-
Global
-
Africa
-
Asia Pacific
-
Europe
-
Latin America
-
Middle East
-
North America
- |
- Partners
- |
-
Currency:Localize your Content
You can set your preferred currency for this account.
Choose a Currency
Currency- CHOOSE YOUR CURRENCY
Update Currency
Changing Currency will cause your current cart to be deleted. Click OK to proceed.
To Keep your current cart, click CLOSE and then save your cart before changing currency.
-
Select Account
Switching accounts will update the product catalog available to you. When switching accounts, your current cart will not move to the new account you select. Your current cart will be available if you log back into this account again.
Account# Account Name City Zip/Post Code CANCELPROCEEDMy Account
-
Support
- View All Productivity Solutions
- Warranties
- Patents
- Global Locations
- Technical Support
- Discontinued Products
- Quality Program and Environmental Compliance
- Return Material Authorization (RMA)
- Legal Documents
- Product Certification
- Software Downloads
- Cyber Security Notifications
- Case Studies and Success Stories
- View All Sensing Solutions
- Sales Contact Form
- Technical Support
- Certificates
- eCOM Portal
- Distributor Inventory
- Return Material Authorization (Test & Measurement)
- Return Material Authorization (Citytech)
- Return Material Authorization (EnviteC)
- Legal Documents
- Intelligent Life Care
- Return Material Authorization (ILC)
-
Global
-
Africa
-
Asia Pacific
-
Europe
-
Latin America
-
Middle East
-
North America
- |
- Partners
- |
You are browsing the product catalog for
You are viewing the overview and resources for
- News & Events
- Featured stories
- Personal Protective Equipment
- Three Gas Detector Technologies that Save Lives
Three Gas Detector Technologies that Save Lives
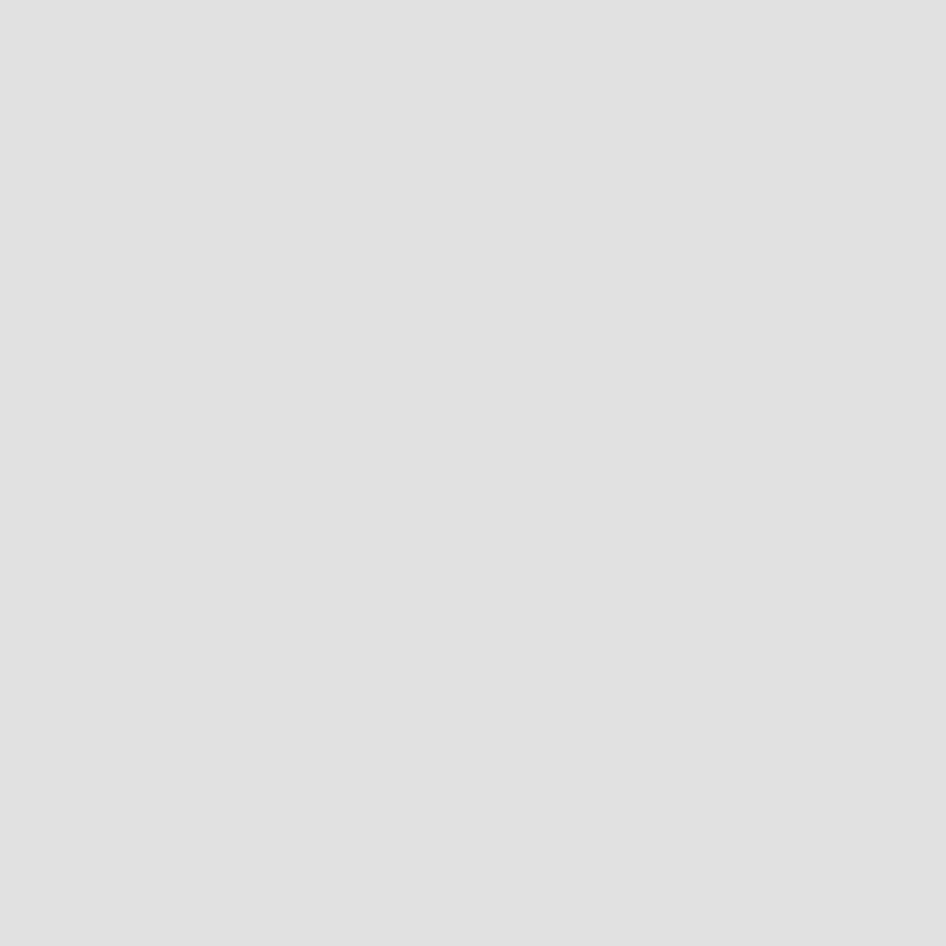
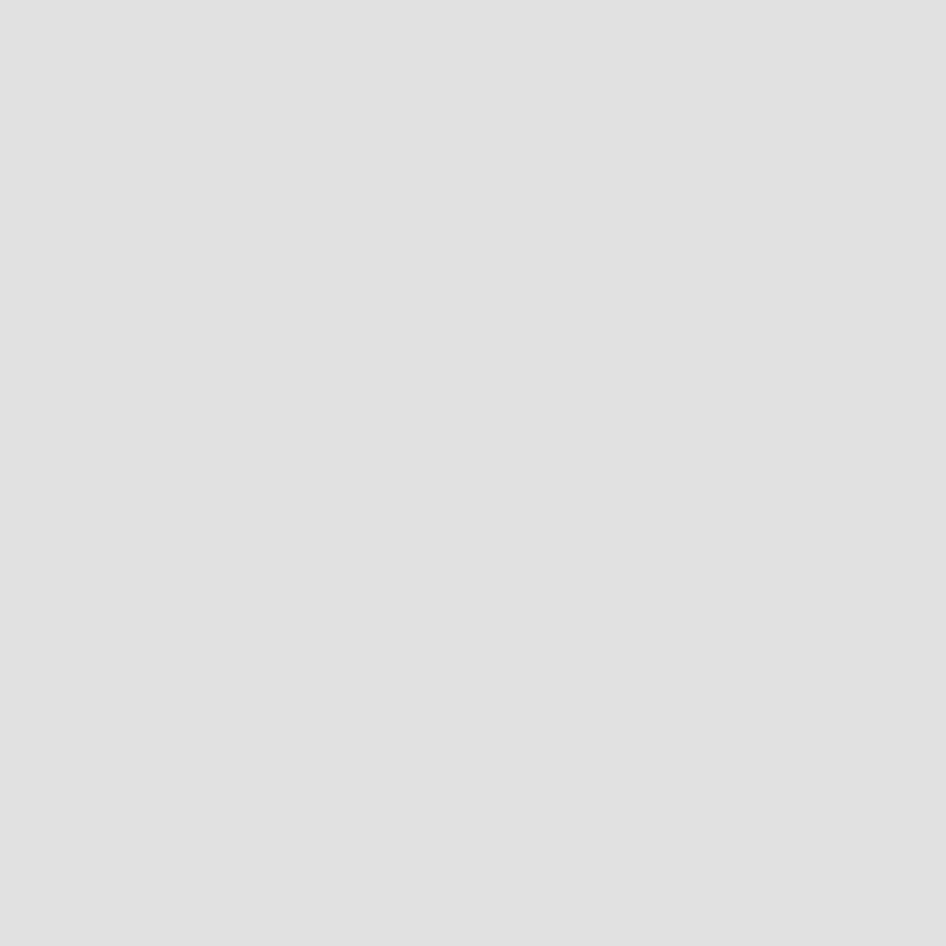
Three Gas Detector Technologies that Save Lives
“Growth is never by mere chance; it is the result of forces working together,” James Cash Penney, the founder of JC Penney says . And the force that works for your business growth as hard as you do is an optimal safety plan that relies on a gas detection solution that best suits your needs, we would add.
In a working environment, safety failings lead to tragic consequences. Delayed gas leak detection poses a huge threat on property, environment and human life. On average, 17 people die each year due to gas leaks in the United States, according to The American Chemical Society. Such incidents also cause about $133 million in property damage annually.
Not getting a handle on your risk management endangers your team morale, the respect of your customers and the productivity and innovation. Here are three gas detection technologies that help you manage gas-related risks.
Early warning signs
Industrial operations imply the production and use of highly dangerous substances such as flammable, toxic gases. The most common igniting gas in industrial facilities, commercial and residential fields is hydrocarbon flammable gas, used for fuel, power generation, heating, and cooking.
Occasional gas escapes are inevitable, creating a potential hazard to industrial plants, employees, nearby neighborhoods, often causing explosions, asphyxiation, and loss of life. In all industries, any safety plan relies on early-warning devices such as gas detectors, that can save lives, protect the plants, and help eliminate environmental incidents.
Gas detectors are commonly used in industrial facilities, in different industries such as oil and gas (offshore platforms, onshore refineries and chemical plants), natural gas facilities, steel mills, printing plants, construction, mining, and utilities.
Flammable gas detector types
Gas detection sensors allow adequate time for protective or remedial measures. They are either independent solutions or part of a total integrated monitoring and safety system, in a layered safety approach.
Safety needs are as diverse as businesses and these are three flammable gas detection solutions to include in your safety plan.
Point Infrared (PI) - the primary detection
PI is a hydrocarbon gas detector that continuously monitors to detect a 5 m3 mass of combustible gas and vapors, the calculated size of a gas cloud that could cause structural damage in case of an explosion.
Placed within a few meters of a leak source, PI gives accurate quantification of actual gas concentration at a point in space and time.
PI can be used in inert atmospheres, clearly indicating where the gas is. Working in adverse weather conditions, such as fog, rain and mist, multiple point gas detectors provide an accurate map of the event.
However, to be detected, the gas must reach the detector point, which doesn’t happen if the wind takes the gas cloud away from the detector or dissipates it to a lower level. Moreover, it doesn’t detect gas leaks if the sensor is buried or covered. Generally, the PI is seen as the industry-preferred secondary gas detector, after the open path devices.
Open Path Infrared (OPI) - the secondary detection
OPI gas detectors are ideal for applications in the harshest environments, where reliability and performance are of utmost importance. Deployed on the same principle as point infrared, it offers an increased chance of detecting a gas leak and is less sensitive to wind speed and direction. Also, it offers the same risk reduction as point detectors with fewer devices.
OPI offers a better area coverage than PIs and the positioning is not as critical as it is withpoint detectors. It is failsafe and can detect low gas concentrations. It integrates the threat to size and concentration and it covers 5 m to 200 m line.
The detection path can be obscured, but this is detected and reported. However, it takes time for the gas to reach the detector and in still-air conditions, the alarm can be generated with non-hazardous levels.
OPI reduces the disadvantages of point detectors in windy conditions but doesn't eliminate them. It is seen as the industry-preferred, primary gas detection method.
Ultrasonic (acoustic) - the tertiary detection
The acoustic gas leak detector delivers with high speed of response reliable gas leak detection, even in the noisiest environments. It prevents false alarms and reduces the cost of ownership. Easy to deploy, it detects high-pressure gas within typically 20 m range.
The ultrasonic gas detector doesn’t need calibration and can withstand the harshest weather conditions. Gas does not have to “reach” the detector-like point or open path detection and it eliminates the dilution and wind direction effect. Its major advantage is that it does not depend on a gas cloud to accumulate.
Ultrasonic gas leak detection provides notifications on the pressure gas leak only and does not indicate the gas concentration. However, it reacts to any high-pressure gas release that creates a broadband ultrasonic sound within range. Also, background ultrasonic noise reduces the detection range.
The ultrasonic gas detector provides the third level of detection and offers an excellent addition to the gas protection layer in conjunction with point and open path devices.
Three steps for optimal detection
The most favorable coverage, detection, hazard mitigation and life protection can be obtained by combining the three technologies described above. Thus, Point Infrared and Open Path Infrared will detect the gas leak at the detection point, unless air movement will take the gas cloud away or dilute it to a lower level.
At this point, the Ultrasonic Gas Leak Detector comes in charge to “hear” the pressurized leak and send the risk alert.
Honeywell recommends to deploy integrated technologies within the gas protection layer and then a flame detection layer above it as the next protection layer.
Independent, yet interrelated layers of protection will deter, prevent, detect and mitigate potential threats and guarantee business performance and confidence.
Alexandra Serban
September 23, 2019
Let's Connect!
Sign up to receive exclusive communications from Honeywell including product updates, technical information, new offerings, events and news, surveys, special offers, and related topics via telephone, email, and other forms of electronic communication.
Copyright © 2025 Honeywell International Inc
Maximum File Size
Maximum Files Exceeded
Due to inactivity you will be logged out in 000 seconds.
Maximum File Size
Maximum Files Exceeded
You cannot access this page as this product is not available in your country.