-
Global
-
Africa
-
Asia Pacific
-
Europe
-
Latin America
-
Middle East
-
North America
- |
- Partners
- |
-
Currency:Localize your Content
You can set your preferred currency for this account.
Choose a Currency
Currency- CHOOSE YOUR CURRENCY
Update Currency
Changing Currency will cause your current cart to be deleted. Click OK to proceed.
To Keep your current cart, click CLOSE and then save your cart before changing currency.
-
Select Account
Switching accounts will update the product catalog available to you. When switching accounts, your current cart will not move to the new account you select. Your current cart will be available if you log back into this account again.
Account# Account Name City Zip/Post Code CANCELPROCEEDMy Account
-
Support
- View All Productivity Solutions
- Warranties
- Patents
- Global Locations
- Technical Support
- Discontinued Products
- Quality Program and Environmental Compliance
- Return Material Authorization (RMA)
- Legal Documents
- Product Certification
- Software Downloads
- Cyber Security Notifications
- Case Studies and Success Stories
- View All Sensing Solutions
- Sales Contact Form
- Technical Support
- Certificates
- eCOM Portal
- Distributor Inventory
- Return Material Authorization (Test & Measurement)
- Return Material Authorization (Citytech)
- Return Material Authorization (EnviteC)
- Legal Documents
- Intelligent Life Care
- Return Material Authorization (ILC)
-
Global
-
Africa
-
Asia Pacific
-
Europe
-
Latin America
-
Middle East
-
North America
- |
- Partners
- |
You are browsing the product catalog for
You are viewing the overview and resources for
- News & Events
- Featured stories
- Costs of Non-OEM Replacement Parts
The Hidden Cost of Non-OEM Replacement Parts
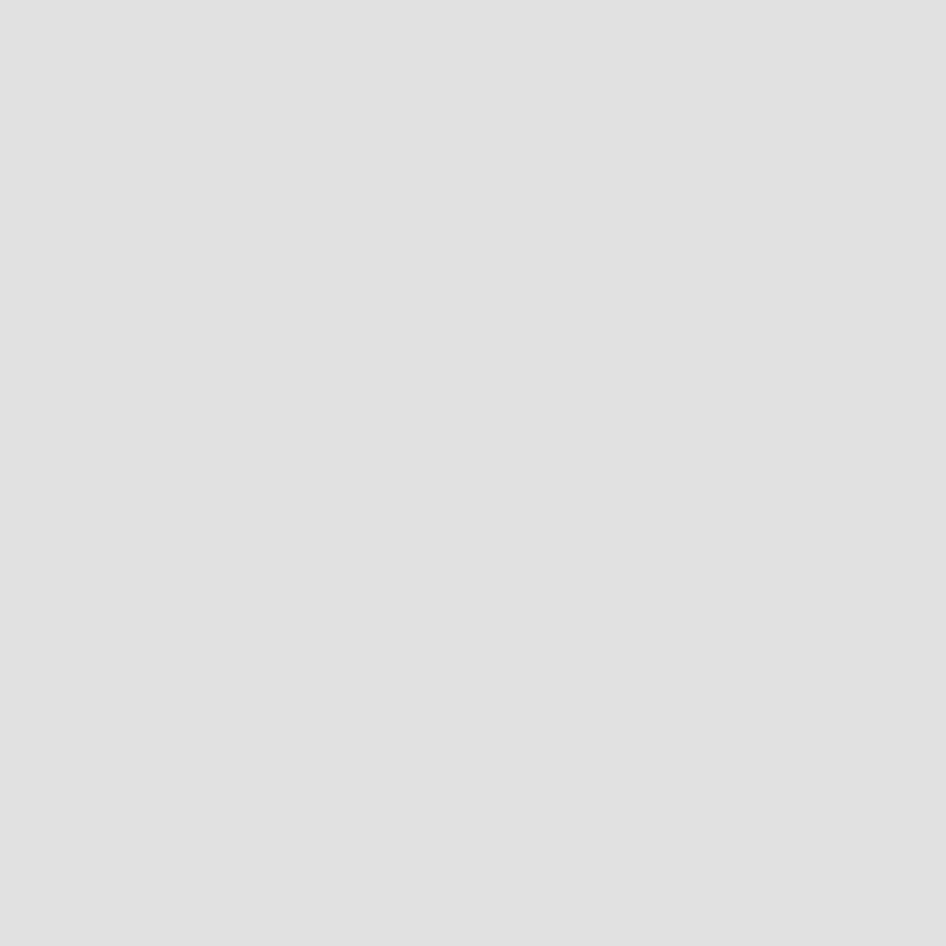
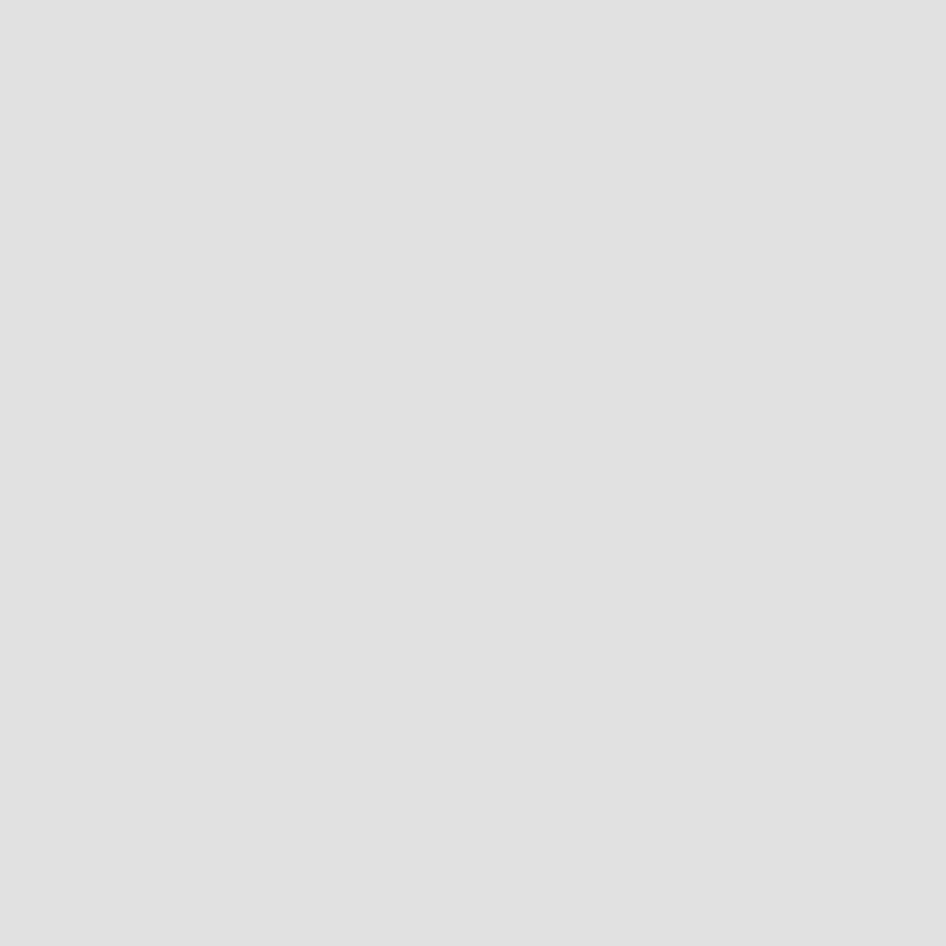
Costs of Non-OEM Replacement Parts
Cindy Lyneis
October 5, 2014
While it can be tempting to reduce short-term operational costs using non-original equipment manufacturer (OEM) parts, cutting corners can lead to crippling unplanned downtime and out-of-warranty equipment damage.
Read on for seven BIG reasons why every facility should be well-stocked with OEM-engineered replacement parts.
1. The true cost of ownership
While hidden costs are not obvious at the time of purchase, smart buying decisions account for the complete cost of ownership. OEM parts are designed to last and meet mean-time-between-failure expectations for preventive maintenance programs. They perform to specification, with no negative impact to ancillary parts.
2. Designed and tested not just to fit, but to function
All materials used in OEM parts satisfy requirements of high-friction applications in which parts interface with each other. Sure, there are some non-OEM parts that function without any apparent issues, but they may just be a ticking time bomb due to inferior build quality and hard-to-detect manufacturing imperfections.
3. The generic part may not be the same as the current OEM replacement
Operations cannot rely on non-OEM suppliers for the latest version of a replacement part. Through the life of equipment, OEM engineers make continuous design enhancements and produce updated iterations of replacement parts. OEMs send updates of new part modifications and availability to ensure enhanced performance and true lifecycle support.
4. Generic parts may come with a “warranty,” but it stops there
Some generic parts come with a warranty, but those are replacement only and do not cover damage caused to other system components. Furthermore, original system warranty compliance requires the use of authentic OEM parts to prevent damage to ancillary parts and systems – the use of generic parts may void the system manufacturer’s warranty.
5. The right part at the right time
The only thing worse than inferior parts is having no parts. When operations require a tight deadline to source a replacement, the OEM is well-prepared with installation information and order histories to instantly know operational needs.
6. Don’t risk an accident due to a poor performing non-OEM part
Faulty generic parts can compromise machinery and expose operations to safety risks. Exclusively stocking reliable OEM-warranted parts increases the facility safety and helps shield operations from costly litigation stemming from workplace injuries.
7. Access to the experts
Most OEMs have 24X7 technical support available to find the best possible solution and ensure that operations never take on a problem on their own. OEMs can assist in lifecycle planning and provide key information on “critical spares” to drive smart budgeting to control maintenance and labor costs.
For more information on the advantages of using genuine OEM spare parts, download the Intelligrated white paper, The Value of OEM Genuine Parts vs. the Cost of Generic Parts.
To subscribe to our blog and receive exclusive communications and updates from Honeywell Intelligrated, click here.
Let's Connect!
Sign up to receive exclusive communications from Honeywell including product updates, technical information, new offerings, events and news, surveys, special offers, and related topics via telephone, email, and other forms of electronic communication.
Copyright © 2025 Honeywell International Inc
Maximum File Size
Maximum Files Exceeded
Due to inactivity you will be logged out in 000 seconds.
Maximum File Size
Maximum Files Exceeded
You cannot access this page as this product is not available in your country.