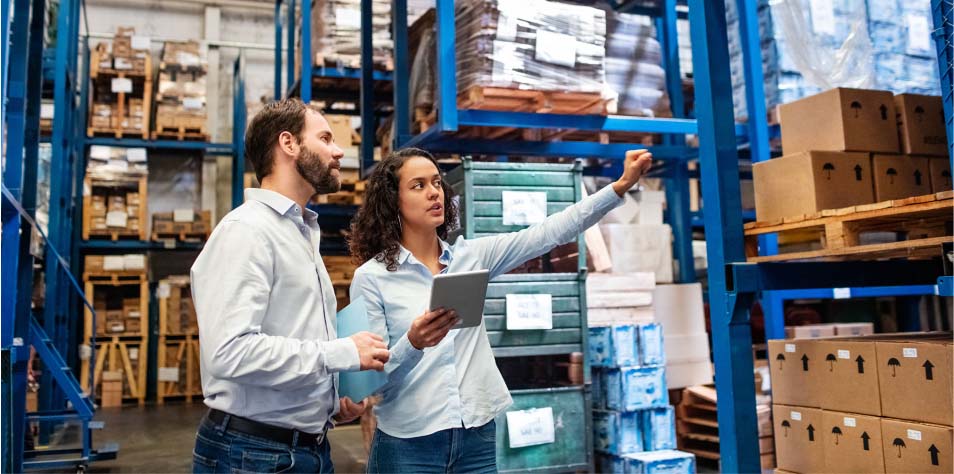
Spare Parts Are Critical in Meeting Tighter Fulfillment Demands
Cindy Lyneis
June 1, 2021
Plan on it
As recently as five years ago, three- to five-day shipping was standard — and consumers were fine with that. Those days are now gone. With e-commerce, the new norm is one- to two-day delivery, and consumers expect businesses to meet that high-pressure schedule. With this shorter delivery window, distribution and fulfillment centers are under the spotlight. Operations and maintenance managers need to be absolutely certain they have the critical parts needed to react quickly when issues and interruptions arise among their material handling systems — because it’s not a matter of if issues will occur, but when.
Distribution center (DC) order volume continues to accelerate as the e-commerce landscape becomes more competitive. The key to keeping a material handling system up and running for the long haul is to always have the right parts on hand to respond quickly when unexpected failures happen. Properly maintaining the spare parts inventory allows you to minimize downtime while containing overhead costs.
Plan for efficiency
Every distribution center can take simple steps to ensure they are always properly supplied without overrunning their respective budget.
- Have a quality computerized maintenance management system (CMMS) for asset management
- Properly align minimum/maximum reorder points
- Conduct routine audits to verify the stocking plan is being followed
- Align with an OEM that can provide guidance on budget and recommended quantities
We live in a very analytical world, and most of the data you need to create a DC’s stocking plan is already available within your CMMS. Your CMMS’s OEM can help with recommendations and analytics — even the best data is only as good as what you do with it. Gather information on how often a specific part is needed throughout your system? Is it in the critical path? Do you have work-arounds for specific areas of your facility? All of these questions lead to creating a complete and efficient parts stocking plan.
Plan on stock maintenance
Work doesn’t stop just because all the data is gathered and a solid stocking plan is developed. Even the best stocking setup requires maintenance. The ongoing stock maintenance in every parts cage starts with ensuring the reliability of the parts. Is your team using proper check-in/check-out procedures? Are they using the parts specified in CMMS work orders? Are reorder checkpoints being followed? Outside of a day-to-day maintenance routine, there are also yearly check-ups to perform. As systems age and change, different parts become obsolescent. It’s essential to keep your parts inventory up to date, turning over stock and proactively determining which parts on your shelf are becoming obsolete. You need to establish go-forward steps that ensure you’ll have the new components available when needed. As always, you can ask your OEM about proactive obsolescence planning and how to make sure you receive notifications of which parts may need replacement.
As the e-commerce market continues to explode and consumers’ demands increase, the importance of staying up and running at all times rises. A smart parts system plays a key role in assuring you can deliver to your customers at the fast pace they have come to not only expect — but demand.
To subscribe to our blog and receive exclusive communications and updates from Honeywell Intelligrated, click here.
Let's Connect!
Sign up to receive exclusive communications from Honeywell including product updates, technical information, new offerings, events and news, surveys, special offers, and related topics via telephone, email, and other forms of electronic communication.
Copyright © 2025 Honeywell International Inc
Maximum File Size
Maximum Files Exceeded
Due to inactivity you will be logged out in 000 seconds.
Maximum File Size
Maximum Files Exceeded
You cannot access this page as this product is not available in your country.