-
Global
-
Africa
-
Asia Pacific
-
Europe
-
Latin America
-
Middle East
-
North America
- |
- Partners
- |
-
Currency:Localize your Content
You can set your preferred currency for this account.
Choose a Currency
Currency- CHOOSE YOUR CURRENCY
Update Currency
Changing Currency will cause your current cart to be deleted. Click OK to proceed.
To Keep your current cart, click CLOSE and then save your cart before changing currency.
-
Select Account
Switching accounts will update the product catalog available to you. When switching accounts, your current cart will not move to the new account you select. Your current cart will be available if you log back into this account again.
Account# Account Name City Zip/Post Code CANCELPROCEEDMy Account
-
Support
- View All Productivity Solutions
- Warranties
- Patents
- Global Locations
- Technical Support
- Discontinued Products
- Quality Program and Environmental Compliance
- Return Material Authorization (RMA)
- Legal Documents
- Product Certification
- Software Downloads
- Cyber Security Notifications
- Case Studies and Success Stories
- View All Sensing Solutions
- Sales Contact Form
- Technical Support
- Certificates
- eCOM Portal
- Distributor Inventory
- Return Material Authorization (Test & Measurement)
- Return Material Authorization (Citytech)
- Return Material Authorization (EnviteC)
- Legal Documents
- Intelligent Life Care
- Return Material Authorization (ILC)
-
Global
-
Africa
-
Asia Pacific
-
Europe
-
Latin America
-
Middle East
-
North America
- |
- Partners
- |
You are browsing the product catalog for
You are viewing the overview and resources for
- News & Events
- Featured stories
- Faster Picking Through Wearable Scanners
Faster Picking Through Wearable Scanners
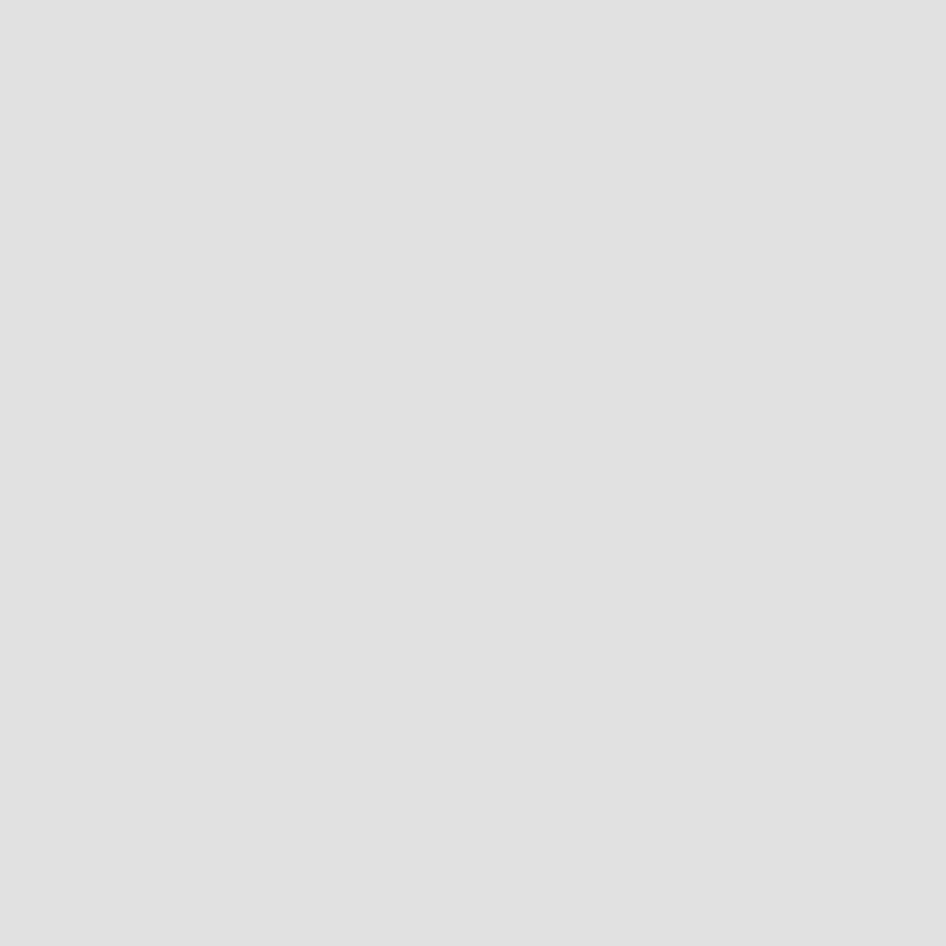
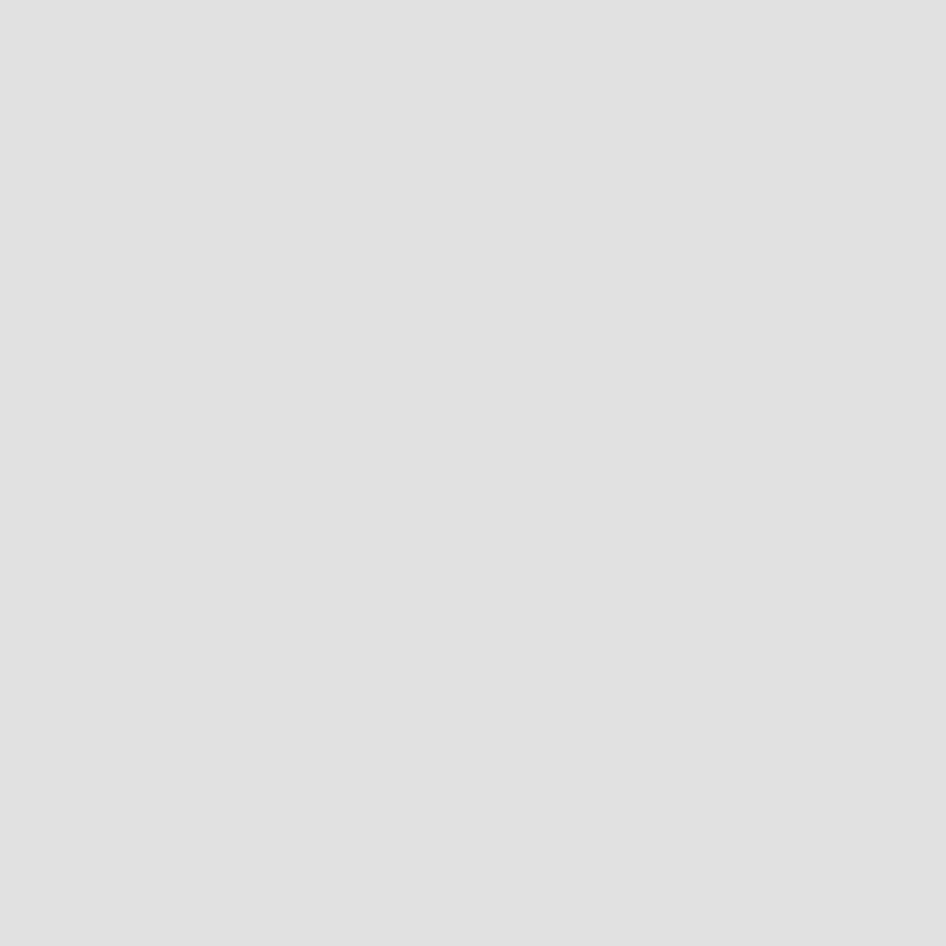
Faster Picking Through Wearable Scanners
Barry J. Ewell
May 26, 2020
If you want to squeeze a few extra seconds out of your picking application, swapping your traditional handheld barcode scanner for a wireless, wearable barcode scanner may be an ideal solution for helping your distribution center workers improve productivity and accuracy.
Wearable barcode scanners are helping DC workers connect to the next era of efficiency in data capture and order fulfillment. Right now, in a typical picking application involving a handheld barcode scanner (not to be confused with a mobile terminal):
- The picker is instructed by an application running through a host computer (for this example, a vehicle mounted computer) to go to a location and pick a certain number of items from that location.
- When the picker arrives at the proper location, he/she scans the location code to confirm they are in the correct spot.
- The picker then scans an item to confirm they are picking the correct product.
- They put the scanner under their arm, in a holster, lay it down somewhere or worse – tie up one hand by having to hold the device.
- They then start picking the specific number of items they need to fulfill the order.
The extra step of managing the scanner while picking can cost a worker three to five seconds per pick– that’s more than 20 minutes of lost time per shift, or 4% of a picker’s total shift time. This is a lot of time wasted and orders not picked.
Let’s go through the same example with an operator using a wireless wearable barcode scanner on his or her hand:
- The picker is told to go to a location and pick a certain number of items.
- The picker scans the location code.
- The picker then scans an item with their wireless wearable scanner
- He/she then immediately starts picking the specific number of items – using both hands – eliminating the hassle of managing the scanner.
Improved efficiency in picking applications is the main driver of wearable scanner adoption. As these benefits continue to be realized, expect to see widespread adoption of wearable devices throughout the distribution center and elsewhere in the supply chain. From stocking to receiving to packing – companies will be able to help increase productivity by replacing their handheld scanner with a wearable device.
We at Honeywell have helped many DCs leverage this technology evolution in real-world applications. We often couple wearable scanners with a voice-based connection to the warehouse management system, to provide major advantages for businesses looking to expand overall worker stamina, accuracy and productivity.
Intimo Lingerie is one of the leading lingerie brands across Australia and New Zealand. The company operates a streamlined direct-to-customer distribution model out of a centralized distribution center in Port Melbourne. The company uses a combination of Honeywell voice and hands-free scanner solutions – including Honeywell’s 8670 Bluetooth Ring Scanner – for their picking processes.
Intimo has seen a 30% increase in productivity since the introduction of the new system. Intimo pickers now pick up to 24 orders at once, compared to six under the previous paper-based system, helping improve warehouse efficiency and leaving resources free to be allocated to other parts of the business.
If a facility already uses voice-directed picking, nearly one in five voice customers integrate wireless wearable scanners into their voice application. Sometimes it is quicker and more accurate to scan a barcode (like a serial number) than to speak it.
There are three types of wireless wearable scanning devices available for warehouses and distribution centers to choose from, giving operators multiple solutions depending on use and need.
- A one-piece ring scanner solution is one where the scanner, Bluetooth radio and battery are all together in one module. The operator typically wears the scanner as a two-finger ring. An advantage to this solution is a simple one-piece design, eliminating the need for extra parts.
- A two-piece ring scanner solution is worn as a ring typically on the index finger tethered to a module that includes the battery and the Bluetooth radio which sits behind the hand. This solution provides comfort, as most of the weight is moved from the fingers to the back of the hand where it is less pronounced.
- A hybrid solution where the scanner, Bluetooth radio and battery are combined into one module like the one-piece option, yet the scanner is worn on the back of the hand attached to a glove. An advantage to this solution is the simplicity of a one-piece design coupled with the comfort of shifting the scanner’s weight further back on the hand. It offers the best features of the one- and two-piece solutions.
Ergonomics are very important when it comes to wearable devices. Wearable barcode scanners must be small enough to not get in the way yet sturdy enough to handle the tough conditions found in a typical DC.
One other benefit of wearables is safety. Risks are reduced as workers have the freedom and flexibility to have both hands available while fulfilling heavier items during the order picking process.
What’s the right solution for a specific DC environment? It depends on the operator, the operations manager and the specific application. Do pickers tend to have smaller or larger hands? It could be that multiple types of wearable scanners are needed.
If you’re considering driving efficiencies in your DC workers, consider using Honeywell 8680i Mobile Mini Wearable Computer as a method to do so. That helped increase efficiency and productivity can have a positive effect on your bottom line.
The 8680i Advanced model drives streamlined workflows onto a single device for many applications, replacing a scanner and mobile computer. The customizable user-facing display communicates workflow instructions, while the two-button interface enables users to navigate menus and confirm selections. The 8680i wearable mini mobile connects directly to the network application through Wi- Fi and the SDK. Converging common applications such as picking, packing, and sorting onto a single device offers improved ergonomics and reduced acquisition cost when replacing current wearable scanner plus mobile computer solutions.
A Standard version offers lightweight, ergonomic Bluetooth®-wearable scanning with clear communication of wireless connection, battery status, and scan results when paired with another device.
Configuration options help tailor the 8680i device to the environment. It is available (and field-reconfigurable) with two-finger ring or back-of-hand glove mount options and can use slim or extended batteries to suit the duty cycle, shift length, and size/weight priorities. With performance to drive effective workflows and durability to survive tough operating environments, the 8680i wearable mini mobile can add efficiency and effectiveness to the most common tasks. A few of the feature/benefits of the 8680i include:
- The 8680i wearable mini mobile is designed to speed frequent scanning tasks, leaving hands free to do the job needed.
- Advanced version offers customizable line-of-sight screen, Wi-Fi, and SDK for application development, enabling the 8680i device to support streamlined workflows as a standalone device, replacing scanner + mobile computer alternatives.
- Field-reconfigurable accessories to the device module enable ring or glove form factor; extended or slim batteries tailor size/ weight to duty cycle needs; Standard or Advanced versions to fit workflow needs.
- Engineered for 2,000 0.5 meter (1.6 feet) tumbles, the 8680i wearable mini mobile is built to endure rugged work environments.
- Honeywell Operational Intelligence workflow analytics to manage battery population lifecycle, ensuring uninterrupted full-shift operation; simple deployment of setting and firmware updates.
Contact a Honeywell Solutions Expert today! Call 1-800-934-3163.
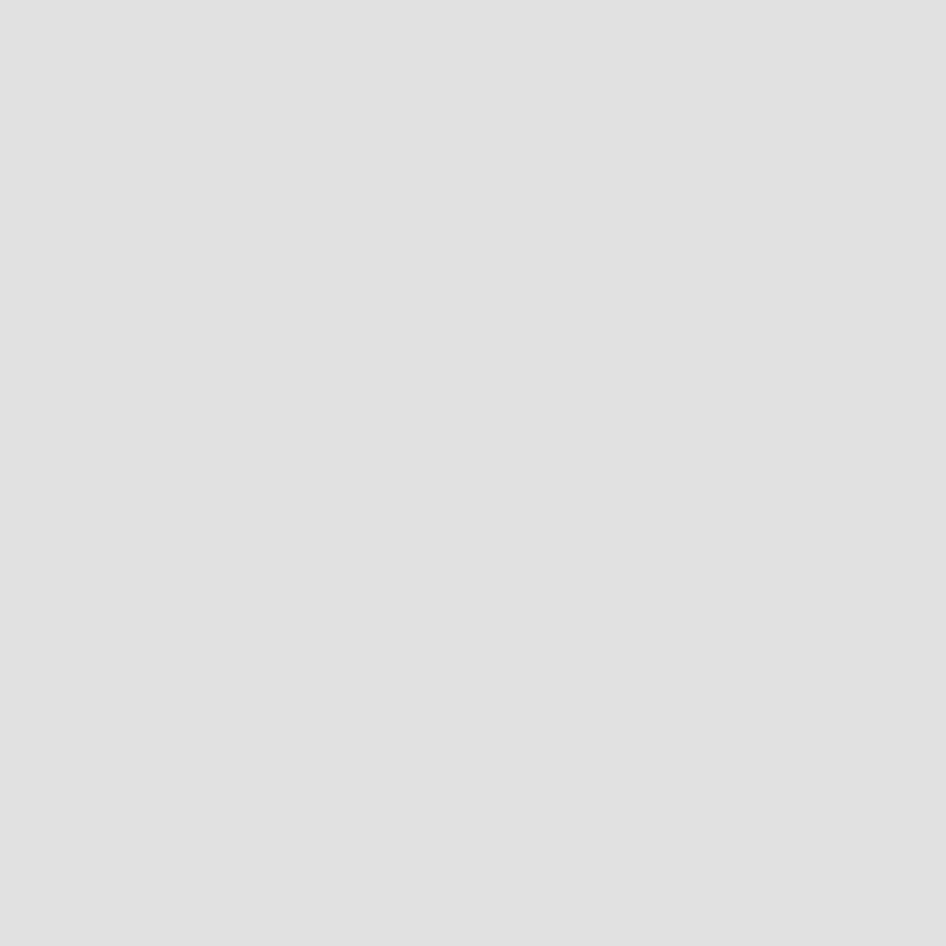
Barry J. Ewell is a Senior Content Marketing Communications Specialist for Honeywell Industrial Automation. He has been researching and writing on supply chain topics since 1991.
Let's Connect!
Sign up to receive exclusive communications from Honeywell including product updates, technical information, new offerings, events and news, surveys, special offers, and related topics via telephone, email, and other forms of electronic communication.
Copyright © 2025 Honeywell International Inc
Maximum File Size
Maximum Files Exceeded
Due to inactivity you will be logged out in 000 seconds.
Maximum File Size
Maximum Files Exceeded
You cannot access this page as this product is not available in your country.