-
Global
-
Africa
-
Asia Pacific
-
Europe
-
Latin America
-
Middle East
-
North America
- |
- Partners
- |
-
Currency:Localize your Content
You can set your preferred currency for this account.
Choose a Currency
Currency- CHOOSE YOUR CURRENCY
Update Currency
Changing Currency will cause your current cart to be deleted. Click OK to proceed.
To Keep your current cart, click CLOSE and then save your cart before changing currency.
-
Select Account
Switching accounts will update the product catalog available to you. When switching accounts, your current cart will not move to the new account you select. Your current cart will be available if you log back into this account again.
Account# Account Name City Zip/Post Code CANCELPROCEEDMy Account
-
Support
- View All Productivity Solutions
- Warranties
- Patents
- Global Locations
- Technical Support
- Discontinued Products
- Quality Program and Environmental Compliance
- Return Material Authorization (RMA)
- Legal Documents
- Product Certification
- Software Downloads
- Cyber Security Notifications
- Case Studies and Success Stories
- View All Sensing Solutions
- Sales Contact Form
- Technical Support
- Certificates
- eCOM Portal
- Distributor Inventory
- Return Material Authorization (Test & Measurement)
- Return Material Authorization (Citytech)
- Return Material Authorization (EnviteC)
- Legal Documents
- Intelligent Life Care
- Return Material Authorization (ILC)
-
Global
-
Africa
-
Asia Pacific
-
Europe
-
Latin America
-
Middle East
-
North America
- |
- Partners
- |
You are browsing the product catalog for
You are viewing the overview and resources for
- News & Events
- Featured stories
- How A DC Walkthrough Can Improve the Inventory Control Workflow
How A DC Walkthrough Can Improve the Inventory Control Workflow
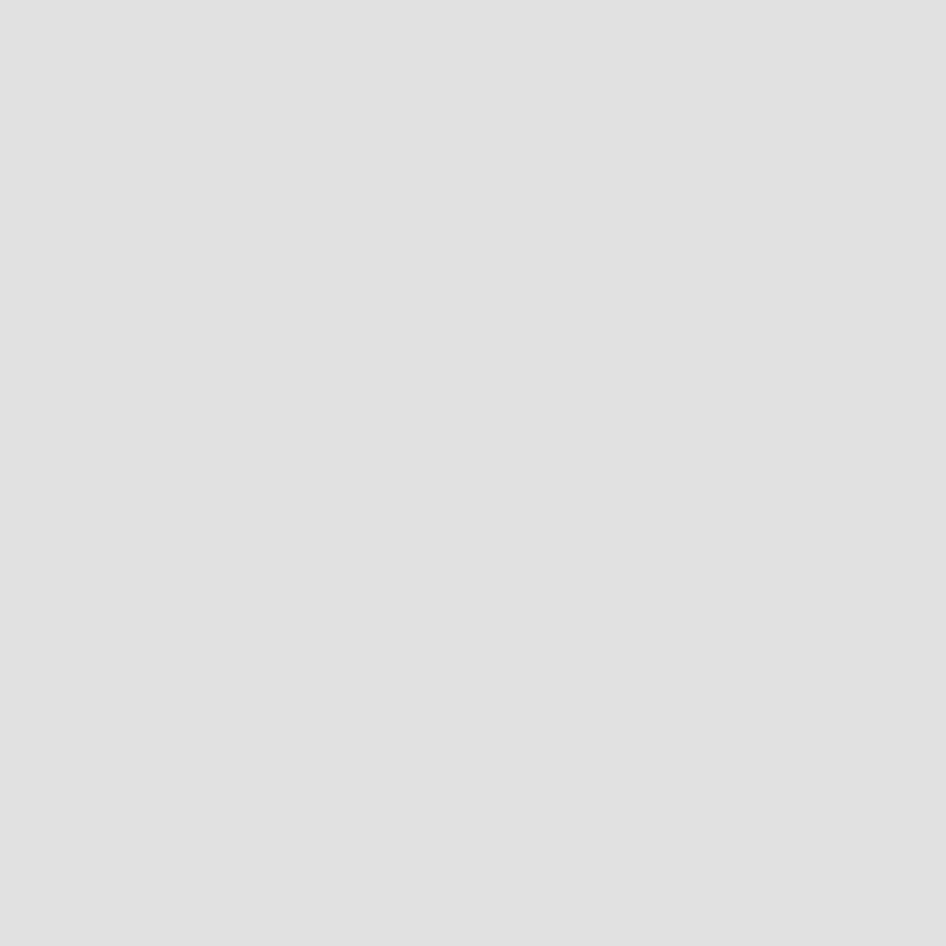
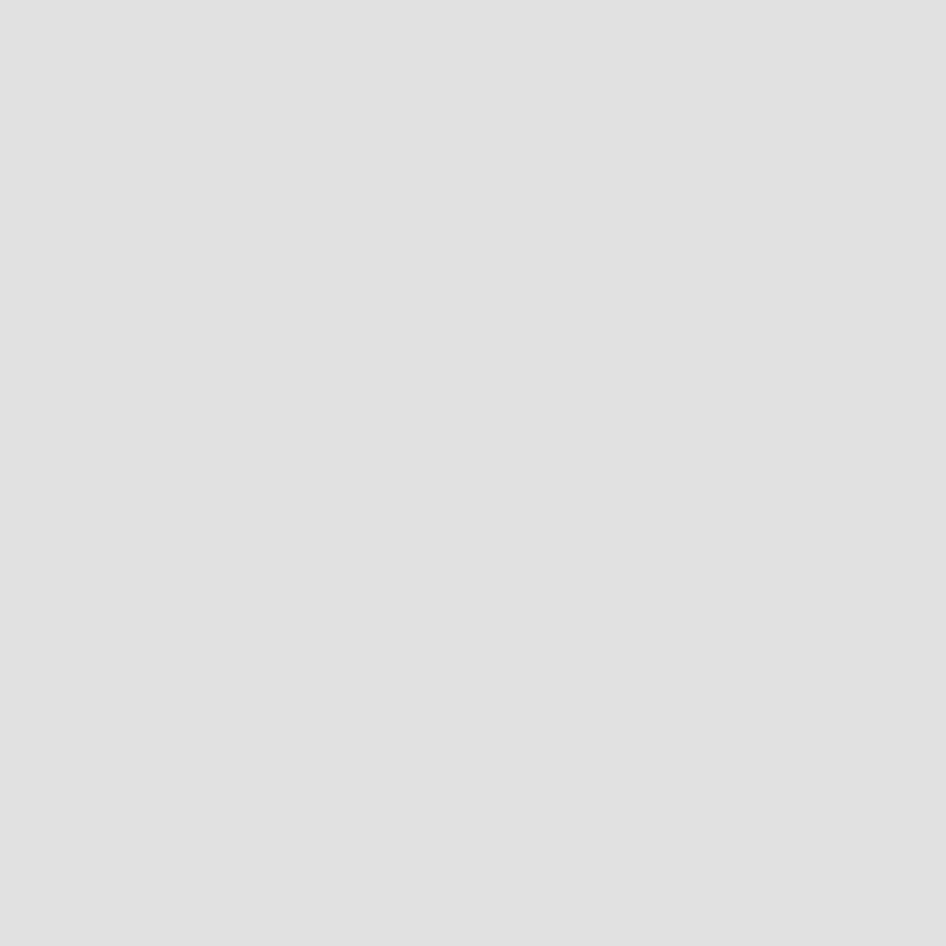
How A DC Walkthrough Can Improve the Inventory Control Workflow
Barry J. Ewell
September 10, 2020
A DC Walkthrough is an engaging assessment that includes discussions, observations, and interviews among workers, supervisors, and management personnel with the objective to document current business and operational processes and look at ways technology and process changes can be applied to make improvements. The DC Walkthrough can be an informal or formal review/audit conducted by the company or external third parties.
At Honeywell we have the opportunity to conduct DC Walkthroughs throughout the world for every conceivable type and size of DC. The goal of our assessment is to validate logistical/operational processes relative to industry best practices focused on time savings, increased worker productivity, and improved accuracy. We focus on the identification of opportunities to both improve stand-alone general processes, as well as improve processes with new technology.
When we review the Inventory Control workflow, we ask questions like:
- Is cycle counting performed in the DC?
- When are cycle counts performed?
- Are cycle counts interleaved with other work processes?
- What tools are used for cycle counts? (paper, RF, voice)
- How are the products/locations determined for cycle counting? (scheduled, random, ABC classification)
- Can cycle counts be requested for specific items/locations? If so, how is this communicated?
- What steps are taken if a discrepancy is discovered?
- What changes are desired in the cycle-count process?
- How often is a physical inventory taken?
- What is the physical process?
- Is it a blind count?
Inventory Control Walkthrough Observations and Recommendations Example
Conducting a DC Walkthrough is done with “fresh eyes.” Fresh eyes is defined as looking at the workflow with the intent of learning and understanding the current state of operations without bias or preconceived conclusions, and then applying industry knowledge and best practices to recommend ways to improve upon the current performance.
The following is an example of a DC Walkthrough Honeywell did for a medium-sized DC in North America for the Inventory Control workflow, which includes observations with associated recommendations.
DC Walkthrough Observations
- Doing physical inventories
- Cost is about $750K annually
- Location utilization is high
- Cube utilization is not as efficient
- 85% of inventory is similar across 3 NA DCs
- Issues with master carton being labeled correctly but material inside carton wrong
- So, is Master carton really labeled correctly, then?
- Overstock area has dog items
- Some have not moved in years
- Carrying cost has now exceeded any revenue gained
DC Walkthrough Best Practices Recommendations
Inventory control practices in a DC are vital to the accuracy of the overall inventory. This accuracy is monitored closely by both internal and external auditors as the accuracy is paramount to properly valuating the inventory contained in your supply chain network.
We recommend using a RF cycle-count process as it should be supported by the WMS. Use any WMS functionality that supports interleaving the process with fork moves or picking where possible. By interleaving the processes, you can count exceptions as they occur and count slots that drop below a certain level once retrieval from a location is made (i.e., less than 3 or 5). By only counting those slots with little inventory you are not negatively impacting the operator’s productivity and you are making the process more proactive vs. reactive. The WMS should also support live cycle counting without the need to shut down an aisle while counting.
If using voice for picking, Honeywell Voice provides an interleaved picking and cycle-count process that provides greater productivity and accuracy in this workflow.
We also recommend utilizing any ABCD functionality in the WMS, which focuses on your fastest movers being counted more often and by default maintains a more accurate overall inventory. Most WMS systems also support Value-Based cycle counting of higher-priced items.
We recommend working with the auditors to prove the cycle-count process accuracies and eliminate the physical inventories. Not only are they costly to perform and costly to the business (the need to halt operations results in being behind in fulfillment), but they can introduce inaccuracy with poor counts.
We noticed that location utilization is high but cube utilization is not ideal in some areas. We know there is a current effort to address this with TI x HI audits and adding additional levels of racking to some areas to create smaller height locations for those items. This a great initiative and should be carried forward aggressively.
Some items in the DC have not moved in years and should be eliminated as judiciously as possible. Industry averages show that carrying costs for inventory can be as high as 3%, so if this product has not moved in years the cost of carrying it this long has already eroded the revenue it would create now.
Recommended hardware and software for these processes includes:
All recommendations are Android™ capable.
Technology Improvements in the Inventory Control Workflow
According to the 2018 WERC study1, technology within the supply chain is becoming increasingly important. Many companies are beginning to focus on digital transformation by focusing more on mobile technologies, cloud-based services, and big data practices.
The study also points out that a majority of distribution centers use no other technology beyond a warehouse management system (WMS) and mobile devices with RF/barcode scanners. In terms of adoption plans, over 90% of warehouse managers expect to be using mobile technologies within five years (which is just over 50% today). Eighty-six percent expect to be using big data and real-time analytics within five years, which is a 60% increase over the percentage of people using the technology today.
Honeywell brings a wide set of solutions together that can influence positive outcomes in the Inventory Control workflow throughout the DC. They include the following:
- Mobile Computers with 1D and 2D Imaging. Utilizing mobile computers with imagers to scan product and label information as well as capture additional data is more productive (~25%) and accurate (~50%) than paper/manual-based methods. It helps ensure quality control, vendor compliance, and quantity-received information is captured in real-time.
- Wearable Solutions. A growing number of companies have turned to hands-free computing solutions to streamline operations and improve productivity. The Honeywell 8680i wearable mini mobile provides a hands-free solution that offers increases in productivity and improved ergonomics over handheld devices.
- Fixed and Mobile Printing and Media. From light-duty to ultra-rugged models – stationary and portable – to printer software, media, service, and parts, Honeywell offers an extensive range of solutions for any environment or print application.
- Industrial Label Printers. For commercial light-volume jobs to rugged, round-the-clock printing, built-in “smarts” means greater efficiency and lower cost: error-proof labeling, easy programmability, advanced networking connectivity and security, RFID, and liner-less technology.
- Desktop Label Printers. The clear choice for a wide variety of light-duty label, ticket, and tag printing applications: quiet and compact, highly intuitive and flexible, and a range of configurations designed to match your needs.
- Mobile Label Printers. From retail floor labels to field service receipts – designed to withstand punishing conditions where dirt, moisture, temperature extremes, and drops are common: fast, rugged, and ready to move, and allow a full day of printing without recharging.
- Printer Media Supplies. For a broad range of barcode printing applications, even in some of the toughest environments. Includes barcode labels and tags, receipt paper and wristbands, and thermal ribbons and RFID labels.
- Voice-Guided and Hands-Free Solutions. Honeywell’s voice-guided solutions have proven to help increase productivity by up to 35% and help increase accuracy to 99.99%+ in a variety of tasks throughout the warehouse. With Voice, workers follow a series of instructions for specific pick locations, products, and quantities, and needed guidance and verification is provided at every step. Voice is available in over 35 languages and has been proven to dramatically reduce training and onboarding time, especially in peak seasons with highly transient workforces.
- RFID. Ideal for applications such as inventory cycle counts, omnichannel order fulfillment, receiving new product, and pick lists – lightweight yet rugged for tough DC environments.
- Material Handling Solutions from Honeywell Intelligrated. We see many medium-size DCs exploring and adding varying degrees of material handling solutions to augment and/or replace manual portions of their DC operations with elements of the Honeywell Intelligrated offering such as:
- Labor Management Software (LMS). Honeywell Intelligrated’s Labor Management software allows you to effectively manage your labor and staffing needs, helping you to maximize labor productivity and minimize labor costs. Actionable insights allow you to accurately evaluate worker performance. Patented algorithms help forecast when workers may be at risk for leaving, giving you the ability to take proactive measures. Our LMS provides an effective way to manage labor productivity while improving training, process compliance, and efficiency.
- Warehouse Execution Systems. Honeywell Intelligrated’s Momentum software helps improve efficiencies, automate manual processes, and fully help optimize fulfillment operations. This unified platform reduces unsupportable, one-off customizations and allows you to select only the functions you need to meet your unique operational requirements.
Achieve Better Outcomes with Honeywell
At Honeywell, we have extensive experience in successfully solving complex problems for a variety of ecommerce and omnichannel businesses. We’re committed to solving your DC accuracy challenges through relentless innovation and a desire to deliver best-fit solutions. We provide access to the actionable insights and information you need to transform your business.
Our expert assessment teams will partner with you to understand your unique business requirements and identify where opportunities exist to optimize your workflows and increase efficiencies within today’s competitive business climate.
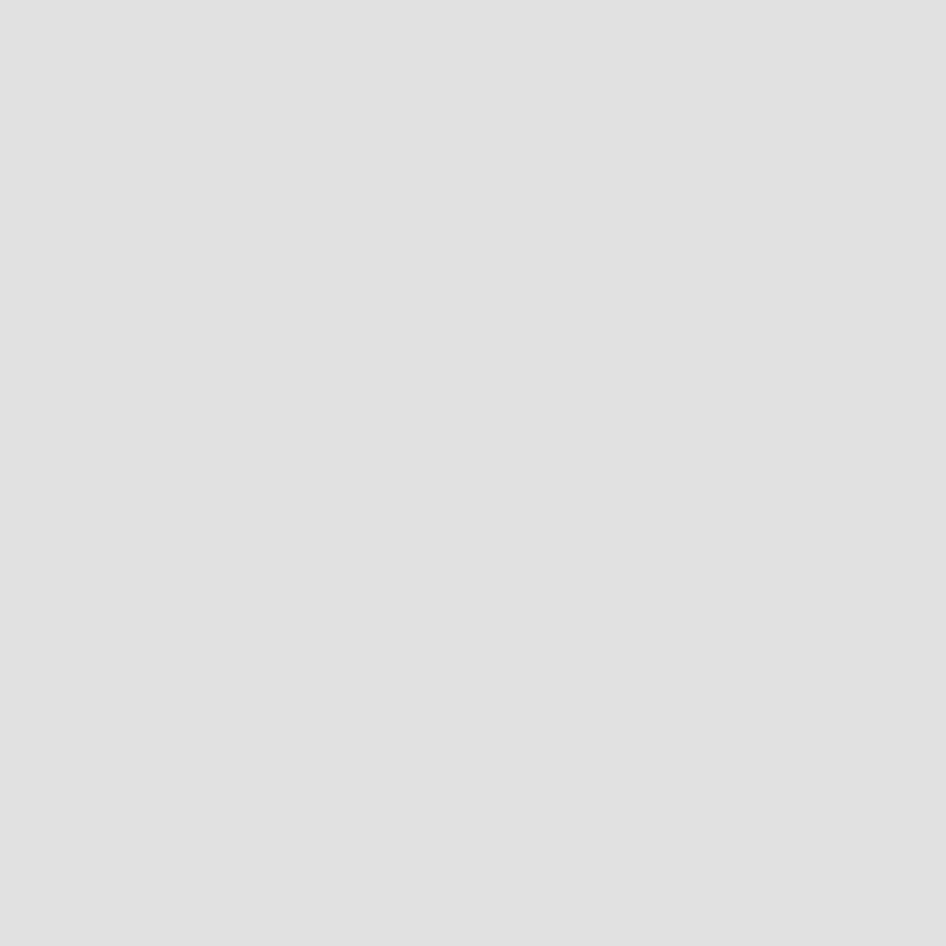
Barry J. Ewell is a Senior Content Marketing Communications Specialist for Honeywell Industrial Automation. He has been researching and writing on supply chain topics since 1991.
Let's Connect!
Sign up to receive exclusive communications from Honeywell including product updates, technical information, new offerings, events and news, surveys, special offers, and related topics via telephone, email, and other forms of electronic communication.
Copyright © 2025 Honeywell International Inc
Maximum File Size
Maximum Files Exceeded
Due to inactivity you will be logged out in 000 seconds.
Maximum File Size
Maximum Files Exceeded
You cannot access this page as this product is not available in your country.