-
Global
-
Africa
-
Asia Pacific
-
Europe
-
Latin America
-
Middle East
-
North America
- |
- Partners
- |
-
Currency:Localize your Content
You can set your preferred currency for this account.
Choose a Currency
Currency- CHOOSE YOUR CURRENCY
Update Currency
Changing Currency will cause your current cart to be deleted. Click OK to proceed.
To Keep your current cart, click CLOSE and then save your cart before changing currency.
-
Select Account
Switching accounts will update the product catalog available to you. When switching accounts, your current cart will not move to the new account you select. Your current cart will be available if you log back into this account again.
Account# Account Name City Zip/Post Code CANCELPROCEEDMy Account
-
Support
- View All Productivity Solutions
- Warranties
- Patents
- Global Locations
- Technical Support
- Discontinued Products
- Quality Program and Environmental Compliance
- Return Material Authorization (RMA)
- Legal Documents
- Product Certification
- Software Downloads
- Cyber Security Notifications
- Case Studies and Success Stories
- View All Sensing Solutions
- Sales Contact Form
- Technical Support
- Certificates
- eCOM Portal
- Distributor Inventory
- Return Material Authorization (Test & Measurement)
- Return Material Authorization (Citytech)
- Return Material Authorization (EnviteC)
- Legal Documents
- Intelligent Life Care
- Return Material Authorization (ILC)
-
Global
-
Africa
-
Asia Pacific
-
Europe
-
Latin America
-
Middle East
-
North America
- |
- Partners
- |
You are browsing the product catalog for
You are viewing the overview and resources for
- News & Events
- Featured stories
- Honeywell Operational Intelligence Revolutionizes IT Asset and Service Management
Honeywell Operational Intelligence Revolutionizes IT Asset and Service Management
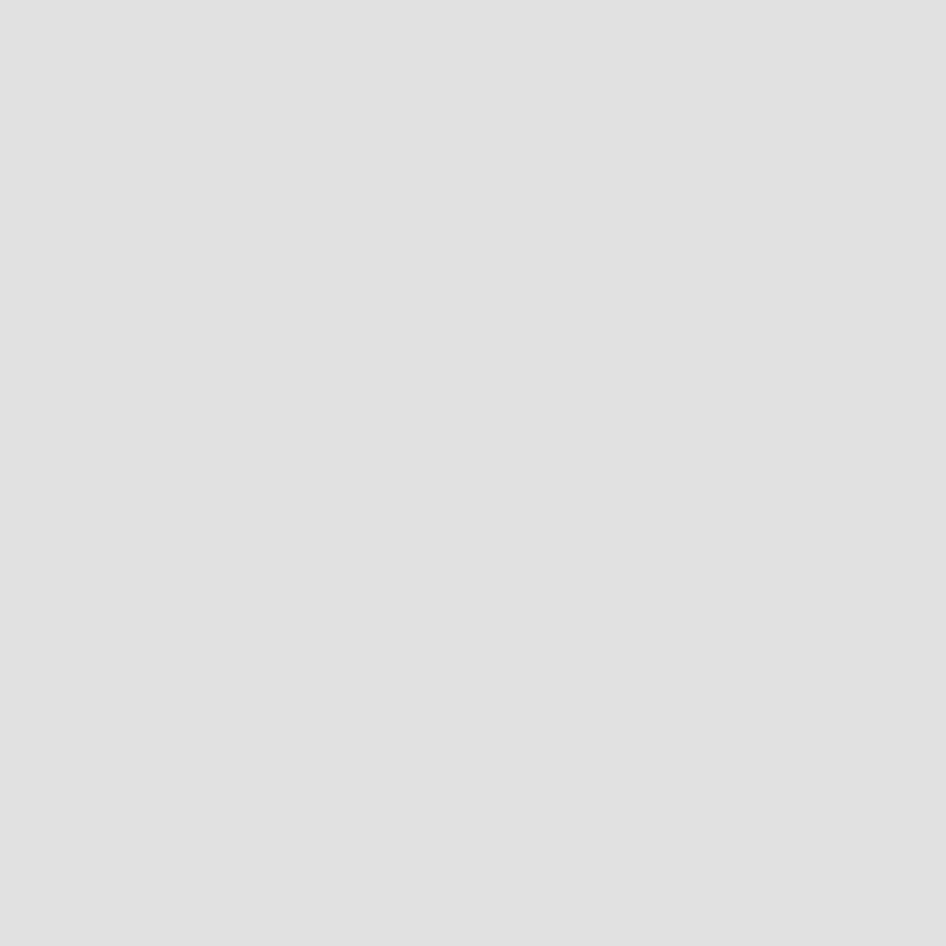
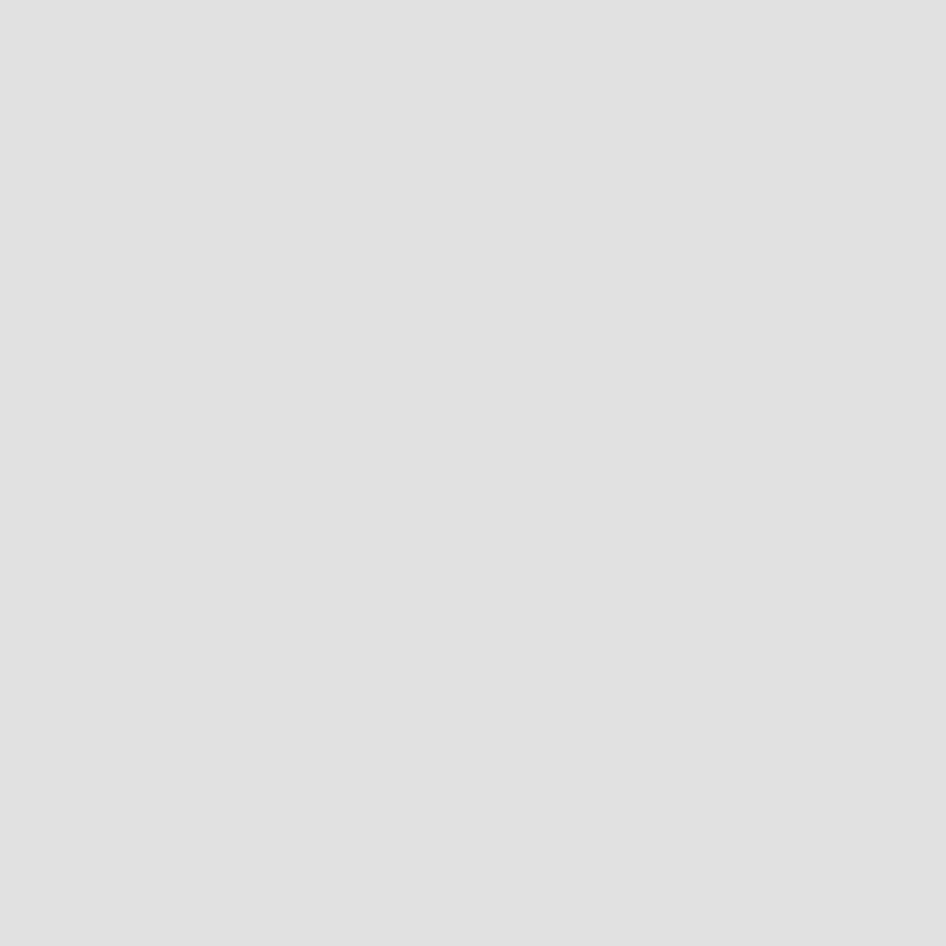
Honeywell Operational Intelligence Revolutionizes IT Asset and Service Management
Barry J. Ewell
November 14, 2019
Introduction
Across the supply chain, organizations deploy fleets of mobile devices made up of assets from multiple manufacturers – ruggedized mobile computers, tablets, barcode scanners, and printers. Each device comes with its own operating system, software, contracts, agreements, and repair processes that must be carefully managed. Many of these devices can collect rich telemetry and event data that can be used to provide actionable insights into how devices are used, how to decrease operational costs, and how to improve productivity. Sadly, organizations are challenged in accessing these insights because they are using separate tools and aggregating the information with spreadsheets and in-house developed tools.
At Honeywell, we believe in the power of intelligence and design products to give you more of it. We have heard our customers tell us that they need the ability to manage and optimize assets throughout their operational lifecycle across all locations. These needs include being able to address the following areas:
- Network Diagnostics. Identify weaknesses in network performance.
- Service Costs. Know service costs for shipping, spare pool rotation, return merchandise authorization (RMA) leakage (no fault found, abuse), and SLA breach recovery.
- Battery Analytics. Know your battery health, consumption profile on your devices, shift readiness, disruption events, charging and replenishment, and end-offline needs around batteries.
- Lifecycle Analytics. Know the current total cost of ownership and when you are reaching diminishing returns to support replacement, upgrade, and end-of-life decisions.
- Smart Alerts and Notifications. Shift from monitoring dashboards and reading reports to actionable information when it is needed.
- Smart Replenishment. Use inventory level and consumption rates to recommend or automatically order ideal quantities for media, printheads, print ribbons, and batteries.
- Enable Service Creation. Design and deliver services based on the data such as Managed Print Service and Service Center consolidation.
- Security and Compliance. Ensure that device firmware and software are at the proper versions to mitigate cyber risk.
- Worker Score/Behavior. Monitor, compare, and score workers for usage and productivity. Predict turnover and identify training needs through productivity insights.
- Device Health Score. Monitor and score device health to ensure equipment is operating optimally.
- Workflow Time Studies. Gain real-time continuous workflow time studies for jobs, leading to dynamic time-standard setting and continuous improvement.
- AI-Based Configuration Optimization. Machine learning on asset usage patterns and device utilization to automatically refine configuration settings to optimize performance and battery life.
Honeywell Operational Intelligence
Honeywell Operational Intelligence solves these needs and problems by providing IT and site leaders and services providers a centralized, cloud-based platform to manage the complete lifecycle of their assets. Operational Intelligence aggregates lifecycle and workflow information into a single flexible tool to capture data, enforce processes, and provide visibility across the entire device workflow for your heterogeneous environment. Operational Intelligence is also capable of communicating with Honeywell devices to gather deep metric and telemetry data; provide software, configuration, OS, and firmware updates to the devices; and track indoor device location.
Operational Intelligence is a powerful analysis software engine that provides dashboards to support your troubleshooting efforts. Over the last several years, Honeywell has been systematically adding powerful “self-analyzing” toolsets to all of our hardware products. These embedded tools are capable of methodically capturing hundreds of performance data points from our devices as they are being used in your operations. When this data is compiled and analyzed, it opens amazing insights into many problems common to AIDC technology users.
Operational Intelligence includes four modules to give you a robust tool to manage and optimize assets across your locations throughout the operational asset lifecycle. These include:
- Service Management: As a vendor-agnostic solution, systematically standardize, manage, and optimize the process of servicing your IT assets.
- Performance Management: Track, analyze, and report on the operational performance of your IT assets. Remotely download software and configurations.
- Configuration Management: Reduce time spent on individual device updates and security risks by keeping devices automatically updated.
- Worker Performance: Analyze worker performance and workflow efficiencies by tracking device and application use.
Service Management
Operational Intelligence is a vendor-agnostic solution that systematically standardizes, manages, and optimizes the process of servicing your IT assets. With the Service Management module, you can:
- Standardize Your IT Asset Database. Bring a consistent methodology to centralize the way you track and service your IT assets inventory across your operations. Consolidate and configure device lifecycle and RMA processes into one efficient system.
- Manage RMA and SLAs. Improve return and repair workflows by supporting your IT asset problem evaluation and repair processes. Receive real-time status updates on assets returned for repair. Track support contracts and verify vendor adherence to Service-Level Agreements (SLAs).
- Optimize IT Asset Inventory. Standardize and manage your device workflow in a centralized system. Use intelligent service reporting to improve business outcomes. “Right-size” your spare pool inventory and “right-place” your IT assets across sites.
Some of the module highlights include:
- All IT assets loaded in a single database by serial number
- Organizes your equipment list by model, type, location, and more
- Keeps track of asset warranty and service contract terms and renewal dates
- Tracks software version levels of your IT assets
- Standardizes the RMA process to eliminate No Trouble Found (NTF) and lost equipment
With Service Management, you can:
- Reduce missing hardware by knowing the location of your mobile devices
- Decrease unnecessary returns through a 25% reduction in No Fault Found (NFF) returns
- Improve profitability through reducing your RMAs by 50%
Building a case for service management
Effective mobile asset management is mission-critical for an organization’s operational lifecycle of each device. Beginning with requisition and procurement followed by deployment and maintenance through to its retirement, operational asset management involves a process.
Effective processes provide control, consistency, and accuracy that benchmark against specific goals and objectives. Per industry experts, when an organization chooses to onboard a well-defined and standardized operational asset management strategy, they will see as much as a 55% cost savings (30% in the first year, followed by 5% in each of the subsequent 5 years).
It’s the difference between being able to know versus guess about the operational lifecycle of your mobile device fleet.
Honeywell and industry research show that it is not uncommon for a company to have 10–30% of their devices either stolen or missing. Think about that. If you had 1,000 devices in your fleet, as many as 300 of them are gone. That is a very expensive proposition when you think of the cost of just one mobile asset.
There is a tremendous challenge of underutilized, unavailable, or mismanaged mobile assets, which brings great opportunities – and this is where Honeywell can help. What is your process for managing your mobile device assets lifecycle? Is your process based on a spreadsheet or operational asset management software or some combination thereof? How does your process stack up against industry best practices?
Remember, lifecycle is what you do; asset tracking records what you have done. Process is how you do it. Process is the foundation of asset management.
With Operational Intelligence, you will gain a well-defined and field-tested solution that provides:
- Well-defined processes to ensure efficient, consistent, and accurate execution of asset management tasks and activities. You gain a configurable RMA process workflow and overall workflow.
- Continuous process improvement to achieve greater levels of your mobile device visibility. You can improve processes based on historical workflow analysis.
- Effective tools that provide process support and automation. You will have a manufacturer-agnostic portal for guided workflow with integration to repair centers, shipping, and mobile device management (MDM) solutions for automation.
Minimizing the loss of mobile devices throughout their lifecycle
With Operational Intelligence, you can minimize the loss of mobile assets by:
- Assigning assets to unique departments and locations for accountability
- Identifying current or last-known location for each asset
- Receiving real-time status updates on assets returned for repair
Managing mobile device security, contracts, and usage throughout the lifecycle
It is not uncommon for a fleet of mobile devices to include assets from multiple manufacturers. Each device comes with its own OS/software, contracts, and agreements that must be carefully managed. Operational Intelligence helps you:
- Track vendor contracts and verify adherence to SLAs
- Verify adherence to RMA vendor contracts
- Manage lease agreements and renewals for financing terms
- Monitor usage utilization and software versions
Standardize, automate, and simplify processes throughout the lifecycle
Per Honeywell device service and repair center studies, about 25% of all returns are classified as No Fault Found (NFF), meaning that the device was in good working condition and did not need repairs.
These NFF devices come with a lot of hidden costs that include shipping, handling, labor, diagnostics, and more. The costs can average $75, which is charged back to the customer. Decisions need to be made to return the device to the customer or place it in the spare pool. Decreasing NFF returns increases productivity and profitability.
With Operational Intelligence, you can also create accountability to reduce unnecessary returns by standardizing the process. You are able to:
- Define self-service checklists
- Consolidate RMA processes into one efficient system
- Control corporate shipping methods
- Right-size spare device inventory
- Develop a vendor-agnostic portal
Performance Management
Operational Intelligence helps to dramatically reduce a huge blind spot that you have with not knowing what is happening to every device in your fleet. You can track, analyze, and report on the operational performance of your IT assets. Remotely download software and configurations. With the Performance Management module, you gain access to:
- Utilization Analytics. Engage with an integrated dashboard delivering key performance indicators that allows you to evaluate the health and utilization levels of your IT assets.
- Event Monitor/Usage Analytics. Manage real-time alarms and notifications generated by user-defined performance disruption events.
- Advanced Analytics. Track device location to reduce loss and inventory-count times. Analyze device drop and fall events to improve care and reduce wear for longer lifespan.
Some of the module highlights include:
- Automatically collects performance data from Honeywell devices such as mobile computers, printers, and barcode scanners
- Supports detailed device performance analysis dashboard including battery health
- Generates alerts and notifications of user-defined trigger events
- Advanced features like locationing (ability to track a mobile computer moving inside a building) and mobile computer drop detection
Analytics used for predictive device health and maintenance
All devices come with specifications that guide the user for optimal use and preventative maintenance to gain the longest life possible. Operational Intelligence gathers rich telemetry and event data and combines it with other disparate data sources to provide actionable insights on how the devices are used, how to decrease operational costs, and how to improve productivity. The following are some examples of the data that is collected from different devices and its value to you:
Honeywell mobile computers incorporating Operational Intelligence capture information about:
- Battery Health. A common problem with mobile IT assets is the batteries. Over time many customers complain that their batteries seem to not support a full day’s work and they don’t know if they need to purchase new batteries or simply do a better job fully charging the batteries that they have. Operational Intelligence opens the entire history and health of your mobile device batteries for full analysis, allowing you to correct charging procedures or locate and remove batteries past their useful life.
- Drop and Fall Drop Detection. Operational Intelligence has the unique ability to track and measure when Honeywell devices are dropped. Not only does it detect and log the drop event, but it captures the height of the fall or if the device may have been forcefully thrown on the floor or against a wall. This is powerful information when diagnosing damaged equipment and finding ways to prevent future equipment damage.
- Scanning. Scanning information such as scanned barcode volume can be a proxy for site productivity. For example, in the warehouse it can define the throughput of packages. In retail it could denote how your sales are doing.
- Operating System. Keeping track of the device OS and firmware versioning provides visibility into security vulnerabilities that can be used to keep security patches up-to-date to enforce compliance and mitigate risk.
- Applications. Many devices in the mobile computer space run custom applications. Operational Intelligence helps with monitoring these applications. You can understand how the user interacts with the application while performing their duties within the workflow. For example, support teams can be alerted when software issues arise or data can be sent back to the development team to assist with software improvements to make it easier for the end user to use the applications. This instance information can show if it is only happening on one device or is aggregated across all devices, indicating it is an issue with a specific software release.
Honeywell printers incorporating Operational Intelligence capture information about:
- Printheads. Printhead usage to detect faulty dots signifying when maintenance or replacement is required to reduce device outages. Also provides historical data that can be used to keep the printhead spare pool stocked to support usage trends.
- Labels and Media. The number of labels printed and how much label media has been printed from a linear meter perspective. By understanding how much is being printed and historical data, it can indicate when to provide preventative maintenance, such as replacing of printheads. When the printer is nearing the media/ribbon being out or some other issue that takes it offline, you can receive alerts allowing you to take proactive action to mitigate possible operational slowdowns.
- Printer Usage. Look across multiple printers and understand how they are being used. For example, do you have one printer that is doing 80% of the printing? Could you balance the load to other printers and thus extend the life of the printhead? Do you have enough printers to support the workload? Many organizations have printers that are unmanned. You can know when the printer is nearing or out of media and/or in need of maintenance, thus increasing printer performance and usage.
Configuration Management
Operational Intelligence reduces time spent on individual device updates and security risks by keeping devices automatically updated. This is possible because Operational Intelligence supports Honeywell’s Mobility Edge™ platform. With the Configuration Management module, you gain access to:
- Software Updates. Remotely update your IT assets’ operating system, firmware, and security software to reduce cybersecurity risks as well as time spent on individual device updates.
- Configuration Updates. Remotely configure your IT assets software systems and applications to be eligible for OS vendor standard support.
- Remote Control. Remotely troubleshoot device issues and test real-time configuration updates.
Some of the module highlights include:
- Pushing out new software updates
- Pushing out new device configuration files
- Remote device control to support advanced troubleshooting
Mobility Edge overview
Mobility Edge is based upon extensive research gathered from Honeywell’s global community of customers from a range of technologies. Honeywell recognized that businesses wanted a unified hardware and software platform for all form factors – one that allowed for rapid deployments, robust performance, and adaptability to changing needs.
We completely rethought our approach to meeting the challenges of supporting a mobile workforce, and Mobility Edge was the answer. This unified, dynamic platform for mobile computing is designed to:
- Accelerate deployments
- Optimize business performance
- Extend lifecycle
- Strengthen security
Honeywell Mobility Edge devices built on this common hardware and software platform are easier and less costly to deploy and manage and have longer lifecycles than similar competitive devices.
Mobility Edge devices feature a common hardware System On Module, or SOM, which is a single, certified module that includes the device’s CPU, memory, WWAN (in selected devices), WLAN, Bluetooth®, near-field communication (NFC), and Zigbee (in selected devices). They also feature a common OS software image and a common software ecosystem, which includes not only Honeywell software, but also software from Honeywell-approved independent software vendors (ISVs).
Having a common SOM and OS software image provides flexibility and reduces costs for businesses to deploy additional device form factors, because there are no added development or certification costs. Companies can validate all their mobile devices, use cases, and software once, and then deploy across multiple devices in multiple form factors, more rapidly and at a lower cost than typical mobile deployments.
Businesses wishing to extend product lifecycle and gain a better return on their technology investment will be assured by the fact that Mobility Edge platform devices can be upgraded through Android™ R. Honeywell also provides critical security updates for up to two years past Google’s last security patch through its Sentinel service, giving customers a product lifecycle through at least 2027.
Honeywell is deeply committed to the longevity and quality of the Mobility Edge platform. The current family of devices includes the CT40, CT60, CN80, CK65, and Thor™ VM1A, all running on Mobility Edge. More devices are in process for future release.
Worker Performance
Operational Intelligence analyzes worker performance and workflow efficiencies by tracking device and application use. With the Worker Performance module, you gain access to:
- Workforce Insights. Monitor, compare, and score your workforce through device usage and productivity to identify opportunities for continuous improvement.
- Worker Time Studies. Gain real-time metrics for each step of your job workflow to identify bottlenecks and create opportunities for process improvement.
- AI-Based Optimization. Machine learning on IT asset usage patterns to optimize performance.
Some of the module highlights include:
- Automatically collects device data and associates it to individual workers
- Data analysis tools for measuring worker behavior
- Supports creating worker time studies
- Artificial Intelligence–based analysis of processes and worker productivity
Workforce time studies drive workflow efficiency
Operational Intelligence allows your organization to collect a constant stream of device data that provides full visibility into workflow patterns. The main object of time study is to determine the proper time required to complete the job. Because the sample size can include every device, it makes root cause analysis easier and more accurate than sparse measurements and the potential for continuous improvement is immense. You can take worker skills into consideration, from veterans to new hires, and look for opportunities to improve process and provide one-on-one training across the team.
Accurate data leads to increased worker efficiency because workers are asked to follow correct methods, use proper tools, and eliminate wasteful motions. It helps in simplifying existing operations by laying the best sequence of essential operations, which leads to economy in labor and a reduction in fatigue.
AI-based optimization for continuous improvement
Operational Intelligence machine learning provides critical information to help managers make more informed business decisions. For example, machine learning helps with:
- Predictive Maintenance. Helps in the creation of highly efficient predictive maintenance plans. Following such predictive maintenance plans will minimize the chances of unexpected failures, thereby reducing unnecessary preventive maintenance activities.
- Workforce Planning. Machine learning can analyze warehouse processes and optimize the sending, receiving, storing, picking, and management of individual products.
Workforce insights guide solutions to everyday needs
Operational Intelligence is the perfect tool to get answers to questions that have likely have been mysteries to you in the past, such as:
- Which zones in my facility do my workers spend the most time in?
- Where are my traffic jams throughout the day?
- When I look at time, are my workers focused in one area of my facilities at one time and in other areas during other hours?
- How many zones are workers traveling per transaction?
- What are the seasonality impacts on my workloads and workflows?
- What additional information can I get for the cause of accidents, damaged inventory, and injury?
- What are the locations of my devices?
The simplicity of the Operational Intelligence approach to gathering insights is that you are already collecting data with the equipment in relation to barcode scanning. You enable the Operational Intelligence software to collect data, you know where your workers are, and the answers to your questions are revealed.
Conclusion
Honeywell Operational Intelligence is a cloud-based platform to manage the complete lifecycle of your assets. Operational Intelligence aggregates lifecycle and workflow information into a single, flexible tool to capture data, enforce processes, and provide visibility across the entire device workflow for your heterogeneous environment. Operational Intelligence is also capable of communicating with Honeywell devices to gather deep metric and telemetry data; provide software, configuration, OS, and firmware updates to the devices; and track indoor device location.
Operational Intelligence is a powerful analysis software engine that provides dashboards to support your troubleshooting efforts. At Honeywell, we believe in the power of intelligence and design products to give you more of it. That’s why we have been systematically adding powerful “self-analyzing” toolsets to all of our hardware products. These embedded tools we call “Edge Intelligence” are capable of methodically capturing hundreds of performance data points from our devices as they are being used in your operations. When this data is compiled and analyzed, it opens amazing insights into many problems common to AIDC technology users.
If you want to learn how Operational Intelligence can help you better manage your mobile assets, contact Honeywell today at https://www.honeywellaidc.com/solutions/workflow/operational-intelligence.
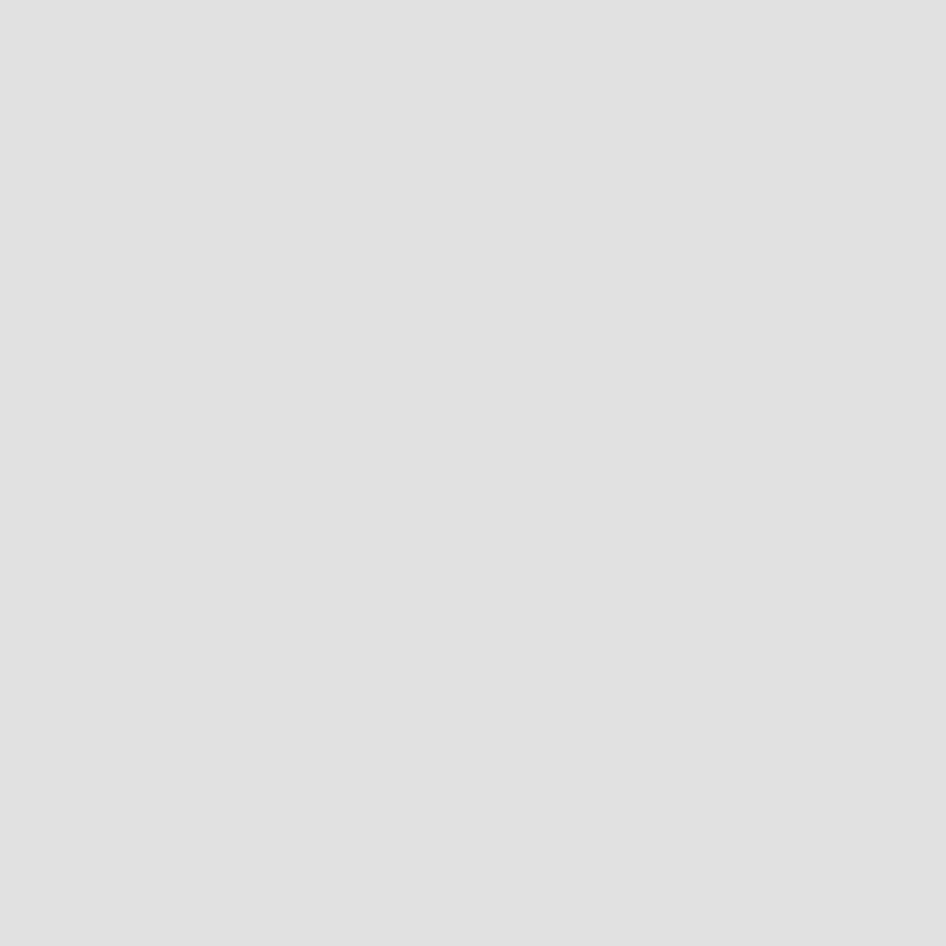
Barry J. Ewell is a Senior Content Marketing Communications Specialist for Honeywell Industrial Automation. He has been researching and writing on supply chain topics since 1991.
Let's Connect!
Sign up to receive exclusive communications from Honeywell including product updates, technical information, new offerings, events and news, surveys, special offers, and related topics via telephone, email, and other forms of electronic communication.
Copyright © 2025 Honeywell International Inc
Maximum File Size
Maximum Files Exceeded
Due to inactivity you will be logged out in 000 seconds.
Maximum File Size
Maximum Files Exceeded
You cannot access this page as this product is not available in your country.