-
Global
-
Africa
-
Asia Pacific
-
Europe
-
Latin America
-
Middle East
-
North America
- |
- Partners
- |
-
Currency:Localize your Content
You can set your preferred currency for this account.
Choose a Currency
Currency- CHOOSE YOUR CURRENCY
Update Currency
Changing Currency will cause your current cart to be deleted. Click OK to proceed.
To Keep your current cart, click CLOSE and then save your cart before changing currency.
-
Select Account
Switching accounts will update the product catalog available to you. When switching accounts, your current cart will not move to the new account you select. Your current cart will be available if you log back into this account again.
Account# Account Name City Zip/Post Code CANCELPROCEEDMy Account
-
Support
- View All Productivity Solutions
- Warranties
- Patents
- Global Locations
- Technical Support
- Discontinued Products
- Quality Program and Environmental Compliance
- Return Material Authorization (RMA)
- Legal Documents
- Product Certification
- Software Downloads
- Cyber Security Notifications
- Case Studies and Success Stories
- View All Sensing Solutions
- Sales Contact Form
- Technical Support
- Certificates
- eCOM Portal
- Distributor Inventory
- Return Material Authorization (Test & Measurement)
- Return Material Authorization (Citytech)
- Return Material Authorization (EnviteC)
- Legal Documents
- Intelligent Life Care
- Return Material Authorization (ILC)
-
Global
-
Africa
-
Asia Pacific
-
Europe
-
Latin America
-
Middle East
-
North America
- |
- Partners
- |
You are browsing the product catalog for
You are viewing the overview and resources for
- News & Events
- Featured stories
- Personal Protective Equipment
- How to Reduce Exposure to Respirable Crystalline Silica
How to Reduce Exposure to Respirable Crystalline Silica
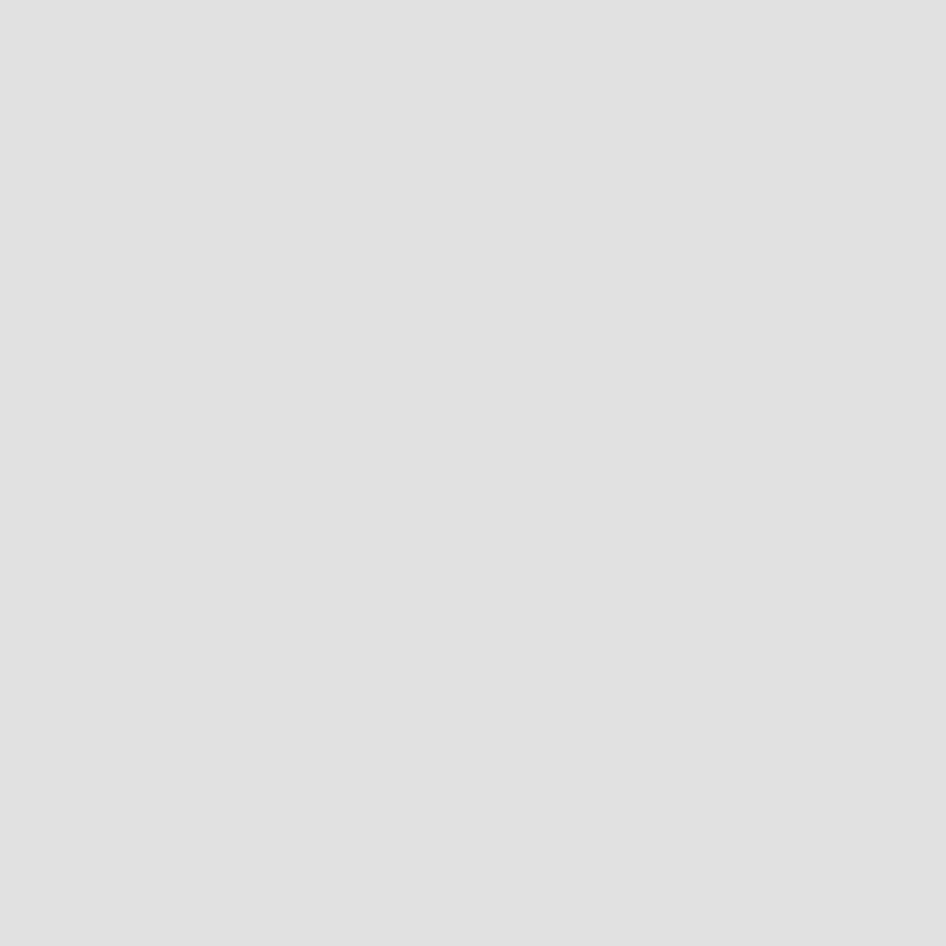
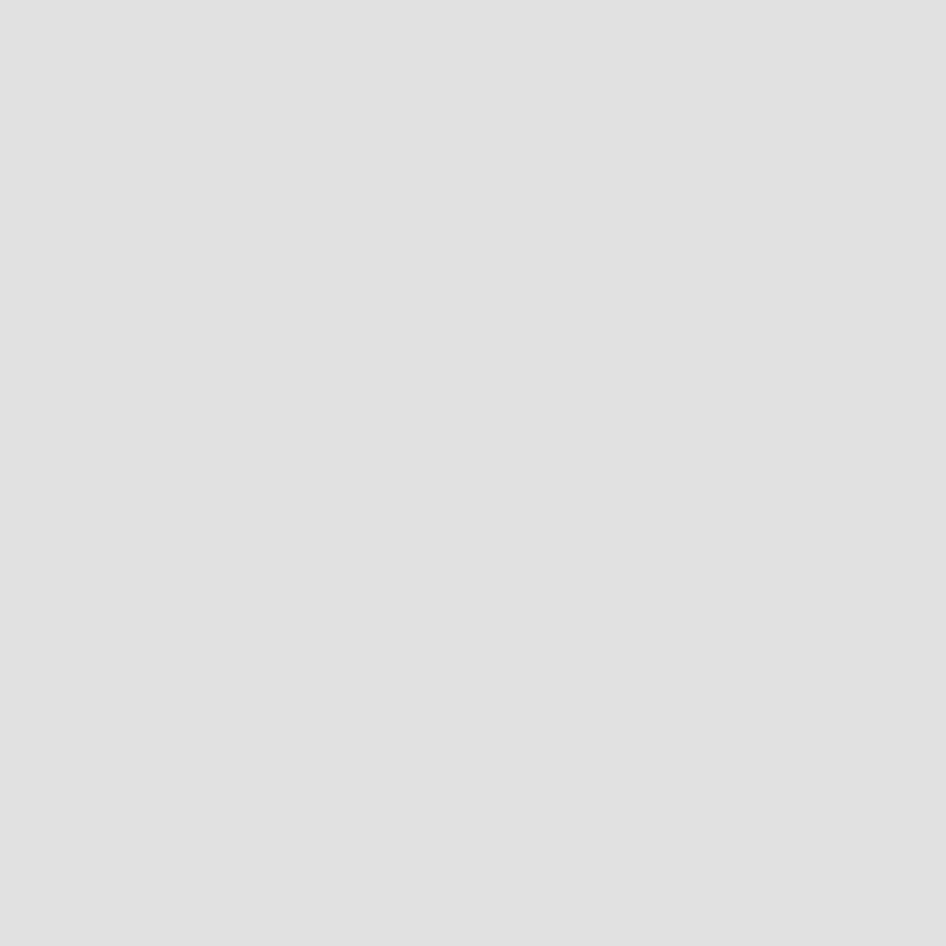
How to Reduce Exposure to Respirable Crystalline Silica
Alexandra Serban
December 2, 2019
Did you know a paver releases 45 million mcg of dust into the air?
According to OSHA’s new rule, for every meter of cubic air the worker breathes, he or she should inhale no more than 50 mcg of silica, averaged over an eight-hour shift.
To understand and comply with the new OSHA PEL, three factors need to be considered: air, time and dust.
· How much dust is released when performing a specific task?
· How much time can a worker be exposed, and at what level of exposure?
Measuring silica exposure is typically done through air monitoring. During a normal work shift, a battery-operated vacuum attached to an operator’s collar collects a sample by pulling air through a cyclone, and the particles are then analyzed in a laboratory. If a worker is exposed to 100 mcg/m3, for instance, he should perform the task for half the time. The more dust, the less time.
The best control measures
On Aug. 15, 2019, OSHA released a request for information and comment on Table 1 of the Respirable Crystalline Silica Standard for Construction (1926.1153). Specifically, the agency is looking for feedback before Oct. 14, 2019, on operations and the effectiveness of dust control measures not currently listed in Table 1. The agency is also gathering information on silica-generating equipment. OSHA will follow through with the revisions if they are approved by the Office of Management and Budget (OMB).
“Expanding Table 1 to include additional engineering and work practice control methods, equipment, and tasks could provide employers with more flexibility and reduce regulatory burdens while maintaining protections for employees,” OSHA’s press release says.
Table 1 outlines 18 tasks commonly associated with respirable silica dust exposure. Each task includes engineering controls, work practices, and the respiratory PPE required. Note that construction employers who follow Table 1 are not required to monitor employee exposure to silica and are not subject to the PEL.
Ideally, silica-containing materials should be replaced, whenever possible. Work processes should be isolated, and proper ventilation should be provided. If this is not possible, engineering controls need to be set up.
Most silica dust control methods imply using tools and equipment that feed water to the work surface to keep dust away. NIOSH tested a water spray to suppress dust created during concrete pavement breaking. This solution reduced dust exposure by 70% to 90%. Other tools include shrouds and dust collections systems, such as vacuums with self-cleaning HEPA filters.
Respirator selection guidance
When these measures prove inefficient, respiratory PPE, or RPE, becomes mandatory.
The employer first needs to establish a comprehensive respiratory protection program, as described in the Guide to Industrial Respiratory Protection (NIOSH 1987a) and as required in the OSHA respiratory protection standard (29 CFR 1910.134 and 1926.103). This program includes periodic environmental monitoring, selection of NIOSH-approved respirators, respirator fit testing, and rules for inspection and cleaning of RPE.
Protection from respirable crystalline silica takes the form of a filtering facepiece or a reusable facepiece with filters, based on the level of dust concentration. NIOSH recommends half-piece particulate respirators with N95 filters for airborne silica particles, for concentrations less or equal to 0.5mg/m3. OSHA also recommends filter efficiency no lower than a 95 rating. For a specific list of work activities and associated RPE, consult Table 1.
How to prevent silica health hazards?
Prevention is always better than cure. Worker health surveillance is important to prevent or detect silicosis or other silica-related diseases. Analyzing past exposure and latency should be part of this process.
Training is also critical to increasing awareness of silica dust sources. Under the new rule, training is performance-based, depending on the worker’s knowledge and understanding of health hazards, best work practices, and respiratory protection specs. Each employer has the liberty to determine the requirements, but the regulations do mention that “a full hour of training will be required for all covered workers.”
Lastly, housekeeping – or how sites clean up – plays a crucial role in keeping health hazards at bay. Make sure spills are cleaned up fast, debris is always removed from equipment, waste is handled correctly, and storage areas are ventilated.
Let's Connect!
Sign up to receive exclusive communications from Honeywell including product updates, technical information, new offerings, events and news, surveys, special offers, and related topics via telephone, email, and other forms of electronic communication.
Copyright © 2025 Honeywell International Inc
Maximum File Size
Maximum Files Exceeded
Due to inactivity you will be logged out in 000 seconds.
Maximum File Size
Maximum Files Exceeded
You cannot access this page as this product is not available in your country.