-
Global
-
Africa
-
Asia Pacific
-
Europe
-
Latin America
-
Middle East
-
North America
- |
- Partners
- |
-
Currency:Localize your Content
You can set your preferred currency for this account.
Choose a Currency
Currency- CHOOSE YOUR CURRENCY
Update Currency
Changing Currency will cause your current cart to be deleted. Click OK to proceed.
To Keep your current cart, click CLOSE and then save your cart before changing currency.
-
Select Account
Switching accounts will update the product catalog available to you. When switching accounts, your current cart will not move to the new account you select. Your current cart will be available if you log back into this account again.
Account# Account Name City Zip/Post Code CANCELPROCEEDMy Account
-
Support
- View All Productivity Solutions
- Warranties
- Patents
- Global Locations
- Technical Support
- Discontinued Products
- Quality Program and Environmental Compliance
- Return Material Authorization (RMA)
- Legal Documents
- Product Certification
- Software Downloads
- Cyber Security Notifications
- Case Studies and Success Stories
- View All Sensing Solutions
- Sales Contact Form
- Technical Support
- Certificates
- eCOM Portal
- Distributor Inventory
- Return Material Authorization (Test & Measurement)
- Return Material Authorization (Citytech)
- Return Material Authorization (EnviteC)
- Legal Documents
- Intelligent Life Care
- Return Material Authorization (ILC)
-
Global
-
Africa
-
Asia Pacific
-
Europe
-
Latin America
-
Middle East
-
North America
- |
- Partners
- |
You are browsing the product catalog for
You are viewing the overview and resources for
- News & Events
- Featured stories
- Improve Uptime With a Predictive Lifecycle Management Program
Improve Uptime With a Predictive Lifecycle Management Program
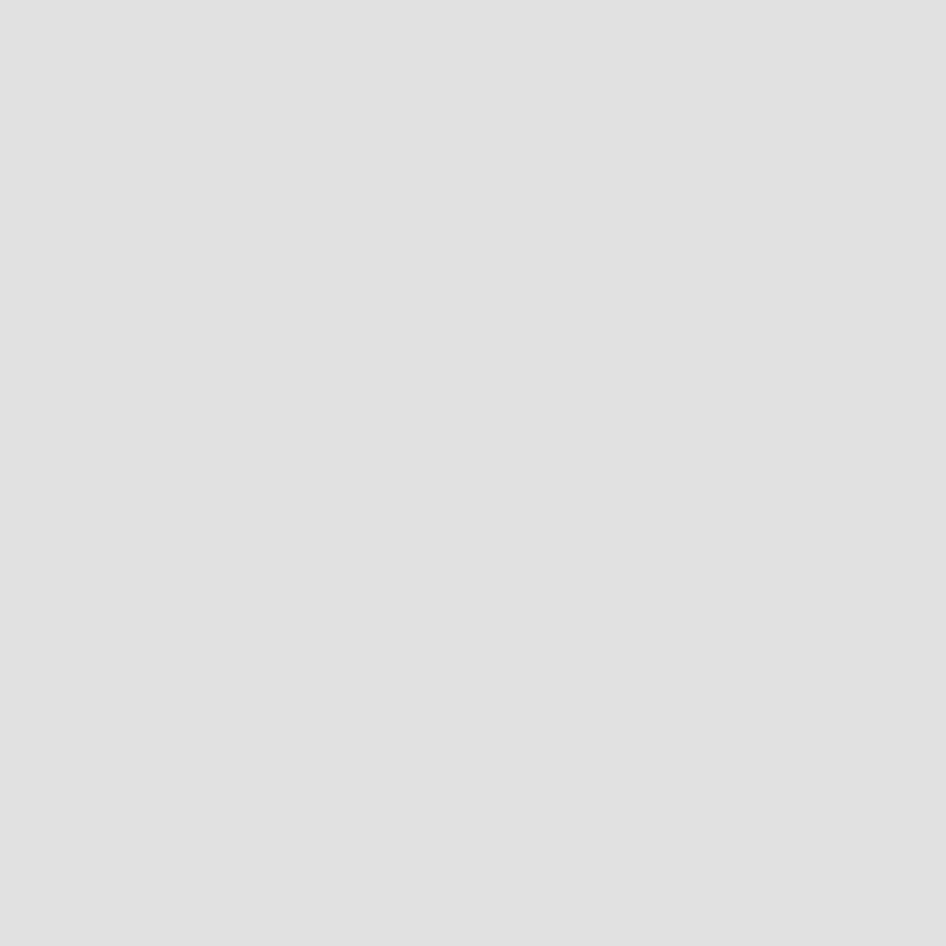
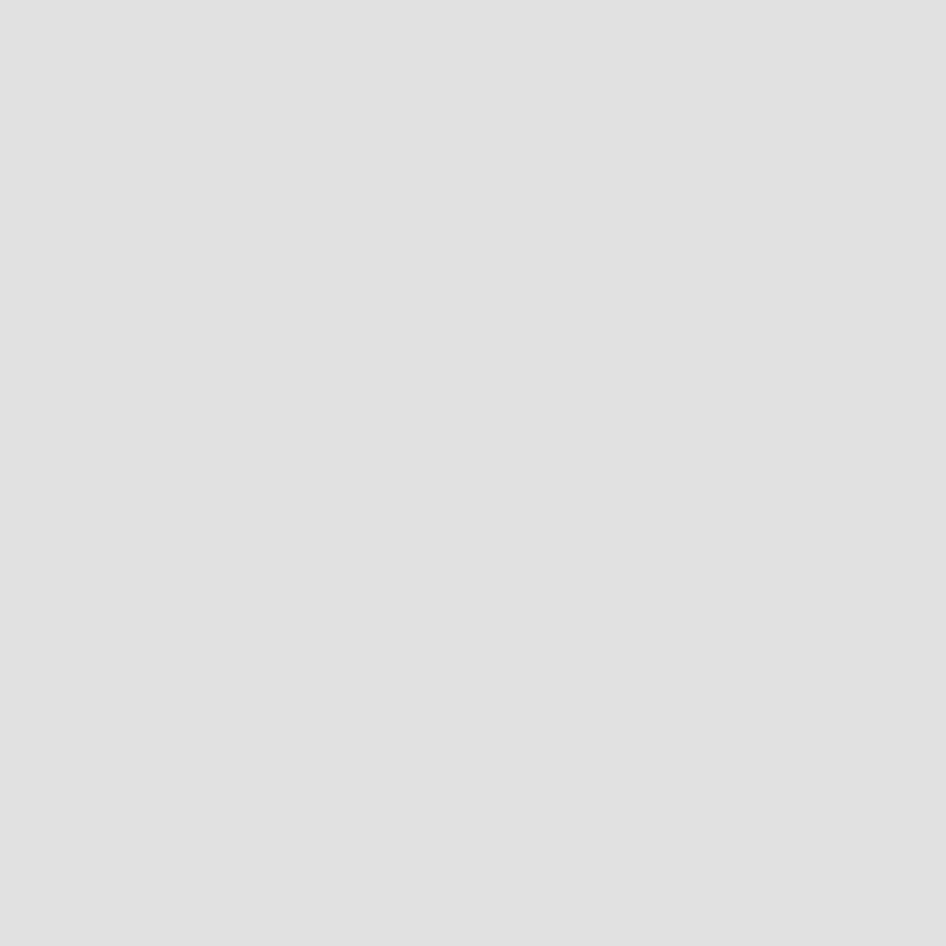
Improve Uptime With a Predictive Lifecycle Management Program
Diane Blair
May 4, 2020
For decades, distribution center (DC) operators have relied on a mix of gut-level intuition and hope to meet throughput targets and business objectives. In fact, nearly two-thirds of supply chain companies confess to not using any technology to monitor their supply chain performance.
But now our industry is at a crossroads. DC operators can maintain business as usual, which will yield diminishing returns as the market continues its shift to next-day and same-day delivery. Or they can tap into an abundance of readily accessible operational data to boost uptime and increase the lifespan of their assets.
As many pure play e-tailers have already determined, the traditional strategy of “react and respond” won’t cut it anymore in today’s hypercompetitive environment. There just isn’t enough slack in the market or cushion in the margins to operate at less than full capacity. This will become increasingly apparent — and painful — as cycle times continue to tighten and consumer service level agreements become more taxing.
To not just survive — but thrive — in this landscape, DC operators must shift to an “analyze and predict” model. By utilizing operational data within a robust lifecycle management program, operators can achieve the efficiency and predictability that are critical to sustainable growth.
A smarter predictive maintenance program
Using data to optimize assets and drive productivity isn’t a radical concept; the benefits have been widely documented for years across a range of industries. Per the Department of Energy, using data in functional predictive maintenance programs has the potential to deliver:
- 10X return on investment
- 25–30% reduction in maintenance costs
- 70–75% elimination of equipment breakdowns
- 35–40% decrease in downtime
- 20–25% increase in production
For distribution centers, much of the data required to drive operational improvements already exists within their control systems. It’s simply a matter of adding machine-level sensors and overlaying both with a data analytics software platform. User-friendly dashboards and performance alerts will translate the data into insights that operators can use to:
- Immediately triage issues with equipment or processes as they arise
- Improve productivity during production
- Optimize maintenance and operations
- Predict and avoid unplanned downtime
As data on their equipment and systems accumulates, operators can fine-tune their maintenance programs. The overall goal is to not just detect, but rather predict and address conditions that degrade performance and productivity. In effect, 99.9 percent uptime could be within reach.
Establishing a foundation for success
DC operators don’t need to be data scientists to implement data-driven lifecycle programs. They do, however, need to ensure the right cultural conditions are in place for the program to take root. Making the switch from managing by gut to strategizing with data requires buy-in from all stakeholders. Floor-level employees in particular may be reluctant to embrace a new standard of operations that will likely change expectations for their own performance.
A successful transition plan will include some degree of change management. This will require that operators:
- Establish a culture of transparency
- Promote trust between functions
- Clearly define their desired business outcomes and ensure that everyone is working toward them
Over the long term, predictive maintenance technologies will help decrease the production downtime and shipping delays that chip away at profitability. By continually highlighting how these outcomes benefit everyone, DC operators can turn even skeptical stakeholders into advocates for a data-driven culture.
At Honeywell Intelligrated, we’re creating the tools to help companies embrace data utilization in their lifecycle management programs. To learn more about how predictive maintenance technologies can deliver on your business outcomes, read our On The Move article, "The Journey to Predictability."
To subscribe to our blog and receive exclusive communications and updates from Honeywell Intelligrated, click here.
Let's Connect!
Sign up to receive exclusive communications from Honeywell including product updates, technical information, new offerings, events and news, surveys, special offers, and related topics via telephone, email, and other forms of electronic communication.
Copyright © 2025 Honeywell International Inc
Maximum File Size
Maximum Files Exceeded
Due to inactivity you will be logged out in 000 seconds.
Maximum File Size
Maximum Files Exceeded
You cannot access this page as this product is not available in your country.