-
Global
-
Africa
-
Asia Pacific
-
Europe
-
Latin America
-
Middle East
-
North America
- |
- Partners
- |
-
Currency:Localize your Content
You can set your preferred currency for this account.
Choose a Currency
Currency- CHOOSE YOUR CURRENCY
Update Currency
Changing Currency will cause your current cart to be deleted. Click OK to proceed.
To Keep your current cart, click CLOSE and then save your cart before changing currency.
-
Select Account
Switching accounts will update the product catalog available to you. When switching accounts, your current cart will not move to the new account you select. Your current cart will be available if you log back into this account again.
Account# Account Name City Zip/Post Code CANCELPROCEEDMy Account
-
Support
- View All Productivity Solutions
- Warranties
- Patents
- Global Locations
- Technical Support
- Discontinued Products
- Quality Program and Environmental Compliance
- Return Material Authorization (RMA)
- Legal Documents
- Product Certification
- Software Downloads
- Cyber Security Notifications
- Case Studies and Success Stories
- View All Sensing Solutions
- Sales Contact Form
- Technical Support
- Certificates
- eCOM Portal
- Distributor Inventory
- Return Material Authorization (Test & Measurement)
- Return Material Authorization (Citytech)
- Return Material Authorization (EnviteC)
- Legal Documents
- Intelligent Life Care
- Return Material Authorization (ILC)
-
Global
-
Africa
-
Asia Pacific
-
Europe
-
Latin America
-
Middle East
-
North America
- |
- Partners
- |
You are browsing the product catalog for
You are viewing the overview and resources for
- News & Events
- Featured stories
- 15 Reasons Why Your Supply Chain Needs Voice Picking Solutions
15 Reasons Why Your Supply Chain Needs Voice Picking Solutions
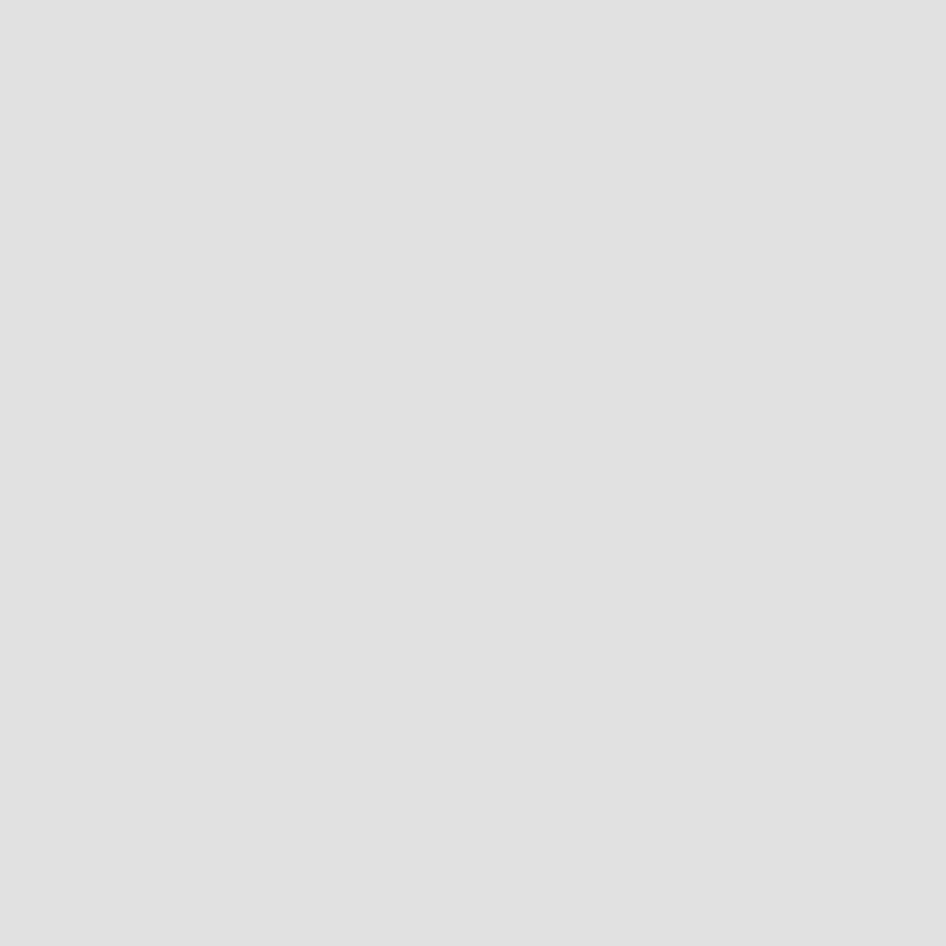
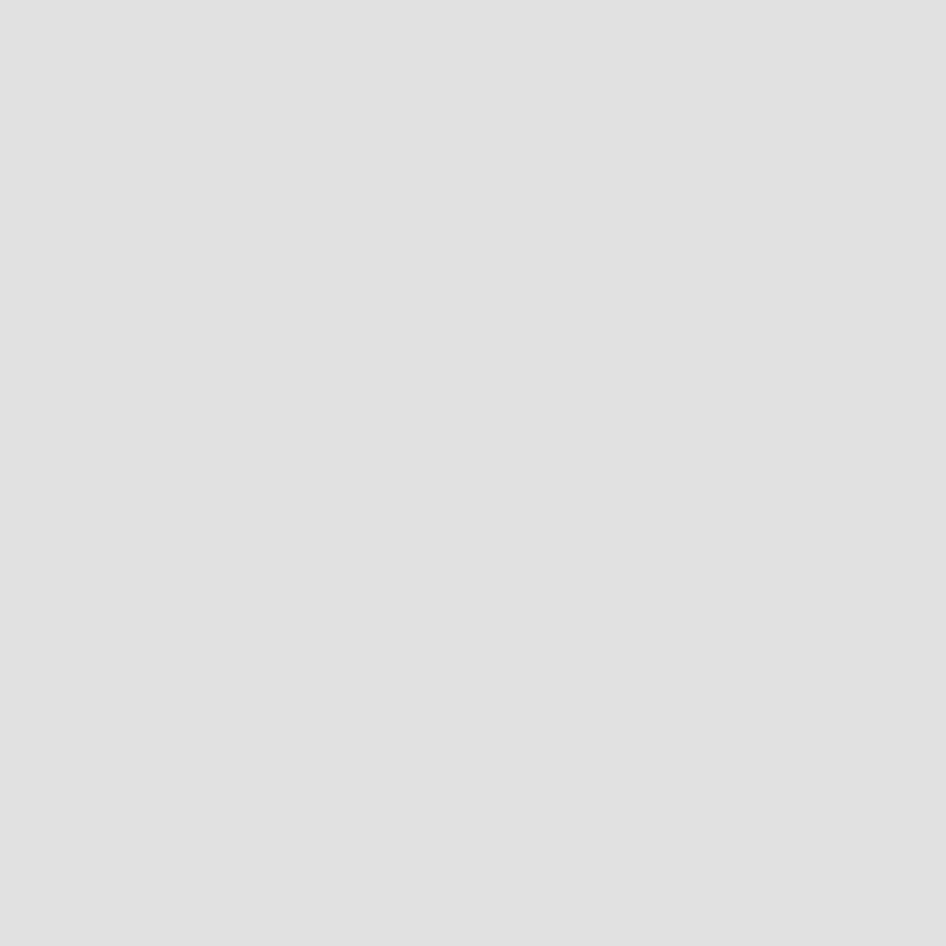
15 Reasons Why Your Supply Chain Needs Voice Picking Solutions
Barry J. Ewell
May 5, 2021
Honeywell Voice is a hands-free, eyes-free hardware and software solution used in 60 countries by over 1 million workers speaking 35 different languages. For over three decades, this best-in-class voice-picking solution has helped large enterprise customers decrease error rates by 50%, increase productivity by 35%, and achieving accuracy levels to 99.99%+.1 Used most often in the order picking workflow in the warehouse/DC, the technology helps eliminate the need for cumbersome paper lists, labels, handheld computers, and scanners — making it a faster, more accurate and safer way to work.
What Applications Use Voice Pickings?
Picking is the most labor-intensive workflow within the warehouse/DC. Traditionally, order pickers are confronted with a variety of error-prone tasks such as:
· Continually moving eye contact back and forth between product stock shelves to reading low-light device display screen, picklist or purchase order
· Keying-entering data
· Scanning bar codes
· Juggling both product and an input device.
Paper-based processes can be quickly filled with steps that slow down productivity levels and efficiency. Common errors include:
· Items can be omitted from orders
· Picking the wrong item
· Miscounting the quantity
· Quantities are misread or transposed.
How does voice picking change paper-based or screen-based picking? Honeywell Voice solution for voice-directed picking is designed for warehouses that need to manage large numbers of SKUs. Wearing a lightweight wireless computer on the belt and a headset, workers receive and communicate responses by speaking into the headset. Communication between the worker and Honeywell voice recognition system would be like the following:
· Voice: Go to location A21b
· User: Confirm check code for A21b
· Voice: Pick 5 cases of product 123
· User: Confirm quantity "5"
· Voice: Go to location A35a
· User: Confirm check code for A35a
· Voice: Pick 5 cases of product ABC
· User: Confirm quantity "5"
· Voice: Capture lot codes for product ABC
· User: Lot 1 "a1b2c3d4"
· User: Lot 2 "xxxxxx".
The resulting data is transmitted from the wearable computer via an enterprise wireless network to a host application, such as a warehouse management system (WMS) or material handling and equipment system (MHE).
What are applications ideal for voice picking? Some of the most common warehouse picking technology applications include:
· Full case picking
· Pallet picking
· Picking for kit assembly
· Picking in cold storage
· Picking in a variety of environments that require unique clothing and protection.
The benefits of the Honeywell voice picking solution come from the hands-free, eyes-up nature of voice technology. Workers can keep their eyes continuously on the task and use both hands for a range of duties. This helps to reduce the need for hands to be holding a device keyboard, a scanner or reaching for picking order. Let's look at some of the real advantages organizations can realize with Honeywell voice picking solutions.
Advantages of Voice Picking on Operational Accuracy
Products moving through the supply chain are all about operational accuracy and ensuring that goods arrive at the designated location on time, in good condition and incorrect quantities. Organizations are hyper-focused on keeping errors to a minimum and are constantly evaluating how to improve accuracy. Honeywell voice-directed picking is a solution that has proven to have a direct impact on improving accuracy and reducing operational costs. For example,
What is the cost of picking errors? Depending on the value of goods and process costs, a simple picking error can cost from $10 to $250 for each mistake, translating into millions of dollars for a sizable operation.
How does the cost of errors add up? Every mistake is creating a ripple effect in the supply chain. Many of the costs are hidden in labor and transportation costs, reduced productivity because picking and delivery activities are interrupted, order fulfillment schedules fall behind, and payments are slowed.
How are the errors exposed? Supply chain operational processes that include workers are filled with the potential for human error. These errors often show up in customer and store order fulfillment in the form of:
· Item not received (out of stock)
· Too few received (or delivered damaged)
· Too many: more items received than ordered
· Wrong item received (e.g., wrong version)
· "Extra" items (not on the P.O.)
· Proper quantity received but does not coincide with paperwork
· Items incorrectly labeled
· Paperwork not matching expectations
· Items received beyond the committed time frame.
How can voice-directed picking help reduce errors? Companies who use voice-directed picking experience results related to reduced mistakes and improved accuracy nearing 100%. This is done by leveraging what Honeywell refers to as voice-directed, hands-free, eyes-up technology, which can typically reduce the number of errors by: 1
· 1–15% improvements for pick-to-light operations
· 8–25% improvements for RF scanning operations
· 50–90% improvements for paper-based operations
· 12 months – or less payback.
How does improved picking improve costs? When orders are delivered the first time correctly, costs are avoided across the value chain associated with repicks, re-delivery, cost of lost sales and administrative charges.
Advantages of Voice Picking on Productivity
Typically, every order's cost includes direct and indirect costs of labor, benefits, packing costs, facilities, processes, and management. These costs are incurred every time an order is placed. More than 50% of the expenses per order are labor-related. Productivity improvements in the picking workflow manifest are reduced errors, increased volume in picked SKUs, and higher-order volumes without increasing staff and square footage. Operations using Honeywell voice-directed picking consistently see worker productivity improvements. For example,
How does voice-directed picking improve productivity? When an organization combines voice-directed, hands-free picking with their warehouse management system (WMS) or similar software, voice-directed picking productivity improvements can reach:1
· 10–35% for paper-based operations
· Up to 30% for pick-to-light operations
· 10–35% for RF scanning operations.
What impact does productivity have on cost savings per worker? If a worker, who earned $24,500, had a 15% savings in productivity using voice picking, the company would save $3,675. In a year, the organization could expect to realize the following:
· 10 employees: $36,750 savings
· 20 employees: $73,500 savings
· 30 employees: $110,250 savings
· 40 employees: $147,000 savings
· 50 employees: $183,750 savings.
Where are picking productivity gains realized? At Honeywell, our customers realize worker productivity gains in the following areas:
· Picker Efficiency (measured in lines per hour). When voice-directed picking is integrated with your WMS, companies can reduce order-cycle times by optimizing warehouse layout and item selection (picking). For example, voice-picking can be the catalyst for helping an operation move from discrete order picking to batch picking and then to multiple orders.
Efficiency is measured in reduced travel times between pick locations and the handling of exceptions (shorts, damage, etc.). For example, a WMS capable of task-interleaving can enhance the worker's ability to dynamically perform multiple roles based on skills and operational priorities – such as blending a cycle-counting task while performing a replenishment activity.
· Hands-Free, eyes-up capable. Voice-directed picking allows the worker to be hands-free, eyes-up capable when performing their tasks. This means the worker can avoid the need to handle paper or devices multiple times during a pick. This results in viewer steps and motions, which reduce the time needed to complete the pick.
Consider the added complexities associated with environmental conditions such as cold storage where workers need to wear gloves. It isn't easy to use a keyboard and enter data when wearing gloves. Using a voice picking system, workers can quickly enter items picked and catch weights.
Voice-picking is usually ideal for the following environmental conditions:
o When protective clothing is used, such as gloves in cold storage and protective clothing in chemical storage
o When operating equipment, such as lift truck
o When there are climate extremes, such as data collection in inclement weather
o When special manufacturing processes are involved, such as with hazardous materials where worker concentration is paramount
o When both hands are required to move goods safely.
· Rapid "new hire" effectiveness. Traditionally, without voice-directed picking, a new worker is trained by working alongside an experienced picker. This process can easily take weeks, if not months, for a new worker to know the layout, products and optimized processes that meet corporate productivity expectations. Within a brief time of use (e.g., hours, shifts), Honeywell's voice-picking solution helps accelerate the workers learning curve and ability to achieve established corporate productivity metrics.
· Use voice-picking performance metrics. Voice-directed picking provides workers with real-time visibility into their performance. If companies have reward systems for worker performance, pickers can ask for their current performance status, ensuring they know their performance level. This can improve productivity, efficiencies and decreases order-cycle time.
· Faster Up-time for seasonal labor or temporary workers. Because voice-directed picking has a faster up-time for learning, seasonal and temporary workers can be up to speed the first day on the job without sacrificing accuracy.
· Workers can improve faster. Over the years of voice-directed picking deployments, workers, who receive instructions via a headset, get into a work rhythm "picking zone" faster by becoming less distracted and increasing their hourly output.
· Reduced scheduling for overtime. Voice-directed picking helps improve picker efficiencies by enhancing the number of line items picked per hour, per worker. This improves operational flexibility when it comes to staffing your warehouse operations.
· Integration of other critical applications into picking workflow. Many operations have found it productive to integrate other critical applications like real-time cycle-counting and replenishment with voice-directed picking. For example, warehouse voice picking technology can be used for replenishment notifications. For example, pickers can be reminded to return unpicked items to the shelf as time becomes available, reducing backtracking at the end of a shift or shipping incomplete orders and expediting additions/missed items.
Advantages of Voice Picking on Staffing and Labor
The organizations that have incorporated voice-directed picking into their operations have also experienced improvement with staffing requirements. For example,
How does voice-directed picking help reduce turnover? Honeywell voice-directed picking contributes to a reduction in staff churn and turnover in several ways:
· The more senior experienced workers have increased productivity, which lessens the need for additional entry-level or less experienced workers where churn rates are higher.
· New hires effectiveness and positive impact on the business is faster
· Workers have an increased sense of value because they see the company investing in them.
· The voice-picking systems help on-native speaking workers build language skills in the predominant local language, which helps increase promotion opportunities and their overall value to the company.
· Individual performance can be recognized and rewarded
How do voice-directed solutions simplify hiring? Voice-directed solutions provide for hiring from a large, more diversified multi-national labor pool, as there is less emphasis on spoken or written language skills. The Honeywell voice picking solution provides multilingual capabilities. The voice picking software speaks to workers in 46 languages/dialects in 85 different voices and understands workers in 68 other languages/dialects. Companies can hire for needed job openings from a larger labor pool who speak various languages or non-native languages/dialects.
How do voice picking solutions improve safety? Voice Honeywell voice-directed, hands-free and eyes-up technology helps improve worker safety by removing and enabling workers to be more aware of their surroundings. Better awareness results in stabilizing staffing predictability and fewer injuries and deaths, reducing legal liabilities while — over sufficient time — helping to lower insurance costs.
Is voice-directed picking safe for the hearing impaired? If the order picker is not 100% hearing impaired, they can most likely use Honeywell voice-directed solutions successfully. The Text-to-Speech engine allows users to choose their preferred voice, pitch and volume to dial it in to a frequency and volume that almost any operator is comfortable with. We have several different headset styles, including a cupped style that eliminates background noise.
Software and Hardware: What Equipment Do You Need for Voice Picking
The Honeywell Voice picking solution is a fully integrated system that includes rugged yet ergonomic hardware that easily integrates into existing technology investments. Honeywell provides its industry-leading guided-work solutions for all the leading WMS or MHE and integrations with SAP and Business One, and Microsoft Dynamics 365 warehousing platform. Wearing a lightweight wireless computer on the belt and a headset, workers receive and communicate responses by speaking into the headset. For example,
Wearable voice terminal. Honeywell is continuing to advance hardware to include the lasted in technology. For example, the A700x, our newest wearable voice processor, consists of the state of the art updates in advanced software, machine learning, sensors and processors. The 700X series includes:
· A730x – Combines voice and occasional scanning, which is ideal for applications such as tote or purchase order induction
· A720x –Includes two industrial-grade breakaway TCO connectors which support headsets, scanners and printers. It is a perfect fit for using wired or wireless headsets and peripherals.
· A710X. Ideal for vehicle-mounted applications, this wireless-only device supports headsets, scanners and printers.
Our A700x series fully supports existing software implementations, making updating this new platform straightforward and cost-effective. The devices have two battery options that last 1-2 shifts (12+ hours).
Comfortable advanced headset. The Honeywell SRX headset series is relaxed and ergonomically refined for improved worker comfort, safety and satisfaction. The headset also includes the latest superior speech recognition with SoundSense™ technology, reducing unwanted word and sound interactions by more than 50%—battery performance last 10+ hours.
Conclusion
This article has highlighted the voice-directed benefits of accuracy, productivity, labor efficiency, and safety. Our expert assessment teams can work closely with you to understand business requirements, identify opportunities to optimize your workflows and increase efficiencies.
Contact a Honeywell Solutions Expert today! Call 1-800-934-3163.
1Results are based on Honeywell's global customer performance benchmarks. Results may vary per customer.
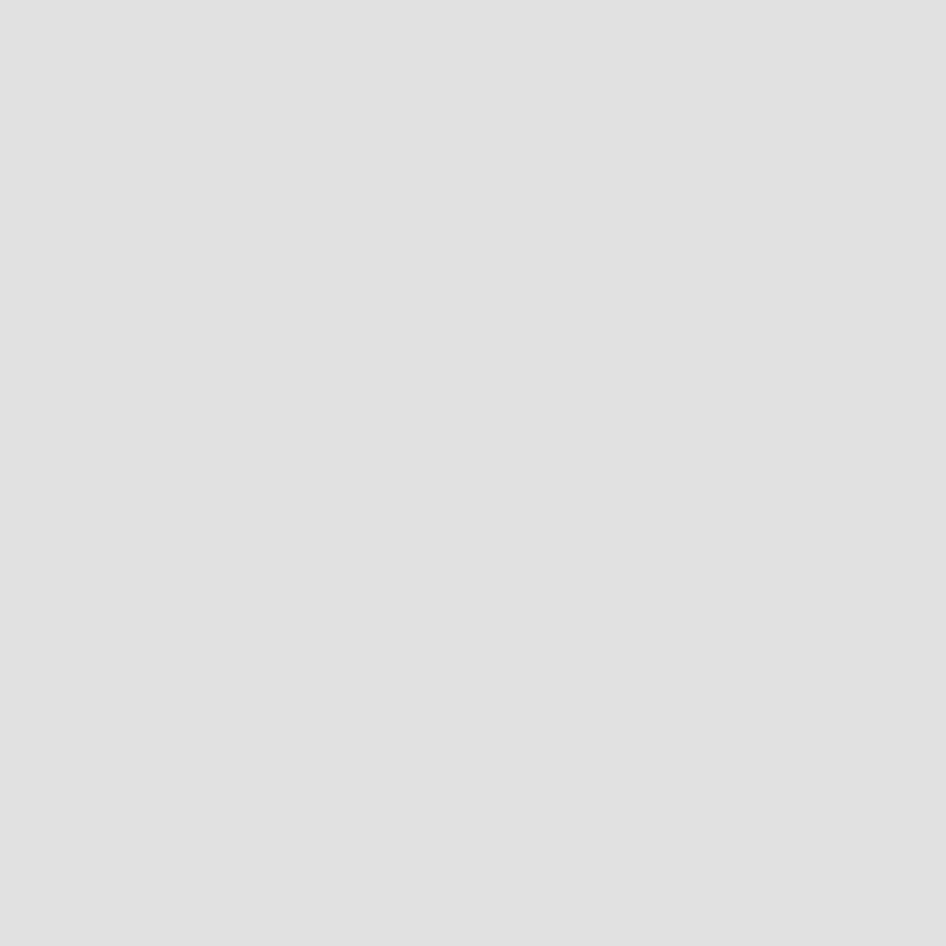
Barry J. Ewell is a Senior Content Marketing Communications Specialist for Honeywell Industrial Automation. He has been researching and writing on supply chain topics since 1991.
Let's Connect!
Sign up to receive exclusive communications from Honeywell including product updates, technical information, new offerings, events and news, surveys, special offers, and related topics via telephone, email, and other forms of electronic communication.
Copyright © 2025 Honeywell International Inc
Maximum File Size
Maximum Files Exceeded
Due to inactivity you will be logged out in 000 seconds.
Maximum File Size
Maximum Files Exceeded
You cannot access this page as this product is not available in your country.