-
Global
-
Africa
-
Asia Pacific
-
Europe
-
Latin America
-
Middle East
-
North America
- |
- Partners
- |
-
Currency:Localize your Content
You can set your preferred currency for this account.
Choose a Currency
Currency- CHOOSE YOUR CURRENCY
Update Currency
Changing Currency will cause your current cart to be deleted. Click OK to proceed.
To Keep your current cart, click CLOSE and then save your cart before changing currency.
-
Select Account
Switching accounts will update the product catalog available to you. When switching accounts, your current cart will not move to the new account you select. Your current cart will be available if you log back into this account again.
Account# Account Name City Zip/Post Code CANCELPROCEEDMy Account
-
Support
- View All Productivity Solutions
- Warranties
- Patents
- Global Locations
- Technical Support
- Discontinued Products
- Quality Program and Environmental Compliance
- Return Material Authorization (RMA)
- Legal Documents
- Product Certification
- Software Downloads
- Cyber Security Notifications
- Case Studies and Success Stories
- View All Sensing Solutions
- Sales Contact Form
- Technical Support
- Certificates
- eCOM Portal
- Distributor Inventory
- Return Material Authorization (Test & Measurement)
- Return Material Authorization (Citytech)
- Return Material Authorization (EnviteC)
- Legal Documents
- Intelligent Life Care
- Return Material Authorization (ILC)
-
Global
-
Africa
-
Asia Pacific
-
Europe
-
Latin America
-
Middle East
-
North America
- |
- Partners
- |
You are browsing the product catalog for
You are viewing the overview and resources for
- News & Events
- Featured stories
- Personal Protective Equipment
- Five Hand Hazards And Safety Gloves for Automotive Workers
Five Hand Hazards And Safety Gloves for Automotive Workers
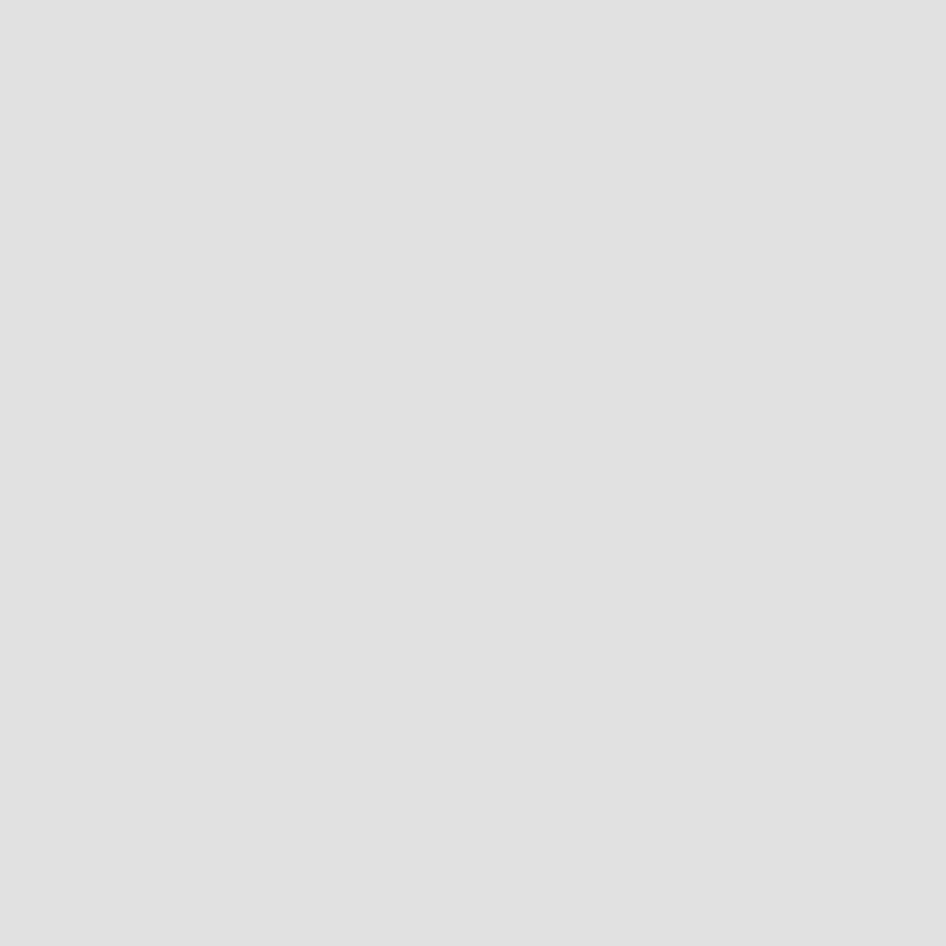
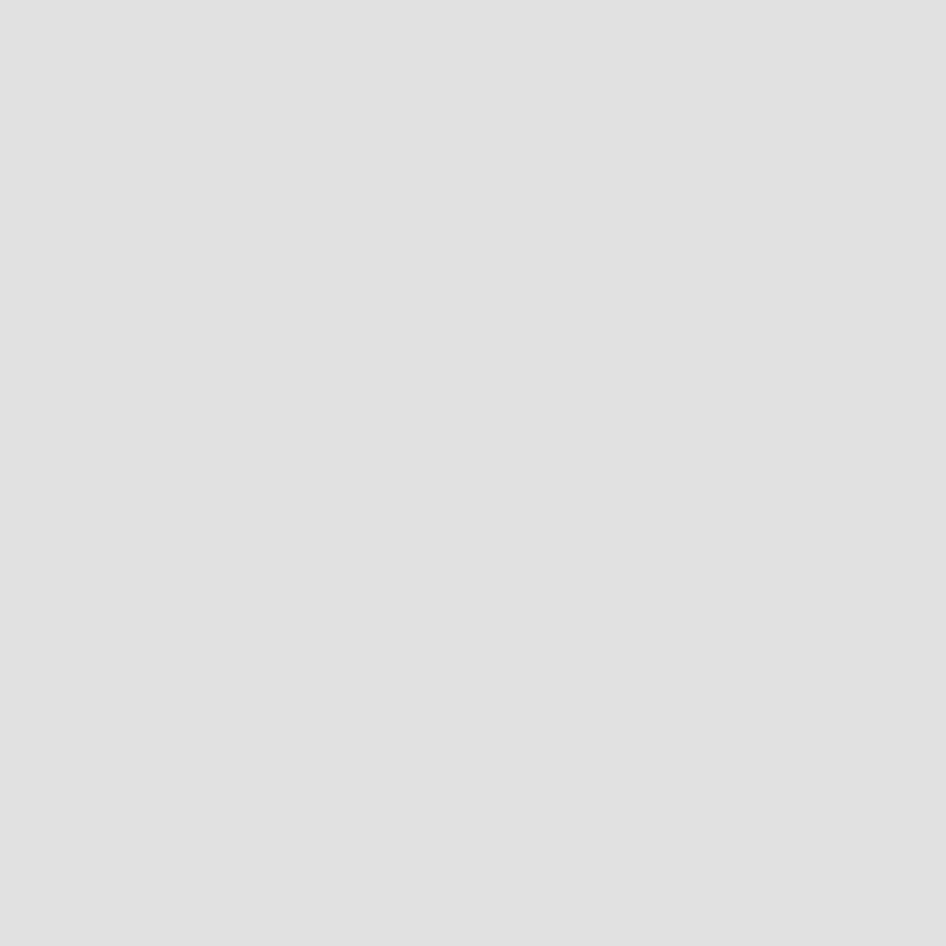
Five Hand Hazards And Safety Gloves for Automotive Workers
Automotive plant workers risk hand cuts day in, day out as vehicles include metal and plastic components with sharp edges. Not only do these parts must be manually handled, but they also must be stamped, pressed, machined, molded and assembled, as required.
Engine assembly, for example, encompasses tasks such as the fitting of pipes, valves, and camshafts, which can put a worker’s hands at risk.
Within a typical automotive plant, risks often vary from one department to another, so there is no one-size-fits-all cut protection. Below are five hazardous situations examples and the hand glove solutions that should be applied each time.
1. Stamping shop work hazards
Feeding the stamping presses with what are often large sheets and panels presents an inherent risk of hand cuts. The handling of stamped parts coming off the other end of the press line is equally hazardous as components have yet to be deburred or finished, meaning they are likely to feature sharp and/or rough edges.
The gloves
Gloves that provide resistance to cuts, abrasion, and puncture. In addition, many of the sheets will be coated in a protective/ lubricating oil, so grip performance in both dry and oily environments is essential. Dexterity is clearly another requirement.
2. Machine shop activity hazards
The machine shop is often considered the heartbeat of an automotive plant and is where a myriad of the engine and structural parts are produced. Here, billets, bars, and tubes of material require handling. Prior to machining, much of this raw material will have been cut to size on an automatic bandsaw or circular saw and feature sharp/rough sawn edges and burrs.
The gloves
Besides resistance to cuts, abrasion and puncture, chemical resistance is also essential as a high proportion of machining operations require the use of coolants or cutting fluids. Grip performance is another important requirement in both wet and dry environments, along with dexterity and tactility. Touchscreen compatibility, for example, is likely a requirement as operators often need to tap commands into a control panel.
3. Assembly line hazards
Common operations on the main assembly lines include chassis assembly, parts picking, and adjusting and fastening components into position. Workers need a high degree of dexterity, but also protection against cuts and abrasion. Simply taking the gloves off isn’t an option.
The gloves
Gloves will need to offer cut and abrasion resistance along with dexterity and tactility. A further factor is protection for the components, which will have been machined or fabricated and carry a high level of added value that would be costly to scrap if any damage occurred due to poor or incorrect handling.
4. Glass fitting work hazards
Among specialist assembly line tasks is the fitting of front and rear windscreens, and door windows. When it comes to gloves, dexterity is paramount, but this should not be at the compromise of cut protection. Glass, even with edges that are made safe through sanding, grinding or polishing, still has the potential to cut without adequate care.
The gloves
If operatives are expected to handle glass, gloves must provide cut, abrasion and puncture resistance. In addition, as the fitting of glass in the automotive industry often requires the application of adhesive, suitable chemical resistance must be provided.
5. Logistics work hazards
In a typical automotive plant, complex logistics operations prevail to ensure the timely delivery of materials and parts through the various processes of manufacturing. This involves handling objects, sometimes with sharp edges, in various environmental conditions.
The gloves
Gloves must offer both cut and abrasion resistance, along with high levels of dry and oily grip performance. One comfort factor to consider here is the need for protection against cold or hot weather, as logistics operators are often required to work outside. Touchscreen compatibility may also be necessary if workers use mobile devices.
When it comes to gloves for automotive plant workers, selecting the right level of cut protection is paramount. Nest-generation gloves carry clear markings of the cut protection levels provided in accordance with the latest standards and regulations.
Alexandra Serban
September 29, 2020
Let's Connect!
Sign up to receive exclusive communications from Honeywell including product updates, technical information, new offerings, events and news, surveys, special offers, and related topics via telephone, email, and other forms of electronic communication.
Copyright © 2025 Honeywell International Inc
Maximum File Size
Maximum Files Exceeded
Due to inactivity you will be logged out in 000 seconds.
Maximum File Size
Maximum Files Exceeded
You cannot access this page as this product is not available in your country.