-
Global
-
Africa
-
Asia Pacific
-
Europe
-
Latin America
-
Middle East
-
North America
- |
- Partners
- |
-
Currency:Localize your Content
You can set your preferred currency for this account.
Choose a Currency
Currency- CHOOSE YOUR CURRENCY
Update Currency
Changing Currency will cause your current cart to be deleted. Click OK to proceed.
To Keep your current cart, click CLOSE and then save your cart before changing currency.
-
Select Account
Switching accounts will update the product catalog available to you. When switching accounts, your current cart will not move to the new account you select. Your current cart will be available if you log back into this account again.
Account# Account Name City Zip/Post Code CANCELPROCEEDMy Account
-
Support
- View All Productivity Solutions
- Warranties
- Patents
- Global Locations
- Technical Support
- Discontinued Products
- Quality Program and Environmental Compliance
- Return Material Authorization (RMA)
- Legal Documents
- Product Certification
- Software Downloads
- Cyber Security Notifications
- Case Studies and Success Stories
- View All Sensing Solutions
- Sales Contact Form
- Technical Support
- Certificates
- eCOM Portal
- Distributor Inventory
- Return Material Authorization (Test & Measurement)
- Return Material Authorization (Citytech)
- Return Material Authorization (EnviteC)
- Legal Documents
- Intelligent Life Care
- Return Material Authorization (ILC)
-
Global
-
Africa
-
Asia Pacific
-
Europe
-
Latin America
-
Middle East
-
North America
- |
- Partners
- |
You are browsing the product catalog for
You are viewing the overview and resources for
- News & Events
- Featured stories
- Your DC Is Never Too Small for Voice: Honeywell Voice DC Walkthrough and Assessment
Your DC Is Never Too Small for Voice: Honeywell Voice DC Walkthrough and Assessment
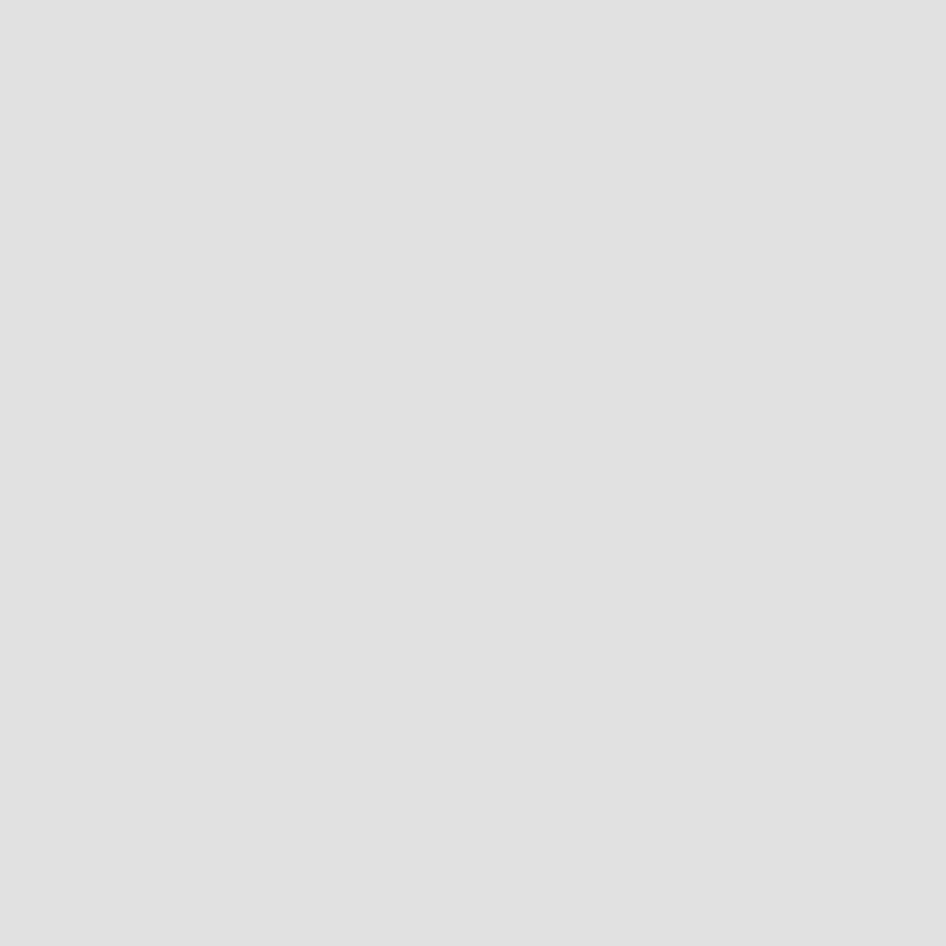
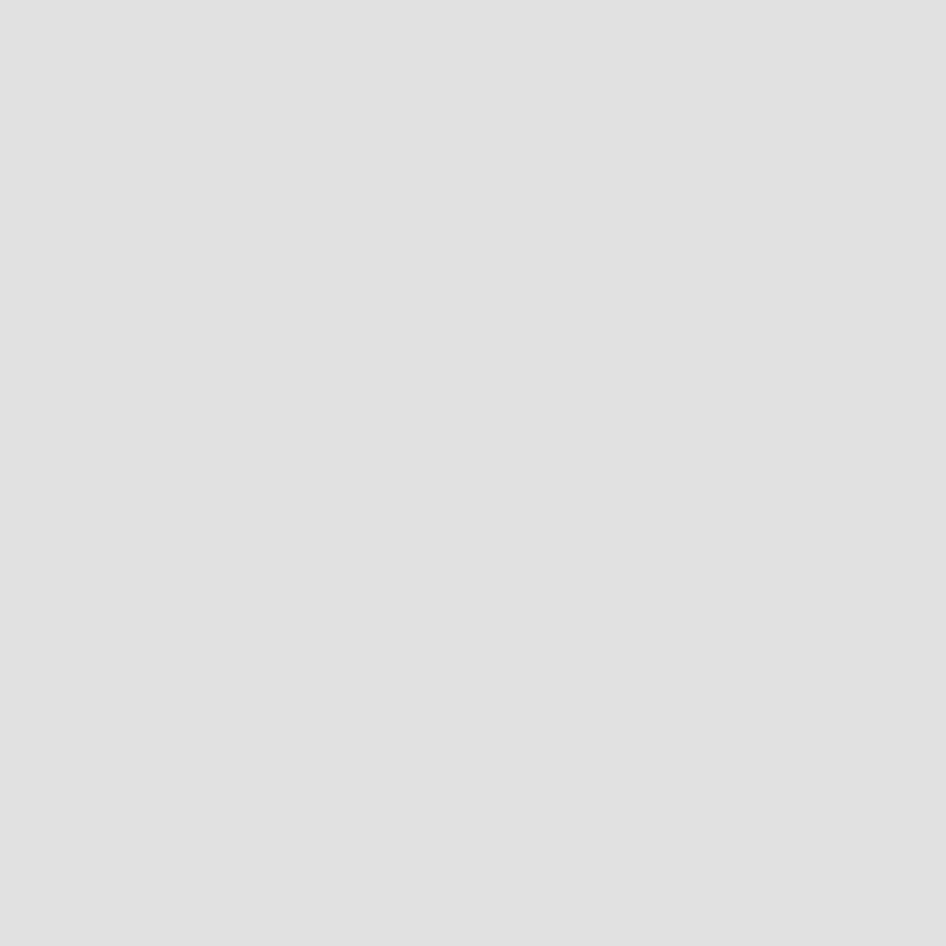
Your DC Is Never Too Small for Voice: Honeywell Voice DC Walkthrough and Assessment
Barry J. Ewell
February 12, 2020
Honeywell Voice works closely with each DC by conducting an assessment and walkthrough that seeks to understand their strategic business challenges, goals and processes.
The foundational needs for every company are different. For some, there are the needs to grow and win new business; for others, it is to meet governmental regulations. Whatever the reason, each DC assessment requires a fresh set of eyes. It’s about understanding why the organization needs to achieve their stated goals, such as improving productivity and increasing accuracy.
As part of the assessment, Honeywell Voice will conduct a 3–6-hour DC walkthrough. This is where our team will literally walk through the DC and engage with your managers, supervisors and workers to understand your DC processes from inbound to outbound. It’s a time for interaction, asking questions, and gaining clarity. From the walkthrough, we will identify and share our observations and opportunities for:
- Process improvements not related to voice
- Process improvements that could benefit from voice
- Process improvements enabled by voice
Improvement isn’t always about fixing something that’s broken. Sometimes it’s about making something good even better.
Every walkthrough is different. The Honeywell team comes with deep experience in understanding DC workflows, processes and voice applications. Observations and recommendations are unique to each facility. Our recommendations are based on DC best practices and Honeywell’s experience with our global ecosystem of DCs using voice technology to achieve desired results.
DC walkthrough video. During the walkthrough, we receive permission to video- record actual workers completing workflows such as picking. From the video, we are able to capture and visually analyze the workflow process that clearly shows efficiencies and mistakes not normally seen and timing for each step within the process. These observations form a foundation for helping Honeywell and the DC management team understand where opportunities exist for refining and achieving DC performance objectives.
DC Walkthrough and ROI Example
The following is an example of an actual DC assessment and walkthrough of a small- to medium-sized DC. Review and results follow.
DC profile:
- Type of DC: 3PL
- Industry: Shoe distribution
- Square footage: 100,000
- Priority workflow: Picking
- Number of employees in picking workflow: 15
Business challenges: The company stated the following business challenges:
- Increased KPIs: Increase picking KPI from 12,000 to 20,000 pairs of shoes per day.
- Customer service: Improve pick accuracy.
- Reduce operational costs: Workers earn double their pay due to overtime to meet increased KPIs.
Observations and process recommendations. During the walkthrough, the following items were found that could improve the picking process workflow:
Pallets
- Observation: Pallets with product were found blocking the aisles waiting for staging.
- Problem: There was reduced productivity because pickers needed to wait for a forklift to move the pallet.
- Recommendation: Designate an area for staging picked products.
Assignment/Label location
- Observation: Pickers went to a central location to retrieve their next picking assignment. All labels were printed out to designate the next pick container they were picking for.
- Problem: There was reduced productivity because each picker needed approximately 17.6 seconds to find labels. Additional headcount was needed to prepare and sort labels for the picker. In addition, accuracy was reduced when the wrong label was chosen by the picker.
- Recommendation: Print labels on demand, saving travel time to the desk, label search time and headcount for label sorting. Re-assign headcount for label sorting to more value-added work.
Mixed Sizes by Location
- Observation: Picker was presented with mixed sizes of a shoe model at a single location.
- Problem: The picker’s productivity was reduced when needing to search for the right shoe size. The average pick per location was 14.1 seconds. Accuracy was reduced by the chance of the picker choosing the wrong shoe size.
- Recommendation: Eliminate commingling of different shoe sizes. For each bin location, have one shoe model and one size. The average pick would be 3.2 seconds per location.
Shelf Space
- Observation: Shelf space was at a premium. There was wasted space for varying quantities of shoes. Multiple labels were present in one bin location.
- Problem: Reduced productivity in finding space to store stock levels, and increased chance for picking errors.
- Recommendation: Use moveable dividers. Easily change the size of locations by sliding the dividers to accommodate how much inventory was going into a specific location.
Pickers Reaching High Shelves
- Observation: Pickers were reaching high locations without proper equipment.
- Problem: Productivity was reduced because boxes had to be shifted onto a lower shelf so the picker could make a space to step to reach the higher levels. Picking times were double when reaching the third shelf. Safety was impacted by the chance of falling or a related injury.
- Recommendation: Use a cart that includes an attached stepladder. Reduces pick by 5–7 seconds. Trolley can carry more than one pick and reduces trips to packing by 50%.
Picking/Shipping Labels
- Observation: Shipping labels were hand-written. Information was identical to the pick label.
- Problem: Hand-writing labels slowed down the packing process.
- Recommendation: Combine labels into one label. Edit the Carton Mark format to include the NOC so that they can print on demand. This change can save approximately 29 seconds for each carton picked.
Paper/RF Scanners
- Observation: Paper and RF scanner are slow.
- Problem: In-hand paper pick instruction and RF device limit the productivity speed of workers. Key entry, laying down the device, and picking up the device equates to time lost. Reading/verifying details on paper draws a worker’s focus away from the task at hand and increases the chance for picking errors.
- Recommendation: Implement voice picking. This enables “hands-free, eyes-free” picking that improves productivity and reduces pick errors typically by 50–80%. Voice picking validates pick location with spoken check-digits and pick quantity/confirmation with spoken confirmation.
Picking Workflow Time/Motion Studies
Time/motion studies allow you to review the details behind the process and steps in a workflow. For this 3PL, we were able to look at their process for picking and apply average times to complete each step.
We looked at four versions of the picking workflow:
- Current picking workflow (paper/RF) and time to complete
- Current picking workflow and time to complete with Honeywell Voice
- Optimized picking workflow (paper/RF) incorporating Honeywell-recommended changes
- Optimized picking workflow incorporating Honeywell-recommended changes and Honeywell Voice
Current picking workflow (paper/RF). A total of 18 steps in the picking process used paper and RF to complete a pick assignment. Total time was 178.8 seconds.
Current picking workflow with Honeywell Voice. When voice was applied to the 18-step paper/RF workflow, the process was reduced to nine steps because steps were either combined and/or eliminated. Total time was 88.2 seconds. This is an estimated 50% time savings over paper/RF.
The following is the comparison between the two processes and associated time without Honeywell recommendations for optimizing the process:
Current Picking Workflow |
Time in Seconds to Complete Task |
Voice Being Applied to Current Picking Workflow |
Time in Seconds to Complete Task |
|
1 |
Pre-pick order prep |
27.0 |
Picker receives picking instruction (PI) via voice at carton box area |
4.8 |
2 |
Picker picks up PI and RF device |
18.0 |
Picker listens to location and travels to location |
32.0 |
3 |
Picker enters SI data to start picking |
5.5 |
Picker says, “check digit” |
1.2 |
4 |
Reads location |
2.7 |
Voice says, “quantity” |
0.9 |
5 |
Travels to location |
32.0 |
Finds shoe size to pick |
14.1 |
6 |
Reads bin label and checks with PI |
3.2 |
Picker picks quantity and confirms |
8.6 |
7 |
Reads PI |
3.2 |
Scans serial numbers |
23.0 |
8 |
Puts down RF device |
1.7 |
Scans carton barcode |
3.6 |
9 |
Finds shoe size to pick |
14.1 |
Sends carton to packing station |
|
10 |
Picks and puts into carton |
8.6 |
Total time to complete pick |
88.2 |
11 |
Writes PI number on carton |
19.3 |
||
12 |
Picks up RF device |
1.7 |
||
13 |
Enters pick data |
3.2 |
||
14 |
Scans serial numbers |
23.0 |
||
15 |
Scans carton barcode |
3.6 |
||
16 |
Puts down RF device |
1.7 |
||
17 |
Writes on PI sheet |
10.3 |
||
18 |
Sends carton to packing station |
|
||
Total time to complete pick |
178.8 |
Optimized current picking workflow with paper/RF. In this version of the picking process, Honeywell recommendations were incorporated, which reduced the process by three steps to 15 steps. Total time was 133.8 seconds. The optimized process using paper/RF was a 30% savings over the unoptimized workflow.
Optimized current picking workflow with Honeywell Voice. Based on best practices, when voice would be applied to the 15-step paper/RF workflow, the process was reduced to six steps. Total time to complete pick was 51.1 seconds. This was an estimated 40% time savings over the optimized paper/RF picking workflow and a 70% improvement over the unoptimized workflow.
The following is the comparison between the two processes and associated time that included the Honeywell recommendations for optimizing the process:
Optimized Workflow (Paper/RF) |
Time in Seconds to Complete Task |
Optimized Workflow With Honeywell Voice |
Time in Seconds to Complete Task |
|
1 |
Picker enters SI data to start picking |
5.5 |
Picker receives PI via voice at carton box area |
4.8 |
2 |
Reads location |
2.7 |
Picker listens to location and travels to location |
32.0 |
3 |
Travels to location |
32.0 |
Picker says, “check digit” |
1.2 |
4 |
Reads bin label and checks PI |
3.2 |
Voice says, “quantity and size” |
0.9 |
5 |
Reads PI |
3.2 |
Picker picks quantity and confirms |
8.6 |
6 |
Puts down RF device |
1.7 |
Scans carton barcode |
3.6 |
7 |
Finds shoe size to pick |
14.1 |
Sends carton to packing station |
|
8 |
Picks and puts into carton |
8.6 |
Total time to complete pick |
51.1 |
9 |
Writes PI number on carton |
19.3 |
||
10 |
Picks up RF device |
1.7 |
||
11 |
Enters pick data |
3.2 |
||
12 |
Scans serial numbers |
23.0 |
||
13 |
Scans carton barcode |
3.6 |
||
14 |
Puts down RF device |
1.7 |
||
15 |
Writes on PI sheet |
10.3 |
||
16 |
Sends carton to packing station |
|
||
Total time to complete pick |
133.8 |
Expanding the picking time/motion study to a five-line pick. Next, we expanded the time study to what it would take to complete a five-line pick. The pick was as follows: pick with five-line times; one bin, one model, one size; and scanning of serial numbers with move to packing.
- Current process vs. current process with voice. A five-line pick using the current process using paper/RF was 474.3 seconds. The five-line pick using the current process with voice was 315.4 seconds — a 33.5% improvement.
- Optimized current process vs. optimized current process with voice. In the optimized processes, the picking workflow included the Honeywell recommendations for process improvement. The five-line optimized pick using paper/RF was 519.3 seconds, which was actually a 9% increase in time over simply staying with the current process. The five-line pick using the optimized process with voice was 315.4 seconds — a 55.27% improvement.
Real-time management visibility. As part of the voice system, the 3PL gained real-time management visibility by:
- Viewing completed orders vs. open orders
- Monitoring workforce performance monitoring
- Seeing real-time updates on order completion to route completion
- Being able to prioritize urgent orders/routes
3PL Review and ROI. Upon completion of the assessment and walkthrough, Honeywell reviewed the findings with the executive team, focusing on how process improvements based on observations, best practices and the inclusion of Honeywell Voice can make a difference in the DC:
- Time savings from PI pick-up and return
- Time savings from PI preparation by supervisor
- Printer consumables cost savings
- Faster picking process from being hand-free and eyes-free
- Operator productivity and individual performance can be monitored easily
- Real-time monitoring on picking progress; urgent orders can be prioritized easily and monitored
Based on 15 users, the conservative productivity improvement was 30% with ROI in 23.8 months.
Conclusion
Honeywell Voice is used by nearly one million mobile workers every day, throughout the world, in a variety of tasks/workflows, in almost every kind and size of DC/warehouse operation. Honeywell Voice has been proven to increase productivity by up to 35% and accuracy to 99.99%+. For example, in picking processes where workers follow a series of instructions for specific pick locations, products and quantities, these tools provide needed guidance and verification at every step. Voice is available in more than 35 languages and has been proven to dramatically reduce training and onboarding time, especially in peak seasons with highly transient workforces.
Click here for more information about Honeywell Voice.
Our expert assessment teams will partner with you to understand your unique business requirements and identify where opportunities exist to optimize your workflows and increase efficiencies within today’s competitive climate.
At Honeywell, we work with thousands of distribution centers of all sizes, across a wide variety of industries worldwide. We bring a deep foundational understanding of the businesses we serve, backed with expert research and data that identifies the real, specific needs of today’s DCs.
With over 130 years of on-the-ground experience, Honeywell is uniquely equipped to help you solve the problems that your business faces every day, see improved results, and be a trusted partner to help you reach and exceed your predetermined goals.
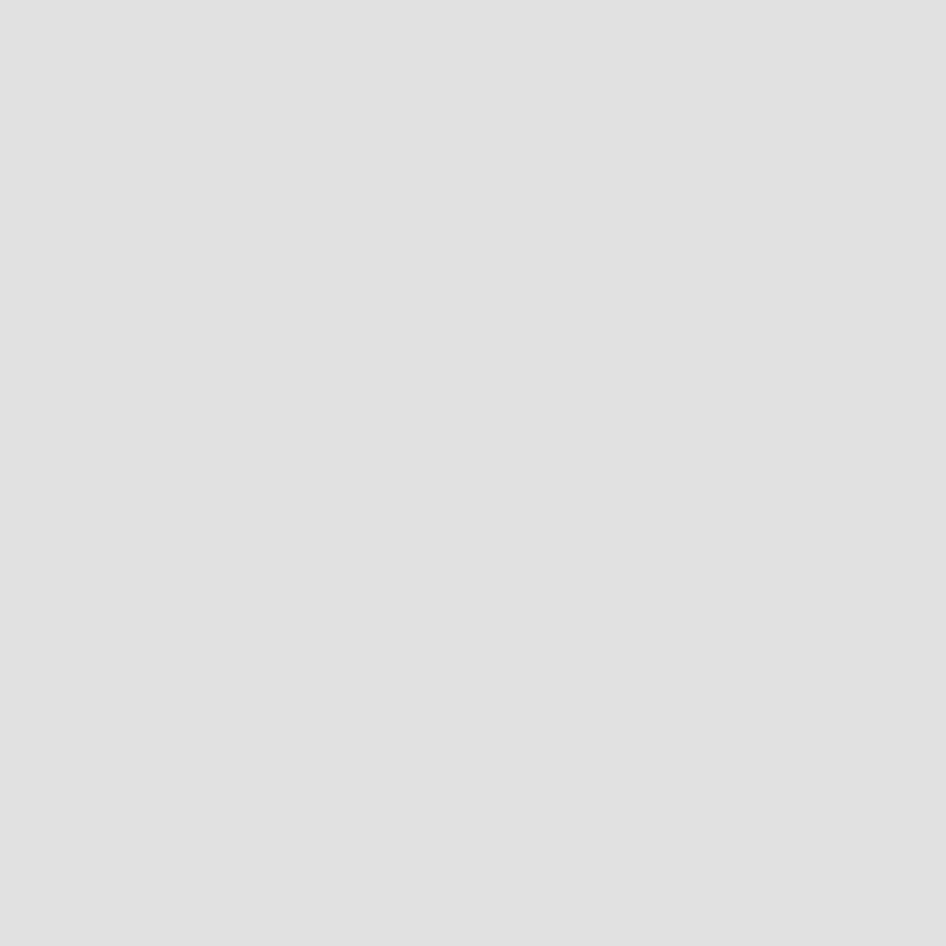
Barry J. Ewell is a Senior Content Marketing Communications Specialist for Honeywell Industrial Automation. He has been researching and writing on supply chain topics since 1991.
Let's Connect!
Sign up to receive exclusive communications from Honeywell including product updates, technical information, new offerings, events and news, surveys, special offers, and related topics via telephone, email, and other forms of electronic communication.
Copyright © 2025 Honeywell International Inc
Maximum File Size
Maximum Files Exceeded
Due to inactivity you will be logged out in 000 seconds.
Maximum File Size
Maximum Files Exceeded
You cannot access this page as this product is not available in your country.