-
Global
-
Africa
-
Asia Pacific
-
Europe
-
Latin America
-
Middle East
-
North America
- |
- Partners
- |
-
Currency:Localize your Content
You can set your preferred currency for this account.
Choose a Currency
Currency- CHOOSE YOUR CURRENCY
Update Currency
Changing Currency will cause your current cart to be deleted. Click OK to proceed.
To Keep your current cart, click CLOSE and then save your cart before changing currency.
-
Select Account
Switching accounts will update the product catalog available to you. When switching accounts, your current cart will not move to the new account you select. Your current cart will be available if you log back into this account again.
Account# Account Name City Zip/Post Code CANCELPROCEEDMy Account
-
Support
- View All Productivity Solutions
- Warranties
- Patents
- Global Locations
- Technical Support
- Discontinued Products
- Quality Program and Environmental Compliance
- Return Material Authorization (RMA)
- Legal Documents
- Product Certification
- Software Downloads
- Cyber Security Notifications
- Case Studies and Success Stories
- View All Sensing Solutions
- Sales Contact Form
- Technical Support
- Certificates
- eCOM Portal
- Distributor Inventory
- Return Material Authorization (Test & Measurement)
- Return Material Authorization (Citytech)
- Return Material Authorization (EnviteC)
- Legal Documents
- Intelligent Life Care
- Return Material Authorization (ILC)
-
Global
-
Africa
-
Asia Pacific
-
Europe
-
Latin America
-
Middle East
-
North America
- |
- Partners
- |
You are browsing the product catalog for
You are viewing the overview and resources for
- Software
- Warehouse Automation
- Momentum WES
Momentum WES
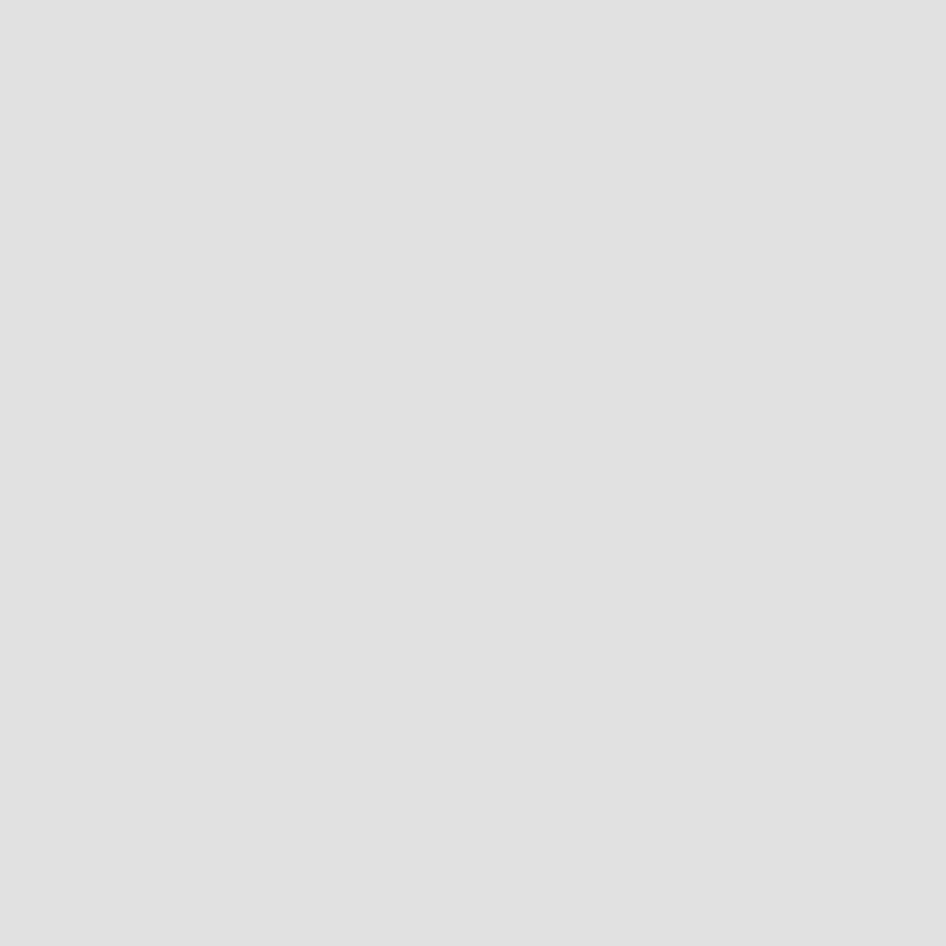
Momentum Warehouse Execution System
Empower your distribution center with the Momentum Warehouse Execution System (WES), a next-generation Cloud-native warehouse software platform designed to orchestrate disparate automation systems.
Built on a trusted foundation, our latest cloud-based Momentum WES release harnesses the power of the cloud to deliver superior performance, effortless updates, and future-ready integration—ensuring your warehouse operations stay ahead of the curve.
Discover the Advantages of a Cloud-Native, Software-driven Approach to Warehouse Automation
- Seamless Automation Integration – Easily connect our warehouse automation software with robotics, conveyors, AS/RS, and material handling equipment for an optimized fulfillment flow.
- Enhanced Agility – Easily deploy updates, expand capacity, and integrate new tools with minimal disruption, reducing downtime and cyber risks.
- Real-Time Visibility & Decision-Making – Cloud-powered data intelligence enables smarter, faster operational decisions based on live warehouse performance.
- Alleviate human resource constraints – Momentum WES helps with labor optimization by dynamically allocating resources based on real-time data.
- Improved support with comprehensive plans that help drive high levels of uptime.
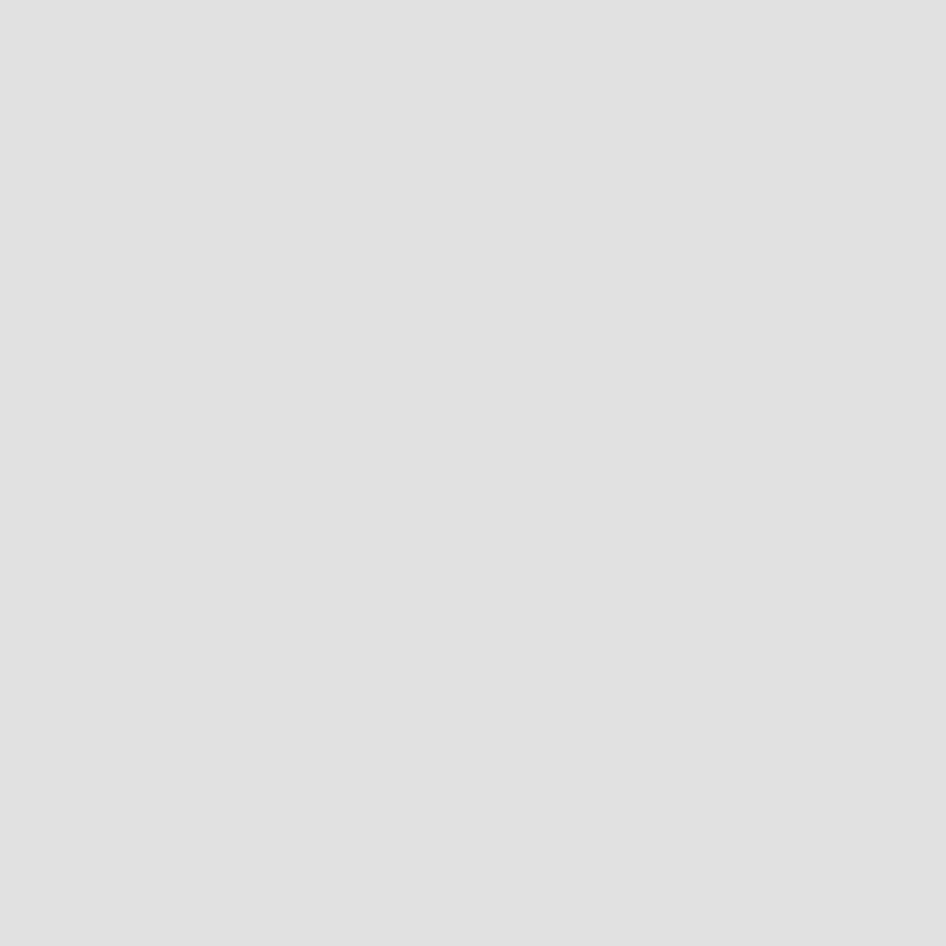
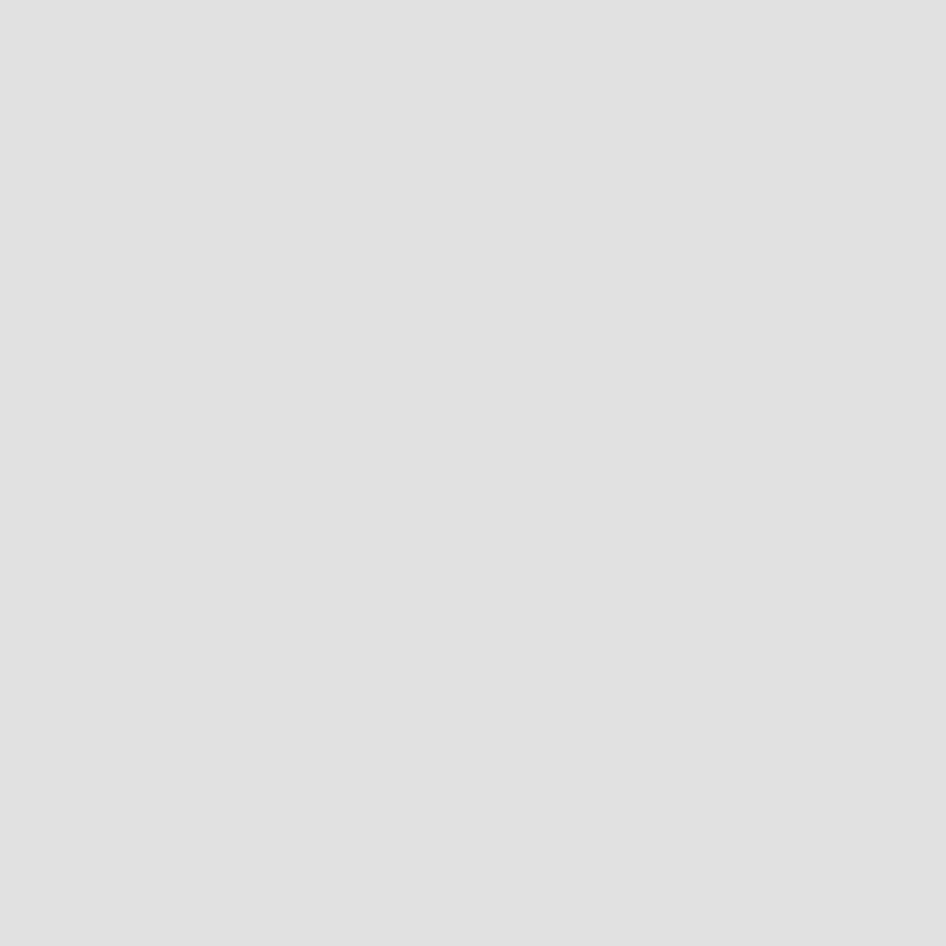
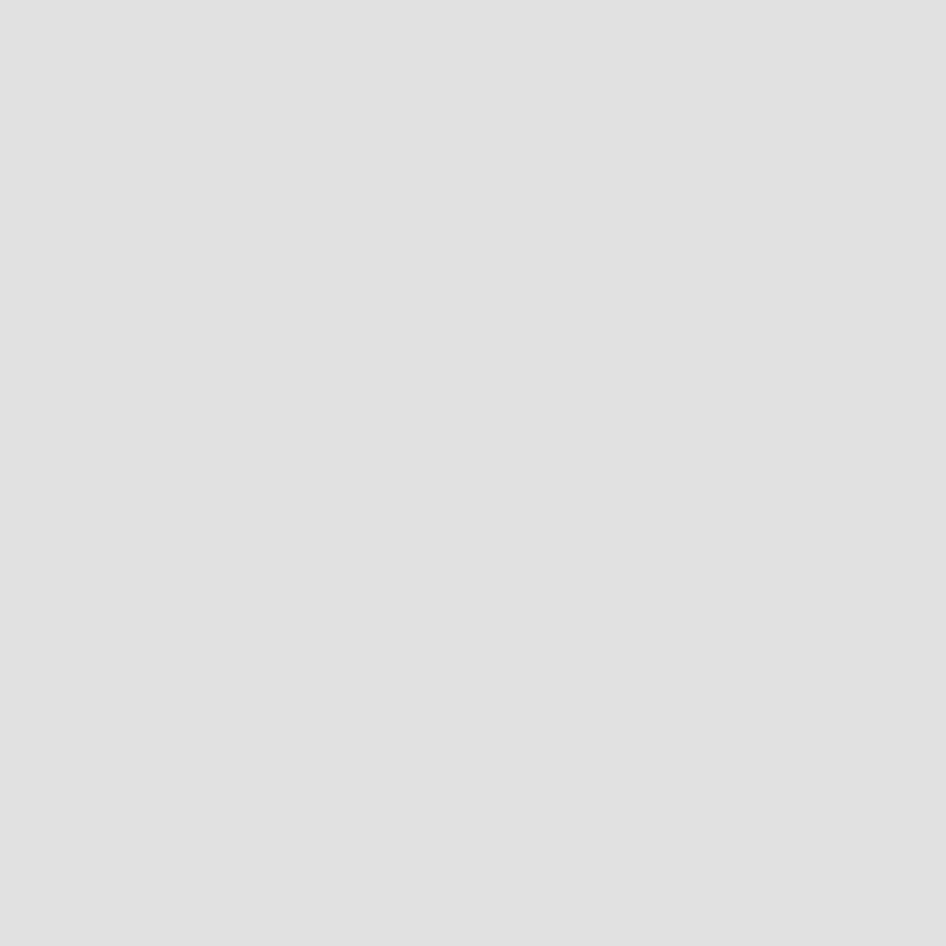
Upgrade from an on-premises WES to Momentum WES and transform your warehouse operations:
- Eliminate Costly IT Infrastructure – Say goodbye to expensive on-prem servers and maintenance costs by shifting to a SaaS for warehouse management model (OpEx). Momentum WES reduces upfront investment (CapEx) and lowers total cost of ownership.
- Expand Without Constraints – Scale operations without the hardware limitations of physical infrastructure. Whether adding automation or opening new facilities, Momentum WES adapts to your needs.
- Keep Pace with Innovation – Unlike static on-prem warehouse management software, Momentum WES allows you to continuously integrate new capabilities without disruptive system overhauls.
- Strengthen Cybersecurity & Compliance – Our WES software cloud infrastructure provides continuous protection, ensuring compliance with evolving security standards.
Discover how Momentum WES transforms warehouse operations.
Request a demo today!
Let's Connect!
Sign up to receive exclusive communications from Honeywell including product updates, technical information, new offerings, events and news, surveys, special offers, and related topics via telephone, email, and other forms of electronic communication.
Copyright © 2025 Honeywell International Inc
Maximum File Size
Maximum Files Exceeded
Due to inactivity you will be logged out in 000 seconds.
Maximum File Size
Maximum Files Exceeded
You cannot access this page as this product is not available in your country.