-
Global
-
Africa
-
Asia Pacific
-
Europe
-
Latin America
-
Middle East
-
North America
- |
- Partners
- |
-
Currency:Localize your Content
You can set your preferred currency for this account.
Choose a Currency
Currency- CHOOSE YOUR CURRENCY
Update Currency
Changing Currency will cause your current cart to be deleted. Click OK to proceed.
To Keep your current cart, click CLOSE and then save your cart before changing currency.
-
Select Account
Switching accounts will update the product catalog available to you. When switching accounts, your current cart will not move to the new account you select. Your current cart will be available if you log back into this account again.
Account# Account Name City Zip/Post Code CANCELPROCEEDMy Account
-
Support
- View All Productivity Solutions
- Warranties
- Patents
- Global Locations
- Technical Support
- Discontinued Products
- Quality Program and Environmental Compliance
- Return Material Authorization (RMA)
- Legal Documents
- Product Certification
- Software Downloads
- Cyber Security Notifications
- Case Studies and Success Stories
- View All Sensing Solutions
- Sales Contact Form
- Technical Support
- Certificates
- eCOM Portal
- Distributor Inventory
- Return Material Authorization (Test & Measurement)
- Return Material Authorization (Citytech)
- Return Material Authorization (EnviteC)
- Legal Documents
- Intelligent Life Care
- Return Material Authorization (ILC)
-
Global
-
Africa
-
Asia Pacific
-
Europe
-
Latin America
-
Middle East
-
North America
- |
- Partners
- |
You are browsing the product catalog for
You are viewing the overview and resources for
- News & Events
- Featured stories
- How to Use Honeywell Voice Throughout the DC
How to Use Honeywell Voice Throughout the DC
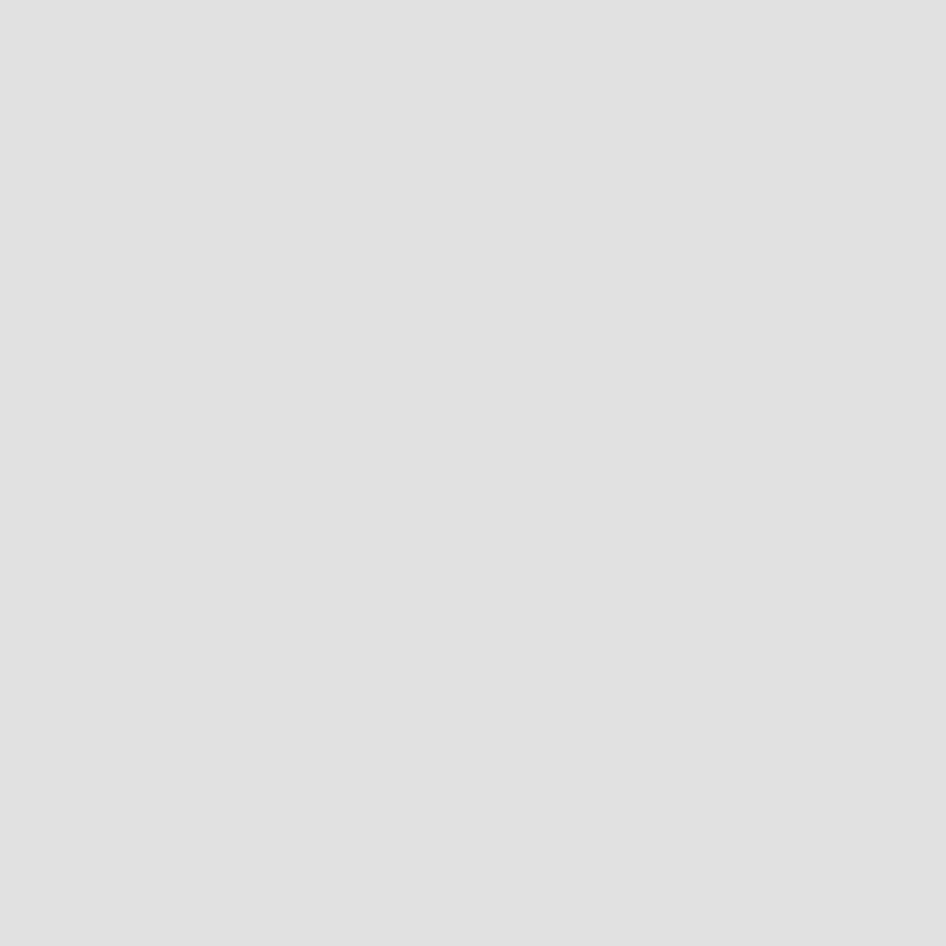
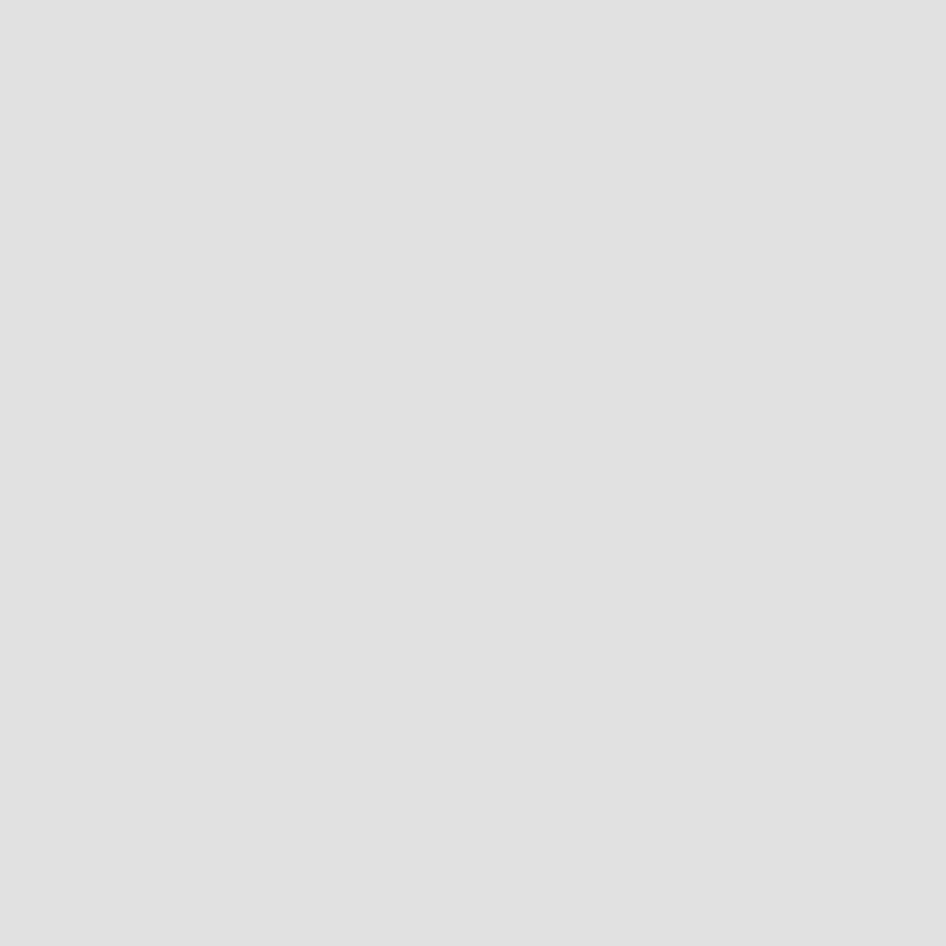
How to Use Honeywell Voice Throughout the DC
Barry J. Ewell
May 20, 2020
Businesses today face unrelenting pressures to reduce operating costs and to better manage their workforce, while continuously delivering perfect customer service. As a result, senior managers are looking for workforce operational improvements.
Honeywell Voice has become a catalyst in the re-engineering of distribution center processes and systems to deliver the next generation of business results. Honeywell Voice is the leading voice technology solution for operational excellence and is in use by almost one million mobile workers each and every day.
Why have our solutions become so popular? The answer is simple: Honeywell Voice delivers quantifiable worker productivity and accuracy gains and offers an elegant and flexible implementation approach to achieve improved business processes quickly. From a business perspective, our solutions have become so attractive because the investment typically has a payback in 9-12 months and your mobile workers appreciate being equipped to succeed in their job, boosting worker retention.
Honeywell Voice in Your Distribution Center
The addition of our solutions in your distribution center can generate performance gains in many areas. While voice technology initially was implemented mainly to enhance order fulfilment tasks, the performance benefits have resulted in a growing number of companies expanding their use of Voice into other areas of the distribution center, including receiving, put-away, loading and more. Voice provides an average of 10% to 25% productivity improvements, it’s no wonder why its adoption continues to gain popularity throughout various areas of the distribution center.
The exciting part for customers that expand their use of Honeywell Voice is that they are able to easily leverage their existing investment as they expand their voice usage. And our solutions also provide you various enterprise integration options to create the most flexible and effective IT infrastructure solution.
Case Picking. Make your mobile workers performing case picking even more productive with Voice. With their eyes focused on what’s ahead of them and not looking at a screen you’ll probably also experience a reduction in accidents.
Piece Picking. Piece picking mobile workers excel with Voice – you should expect to obtain up to 25% improvements in productivity because both hands are free and the voice commands streamline exception processing.
Pick to Tote. Pick-to-Tote roller feed operations are natural environments to use voice. You will see 15% gains in your piece pick per hour performance results and gain valuable insight on individual worker performance.
Gravity Feed Piece Picking. Workers performing piece picking in gravity feed environments see immediate improvements with voice. It supports using workers across zones in larger multi-zone layouts and reduces travel time dramatically when batch picking is implemented.
Carousel Line Loading. Voice enabling your line loading activities is a quick way to improve worker productivity. Workers can build pallets and process customized instructions more effectively using voice than other technology options.
Batch Picking. Picking multiple orders with Voice using pull carts greatly helps reduce your total travel time and provides exceptional gains in worker throughput.
Trolley / Pull Cart Picking. Voice excels at supporting pull trolley cages and delivering exceptional performance gains while offering workers the comfort of Voice leading wired or wireless headsets optimized for the distribution center.
In the Freezer. Voice’s market breakout occurred due to its ability to work in a variety of operating environments, including the freezer. Our voice-enabled mobile devices and batteries are quality tested and rated to support more than a full shift in extreme conditions.
Product Traceability. Specialty or high-valued items often require secondary data capture such as UPC, lot, serial, expiration date, best before date, batch, manufacture date, firmware version, cure date, etc. Voice is used by many customers to help ensure a seamless process that captures data quickly, reliably and consistently.
Put-to-Store / Flow-Through. Voice offers excellent worker productivity performance gains for workers using put-to-store and flow-through staging to break full pallets or cases into store-level orders without storing incoming products.
Put-to-Store (Apparel). Voice out performs traditional methods for piece pick apparel products. Not only does having both hands free help create a more positive worker experience, it also greatly improves overall throughput by being able to help reduce wasteful dead head travel time with reverse picking paths.
Catch Weights. Whether you call it catch-weight or random weight, Voice can support the capture of the exact packaging unit weight during the picking process to help ensure that the box is properly priced by its weight unit (lbs or kgs) without having to weigh the orders.
Receiving. The ability to easily pair workers using Voice with workers with ring scanners and portable printers for missing LPN labels makes receiving an excellent opportunity to streamline processes. Working extremely well with RFID-enabled receiving dock facilities, makes receiving our second fastest growing voice-enabled solution in the warehouse.
Put-Away. The put-away function has always been one of those tasks that challenges your team as they position older stock with newer stock. Voice enables workers to operate with both hands, as well as providing them sufficient vehicle mobility.
Stocking / Replenishment. Stocking/Replenishing your inventory is another traditional use of Voice t. The ability for the worker to stay focused on where they are going by listening to their directions will help ensure greater bin and slot location replenishment accuracy.
Supporting Narrow Aisle & High Reach Trucks. Voice-enabling your workers in narrow aisles and on high reach vehicles creates additional ways to better leverage your existing Voice investment throughout your facility.
Transferring. Transferring stock is another traditional use of Voice. This function can be interleaved with put-to-store, replenishment and back-stocking tasks.
Cross-Docking. Cross-docking is a growing logistics practice to rapidly consolidate shipments from disparate sources and realize economies of scale in outbound transportation. Voice-enabling this task is becoming more prominent each year as more customers leverage a hybrid model of using voice with scanning to help increase worker productivity and reduce data entry errors.
Internet Store & Packing Station. Meeting the explosive growth of consumer direct item orders from Internet orders has become the fastest growing application of Voice. When combined with the Voice Packing Station workflow task, you’ll eliminate up to 50% of the steps it takes to pack an order and you will reduce the time each order takes to complete up to 20%.
Audit & Quality Control. Your increase in accuracy will positively impact your overall quality and auditing results. Voice can also be used to validate products during receipt (using your ASN information) and shipment. Your observations around potentially damaged products also can be captured.
Cycle-Counting & Physical Inventory. Voice can easily interleave cycle-counting and physical inventory with other work assignments to maximize your worker efficiency and to aid in overall worker productivity, without the need to add a scanning step to the workflow process.
Loading. Your fork truck operators can even leverage Voice to help improve their order loading activities. The ability for managers to split large orders amongst other workers helps ensure you can meet those tight order shipment windows from staging to shipping.
Pick to Load. Your workers can even leverage Voice to direct load a picked order and eliminate the traditional staging step.
Shipping Manifests. The Voice Packing Station workflow task frees hands and seamlessly works with your scales and supports your existing integration with major parcel delivery services and LTL providers.
Improved Accuracy. Increased Productivity. Real Business Results.
Honeywell is a leading provider of innovative voice technology solutions, helping companies with mobile workers run a better business with voice. Every day, our Honeywell Voice solutions enable over one million global mobile workers to move $Billions of goods and annually saves companies millions.
Honeywell Voice enables companies to further help optimize operations, improve business decision capabilities, and deliver the industry’s premier worker experience in challenging industrial environments. Honeywell Voice t integrates with all major WMS, ERP, material handling systems and maintenance & inspection systems and supports the industry’s leading mobile computing devices.
Contact a Honeywell Solutions Expert today! Call 1-800-934-3163.
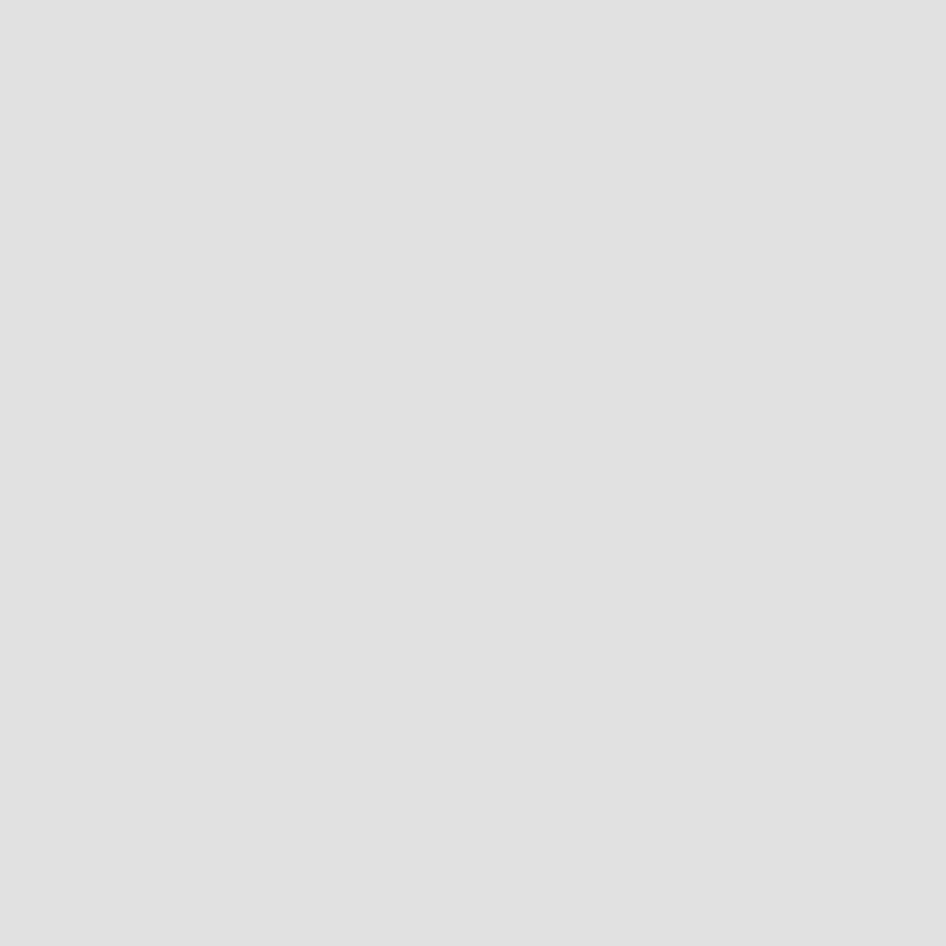
Barry J. Ewell is a Senior Content Marketing Communications Specialist for Honeywell Industrial Automation. He has been researching and writing on supply chain topics since 1991.
Let's Connect!
Sign up to receive exclusive communications from Honeywell including product updates, technical information, new offerings, events and news, surveys, special offers, and related topics via telephone, email, and other forms of electronic communication.
Copyright © 2025 Honeywell International Inc
Maximum File Size
Maximum Files Exceeded
Due to inactivity you will be logged out in 000 seconds.
Maximum File Size
Maximum Files Exceeded
You cannot access this page as this product is not available in your country.