-
Global
-
Africa
-
Asia Pacific
-
Europe
-
Latin America
-
Middle East
-
North America
- |
- Partners
- |
-
Currency:Localize your Content
You can set your preferred currency for this account.
Choose a Currency
Currency- CHOOSE YOUR CURRENCY
Update Currency
Changing Currency will cause your current cart to be deleted. Click OK to proceed.
To Keep your current cart, click CLOSE and then save your cart before changing currency.
-
Select Account
Switching accounts will update the product catalog available to you. When switching accounts, your current cart will not move to the new account you select. Your current cart will be available if you log back into this account again.
Account# Account Name City Zip/Post Code CANCELPROCEEDMy Account
-
Support
- View All Productivity Solutions
- Warranties
- Patents
- Global Locations
- Technical Support
- Discontinued Products
- Quality Program and Environmental Compliance
- Return Material Authorization (RMA)
- Legal Documents
- Product Certification
- Software Downloads
- Cyber Security Notifications
- Case Studies and Success Stories
- View All Sensing Solutions
- Sales Contact Form
- Technical Support
- Certificates
- eCOM Portal
- Distributor Inventory
- Return Material Authorization (Test & Measurement)
- Return Material Authorization (Citytech)
- Return Material Authorization (EnviteC)
- Legal Documents
- Intelligent Life Care
- Return Material Authorization (ILC)
-
Global
-
Africa
-
Asia Pacific
-
Europe
-
Latin America
-
Middle East
-
North America
- |
- Partners
- |
You are browsing the product catalog for
You are viewing the overview and resources for
- News & Events
- Featured stories
- DC Picking Workflow Provides Biggest Opportunity for Improvement
DC Picking Workflow Provides Biggest Opportunity for Improvement
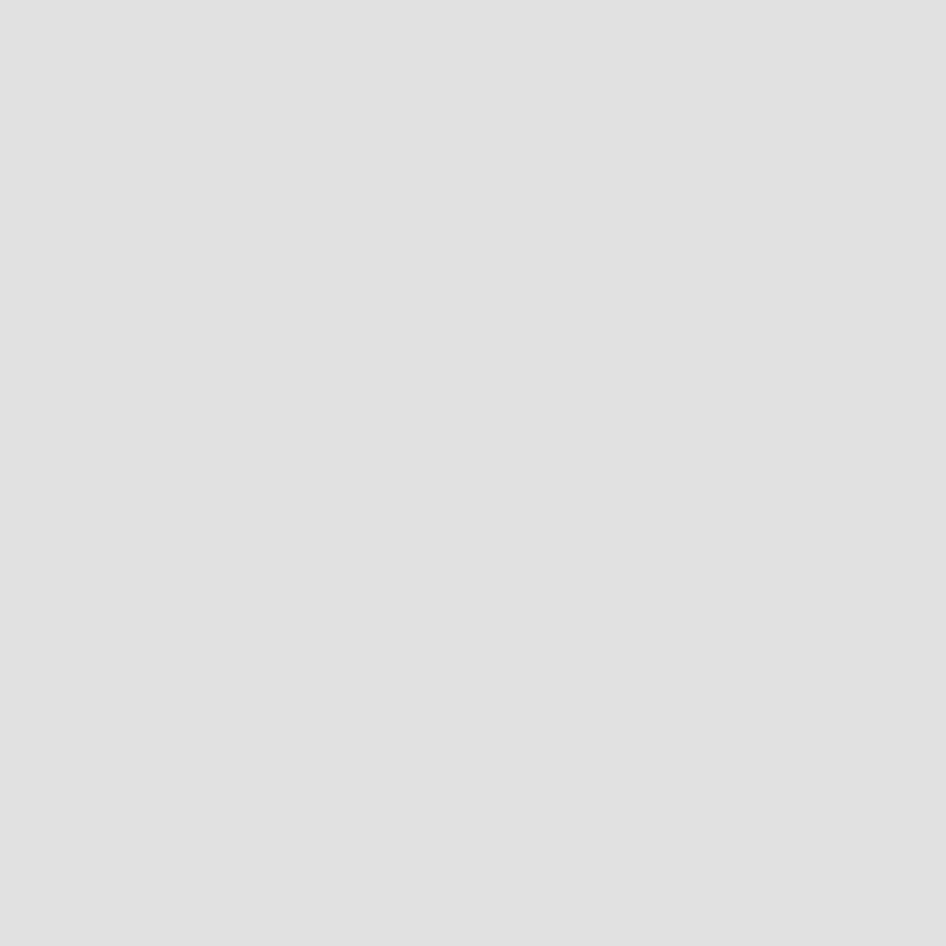
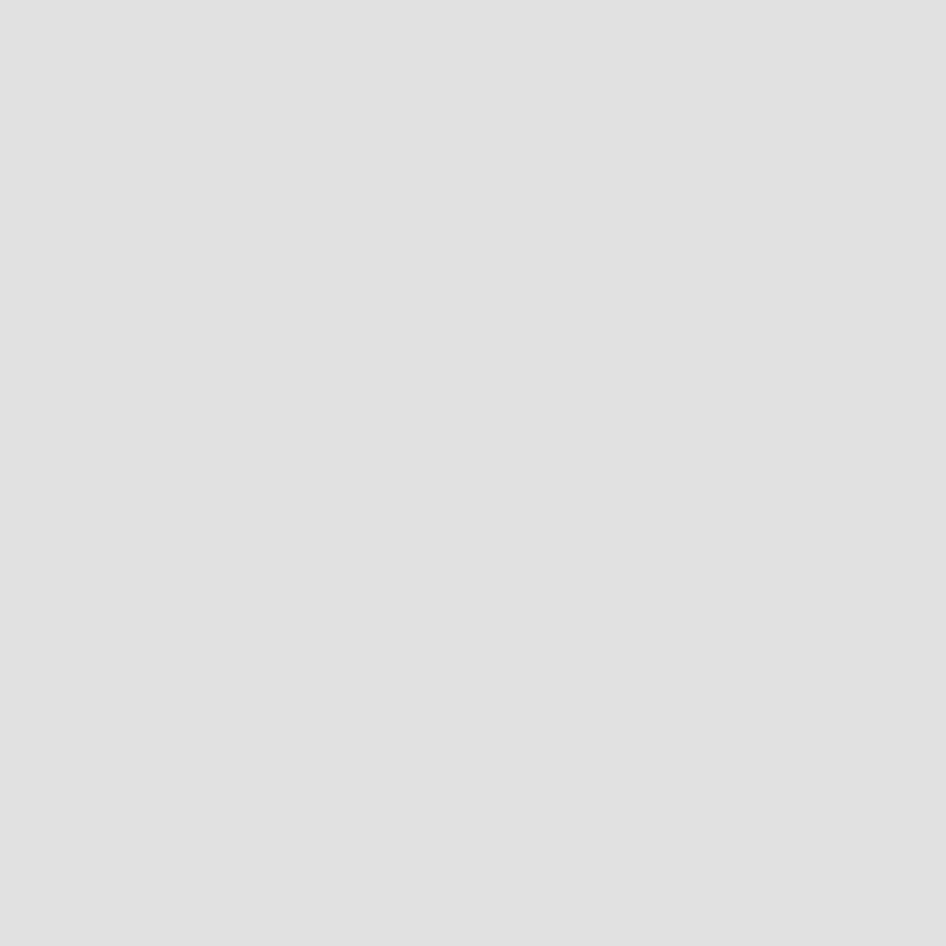
DC Picking Workflow Provides Biggest Opportunity for Improvement
Barry J. Ewell
January 30, 2019
The picking process is by far the most labor-intensive workflow in the DC and also an activity that is prone to error. This process area is typically the biggest opportunity for improvement in the DC operation.
The order picking process involves significant labor costs, including costs of incorrect items picked, any secondary audit processes required, and the potential for returns or losses due to incorrect products that are not returned and/or not paid for, and the impact on customer satisfaction levels directly attributed to picking quality is significant.
There are a number of picking methods and technology solutions available. The methods for order picking vary greatly. The characteristics of the product being handled, total number of transactions, total number of orders, picks per order, quantity per pick, total number of SKUs, value-added processing activities such as kitting or private labeling, and handling of piece pick, case pick, or full-pallet loads are all factors that affect the method for order picking. Often a combination of picking methods is needed to handle diverse product and order characteristics.
Best Practices in the Picking Workflow
Key objectives in order picking best practices include increased productivity, reduced cycle time, and increased accuracy.
- Productivity. Productivity in order picking is measured by the pick rate. Piece-pick operations usually measure the pick rate in pieces picked per hour, while case pick operations measure cases picked per hour. In pallet pick operations, the best measure is pallets picked per hour. Productivity includes the time it takes to travel to the item’s physical location, select and handle the item (or the total of the items on a given order) to be loaded on a pallet or packed in a tote or carton, and then take the item(s) to the final destination.
- Accuracy. Regardless of DC operation, accuracy is always a key objective. Virtually every decision made in setting up a DC impacts accuracy, from product location and numbering scheme, slotting, pick face labeling, product labels, and even lighting. All these elements of DC design impact picking accuracy. Technologies that aid in picking accuracy include voice picking systems, barcode scanning, and pick-to-light systems. Other major factors affecting accuracy include employee training, strong accuracy tracking, and accountability methodologies including audits and pay-for-performance incentives.
- Cycle Time. Cycle time is the amount of time it takes from order entry to shipping the order. Customer expectations for service levels vary, but inventory turn metrics. Lean and just-in-time inventory practices, as well as same-day shipment business models, have put greater emphasis on reducing cycle times from days to hours or minutes.
On the Path to Continuous Improvement
Supply chain leaders who are responsible for DCs continually seek to balance best practices with identifying the most impactful KPIs/metrics to drive productivity, cost optimization, and service excellence.
The real value of metrics comes from analyzing the metrics output and driving a continuous improvement mindset throughout each workflow in the DC/warehouse.
We can point to almost any DC KPI and learn the best-in-class metrics that provide us a benchmark to measure against. The path to best-in-class is a process of improvement in which you can identify workflow pain points and develop a path that incorporates a combination of investment in technology and continuous improvement.
As a tool to help review and identify opportunities for improvement, DCs conduct what we at Honeywell refer to as a DC Walkthrough for each workflow, which should be done every two to three years. This is a review/audit based on best practices that can yield clear and measurable actions to use and consider when planning for workflow improvement and investment. We’ll take a closer look later in the article.
According to the WERC study “DC Measures 2018 Trends and Challenges1,” the following are a few of the KPIs that DCs use in part to measure the Picking workflow:
- Order Picking Accuracy (percent by order)
- Definition. This measures the accuracy of the order picking process against errors caught prior to shipment, such as during packaging.
- Calculation. Orders picked correctly / Total orders picked.
- Quintile performance metrics.
- Best-in-class. >= 99.9%
- Median. 99.30%
- Typical. >= 99% and < 99.5%
- Disadvantage. >= 98% and < 99%
- Inventory Count Accuracy by Location
- Definition. Indicates that 10 units of part number XYZ are in slot B0029. The inventory count accuracy indicates how frequently one can go to that location and find that the physical count matches the system’s.
- Calculation. The sum of the number of locations containing an error / The total number of locations counted.
- Quintile performance metrics.
- Best-in-class. >= 99.88%
- Median. 98.40%
- Typical. >= 97% and < 99%
- Disadvantage. >= 90% and < 97%
- Lines Picked and Shipped per Hour
- Definition. Measures the productivity of picking and shipping operations in lines per-person hour.
- Calculation. Total order lines picked and shipped / Total hours worked in the picking and shipping operation.
- Quintile performance metrics.
- Best-in-class. >= 92.8 per hour
- Median. 35
- Typical. >= 26 and < 47.6
- Disadvantage. >= 12 and < 26
- Orders Picked and Shipped per Hour
- Definition. Measures the productivity of picking and shipping operations in orders per-person hour.
- Calculation. Total orders picked / Total hours worked in the picking and shipping operation.
- Quintile performance metrics.
- Best-in-class. >= 35 per hour
- Median. 10
- Typical. >= 6.08 and < 15
- Disadvantage. >= 2.76 and < 6.08
Improving the Picking Workflow with a DC Walkthrough
A DC Walkthrough is an engaging assessment that includes discussions, observations, and interviews among workers, supervisors, and management personnel with the objective to document current business and operational processes and look at ways technology and process changes can be applied to make improvements. The DC Walkthrough can be an informal or formal review/audit conducted by the company or external third parties.
At Honeywell, we have the opportunity to conduct DC Walkthroughs throughout the world for every conceivable type and size of DC. The goal of our assessment is to validate logistical/operational processes relative to industry best practices focused on time savings, increased worker productivity, and improved accuracy. We focus on the identification of opportunities to both improve stand-alone general processes, as well as improve processes with new technology.
When we review the Picking workflow, we ask questions like:
- How are the orders picked in the facility? (paper, label, RF, voice, etc.)
- What types of transportation/carriers are used for inbound? What type of equipment is used for picking? (pallet jack, forklift, pick carts, etc.)
- What types of locations are product picked from? (shelving, case flow, pallet flow, conventional rack, carousels, etc.)
- Is there any seasonality to order volume? What is the order volume during peak periods?
- What is the normal lead time between receiving the order and fulfilling?
- How are the orders grouped for picking?
- How are the loads planned?
- How is work released to the floor? (large batches of orders, orders by customer, etc.)
- What is the current pick accuracy?
- Are some orders treated as priority?
- Are there any customer-specific instructions included with the order?
- What pick methods are used? (discrete, batch, zone, wave, etc.)
- Is picking interleaved with other processes? (cycle count, etc.)
- What is the selector required to do at each location/item to complete the pick? (RF/manual validation)
- What pick pattern is used through the aisles?
- Are any labels applied during the pick process?
- Is there a bottleneck in the existing process?
- Where are picked orders taken/staged/placed after picking?
- Is there any automation/robotics involved in the pick process?
- What steps are required if the selector cannot find the entire quantity in the appropriate location?
- What is the process if all items or quantities on the order cannot be shipped?
- What container types are picked to? (pallet, tote, outbound carton, cart, etc.)
- Are pickers required to wrap or perform any additional tasks as part of picking?
- At what point are shipments confirmed to the host system?
- What changes/improvements to the pick process are desired?
Picking/Packing Walkthrough Observations and Recommendations Example
Conducting a DC Walkthrough is done with “fresh eyes.” Fresh eyes is defined as looking at the workflow with the intent of learning and understanding the current state of operations without bias or preconceived conclusions, and then applying industry knowledge and best practices to recommend ways to improve upon the current performance.
The following is an example of a DC Walkthrough Honeywell did for a medium-sized DC in North America for the Picking/Packing workflow, which includes observations with associated recommendations.
DC Walkthrough Observations
- Regional Orders
- Arrive by 1:30 p.m.
- Picked by 7:00 a.m. next day
- User Orders
- Arrive all day 8:00 a.m. – 5:00 p.m.
- 35% to 40% arrive after 3:00 p.m.
- Picked by end of day
- Use part-timers for late picks
- Arrive all day 8:00 a.m. – 5:00 p.m.
- Special Orders
- Will Calls
- Includes Hazmat
- Orders Separated into Lines (SKUs)
- Average 3,000 lines daily
- 60% lines for end-user orders
- 2.3 lines/order average
- 40% lines for regional orders
- ~ 11 lines/order average
- DC A / DC B can 70% to 30% reverse
- Average 4,800 lines DC A
- Average 5,200 lines DC B
- Using RF for Pick
- Also, some Bluetooth® ring scanners
- Pick for UPS, LTL, Specials
- Pick Pallet/Case/Each
- Bin Shelving
- Fast-moving each picks
- Orders broken into picks by management
- Area, level, etc.
- Combines in system, scans the numbers, and writes a combined number on top sheet
- Pickers enter the top number in device and begin pick
- Why not scan this number? SAP limitation?
- Discrete orders
- One picker picks entire order regardless of area
- Might necessitate switching out MHE types
- Pick
- Scan or hand type order/code into device
- Proceed to first location
- Scan location ID
- Receive error message of wrong location
- Scan product
- Enter quantity
- Repeat process
- Order completion
- Drop at specific areas
- LTL on dock
- No visible stage placards
- Parcel to packing area (convey)
- Drop product and paperwork into tote (several sizes)
- Place on conveyor
- Specials to front right of dock
- LTL on dock
- Drop at specific areas
- Pick Types
- LTL
- Pick to pallet
- Parcel
- Pick to large blue cart on forks
- Pick to walk carts from bins
- LTL
- Pick Goals
- User – 250 lines/daily
- Regular – 400 lines/daily
- Packing
- Goals
- User – 300 lines/daily
- Regional – 350 lines/daily
- Scan order
- Scan products
- Enter quantity
- Provides audit
- If scanning each item, is audit automatic?
- Once all correct prints packing list
- Picks box size
- Puts product and slip in box
- Vendor box does not need to be opened
- Uses packing list with packing envelope
- Adds dunnage, seals, and pushes to convey
- Goals
- Manifesting occurs at another end of conveyor
- Sometimes strapping multiples together for shipment savings
- UPS system with Dim/Weight capture and Zebra printer
- Prints destination label upon Dim/Weight completion
- Fluid load into staged trailer
- Lane 4
- Non-conveyable
- Using hand tape measure to capture Dim/Weight
- Do have instances of bad label prints
DC Walkthrough Best Practices Recommendations
The picking function should be paper-free and include scans or other data capture forms to verify picks from locations. Picking such as this can be done in multiple fashions. The Honeywell CN80 or Honeywell CK65 series mobile computers can be utilized for this process. However, hands-free picking solutions such as wearable computers and/or voice can offer even greater productivity increases (up to 35%) and accuracy efficiencies (up to 99.99% plus).
The Honeywell 8680i wearable mini mobile computer is one option for the picking process. This will allow the pickers to perform scans in a hands-free manner and still provide them with basic instructions if needed. This solution can be used in all the different picking types that could occur – full pallet, case, and each picking. A growing number of companies have turned to hands-free computing solutions to streamline operations and increase productivity with improved ergonomics.
Another solution for picking that can provide the capabilities needed is voice. Honeywell Voice has been proven to help increase productivity by up to 35% and help increase accuracy to 99.99%+. The hands-free, focused, and intuitive nature of voice has also been shown to help reduce injury through better ergonomics, increase safety, and reduce turnover through higher morale. Voice is also available in over 35 languages and has been proven to dramatically reduce training and onboarding time, especially in peak seasons with highly transient workforces. Honeywell Voice also works with the 8680i wearable mini mobile, so if desired both technologies can be deployed to gain the efficiencies of hands-free technology and keep the scanning technology if needed.
Both solutions would enable the picker to eliminate the hand entry of quantity that occurs now, thus adding even more productivity to this process. It would also eliminate the use/carrying of any paper pick list as the work task would be system-directed in real-time. Honeywell Voice has a direct interface to many warehouse management systems (WMS)/enterprise resource planning (ERP) systems.
Honeywell also recommends standardizing the pick process across the several areas and the technologies suggested will support this. Another recommendation is to utilize zone and/or batch picking when feasible to reduce the higher amount of travel time and MHE swapping currently in discrete picking. A typical pick order is roughly 50% travel time, but we observed this being quite a bit higher in this DC, especially when picks from multiple areas were involved. Picks can be done by zone and product married together at dock for loading. There are ways to marry this product at the dock through scans that can assist in this process change.
Packing is a process common in DC operations handling small parcel orders and/or direct-to-consumer. It is usually done at fixed stations that can be fed by conveyors and/or sorters or serviced by carts. They are usually equipped with PCs, dunnage/tape dispensers, scanners, printers, and outbound shipping containers. Some are equipped with scales. Packing stations are process areas where productivity and accuracy can be improved with technology.
This DC is currently packing in a dedicated area using an automated conveyor system to deliver cartons to manifesting. This best practice should continue; however, combining the packing and manifesting functions in one area is something to consider for the future, especially if volumes begin to increase and the space currently occupied by packing is needed for storage/picking. There was ample space on the dock to combine these processes into one process area. A printing option could be to deploy fixed smart printers from Honeywell to streamline the packing area and reduce the cost of the station, its footprint, and possible repair/replacement of multiple components. Honeywell smart printers can host the shipping software, thus eliminating the need for separate and costly hard drives and PCs.
They easily integrate with scales (can be Bluetooth®) to provide weight capture. Scales can even be shared across packing stations if needed. They also work with Honeywell scanners in a tethered or wireless fashion to provide the scan capability needed in packing. The 8680i wearable mini mobile or voice can also be deployed in packing for hands-free work processes. Honeywell media labels can also be deployed in a fashion where the multi-part label contains both the shipping information and the packing list, thus eliminating the need for any document printer at the packing station.
The new Honeywell PX940 label printer is an automatic verifier printer that prints labels quickly and verifies accuracy and/or good label reads. Should any label be deemed not scannable, the printer marks that label and prints a replacement in seconds. This can avoid bad scans downstream within the DC or at the parcel sorting centers. These printers can be integrated into the existing manifest systems.
Recommended hardware and software for these processes includes:
- Picking/Packing
- 8680i wearable mini mobile and/or
- Voice
- PX940 verifying printer with associated media
- All mobility and voice recommendations are Android™ capable.
Technology Improvements in the Picking Workflow
According to the 2018 WERC study1, technology within the supply chain is becoming increasingly important. Many companies are beginning to focus on digital transformation by focusing more on mobile technologies, cloud-based services, and big data practices.
The study also points out that a majority of distribution centers use no other technology beyond a warehouse management system (WMS) and mobile devices with RF/barcode scanners. In terms of adoption plans, over 90% of warehouse managers expect to be using mobile technologies within five years (which is just over 50% today). Eighty-six percent expect to be using big data and real-time analytics within five years, which is a 60% increase over the percentage of people using the technology today.
Honeywell brings a wide set of solutions together that can influence positive outcomes in the picking workflow throughout the DC. They include the following:
- Voice. Voice picking is hands-free and eyes-free, so it helps increase accuracy and productivity through focused work activity. Voice can be deployed in any type of pick operation to include pallet picking, case picking, and each picking to tote or carton. There are additional benefits with voice including safety and ergonomic gains, training time reduction (very relevant for seasonal picking), employee satisfaction, and the resulting retention and language-barrier removal.
Honeywell’s voice-guided solutions have proven to help increase productivity by up to 35% and increase accuracy to 99.99%+ in a variety of tasks throughout the warehouse. For example, in picking processes where workers follow a series of instructions for specific pick locations, products, and quantities, these tools provide needed guidance and verification at every step. Voice is available in over 35 languages and has been proven to dramatically reduce training and onboarding time, especially in peak seasons with highly transient workforces. - Wearable Solutions. There are instances where scanning additional critical data is required and these are opportunities to deploy wearable scanners to be used with voice picking. A growing number of companies have turned to hands-free computing solutions to streamline operations and improve productivity. The Honeywell 8680i wearable mini mobile provides a hands-free solution that increases productivity and improves ergonomics over handheld devices.
- Barcode Scanning. Though very useful in helping increase accuracy levels, barcode scanners in a fast-paced piece pick operation tend to become cumbersome and can significantly reduce pick rates. The reason for this is the high amount of product handling required and the ergonomic penalties of having a scanner in the hand while picking. Scanners are better suited to case pick, pallet load, put-away, and order checking operations and in selected picking situations where the actual speed required in the picking function is mitigated to some degree with travel times.
- Mobile Computers with 1D and 2D Imaging. Mobile computers are also used in pick operations and are best suited for low-volume, basic operating environments. If the workforce is expected to perform multiple operational processes such as picking, receiving, loading, etc. during a single shift, then it may be advantageous to equip them with voice-enabled multi-function (scan/key/voice) mobile computers so that a single device with a single supporting infrastructure (batteries, chargers, etc.) can be utilized.
Utilizing mobile computers with imagers to scan product and label information, as well as capture additional data, is more productive (~25%) and accurate (~50%) than paper/manual-based methods. It helps ensure quality control and vendor compliance, and quantity-received information is captured in real-time. - Fixed and Mobile Printing and Media. As part of the picking process, destination labels are usually required to be applied to the finished container (pallet, tote, etc.). This can be accomplished by placing fixed printers throughout the facility so that the picker can retrieve them either before or after completing their pick task. These fixed printer stations can, however, become choke points in high-volume operations. Mobile printers can also be deployed, especially in operations such as Convenience and Drugstore DCs that require a shelf or pricing label be applied to each item picked, or in each picking where tote or carton labels are required.
- Automation. The use of automation and/or robotics is becoming increasingly relevant in DC operations. These technologies are currently typically deployed in very high-volume operations where the product being handled is very similar or standard in nature. If you are doing zone or wave picking, automated conveyor and sortation systems will likely be a part of the system. In case picking, you may see standard conveyors to transport individual cases or unit-load conveyors to transport pallets. This operation is often referred to as “pick-to-belt”.
- Automated Storage and Retrieval Systems (AS/RS). When combined with unit-load conveyors and sortation systems, AS/RS can provide fully automatic pallet-picking operations, and the ability to store product in racking up to 100 feet high gives excellent storage density. AS/RS systems are used effectively in full-pallet operations to defray labor costs. While extremely costly and complex mechanically, AS/RS systems can be economical over longer payback periods.
- Motorized Equipment. There is also an increase in the use of motorized equipment that allows workers to remain in their pick zones and reduces the travel time associated with conventional picking. Some of these processes involve the movement of pallets to each zone by motorized equipment and the worker will pick items from their zone to the pallet that then moves to the next zone. The use of voice technology for picking the items in the zone is a great complement to this technology. In some instances, the motorized equipment will arrive with a new empty container while the full container will be transported to the dock by motorized equipment.
Achieve Better Outcomes with Honeywell
At Honeywell, we have extensive experience in successfully solving complex problems for a variety of ecommerce and omnichannel businesses. We’re committed to solving your DC accuracy challenges through relentless innovation and a desire to deliver best-fit solutions. We provide access to the actionable insights and information you need to transform your business.
Our expert assessment teams will partner with you to understand your unique business requirements and identify where opportunities exist to optimize your workflows and increase efficiencies within today’s competitive business climate.
Take your DC to the next level. Contact us today.
1 DC Measures 2018 Trends and Challenges, WERC
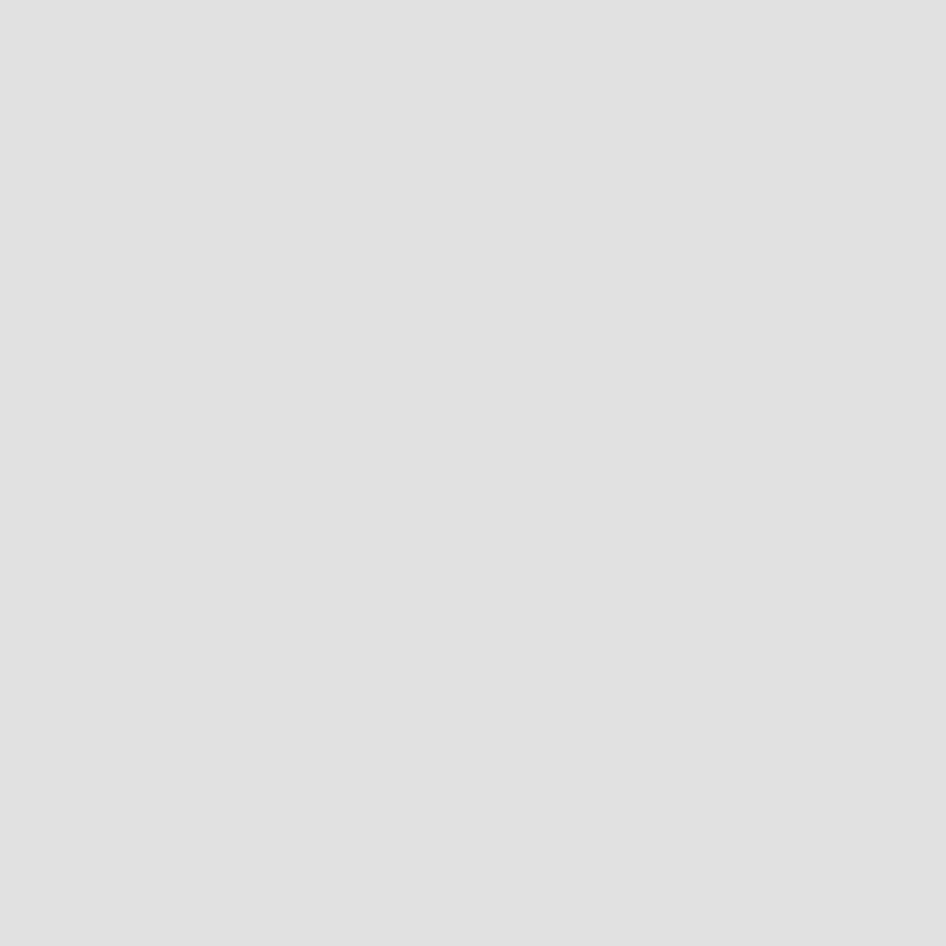
Barry J. Ewell is a Senior Content Marketing Communications Specialist for Honeywell Industrial Automation. He has been researching and writing on supply chain topics since 1991.
Let's Connect!
Sign up to receive exclusive communications from Honeywell including product updates, technical information, new offerings, events and news, surveys, special offers, and related topics via telephone, email, and other forms of electronic communication.
Copyright © 2025 Honeywell International Inc
Maximum File Size
Maximum Files Exceeded
Due to inactivity you will be logged out in 000 seconds.
Maximum File Size
Maximum Files Exceeded
You cannot access this page as this product is not available in your country.