-
Global
-
Africa
-
Asia Pacific
-
Europe
-
Latin America
-
Middle East
-
North America
- |
- Partners
- |
-
Currency:Localize your Content
You can set your preferred currency for this account.
Choose a Currency
Currency- CHOOSE YOUR CURRENCY
Update Currency
Changing Currency will cause your current cart to be deleted. Click OK to proceed.
To Keep your current cart, click CLOSE and then save your cart before changing currency.
-
Select Account
Switching accounts will update the product catalog available to you. When switching accounts, your current cart will not move to the new account you select. Your current cart will be available if you log back into this account again.
Account# Account Name City Zip/Post Code CANCELPROCEEDMy Account
-
Support
- View All Productivity Solutions
- Warranties
- Patents
- Global Locations
- Technical Support
- Discontinued Products
- Quality Program and Environmental Compliance
- Return Material Authorization (RMA)
- Legal Documents
- Product Certification
- Software Downloads
- Cyber Security Notifications
- Case Studies and Success Stories
- View All Sensing Solutions
- Sales Contact Form
- Technical Support
- Certificates
- eCOM Portal
- Distributor Inventory
- Return Material Authorization (Test & Measurement)
- Return Material Authorization (Citytech)
- Return Material Authorization (EnviteC)
- Legal Documents
- Intelligent Life Care
- Return Material Authorization (ILC)
-
Global
-
Africa
-
Asia Pacific
-
Europe
-
Latin America
-
Middle East
-
North America
- |
- Partners
- |
You are browsing the product catalog for
You are viewing the overview and resources for
- News & Events
- Featured stories
- Personal Protective Equipment
- Spilling the Tea on Chemical Hazards and Skin Safety
Spilling the Tea on Chemical Hazards and Skin Safety
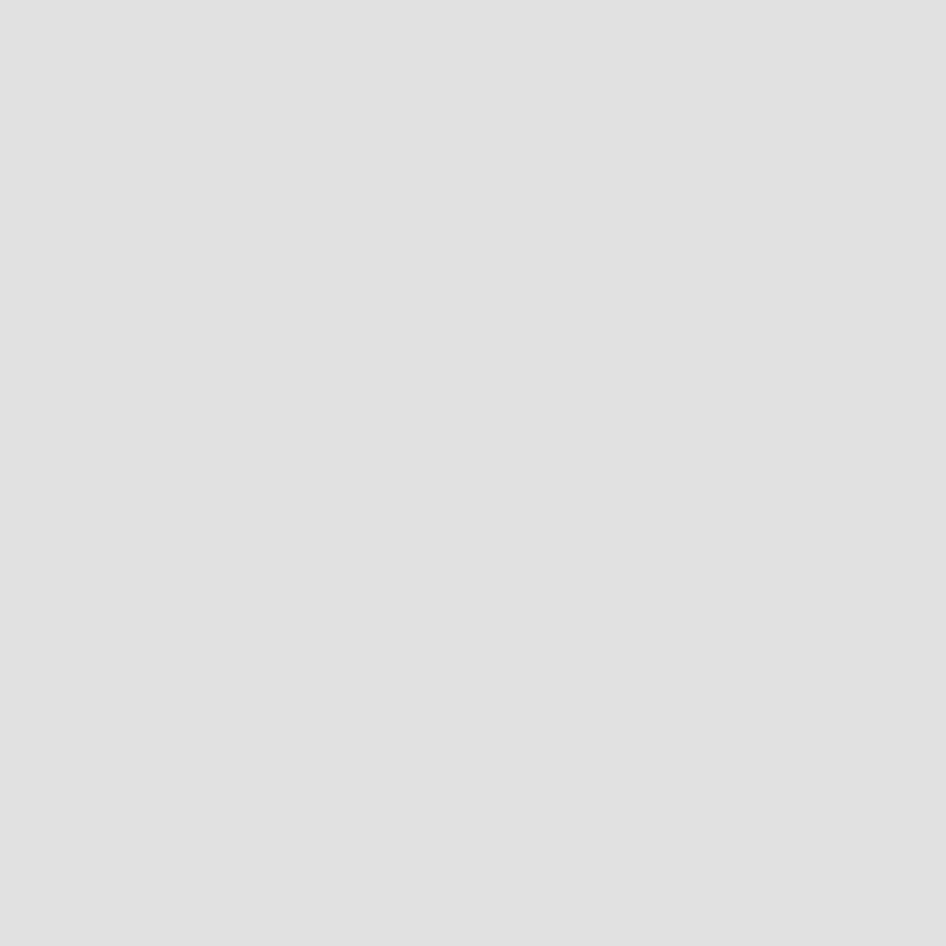
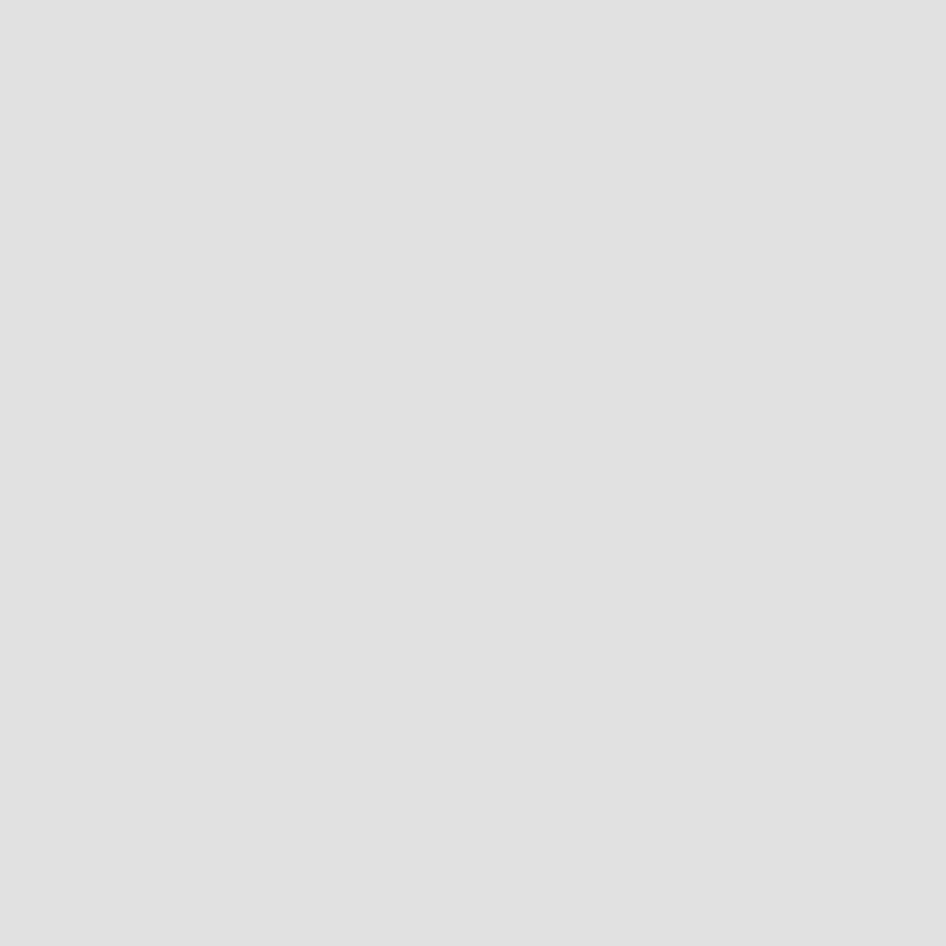
Spilling the Tea on Chemical Hazards and Skin Safety
Alexandra Serban
November 18, 2019
When working in your backyard garden, garage or making dinner, you expose your skin to mechanical, electrical, radiological, environmental or chemical risks. Needless to say, hazards are at their highest in your workplace if you work with sharp objects, heavy machinery or chemicals.
As always, prevention is better than cure. Therefore, no matter the industry you activate in, you should be well-informed and aware of the threats to your skin.
Find out all you need to know about the dangers your skin is exposed to in at work.
Skin is the largest human organ, covering an area of about two square meters. It prevents germs and bacteria from entering the body, defending muscles, bones and internal organs against diseases and infections. It also helps detect hot and cold, regulates body temperature through the sweat glands and alerts the body to potential dangers by detecting pressure, pain, heat and cold.
Work-related skin hazards
Working with sharp objects or pointed tools, products or equipment increases the risk of skin cuts and abrasions. Manipulating heavy machinery can lead to serious bruises, while excessive heat or cold can cause severe burns or chilblains. An unearthed electricity supply, arcing systems or electrostatic discharges can lead to burns and electrocutions.
Working in the sun might seem a pleasant activity, but UV exposure can pose a serious threat to the health of the workers who spend long periods outdoors, in hot, sunny environments.
Chemicals are everywhere
Chemicals are components of an immense variety of products that influence every aspect of our lives, from our home activities to industrial environments.
While soaps, detergents, and perfumes are consumer chemicals, other substances will support the production process of other products or services. Workers are likely to come into contact with chemicals that can cause damage to the skin, every day. Hands are exposed the most, as they are the first that come in touch with skin irritants.
In Europe, 70% of chemicals are used by most industries in their production processes to manufacture other goods, according to essentialchemicalindustry.org
Chemicals are widely used in industries such as chemical and petrochemical, metal and foundry, catering, printing and hairdressing. Agricultural workers, beauticians, cleaners, construction workers, machine operators, aerospace production workers, pharmaceutical or workers in the oil and gas sector and many other professionals regularly expose their hands to skin irritants. They range from lubricating oils, epoxy resins, acids, alkalis, to long-period water exposure, soaps, detergents and antiseptics.
The risk of irritants, and allergens
According to the Institution of Occupational Safety and Health (IOSH) from the UK, damage to the hands is one of the most common occupational injuries, with skin infections and irritations among the most typical conditions suffered by workers.
The National Institute for Occupational Safety and Health (NIOSH) estimates that in the USA, occupational dermatitis costs the country at least 1 billion dollars per year.
Skin can be damaged by two types of substances: irritants and allergens, the main causes of dermatitis. The first reaction of contact with an allergen or irritant substance occurs within a few hours or days of exposure to the substance. Repetitive exposure to chemicals can lead to chronical dermatitis, a disease that significantly reduces the quality of life.
Irritant contact dermatitis is a type of eczema, an inflammation of the skin with symptoms such as skin redness, blisters, scales or crusts. Some of the irritating substances are soaps and detergents, solvents, regular contact with water, antiseptics and antibacterial substances, perfumes and preservatives in toiletries or cosmetics. Machine lubricating or cutting oils, disinfectants, acids and alkalis, cement, powders, dust and soil are also skin irritants.
Allergic contact dermatitis appears when a person is exposed to an allergen he or she is sensitive to. When coming in contact with the allergen, the person’s immune system reacts with symptoms such as itching, blistering, skin redness, swelling and in some cases even urticaria or hives that can grow up to the size of a hand.
Some of the causes of urticaria in the industrial environment are allergic reactions to latex, pressure to the skin or a change in water composition. The most common allergens include cosmetic ingredients such as fragrances, hair dye and nail varnish hardeners, metals such as nickel and cobalt, rubber, including latex, textiles, dyes or resins, especially epoxy resin. Epoxy resin and its components can be irritant to the eyes and skin, causing allergic contact dermatitis, but may also be toxic or even carcinogenic.
Eight steps for hand protection
Can a worker totally avoid contact with harmful substances or objects?
As we have seen so far, irritants and allergens are present in chemicals used in most industries. Therefore, personal protective equipment (PPE), such as hand protection gloves, plays a crucial role in workers’ health.
However, unless carefully selected, the gloves themselves can be a cause of skin irritation, if the worker is allergic to the glove material, if there are broken glass fibres in the mechanical protection gloves or if they are old and have lost their protection ability.
In the US, OSHA recommends these eight steps for glove selection:
1. Identify the type of chemicals handled
2. Identify the nature of the contact (total immersion, splash, etc.)
3. Identify the duration of contact with the substance
4. Determine the area requiring protection (hand only, forearm, arm)
5. Establish the grip requirements (dry, wet, oily)
6. Determine if you need thermal protection
7. Ensure that the gloves fit well, are suitable for the task and are of a material which itself does not cause skin irritation
8. Ensure that the gloves meet abrasion and resistance requirements and conform with current standards.
Types of chemical resistant gloves
According to OSHA, chemical resistant gloves are made with different kinds of rubber: natural, butyl, neoprene, nitrile and fluorocarbon (viton), or various kinds of plastic: polyvinyl chloride (PVC), polyvinyl alcohol and polyethylene. These materials can be blended or laminated 25 for better performance. OSHA notes that the thicker the glove material, the greater the chemical resistance. However, thick gloves may impair grip and dexterity, having a negative impact on safety.
Butyl gloves are made of synthetic rubber and protect against a wide variety of chemicals, such as peroxide, rocket fuels, highly corrosive acids (nitric acid, sulfuric acid, hydrofluoric acid, and red-fuming nitric acid), strong bases, alcohols, aldehydes, ketones, esters, and nitro compounds. Butyl gloves also resist oxidation, ozone corrosion, and abrasion, and remain flexible at low temperatures.
Natural (latex) rubber gloves are comfortable to wear, which makes them a popular general-purpose glove. They feature outstanding tensile strength, elasticity and temperature resistance. In addition to resisting abrasions caused by grinding and polishing, latex gloves protect employees’ hands from most water solutions of acids, alkalis, salts, and ketones. Hypoallergenic gloves, glove liners, and powderless gloves are alternatives for employees who are allergic to latex gloves.
Neoprene gloves are made of synthetic rubber and offer good pliability, finger dexterity, high density and tear-resistance. They protect against hydraulic fluids, gasoline, alcohols, organic acids and alkalis. Neoprene gloves generally have chemical and wear resistance properties superior to those made of natural rubber.
Nitrile gloves are made of a copolymer and provide protection from chlorinated solvents such as trichloroethylene and perchloroethylene. Although intended for jobs requiring dexterity and sensitivity, nitrile gloves stand up to heavy use even after prolonged exposure to substances that cause other gloves to deteriorate. Nitrile gloves offer skin protection when working with oils, greases, acids, caustics, and alcohols.
Choosing the most appropriate gloves from a trusted supplier is an obligation. Hand protection gloves must ensure quality, comfort, safety and total adaptability to the workplace. It is vital for employers to seek expert consultation to obtain information such as detailed permeation times for certain chemicals.
Let's Connect!
Sign up to receive exclusive communications from Honeywell including product updates, technical information, new offerings, events and news, surveys, special offers, and related topics via telephone, email, and other forms of electronic communication.
Copyright © 2025 Honeywell International Inc
Maximum File Size
Maximum Files Exceeded
Due to inactivity you will be logged out in 000 seconds.
Maximum File Size
Maximum Files Exceeded
You cannot access this page as this product is not available in your country.