-
Global
-
Africa
-
Asia Pacific
-
Europe
-
Latin America
-
Middle East
-
North America
- |
- Partners
- |
-
Currency:Localize your Content
You can set your preferred currency for this account.
Choose a Currency
Currency- CHOOSE YOUR CURRENCY
Update Currency
Changing Currency will cause your current cart to be deleted. Click OK to proceed.
To Keep your current cart, click CLOSE and then save your cart before changing currency.
-
Select Account
Switching accounts will update the product catalog available to you. When switching accounts, your current cart will not move to the new account you select. Your current cart will be available if you log back into this account again.
Account# Account Name City Zip/Post Code CANCELPROCEEDMy Account
-
Support
- View All Productivity Solutions
- Warranties
- Patents
- Global Locations
- Technical Support
- Discontinued Products
- Quality Program and Environmental Compliance
- Return Material Authorization (RMA)
- Legal Documents
- Product Certification
- Software Downloads
- Cyber Security Notifications
- Case Studies and Success Stories
-
Global
-
Africa
-
Asia Pacific
-
Europe
-
Latin America
-
Middle East
-
North America
- |
- Partners
- |
You are browsing the product catalog for
You are viewing the overview and resources for
- News & Events
- Featured stories
- Your DC Is Never Too Small for Voice: Evaluating Voice Versus Paper-Based, RF Scanners and Pick-to-Light Solutions
Your DC Is Never Too Small for Voice: Evaluating Voice Versus Paper-Based, RF Scanners and Pick-to-Light Solutions
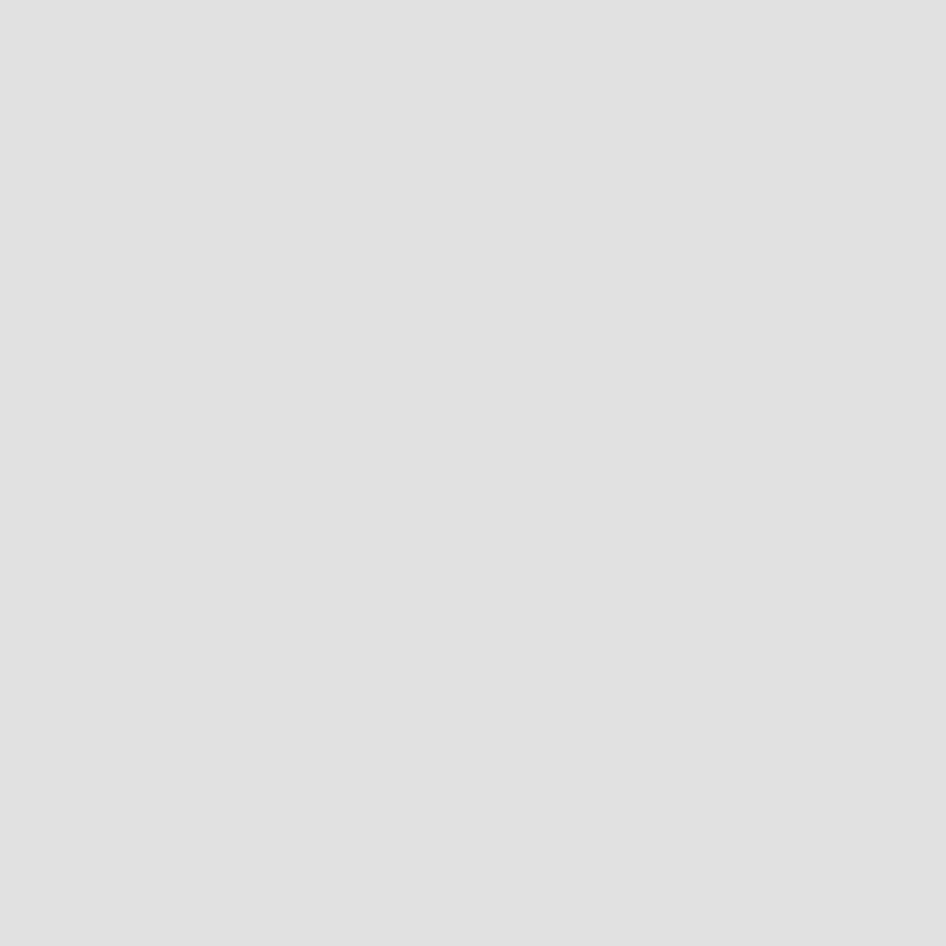
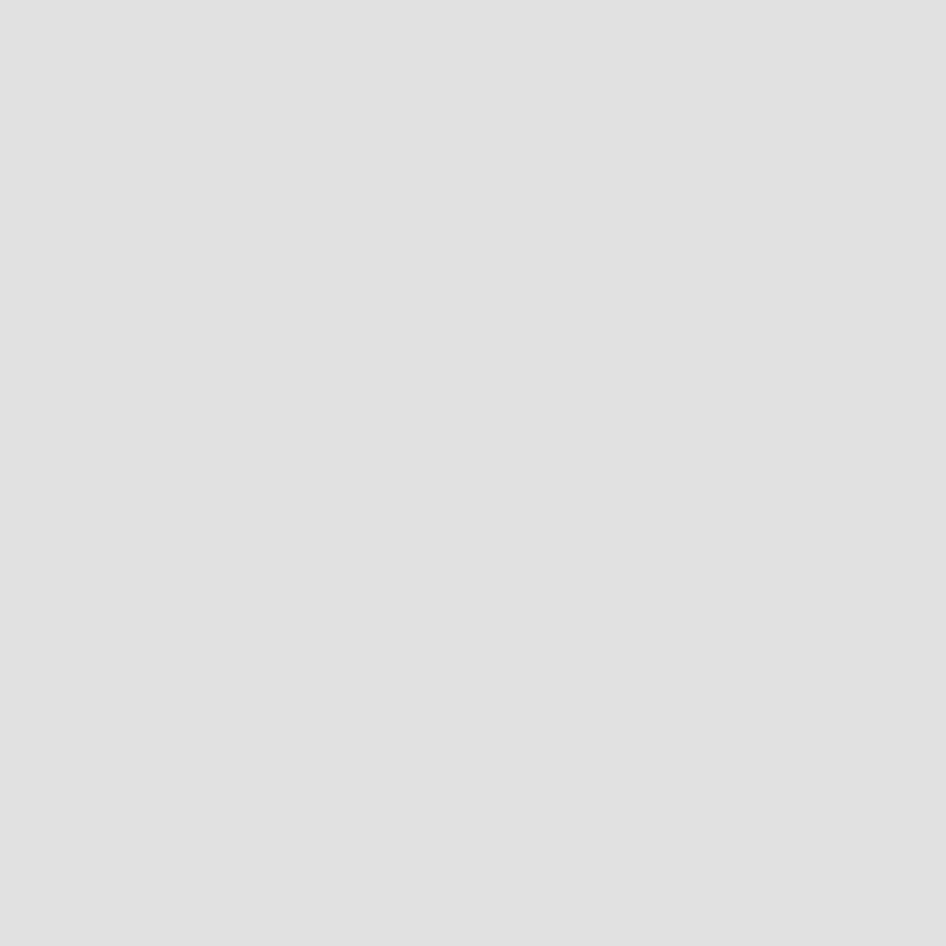
Your DC Is Never Too Small for Voice: Evaluating Voice Versus Paper-Based, RF Scanners and Pick-to-Light Solutions
Barry J. Ewell
June 26, 2020
Maximizing DC/warehouse utilization and consistently maintaining peak performance are common goals shared by operations. This starts with identifying and evaluating your unique business requirements and addressing your most common challenges with solutions that will consistently deliver required outcomes.
For many, analog or paper-based systems are still a big part of many everyday tasks and workflows. This methodology is highly prone to introduce errors in every step of the process, and severely impairs receiving, inventory counting, picking and packing workflows. Companies are taking paper out of the equation and employing automation solutions such as radio frequency (RF) scanners, light- and voice-directed picking, mobile computers and scanners to drive significant efficiency and accuracy improvements.
Building a Case for Voice-Directed and Hands-Free Workflows
Traditionally, when we first approach small- to medium-sized operations (between 100,000 and 500,000 square feet) about using Honeywell Voice as a replacement and/or alternative for paper-based, pick-to-light or RF scanner solutions, we get answers like:
- “We are too small.”
- “It’s too expensive.”
Per Gartner: Voice-directed warehouse management solutions involve the use of speech recognition and/or speech synthesis technologies to drive activities in warehouse operations, integrating speech-collected information into a WMS or other database. This enables hands-free operations for tasks such as carton or ‘eaches’ (single-item) picking, where the additive data collection steps can be removed with the use of speech input. This provides 40% to 50% improved productivity for a similar task that, historically, required paper-based or barcode data collection.
Enterprises that use speech recognition applications to replace paper-based picking or pick-to-light solutions can achieve a ROI in less than one year. Other applications in the warehouse that can also use speech recognition include receiving, shipping, put-away and cycle-counting, and/or inventory management, and the payback on these implementations is getting more attractive with the elimination of specific-use data collection devices.1
Use cases for the technology are fairly-well understood and technical barriers to adoption are pretty much nonexistent. The once-high costs of adopting voice are now on par with other technologies.
Gartner continues, “Bottom line: voice works, the filtering is strong, and the use cases are well-proven. Adoption has primarily been constrained by higher costs for voice hardware and software when compared to conventional mobile ruggedized radio frequency (RF) scanning devices. While transactional voice offerings had higher costs, these costs have come down as vendors have transitioned from traditional rugged devices to more consumer-grade devices, so interest in voice is growing again.”2
Voice vs. Paper-Based, RF Scanners, and Pick-to-Light
Honeywell Voice works closely with each DC by conducting an assessment and walkthrough that seeks to understand their strategic business challenges, goals, and processes. The following is a brief overview and consolidation of what our customers tell us about what they have experienced with each type of solution that is present in DC/warehouse workflows.
Paper/Label-Based Systems vs. Voice
Many small- to medium-sized warehouses were built around paper-based systems. Invoices were on paper. Work instructions were written down. Bills of materials, routings, receipts, material movements, and many other things were maintained through paper. Paper-based processes are filled with steps that can bog down productivity levels and efficiency. For example, within the picking process, you can easily see eight or more steps:
- Orders entered into order entry system
- Pick tickets printed
- Pickers read each line item (SKU and quantity)
- Pickers walk the warehouse, searching for pick slots
- Each line item is picked into a tote, cart or forklift
- Picker walks entire pick path for each order
- Picked orders are checked for accuracy
- Orders are packed for shipping
As we perform DC assessments and walkthroughs, we see the following types of problems with paper-based picking:
- Items can be omitted from orders. In batch processes, inventory information is routinely not updated when the event occurs or there is poor-quality inventory counting. This can be the cause for omitting an item on the order, even though the items are in stock.
- Picking the wrong item. When a worker goes to the wrong location or multiple items are commingled in the same pick location, it is easy for the wrong item to be chosen.
- Miscounting the quantity. This happens when the worker reads the correct quantity but miscounts the pieces to be picked. This can easily happen when there are large quantities in units to be picked from split- or full-case locations.
- Quantities are misread or transposed. This takes place when the worker misreads the quantity. The root cause can be pick list formatting, faded printer ink on the pick list, or poor lighting.
Improvement with voice. Typically, when a company chooses to replace their paper-based system with voice, they realize:
- 10–15+% increase in productivity (faster)
- 80% increase in accuracy with 10–20 less errors per 1,000
- 60% reduced time in training
- Real-time associate visibility and accountability
- Real-time inventory, people and system updates
- Ability to batch-pick
- Substantial reduction in data errors
- Reduced cost in labor and materials that were used to handle paper
- Hands-free and eyes-free
Pick-to-Light vs. Voice
Pick-to-Light (PTL) systems use a lighting system to guide manual picking. PTL consists of light displays that are mounted per each pick location in shelving units, storage racks, work benches and other storage locations. The order picking tasks are downloaded to a system that lights up the display for workers to know where to go. The light identifies the pick location where the pick is to take place. The display denotes the pick quantity and which carton/tote to place the items. The operator confirms the completion of a pick by pressing the lighted button. PTL is designed to be a team-based process where each operator covers a series of bins that equal a zone. Orders are usually passed from zone to zone via cart or conveyor.
As we talk with DCs using pick-to-light systems, we consistently receive the following comments from operators:
- PTL investment based on number of SKUs. Initial costs for PTL systems are based on the number of SKUs, which quickly becomes impractical for many companies.
- High maintenance costs. As the PTL system ages into the third year, components such as buttons, lights and displays regularly fail. When it comes time to adjust, users find PTL inflexible, not portable, and difficult to reconfigure.
- Productivity losses due to “jams” caused by unbalanced zones. Once the initial zones are created, picking can equal among zones. As time passes, the picking becomes unbalanced among operators, thus causing what is referred to as jams, with some zones picking more than others, causing consistent slowdowns in the line.
Improvement with voice. Typically, when a company chooses to replace their pick-to-light system with voice, they realize:
- 15–25+% increase in productivity (faster)
- 80% increase in accuracy with 2–4 less errors per 1,000
- 50–55% reduced time in training
- Dramatically reduces chances for workflow bottlenecking
- Can assign workers where needed
- Easily expand, reduce or rearrange warehouse space/shelving
- Reduce points of failure associated with pick-to-light system
- Ability to batch-pick
RF Scanning vs. Voice
RF scanning devices are used across all workflows in the warehouse because they are capable of capturing product- and customer-specific information (e.g., lot number, serial number, catch weight). Some of the common problems we hear from customers include:
Errors. Errors happen because barcodes are missing or damaged, the operator scans the right product but picks the wrong quantity after placing the device down, etc.
- Many points of failure. Common problems like device battery issues cause workers to need to find replacement devices, batteries, etc. Devices are regularly dropped or fall from placement while completing an assignment or are misplaced and lost, which adds to the total cost of ownership (TCO) and need of spare pools for replacement of 30% more devices.
- Cumbersome keyboard interaction and device placement. Keyboards are small, require the user to input quantity, and can be a common point of error. Workers are constantly needing to find a safe place to put the device while completing workflow assignments. This can be on the racking, cart or under the arm, thus slowing and adding more steps in the process.
- Productivity drop with change in technology. When moving from paper-based systems to RF scanning, there can be as high as a 20% loss in productivity because of the interaction with the device. The upside is you get increased accuracy from scanning.
- Eyes off the product creates errors. Every time you look at the scan gun screen or place the device down, eyes are taken off the product. Simple errors like picking the wrong product or scanning the wrong barcode/label can occur.
- Safety and ergonomic issues. With a handheld device, the worker is often unaware of their surroundings, creating real safety issues with moving equipment and other workers. Devices can be cumbersome and heavy, which is cause for ergonomic strain.
- Extensive training. Training can take up to two weeks to learn the system.
Improvement with voice. Typically, when a company chooses to replace their RF scanners with voice, they realize:
- 15–25+% increase in productivity (faster)
- 80% increase in accuracy with 2–4 less errors per 1,000
- 50–55% reduced time in training
- Training reduced to hours
- Productivity increases because you do not have to carry a device, press keys, scan, etc.
- Safety issues are reduced due to workers being more alert to their surroundings
- Hands-free and eyes-free
- Equipment failure and need for spare pool dramatically reduced
Reduced spend on repairs and replacements. The implementation of voice-enabled technologies means a direct reduction in the overall spend on repairs and replacement of expensive scanners, which are usually dropped when having to handle products and the scanners at the same time. By using voice-enabled technology, this becomes one of the more immediate and tangible paybacks apart from improved productivity and data accuracy.
Conclusion
Honeywell Voice is used by nearly one million mobile workers every day, throughout the world, in a variety of tasks/workflows, in almost every kind and size of DC/warehouse operation. Honeywell Voice has been proven to increase productivity by up to 35% and accuracy to 99.99%+. For example, in picking processes where workers follow a series of instructions for specific pick locations, products and quantities, these tools provide needed guidance and verification at every step. Voice is available in more than 35 languages and has been proven to dramatically reduce training and onboarding time, especially in peak seasons with highly transient workforces.
Click here for more information about Honeywell Voice.
Our expert assessment teams will partner with you to understand your unique business requirements and identify where opportunities exist to optimize your workflows and increase efficiencies within today’s competitive climate.
At Honeywell, we work with thousands of distribution centers of all sizes, across a wide variety of industries worldwide. We bring a deep foundational understanding of the businesses we serve, backed with expert research and data that identifies the real, specific needs of today’s DCs.
With over 130 years of on-the-ground experience, Honeywell is uniquely equipped to help you solve the problems that your business faces every day, see improved results, and be a trusted partner to help you reach and exceed your predetermined goals.
Related articles in this six-part series:
Your DC Is Never Too Small for Voice: Using Voice in Many Workflows
Your DC Is Never Too Small for Voice: Honeywell Voice DC Walkthrough and Assessment
Your DC Is Never Too Small for Voice: A Closer Look at Voice in the Picking Workflow
Your DC Is Never Too Small for Voice: Honeywell Guided Work Solutions
Your DC Is Never Too Small for Voice: Meet Five DCs That Chose Honeywell Voice
Sources:
1 Gartner. Revisit Your Ruggedized Strategy Before You’re Hit by the End of OS Support. Leif-Olof Wallin, Stephen Kleynhans, et al. Published 27 March 2017.
2 Gartner. Emerging Technology Analysis: Build Voice-Enabled Technologies Into Manufacturing and Supply Chain Processes. Emil Berthelsen, Tim Zimmerman, et al. Published 30 March 2018.
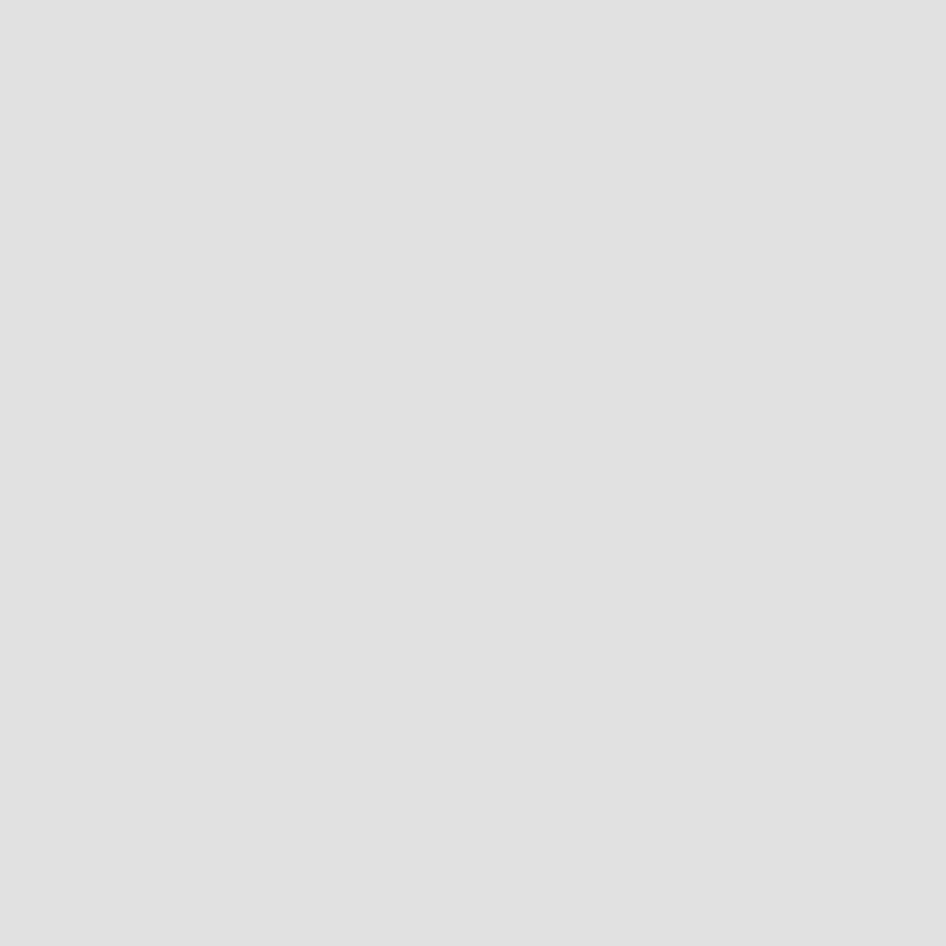
Barry J. Ewell is a Senior Content Marketing Communications Specialist for Honeywell Industrial Automation. He has been researching and writing on supply chain topics since 1991.
Let's Connect!
Sign up to receive exclusive communications from Honeywell including product updates, technical information, new offerings, events and news, surveys, special offers, and related topics via telephone, email, and other forms of electronic communication.
Copyright © 2025 Honeywell International Inc
Maximum File Size
Maximum Files Exceeded
Due to inactivity you will be logged out in 000 seconds.
Maximum File Size
Maximum Files Exceeded
You cannot access this page as this product is not available in your country.