-
Global
-
Africa
-
Asia Pacific
-
Europe
-
Latin America
-
Middle East
-
North America
- |
- Partners
- |
-
Currency:Localize your Content
You can set your preferred currency for this account.
Choose a Currency
Currency- CHOOSE YOUR CURRENCY
Update Currency
Changing Currency will cause your current cart to be deleted. Click OK to proceed.
To Keep your current cart, click CLOSE and then save your cart before changing currency.
-
Select Account
Switching accounts will update the product catalog available to you. When switching accounts, your current cart will not move to the new account you select. Your current cart will be available if you log back into this account again.
Account# Account Name City Zip/Post Code CANCELPROCEEDMy Account
-
Support
- View All Productivity Solutions
- Warranties
- Patents
- Global Locations
- Technical Support
- Discontinued Products
- Quality Program and Environmental Compliance
- Return Material Authorization (RMA)
- Legal Documents
- Product Certification
- Software Downloads
- Cyber Security Notifications
- Case Studies and Success Stories
- View All Sensing Solutions
- Sales Contact Form
- Technical Support
- Certificates
- eCOM Portal
- Distributor Inventory
- Return Material Authorization (Test & Measurement)
- Return Material Authorization (Citytech)
- Return Material Authorization (EnviteC)
- Legal Documents
- Intelligent Life Care
- Return Material Authorization (ILC)
-
Global
-
Africa
-
Asia Pacific
-
Europe
-
Latin America
-
Middle East
-
North America
- |
- Partners
- |
You are browsing the product catalog for
You are viewing the overview and resources for
- News & Events
- Featured stories
- Step 1 of 10 Steps to Improve Operational Efficiency Without Investing in Automation
Step 1 of 10 Steps to Improve Operational Efficiency Without Investing in Automation
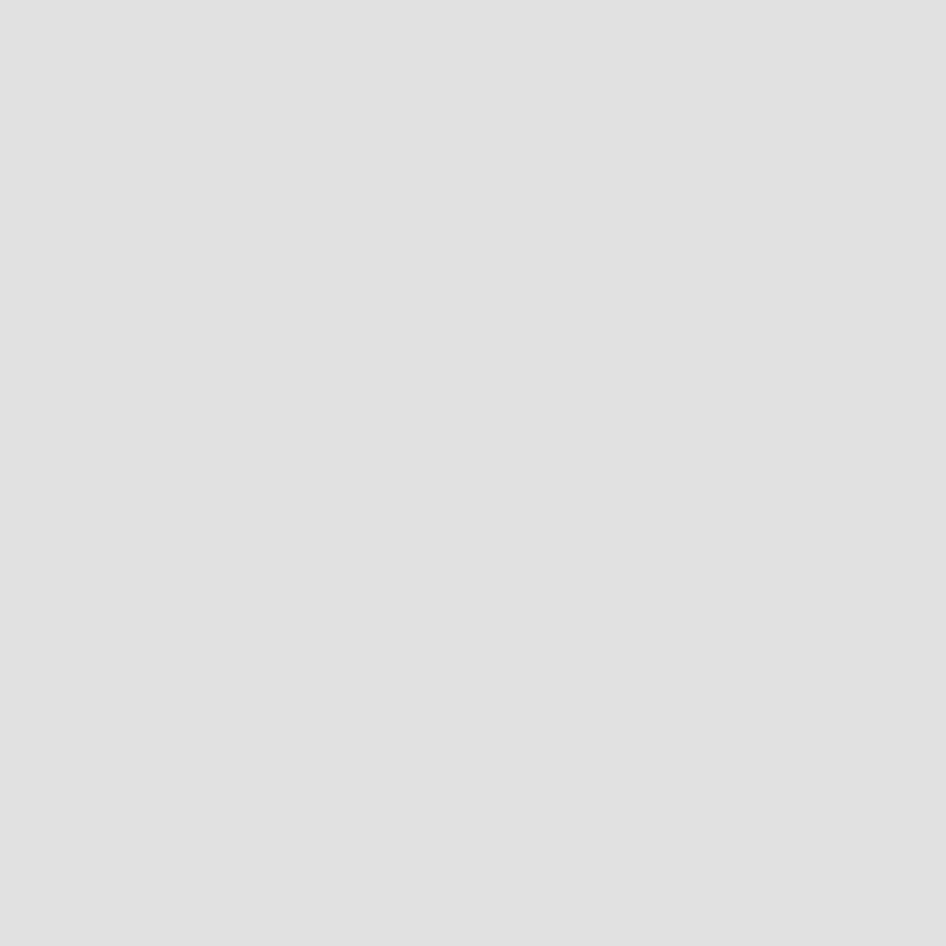
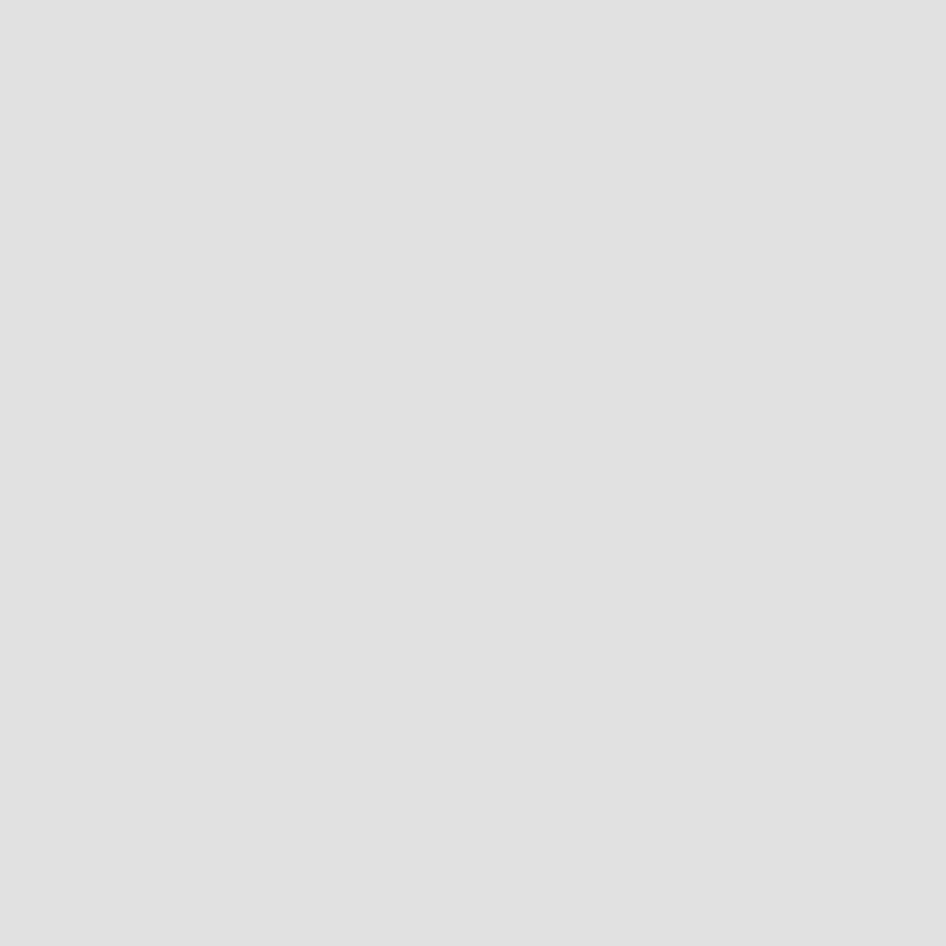
Step 1 of 10 Steps to Improve Operational Efficiency Without Investing in Automation
Doug Fukushima
March 23, 2020
Thanks to the e-commerce boom and the subsequent push to fill as many orders as fast as possible, companies in retail, apparel, health and beauty, electronics, pharmaceuticals and other industries are constantly looking to improve operational efficiency.
While investments in automated material handling solutions — including robotics, autonomous sortation solutions, automated storage and retrieval systems, and more — can deliver significant improvements to order fulfillment while addressing labor and flexibility challenges, there are other, less complex measures that can be taken as well.
This post is part 1 in a series of 10 different approaches to addressing the common challenges faced by distribution centers (DCs) across a broad range of industries without investing in automation.
Step 1: Know Your Operation
Most DC managers actually don’t know their operation as well as they think. While that may sound surprising, consider when you last looked at which metrics — or key performance indicators (KPIs) — are being measured. And look not only at department levels, but also across the facility as a whole.
Although DC managers recognize metrics as valuable business intelligence tools that help to identify areas for improvement, many operations fall into metrics silos, i.e., each department primarily focuses on its own productivity, which can hamper the overall efficiency of the entire operation. A better approach is to ensure that the KPIs tracked by department are selected based on their impact on the goals of the facility, especially at department interfaces.
When reviewing what metrics are being tracked, also consider what’s still relevant to your current business objectives. Depending on the business, tracked KPIs could span a range of categories, including:
- Inventory (Paid inventory ratio; Inventory accuracy percentage; Inventory days on hand; Inventory visibility; Damaged inventory percentage)
- Order Fulfillment (Order fill rate; Order accuracy; Order cycle times; On-time delivery)
- Receiving (Dock to stock hours; Dollar value per unit received)
- Productivity (Units per labor hour; Sales per labor hour)
- Overall Operations (Cost per labor hour; Storage utilization percentage)
Many operations track specific KPIs because they were important a few years ago. Or management once published a handbook of metrics to be monitored both departmentally and facility-wide, but in reality, only the items on the first few pages are tracked consistently. Either way, assessing what data is currently being gathered — and to what end — might reveal that it’s time to make adjustments in order to match today’s goals, as well as to achieve greater operational efficiencies going forward.
To learn more about the other nine steps, download the latest Honeywell Intelligrated white paper, 10 Steps to Improve Operational Efficiency: Addressing Common Order Fulfillment Challenges Without Investing in Automation. And, be sure to Subscribe to our blog so you don't miss the second step in this series: “Train, Train and Train Again.”
To subscribe to our blog and receive exclusive communications and updates from Honeywell Intelligrated, click here.
Let's Connect!
Sign up to receive exclusive communications from Honeywell including product updates, technical information, new offerings, events and news, surveys, special offers, and related topics via telephone, email, and other forms of electronic communication.
Copyright © 2025 Honeywell International Inc
Maximum File Size
Maximum Files Exceeded
Due to inactivity you will be logged out in 000 seconds.
Maximum File Size
Maximum Files Exceeded
You cannot access this page as this product is not available in your country.