-
Global
-
Africa
-
Asia Pacific
-
Europe
-
Latin America
-
Middle East
-
North America
- |
- Partners
- |
-
Currency:Localize your Content
You can set your preferred currency for this account.
Choose a Currency
Currency- CHOOSE YOUR CURRENCY
Update Currency
Changing Currency will cause your current cart to be deleted. Click OK to proceed.
To Keep your current cart, click CLOSE and then save your cart before changing currency.
-
Select Account
Switching accounts will update the product catalog available to you. When switching accounts, your current cart will not move to the new account you select. Your current cart will be available if you log back into this account again.
Account# Account Name City Zip/Post Code CANCELPROCEEDMy Account
-
Support
- View All Productivity Solutions
- Warranties
- Patents
- Global Locations
- Technical Support
- Discontinued Products
- Quality Program and Environmental Compliance
- Return Material Authorization (RMA)
- Legal Documents
- Product Certification
- Software Downloads
- Cyber Security Notifications
- Case Studies and Success Stories
- View All Sensing Solutions
- Sales Contact Form
- Technical Support
- Certificates
- eCOM Portal
- Distributor Inventory
- Return Material Authorization (Test & Measurement)
- Return Material Authorization (Citytech)
- Return Material Authorization (EnviteC)
- Legal Documents
- Intelligent Life Care
- Return Material Authorization (ILC)
-
Global
-
Africa
-
Asia Pacific
-
Europe
-
Latin America
-
Middle East
-
North America
- |
- Partners
- |
You are browsing the product catalog for
You are viewing the overview and resources for
- News & Events
- Featured stories
- Personal Protective Equipment
- How to Determine the Ergonomic Properties of a Full Body Harness
How to Determine the Ergonomic Properties of a Full Body Harness
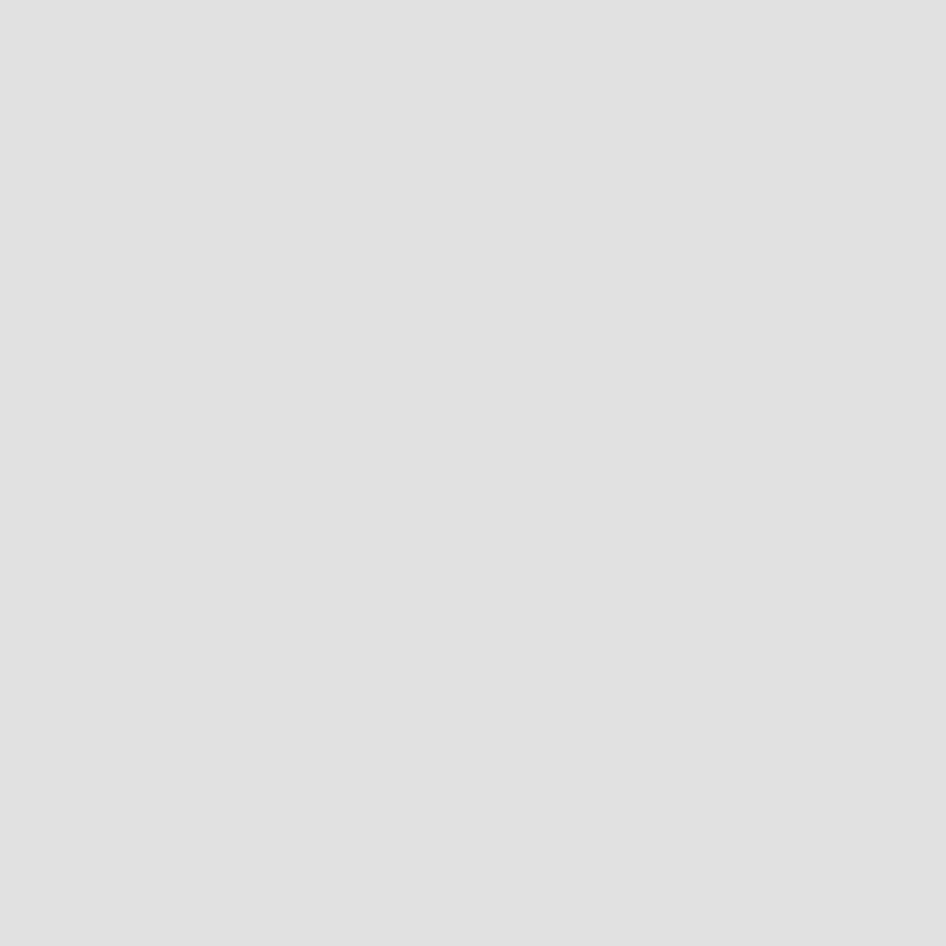
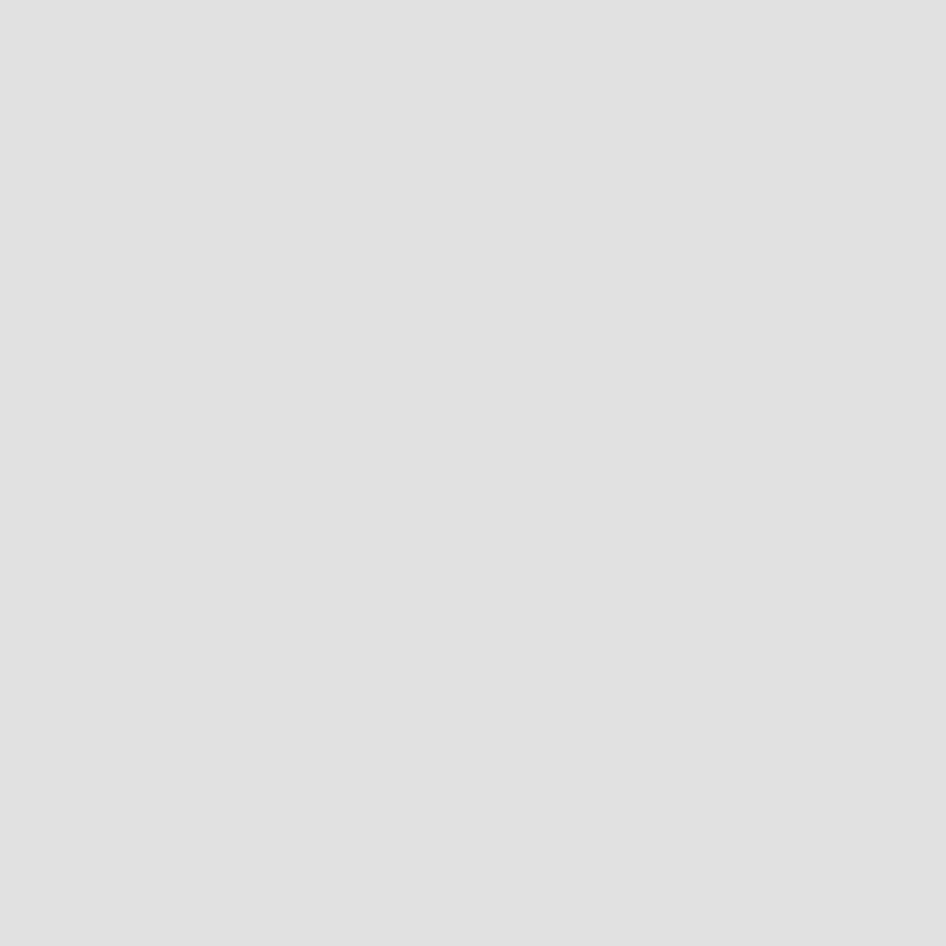
How to Determine the Ergonomic Properties of a Full Body Harness
Ana Ilie
January 18, 2022
Trying to find a truly protective fall protection harness that not only improves the safety of your workers, but also increases their efficiency, is no easy feat. The delicate balance between compliance, safety, and ergonomics makes the difference between a good harness and a great one.
Bringing workers home safely is a great responsibility, and the construction industry is one of the most hazardous in the world with the highest number of annual fatalities. Therefore, increased safety on job sites is always the main concern. However, just as important as safety is improving workers’ long-term well-being by mitigating the risk of muscular fatigue and discomfort, which can lead to musculoskeletal diseases (MSDs). In turn, MSDS translate to lost workdays, plus reduced efficiency and productivity.
When designing a comfortable, lightweight, and breathable harness, applying the science of ergonomics determines the exact pain points and how they can be mitigated.
The textbook definition of ergonomics describes it as “the science of workplace, tools, and equipment designed to reduce worker discomfort, strain, and fatigue and to prevent work-related injuries.”
When applied to fall protection harnesses, designers use it to optimize the comfort and protection properties of fall protection equipment. This leads to important innovations in terms of the materials used, the actual shape of the harness components, and the way pressure is distributed as to make working at height as comfortable as possible.
Imagine a construction worker who day-after-day performs his/her job that requires not only skills and knowledge, but also extraordinary physical strength, endurance, and flexibility. Those long hours spent in a restrictive, non-ergonomic heavy harness can lead to overexertion and muscular fatigue due to restricted freedom of movement, repetitive tasks, sweat, and heat build-up.
That’s why, before designing a new harness, a complete ergonomic assessment must be performed to determine how workers are performing their tasks. This can identify ergonomic risks such as repetitive tasks that can cause strains, improper work area setup, and use of tools, which can all result in the development of work-related musculoskeletal disorders.
A typical ergonomic assessment is based on scientific data such as:
- Anthropometric data - height, weight, waist circumference
- Human anatomy - lumbar support, weight distribution, shoulder stabilization, musculoskeletal benchmarks
- Range of motion study - rotation, extension, lateral bending and flexion, movement focused technology
- Heatmapping Thermal comfort - body heat radiation and evaporative cooling
- Pressure mapping - computerized clinical tool for assessing pressure distribution
Design starts based on this assessment, and as with every new prototype, innovation is born out of strenuously testing the performance of the harness. Key concepts in measuring ergonomic performance are:
- Body surface contact
- Breathability
- Pressure point distribution
- Heat and sweat buildup
How exactly do these determine if the harness is providing the optimum level of ergonomic comfort? Here’s how internal tests are conducted and evaluated on Honeywell’s latest and most advanced fall protection harness, the Honeywell Miller H700:
- Body surface contact (airflow)
This test’s objective is to measure the contact area between the harness and the body. The smaller the contact area, the more airflow comes in and the more comfortable the harness is for long-time wear.
The airflow test is conducted by applying pressure to a pressure measurement film positioned on top of the harness. The film turns pink when pressure is added, simulating how people wearing the harness may feel pressure on the paddings.
What is of interest here is the contact area where the harness touches the body. This is calculated as the ratio between the total area of the padding and the contact area that gets in touch with the body. A lower contact area ratio means the worker will benefit from more airflow, less thermal storage (heating), and an overall cooling effect.
Compared to the next two best alternatives on the market, the H700’s ergonomic design offers the smallest contact area and contact area ratio, which significantly reduces body contact around the neck and lower back, reducing chafing and irritation, and improving airflow.
2. Breathability
This test measures the water vapor resistance (RET) of a harness. A lower water vapor resistance means a lower barrier to water vapor, which means the material is breathable and more comfortable to wear.
RET is a quality specific to textile materials or composites that determines the evaporative heat flux in response to a steady applied water-vapor pressure gradient.
The water vapor resistance test consists of placing a specimen of the textile material flat across the measurement unit, with the side normally facing the human body (skin contact side) in contact with a hotplate, which has a temperature of 35˚ Celsius. The RET is calculated when the temperature of the testing environment is 35˚C, while the relative humidity is 40% and wind speed is 1 meter/second.
An SGS test inspection and certification determined that the Miller H700 has a lower water vapor resistance (RET value 26.4) when compared to the two next best alternatives on the market.
It is the high-tech, multi-layered padding sported by the H700 harness that is keeping workers drier and cooler by combining airflow channel breathability, moisture dispersion technology, and a 3D knitted fabric.
The additional back protection area, which is made up of a warp mesh layer, a 3D knitting spacer with supportive PET monofilament, and a 3D knitting stripe, allows airflow to travel through the padding, making workers feel cooler.
3. Pressure Distribution
This test measures the pressure distribution around the waist of the worker wearing the harness in various working positions. The more even the distribution, and the more the material extends, the more comfortable it feels for the wearer.
The pressure distribution test is conducted by having a test subject wear the harness in various working positions and measuring how the pressure is distributed across the waist pad when the subject is leaning his entire body against the equipment. An even distribution of the pressure means that the harness is comfortable and will not strain unevenly on one side of the body or stop blood circulation.
The compression test is conducted by placing a 50 mm-thick padding filler between two compression plates. The plates compress the material with a force of 1000N, 2000N, and 3000N. What is measured is the deformation of the material under different compressive forces. The underlying principle is that when the compression is the same, the more the material extends, the softer it is.
An SGS test established that the H700 3D warp knitting spacer filler offers a bigger deformation range, which implies that the filler is softer and more comfortable.
Honeywell’s internal comparative tests have shown that the Miller H700 generated a more even pressure distribution than two of its competitors and a bigger deformation (extension), which translates into more comfort.
These tests prove that ergonomic safety is key to improving safety and comfort for workers. Innovative materials and advanced design principles enable worker compliance, safety, and comfort.
Find out more about Honeywell’s H700 Series and take your safety program to the next level of ergonomics.
© 2021 Honeywell International Inc. All rights reserved.
Trademarks used herein are the property of their respective owners.
Let's Connect!
Sign up to receive exclusive communications from Honeywell including product updates, technical information, new offerings, events and news, surveys, special offers, and related topics via telephone, email, and other forms of electronic communication.
Copyright © 2025 Honeywell International Inc
Maximum File Size
Maximum Files Exceeded
Due to inactivity you will be logged out in 000 seconds.
Maximum File Size
Maximum Files Exceeded
You cannot access this page as this product is not available in your country.