-
Global
-
Africa
-
Asia Pacific
-
Europe
-
Latin America
-
Middle East
-
North America
- |
- Partners
- |
-
Currency:Localize your Content
You can set your preferred currency for this account.
Choose a Currency
Currency- CHOOSE YOUR CURRENCY
Update Currency
Changing Currency will cause your current cart to be deleted. Click OK to proceed.
To Keep your current cart, click CLOSE and then save your cart before changing currency.
-
Select Account
Switching accounts will update the product catalog available to you. When switching accounts, your current cart will not move to the new account you select. Your current cart will be available if you log back into this account again.
Account# Account Name City Zip/Post Code CANCELPROCEEDMy Account
-
Support
- View All Productivity Solutions
- Warranties
- Patents
- Global Locations
- Technical Support
- Discontinued Products
- Quality Program and Environmental Compliance
- Return Material Authorization (RMA)
- Legal Documents
- Product Certification
- Software Downloads
- Cyber Security Notifications
- Case Studies and Success Stories
- View All Sensing Solutions
- Sales Contact Form
- Technical Support
- Certificates
- eCOM Portal
- Distributor Inventory
- Return Material Authorization (Test & Measurement)
- Return Material Authorization (Citytech)
- Return Material Authorization (EnviteC)
- Legal Documents
- Intelligent Life Care
- Return Material Authorization (ILC)
-
Global
-
Africa
-
Asia Pacific
-
Europe
-
Latin America
-
Middle East
-
North America
- |
- Partners
- |
You are browsing the product catalog for
You are viewing the overview and resources for
- News & Events
- Featured stories
- Offset Labor Challenges With AS/RS Shuttle Automation
Offset Labor Challenges With AS/RS Shuttle Automation
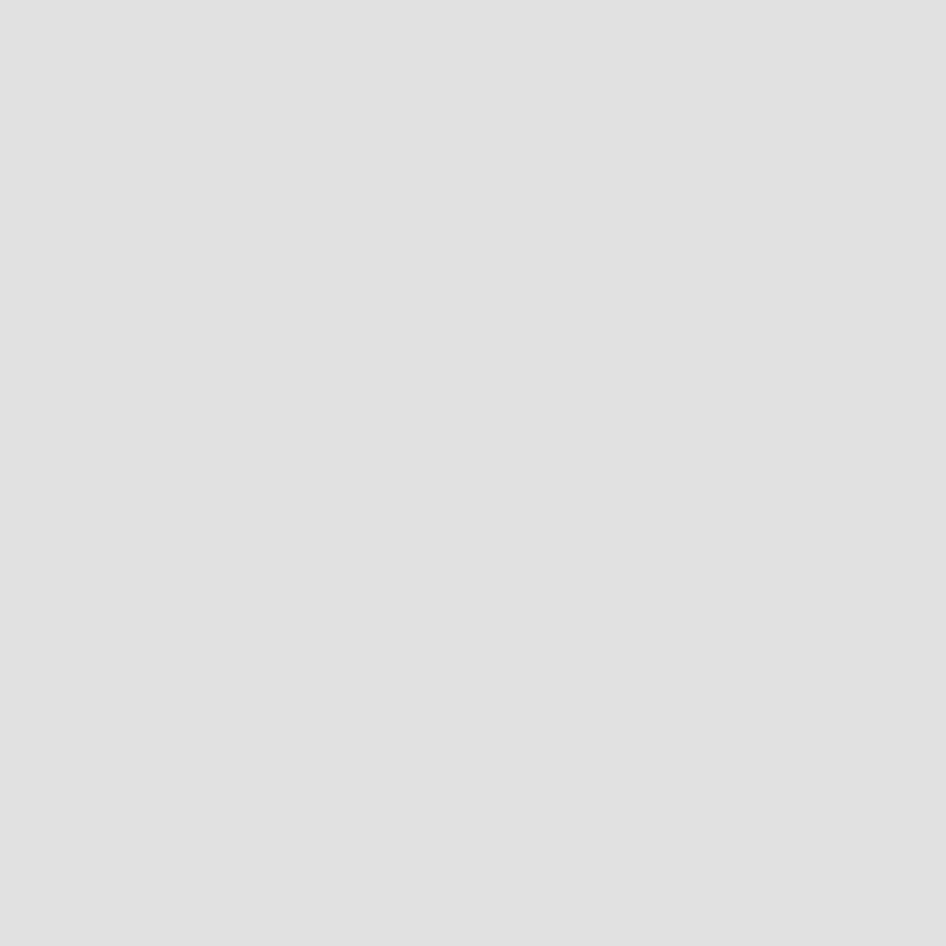
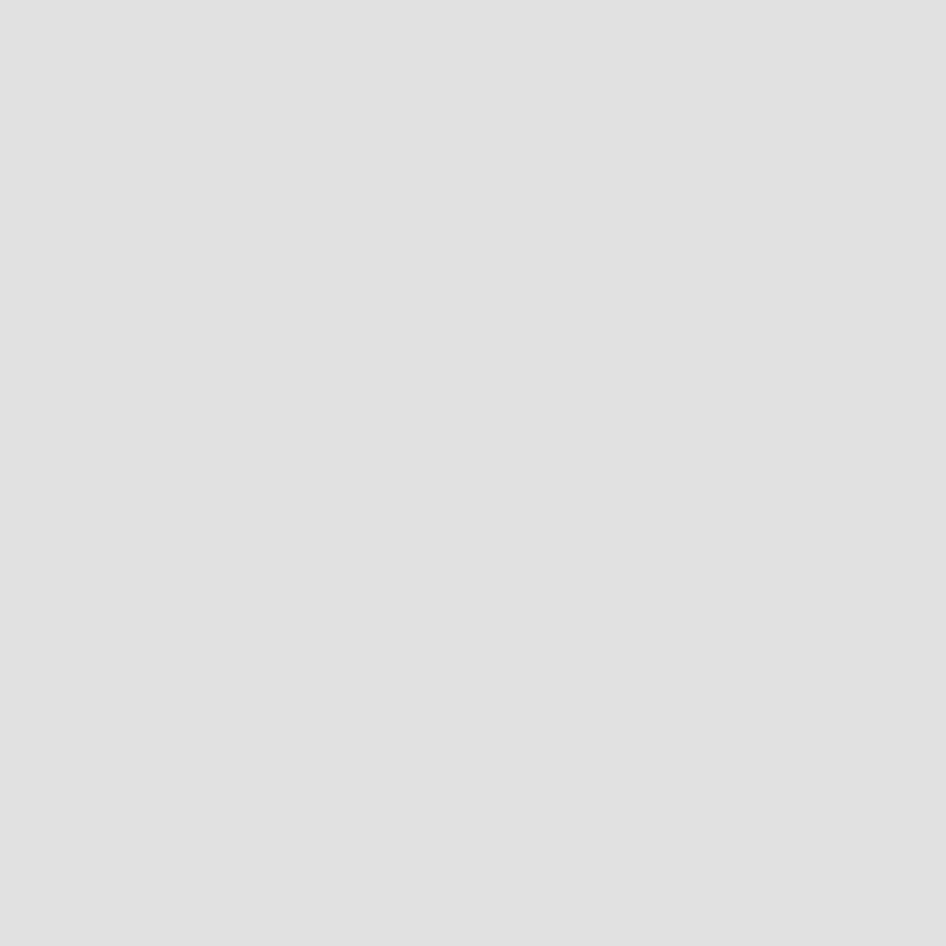
Offset Labor Challenges With AS/RS Shuttle Automation
June 16, 2020
Rapidly increasing customer expectations are creating a challenging fulfillment landscape. E-commerce order volumes are three times higher than the retail industry as a whole. Consumers want greater product variety, creating larger and more volatile inventories, and they expect fast — and free — delivery. Mass urbanization adds additional challenges by limiting the availability of warehouse space and making prime locations more expensive.
These demands are compounded by a shrinking labor pool, which is placing upward pressure on wages. U.S. warehouses currently face 600,000 unfilled jobs and a 25 percent turnover rate. The cost of finding and training a replacement can easily reach 25 percent of a lost worker’s salary — not to mention lost productivity, stress on other associates while a position is being filled, training time and reduced efficiency during onboarding. In this challenging environment, you need to make the best use of the valuable labor you have and keep them sufficiently engaged so they aren’t tempted to seek other employment options.
Automation and fulfillment technologies can help you achieve both of these goals by shifting your picking workflow from traditional operator-to-goods (OTG) processes to a goods-to-operator (GTO) fulfillment model.
An operator-to-goods workflow is like shopping in a supermarket, where workers spend as much time walking between pick locations as they do picking. Adding more workers offers only diminishing returns, as overcrowding and aisle congestion create higher cycle times. The benefits of low capital investment are quickly lost to high operating costs, which are increasingly unsustainable in today’s competitive market.
In contrast, costly walk time is completely eliminated in the goods-to-operator fulfillment model, which uses automation to retrieve inventory and deliver it to employees. Think of the carousels that bring clothing directly to the worker at the front of a dry cleaner and you have the basic idea behind GTO.
GTO workflows tackle the continual problem of sourcing labor by enabling significantly higher pick rates while reducing overall labor requirements. GTO facilities maintain high efficiency as order volumes rise when demand spikes require boosting the system’s capacity at a moment’s notice. Workers also reap the benefits of improved ergonomics, higher safety, increased focus and greater long-term productivity.
While GTO systems require more capital investment, their operational benefits and lower operating costs drive sustainable long-term savings. Simply put, more orders are fulfilled faster and with greater accuracy using fewer employees.
Automated storage and retrieval system (AS/RS) shuttles are essential in the GTO model. These powerful warehouse automation systems enable:
- Greater storage density
- More storage capacity
- Layout flexibility
- Easier scalability
- Quicker access to inventory to feed downstream processes
Shuttles deliver these benefits by retrieving inventory in cartons, totes, cases or other storage media from narrow aisles. End-of-aisle lifts enable shuttles to travel between rows, and multiple shuttles can operate in the same row to increase throughput capacity. Compared to other AS/RS solutions, shuttles offer the most efficient method of satisfying the growing demands of e-commerce distribution.
While AS/RS is a significant investment, the current industry environment and the return on investment far outweigh the cost. GTO and AS/RS deliver the following benefits:
- Ease of finding, training and retaining labor
- Reduced operating costs
- Deferred need to invest in new facilities
- Increased throughput
Read our white paper to learn how AS/RS can increase efficiency for high-volume, e-commerce fulfillment operations.
To subscribe to our blog and receive exclusive communications and updates from Honeywell Intelligrated, click here.
Let's Connect!
Sign up to receive exclusive communications from Honeywell including product updates, technical information, new offerings, events and news, surveys, special offers, and related topics via telephone, email, and other forms of electronic communication.
Copyright © 2025 Honeywell International Inc
Maximum File Size
Maximum Files Exceeded
Due to inactivity you will be logged out in 000 seconds.
Maximum File Size
Maximum Files Exceeded
You cannot access this page as this product is not available in your country.