-
Global
-
Africa
-
Asia Pacific
-
Europe
-
Latin America
-
Middle East
-
North America
- |
- Partners
- |
-
Currency:Localize your Content
You can set your preferred currency for this account.
Choose a Currency
Currency- CHOOSE YOUR CURRENCY
Update Currency
Changing Currency will cause your current cart to be deleted. Click OK to proceed.
To Keep your current cart, click CLOSE and then save your cart before changing currency.
-
Select Account
Switching accounts will update the product catalog available to you. When switching accounts, your current cart will not move to the new account you select. Your current cart will be available if you log back into this account again.
Account# Account Name City Zip/Post Code CANCELPROCEEDMy Account
-
Support
- View All Productivity Solutions
- Warranties
- Patents
- Global Locations
- Technical Support
- Discontinued Products
- Quality Program and Environmental Compliance
- Return Material Authorization (RMA)
- Legal Documents
- Product Certification
- Software Downloads
- Cyber Security Notifications
- Case Studies and Success Stories
- View All Sensing Solutions
- Sales Contact Form
- Technical Support
- Certificates
- eCOM Portal
- Distributor Inventory
- Return Material Authorization (Test & Measurement)
- Return Material Authorization (Citytech)
- Return Material Authorization (EnviteC)
- Legal Documents
- Intelligent Life Care
- Return Material Authorization (ILC)
-
Global
-
Africa
-
Asia Pacific
-
Europe
-
Latin America
-
Middle East
-
North America
- |
- Partners
- |
You are browsing the product catalog for
You are viewing the overview and resources for
- News & Events
- Featured stories
- What Is the Future of Voice-Directed Applications?
What Is the Future of Voice-Directed Applications?
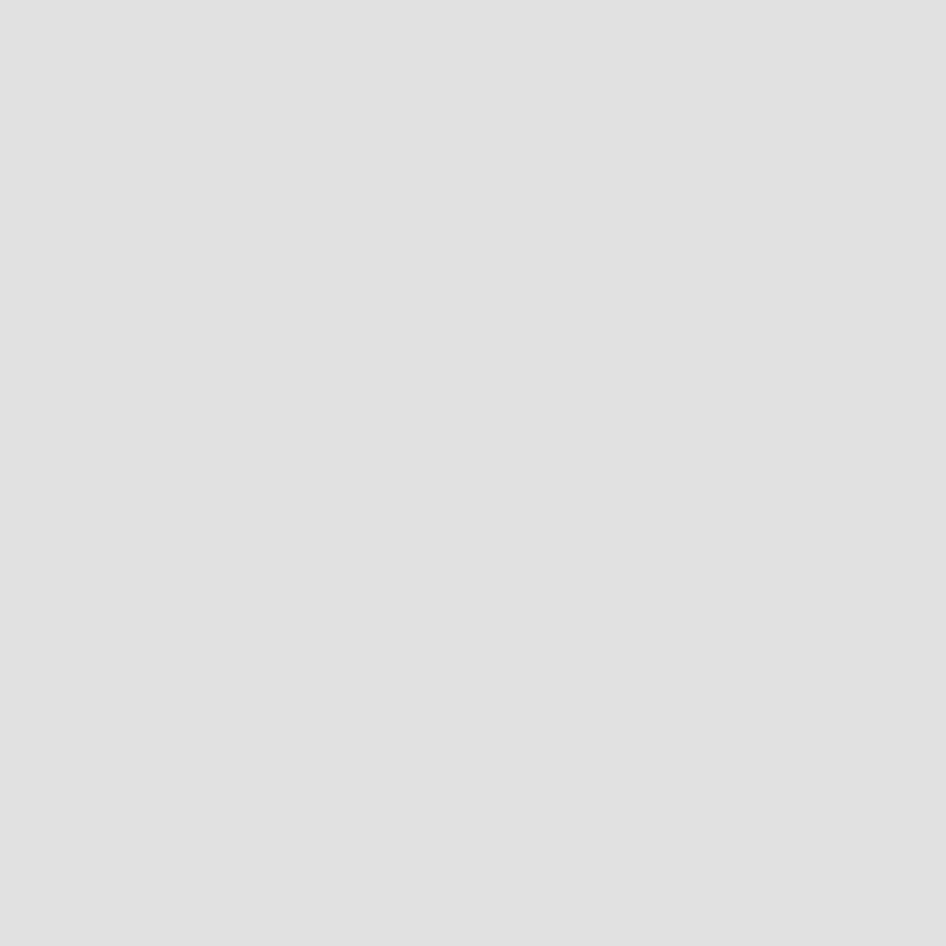
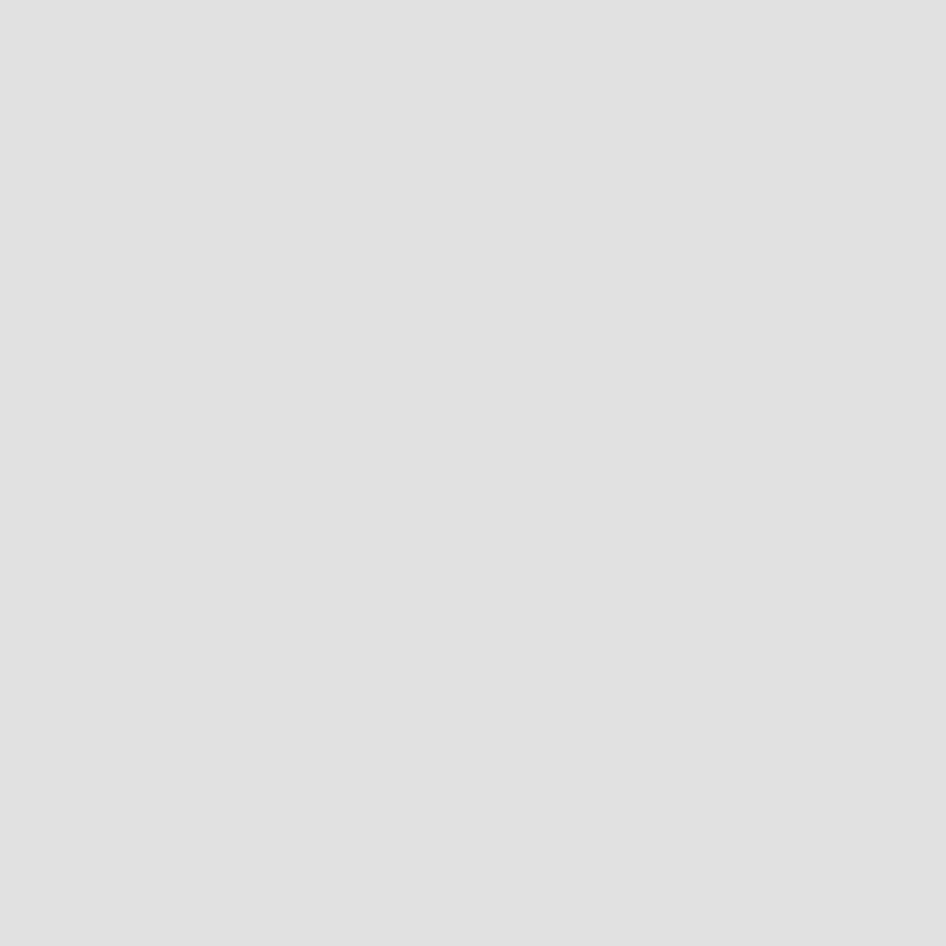
What Is the Future of Voice-Directed Applications?
Barry J. Ewell
November 21, 2019
Recently, a colleague of mine, Whitney Ellis, and I had the opportunity to interview James Hendrickson, Director of Product Management, Honeywell Voice and get his thoughts on voice technology as it relates to a wide variety of topics including ecommerce, technology, voice-picking, and more. If you have ever had the chance to listen to James in a webinar, interview with the press, or authored material, you quickly recognize that you are with someone who has a deep passion for voice technology and its ability to improve the operations and lives of mobile workers.
I have been fortunate to work closely with James on a couple projects and have always been “impressed” with the man, his knowledge, and love for what he does every day. Getting time with him can be a bit challenging. Here is what he had to say…
The growth in online shopping is putting more and more pressure on the picking process – what are the critical challenges that result from this?
Accuracy is king. Consumers expect a seamless and flawless online shopping experience. Anything less than perfect – from a poor customer experience to a cumbersome returns process – reflects negatively on the business and can prove costly. Typically, businesses only look at the acute problem and select a solution to help resolve that one issue. However, to achieve the best results, it’s important to take a holistic look at the business’s entire operation, including put-away, restocking, and let down too, and in turn consider applying scalable and flexible technology solutions in multiple areas. Selecting adaptable technologies that can grow alongside their ecommerce operations such as robotics – not necessarily full automation, but pairing it with another solution such as voice technology – can contribute to the establishment of best-in-class processes and workflows.
Which technologies are most suited to meet future needs: voice, automation, robotics, pick to light, etc.?
There is no one right answer – businesses should look at technology and their investment in it from a best-in-breed/best-in-class perspective. The more accurate question may be “What is the best technology or technologies that will help their business grow in today’s competitive marketplace?” A business should look at their requirements or the challenge they are trying to solve, such as loss of worker productivity or decreases in picking accuracy. Based on this they should select the technology that resolves those issues, which may include some that they were previously unaware of. Businesses can’t afford to blindly apply certain technologies over others because of preference, and the best way to ensure that does not happen is to partner with a trusted vendor that understands their business challenges and offers solutions that help in the short and long term.
There is always a trade-off between efficiency and flexibility, but is there a sweet spot that companies should be aiming for?
There are some trade-offs. Efficiency, for example, could look like a fully automated robotic environment; however, that typically does not offer much flexibility. So, when selecting technology that can solve your business challenges, it’s important to make sure you are choosing technologies that give your workers the best tools for success. Voice technology provides a simple and straightforward training template to rapidly get workers up and running in the DC – ensuring that the mobile worker is equipped to succeed from day one. At the same time, the mobile worker that is utilizing this voice technology can continue to interface naturally with robotics in the DC (i.e., Cobots or co-robots, which are robots intended to interact with humans in a shared workspace) in ways that other technology solutions simply cannot.
There are ROI implications for all the options – how do the different technologies compare?
No business is going to invest in something that does not have a clear return on investment. Some investments in technology have a longer payback, as is the case when fully automating your DC operations. What is more significant for businesses today is the total cost of ownership, or TCO. Businesses must partner with a trusted vendor that can help them assess their technology requirements as well as fully outline the initial and long-term costs for such investments. Are these businesses just looking at the cost of automation without considering the maintenance costs down the road? What if they are looking to employ a bring-your-own-device program into their DC, which is a rugged environment? Are there implications to that strategy? There are significant cost implications to investing in new technology, so selecting the right partnerships for DC operations is just as critical as the selection of the technology itself.
Looking ahead, what are the innovations that are set to become “must-have” technologies for order picking?
For Honeywell, the bigger questions are “How is technology applied within the DC?” and “How does the application of technology interact with mobile workers?” Honeywell sees the application of technology as an opportunity to impact DC operations while supporting the day-to-day responsibilities of mobile workers and the tasks that they do best. So, while we will continue to see a deeper and more seamless integration of technology throughout the DC, what we should focus on is the application of that technology to complement the mobile workforce – for example, pairing robotics with voice technology to help eliminate travel time for the mobile worker. In this case, the worker remains stationary while the robot is constantly traveling to retrieve items and deliver them to the worker at a central location, making the environment safer and more efficient for both the worker and others in the DC.
Voice-Picking in the DC
I would like to change direction and have you talk about voice-picking in the DC. How are SKU proliferation trends affecting warehouse operations?
The increase of SKUs in warehouse operations can prove to be challenging as businesses continue to learn about what their customers want in terms of products and how they work to meet those requirements. Through it all warehouse operations must maintain their flexibility to manage this growth and accuracy as they pick, pack, ship, and receive.
For example, increasing inventory of a specific type of product from five SKUs to 20 SKUs naturally can have an impact on how warehouse operations manage this growth. Having a flexible solution – like voice-picking technology – can help to make the transition to larger SKU volume more manageable. Additionally, SKU proliferation requires that warehouse operations maintain or improve their accuracy. Today, the supply chain is expected to deliver a seamless and flawless experience at all points in the value chain. Anything less than perfect – from a poor customer experience to delays in shipping or processing to a cumbersome returns process – reflects negatively on the business and can prove costly. Adding additional SKUs to a warehouse only compounds this as more and more products become available in one DC location.
What market trends are impacting warehouse operations and are they industry-specific?
Regardless of industry, these are the trends that we see impacting warehouse operations. They include incorporation of machine learning, increased responsiveness and turnaround times for last-minute orders, developing seamless interfaces with WMS systems and other technology suppliers, and additional incorporation of robotics and automation. When it comes to adapting to these trends it’s important to take a holistic look at the business’s entire operation and in turn consider applying scalable and flexible technology solutions in multiple areas. Selecting adaptable technologies that can grow alongside their DC operations such as robotics – not necessarily full automation, but pairing it with another solution such as voice technology – can contribute to the establishment of best-in-class processes and workflows.
How are solutions like voice-picking technology working in conjunction with these trends?
For Honeywell, the bigger questions are “How is technology applied within the DC?” and “How does the application of technology interact with mobile workers?” Honeywell sees the application of technology as an opportunity to impact DC operations while supporting the day-to-day responsibilities of mobile workers and the tasks that they do best. So, while we will continue to see a deeper and more seamless integration of technology throughout the DC, what we should focus on is the application of that technology to complement the mobile workforce.
The mobile worker that is utilizing this voice technology can continue to interface naturally with robotics in the DC (i.e., Cobots or co-robots, which are robots intended to interact with humans in a shared workspace) in ways that other technology solutions simply cannot. For example, pairing robotics with voice technology to help eliminate travel time for the mobile worker. In this case, the worker remains stationary while the robot is constantly traveling to retrieve items and deliver them to the worker at a central location, making the environment safer and more efficient for both the worker and others in the DC.
What is the learning curve for warehouse employees and voice-picking?
Voice workers typically require very little training or onboarding because the system guides them through the process. Voice technology provides a simple and straightforward training template to rapidly get workers up and running in the DC – ensuring that the mobile worker is equipped to succeed from day one. For example, Honeywell Voice offers “Pick Up and Go” technology that eliminates training and enables the mobile worker to simply pick up our Honeywell A700X device and begin their work. Not only does this efficiency help mobile workers in any DC environment, but it also helps DC operations managers that are responsible for hiring temporary or seasonal workers. Additionally, all Honeywell Voice devices and headsets utilize TouchConnect™ for seamlessly pairing a Honeywell mobile computing device and Bluetooth® wireless headset – reducing shift start-up processes from minutes to seconds.
What is the ROI for voice-picking technology?
No business is going to invest in something that does not have a clear return on investment. Some investments in technology have a shorter payback, as is the case when implementing voice-picking into DC operations. What is more significant for businesses today is the total cost of ownership, or TCO. Businesses must partner with a trusted vendor that can help them assess their technology requirements as well as fully outline the initial and long-term costs for such investments. Are these businesses just looking at the cost of automation without considering the maintenance costs down the road? What if they are looking to employ a bring-your-own-device program into their DC, which is a rugged environment? Are there implications to that strategy? There are significant cost implications to investing in new technology, so selecting the right partnerships for DC operations is just as critical as the selection of the technology itself.
How does this compare to other material handling solutions?
If a business can automate material handling, then that should be a serious consideration; however, for warehouse environments that have automation and mobile workers it is critical to enable them with the tools that help them succeed in terms of productivity, accuracy, and efficiency when compared to automation.
What improvements have been applied to voice-picking technology?
While voice technology may be viewed as mature technology used by many companies worldwide, there are continual improvements made in this segment – from investments in technology that leverage deep neural networks, or DNN, to hardware that can perform in varying yet extreme environments, and software that is designed to support operations today and future growth.
For example, Honeywell Voice technology continues to focus on areas such as processor speed, operating system, “Pick Up and Go” speech recognition technology, and built-in sensors for better data capturing. These features are designed for faster start-up times, more reliable performance, and greater accuracy – directly impacting the day-to-day success of the mobile worker.
What solutions do you provide in relation to voice-picking?
Honeywell Voice is well established in standard warehouse picking, but in recent years with the rise of ecommerce, our voice technology can be applied to other areas and workflows within and outside the DC. For example, additional workflows where voice technology is applicable include multiple picking, pick and pack, replenishment, and restocking. Voice technology is all about accuracy and that accuracy does not have to be limited just to picking items. Honeywell Voice can also be applied to inspection and checklist operations as well as applications within retail environments.
What is on the horizon for voice-picking technology and the beverage market?
The biggest benefit of voice technology to the beverage market is the ability for mobile workers to have their hands free to do full case picking. Holding a device is a cumbersome option in this scenario. And voice technology has clearly helped in this area over the years. So, what is next ties back into what was mentioned earlier – expanding into other workflows like replenishment, restocking, pick and pack – and continuing to integrate seamlessly with other emerging technology trends like vision picking, augmented reality, and robotics. Those latter trends when tied to the mobile worker create a true “Cobot” experience within the DC.
Conclusion
Click here for more information about Honeywell Voice.
Our expert assessment teams will partner with you to understand your unique business requirements and identify where opportunities exist to optimize your workflows and increase efficiencies within today’s competitive climate.
At Honeywell, we work with thousands of distribution centers of all sizes, across a wide variety of industries worldwide. We bring a deep foundational understanding of the businesses we serve, backed with expert research and data that identifies the real, specific needs of today’s DC.
With over 130 years of on-the-ground experience, Honeywell is uniquely equipped to help you solve the problems that your business faces every day, see improved results, and be a trusted partner to help you reach and exceed your predetermined goals.
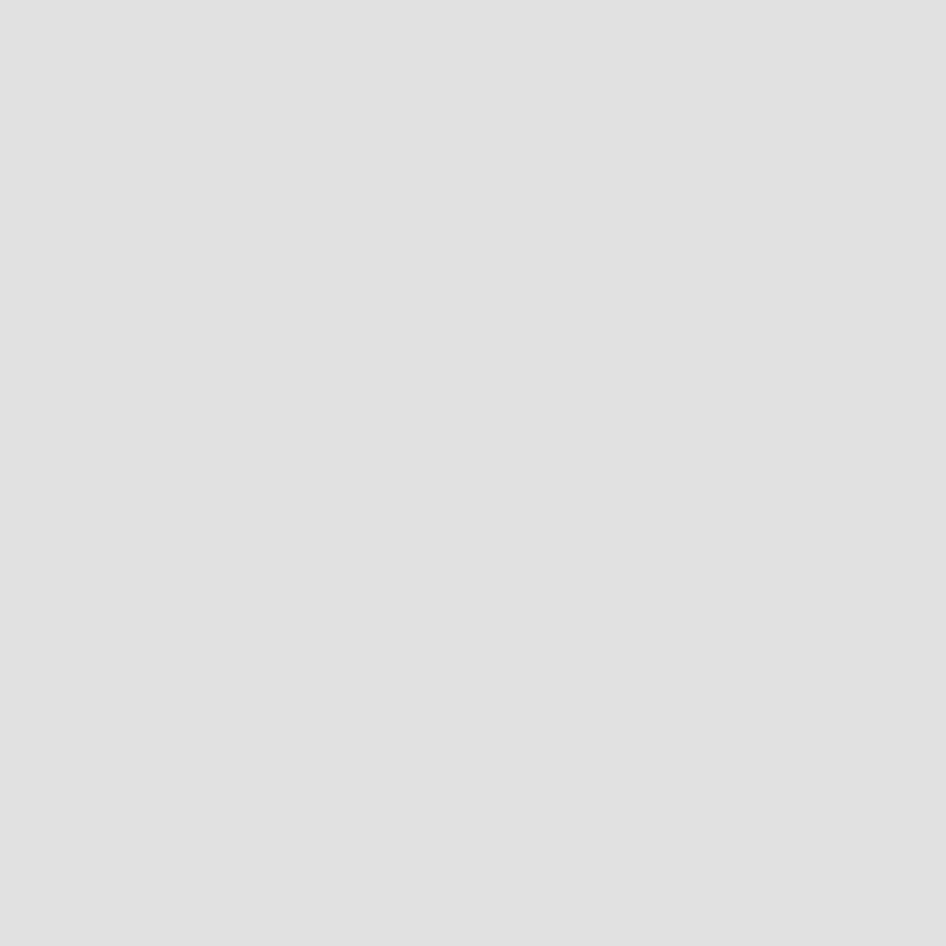
Barry J. Ewell is a Senior Content Marketing Communications Specialist for Honeywell Industrial Automation. He has been researching and writing on supply chain topics since 1991.
Let's Connect!
Sign up to receive exclusive communications from Honeywell including product updates, technical information, new offerings, events and news, surveys, special offers, and related topics via telephone, email, and other forms of electronic communication.
Copyright © 2025 Honeywell International Inc
Maximum File Size
Maximum Files Exceeded
Due to inactivity you will be logged out in 000 seconds.
Maximum File Size
Maximum Files Exceeded
You cannot access this page as this product is not available in your country.