-
Global
-
Africa
-
Asia Pacific
-
Europe
-
Latin America
-
Middle East
-
North America
- |
- Partners
- |
-
Currency:Localize your Content
You can set your preferred currency for this account.
Choose a Currency
Currency- CHOOSE YOUR CURRENCY
Update Currency
Changing Currency will cause your current cart to be deleted. Click OK to proceed.
To Keep your current cart, click CLOSE and then save your cart before changing currency.
-
Select Account
Switching accounts will update the product catalog available to you. When switching accounts, your current cart will not move to the new account you select. Your current cart will be available if you log back into this account again.
Account# Account Name City Zip/Post Code CANCELPROCEEDMy Account
-
Support
- View All Productivity Solutions
- Warranties
- Patents
- Global Locations
- Technical Support
- Discontinued Products
- Quality Program and Environmental Compliance
- Return Material Authorization (RMA)
- Legal Documents
- Product Certification
- Software Downloads
- Cyber Security Notifications
- Case Studies and Success Stories
- View All Sensing Solutions
- Sales Contact Form
- Technical Support
- Certificates
- eCOM Portal
- Distributor Inventory
- Return Material Authorization (Test & Measurement)
- Return Material Authorization (Citytech)
- Return Material Authorization (EnviteC)
- Legal Documents
- Intelligent Life Care
- Return Material Authorization (ILC)
-
Global
-
Africa
-
Asia Pacific
-
Europe
-
Latin America
-
Middle East
-
North America
- |
- Partners
- |
You are browsing the product catalog for
You are viewing the overview and resources for
- News & Events
- Featured stories
- Simulations Can Answer Questions About Potential DC Automation Changes
Simulations Can Answer Questions About Potential DC Automation Changes
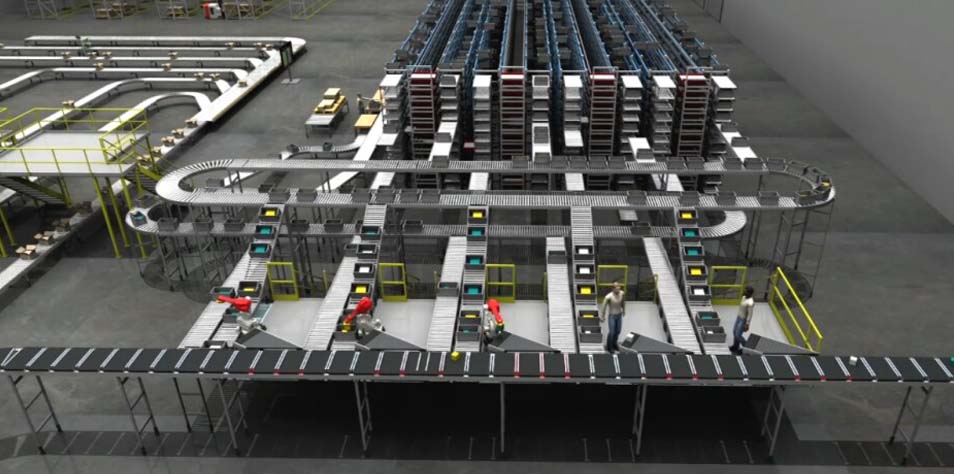
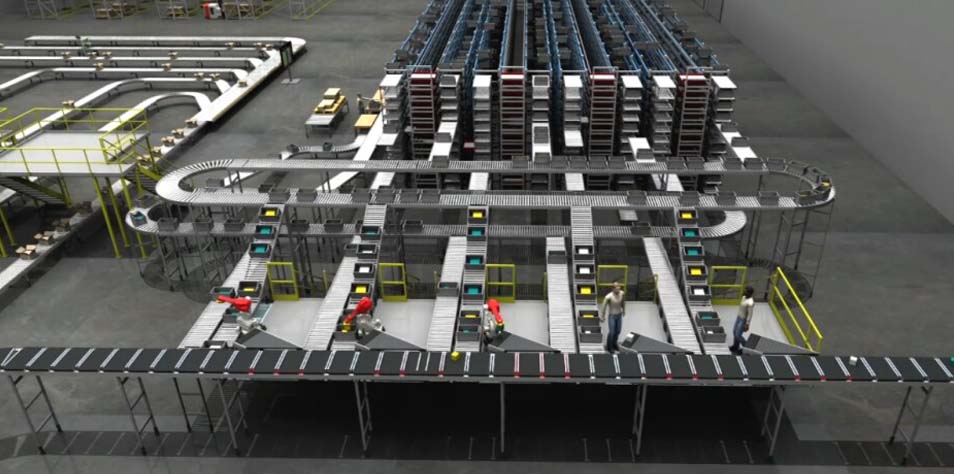
Simulations Can Answer Questions About Potential DC Automation Changes
John Daugherty
October 19, 2020
In our current, pandemic-influenced environment, it should come as no surprise that surveys of companies with supply chain organizations have found automation to be top of mind. After all, such solutions can increase productivity, accuracy and throughput while helping operations safeguard worker health with social distancing and other safety protocols. Our own research has found that 43% of large (1,000+ employees) companies cite improving automation processes in distribution centers (DCs) as one of their top three business goals. More than half of those same respondents, however, believe their organization is unprepared to achieve that objective. This paradox introduces an aspect of risk.
One tool to help reduce such risk is simulation. Simulation refers to the representation of a physical environment — either one already in existence (brownfield) or one not yet constructed (greenfield) — as a computer model upon which different tests, or scenarios, are run. Simulation programs determine what would happen (i.e., “what ifs”) if different aspects of the model are changed. Because the model allows time to be sped up, hundreds of “days” can be run within a single simulation. What’s more, there’s no limit on the amount or types of scenarios that can be simulated.
For clarification, the term simulation is often confused with emulation and the concept of digital twins. Emulation connects a simulation model to the machine code in an actual control device, such as a programmable logic controller (PLC); it is often used as part of on-site commissioning to verify correct operation of new automated equipment prior to going live. A digital twin is a simulated or emulated model that duplicates a real-world environment to enable planning, predictions or forecasting based on the outcomes of different scenarios.
In our most recent On The Move webinar, I shared how discrete event simulation can help companies leverage data-driven design methodologies to safely envision a more automated, future iteration of their DC operations.
How can simulation help?
Discrete event simulations answer specific operational questions, typically about the impacts of changes made to a DC — such as the addition of automation — while mitigating the risks associated with making those changes in real life.
To successfully utilize simulation, it is important to follow these steps:
- Develop a specific question. The more pointed the query, the more successful the simulation will be in answering it. When creating a simulation for a brownfield facility, the objective is usually to answer two questions: a) Will the suggested changes work? b) How will our current operations be improved by these changes? The goals of greenfield facility simulations are to validate that the design will work prior to implementation, and to determine if there are even more efficient ways to achieve the facility owner’s objectives.
- Source appropriate, actual data. Data will come from three key business processes: physical (e.g., equipment, technologies), logical (e.g., routing, process) and operational (e.g., waves, shifts, operators). For example, the question “How will changing shifts affect throughput?” primarily requires operational data, with some logical data and a little bit of physical data.
- Define data subsets. These are based on the question to be answered. Creating these definitions requires a deep dive into details about orders, products, inventory, travel times, turn times, distances, equipment utilization, read/failure rates, throughput requirements and more.
- Take “CARE” of the data. That is, ensure data is: complete, accurate, representative and error-free. Doing so often becomes the most time-intensive portion of the process yet is of critical importance to achieving a successful simulation that delivers the most accurate predictions.
- Build the simulation model. Make sure it allows for quick, easy changes that enable testing of different scenarios. The more flexible the model, the greater the ability to delve deeper into some of the insights and perspectives that may arise.
To learn more about how simulation technologies can answer your questions about potential DC changes — as well as how artificial intelligence (AI) and machine learning (ML) will enhance simulations in the future — view the Simulate the Future of Your Distribution Center webinar.
To subscribe to our blog and receive exclusive communications and updates from Honeywell Intelligrated, click here.
Let's Connect!
Sign up to receive exclusive communications from Honeywell including product updates, technical information, new offerings, events and news, surveys, special offers, and related topics via telephone, email, and other forms of electronic communication.
Copyright © 2025 Honeywell International Inc
Maximum File Size
Maximum Files Exceeded
Due to inactivity you will be logged out in 000 seconds.
Maximum File Size
Maximum Files Exceeded
You cannot access this page as this product is not available in your country.