-
Global
-
Africa
-
Asia Pacific
-
Europe
-
Latin America
-
Middle East
-
North America
- |
- Partners
- |
-
Currency:Localize your Content
You can set your preferred currency for this account.
Choose a Currency
Currency- CHOOSE YOUR CURRENCY
Update Currency
Changing Currency will cause your current cart to be deleted. Click OK to proceed.
To Keep your current cart, click CLOSE and then save your cart before changing currency.
-
Select Account
Switching accounts will update the product catalog available to you. When switching accounts, your current cart will not move to the new account you select. Your current cart will be available if you log back into this account again.
Account# Account Name City Zip/Post Code CANCELPROCEEDMy Account
-
Support
- View All Productivity Solutions
- Warranties
- Patents
- Global Locations
- Technical Support
- Discontinued Products
- Quality Program and Environmental Compliance
- Return Material Authorization (RMA)
- Legal Documents
- Product Certification
- Software Downloads
- Cyber Security Notifications
- Case Studies and Success Stories
-
Global
-
Africa
-
Asia Pacific
-
Europe
-
Latin America
-
Middle East
-
North America
- |
- Partners
- |
You are browsing the product catalog for
You are viewing the overview and resources for
- News & Events
- Featured stories
- Personal Protective Equipment
- How to Detect Atmospheric Hazards in Confined Spaces
How to Detect Atmospheric Hazards in Confined Spaces
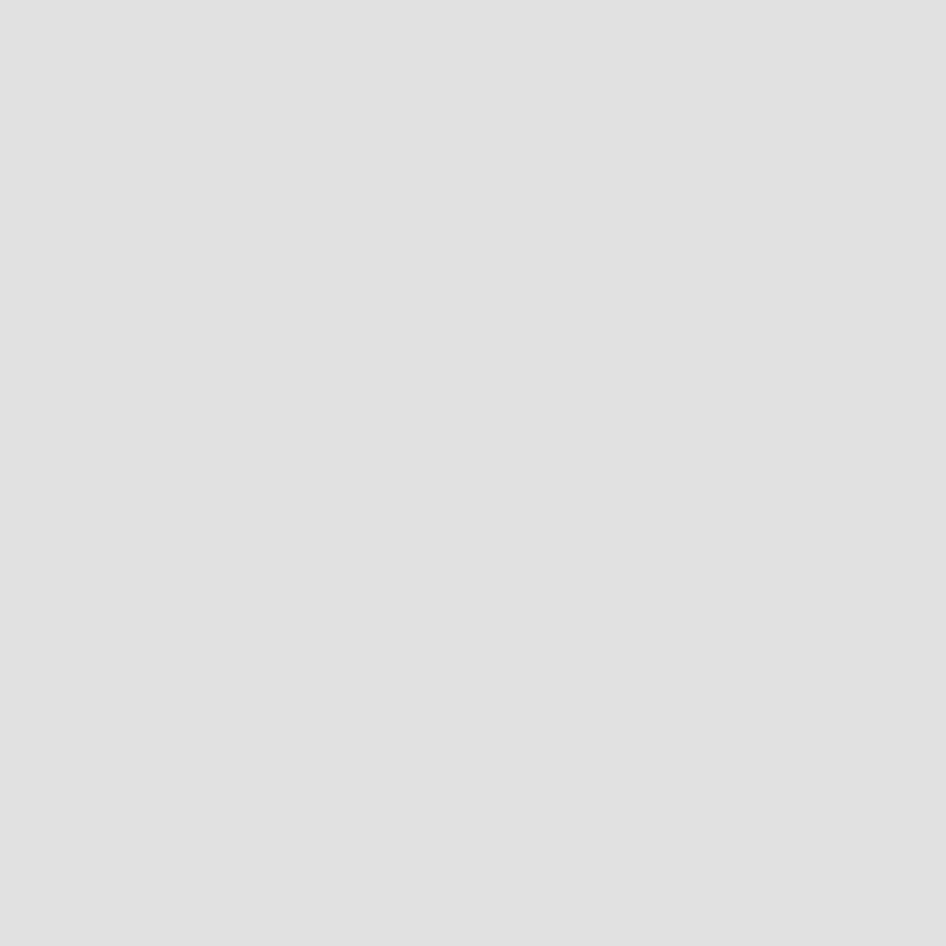
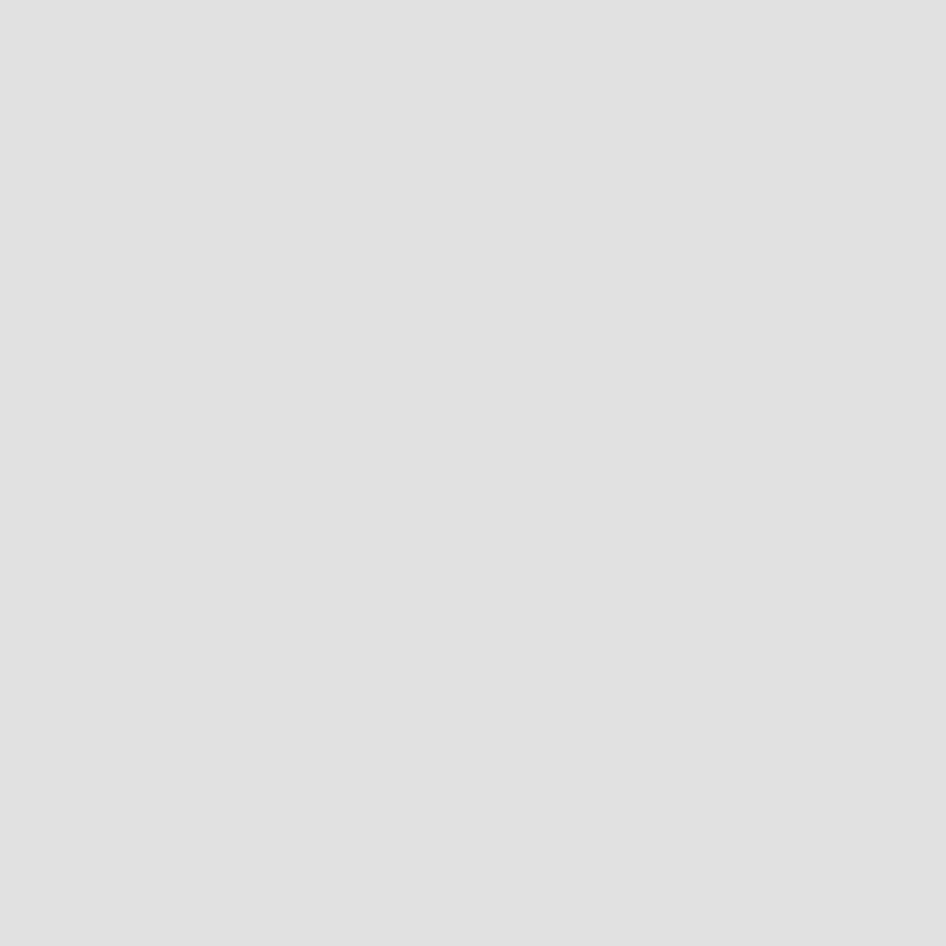
How to Detect Atmospheric Hazards in Confined Spaces
Jacob Spector
September 12, 2019
Poor air quality and hazards posed by asphyxiates and toxic gases are some of the most common and deadly hazards faced in a confined space.
How do we identify them as efficiently as possible before putting people at risk?
Confined space regulations define an atmospheric hazard “as an atmosphere that may expose workers to the risk of death, incapacitation, impairment of ability to self-rescue, injury, or acute illness.” Common causes include:
1. Oxygen deficiency
2. Flammable gases, vapors, mists with more than 10% of its lower explosive limit (LEL).
3. Toxic gases
4. Airborne combustible dust at a concentration that meets or exceeds its LEL.
Toxic gases
The most common toxic gases found in confined spaces are Volatile Organic Compounds (ppm VOC), Carbon Monoxide (ppm CO) and Nitrogen Dioxide (ppm NO2). They are usually the by-product of operations such as painting and gas or diesel generators. When found in excess, workers can experience acute issues like headaches, confusion, and unconsciousness. Even in lower levels, workers can experience longer term health effects.
Oxygen
An asphyxiating and therefore,” inadequate” atmosphere is one which contains less than 19.5 percent oxygen, according to OSHA. The normal volume of oxygen in ambient air is 20.9%. Alarm levels are 19.5% for oxygen deficiency, 23.5% for oxygen enrichment and 10% LEL for combustion gases.
Low levels of oxygen can be the result of open flame operations, such as welding, cutting or brazing or natural phenomena present in swampy areas, sewers or landfills. Some materials, such as charcoal may absorb oxygen or consume it in their chemical reactions, such as rusting. In some cases, some gases, such as nitrogen, helium or carbon dioxide have been intentionally used to purge an environment before work can be completed, thus displacing oxygen.
Flammable gases
Combustible gas buildup in a confined space can lead to the most dangerous of situations. It doesn’t take long for a combustible gas, like Methane, to build up in a small confined area. Combine that with the right Oxygen levels and all you need is a spark to cause a catastrophic explosion. Therefore, air monitoring is required and should be done remotely before entering a confined space. Being careful to check that Oxygen and Combustible gas levels are normal.
Which gases should I monitor?
The responsibility of choosing what gases to monitor typically lies in the hands of a safety specialist or certified industrial hygienist. Gases are usually monitored in this order, as recommended by OSHA:
1. Oxygen – to ensure proper levels are present and another gas is not displacing Oxygen.
2. Combustible gases – to ensure they are not present.
3. Toxic gases - to make sure they are below OSHA’s permissible exposure limit.
The results must be recorded on the work entry permit, below the levels identified for safe entry.
What tools to use?
There are many four-gas confined space monitors on the market that will only be equipped with a combination of four gas sensors. However, through safety evaluation, additional gas hazards may be identified. In those cases, a 5 or 6 gas monitor, equipped with the appropriate sensors, is best.
But first, let’s talk a bit about sensors. Sensors are at the heart of every gas monitor. These devices are packed with various types of sensors: combustible gas sensors, photoionization sensors, infrared sensors, , electrochemical sensors etc. They serve a variety of applications and are quite common in industrial plants, refineries, and applications with Confined Space areas.
Four-gas vs. Five + gas monitors
Knowing the application is the first step in choosing the right type of monitor. And this decision can go a long way in saving costs, while making your work more time-effective and giving you a better overall experience.
There are two main types of gas detectors.
- 4-gas monitors are great solutions for most confined space applications. They usually have the lowest up front cost and are smaller and lighter than other confined space monitors in the market. However, they are limited to just 4 sensors, usually without the ability to add a 5th later down the road.
- 5+ gas monitors are much more flexible and can be configured to meet a variety of applications both when used and in the future. However, unlike the 4-gas monitor, 5+ gas monitors usually come with a higher initial price point and will be larger and heavier.
Whatever solution you choose, it’s important to remember that cheaper is not always better, as maintenance costs need to be considered as well. Can the gas detector be repaired, is it robust enough for the environment, how much are service parts?
General guidelines for sampling procedures
Depending on the application and type of confined space entry pre-check needed, there can be a variety of methods to get the job done.
Before monitoring, make sure the instrument is operational and filters are in good condition – not contaminated, intact and ready for use. Inspect the probe to ensure the seals are intact and you have a good sampling path, without any blockage. Make sure the tubing attached to the end of the probe and the pump is in good repair.
When it comes to calibrating air monitoring equipment to ensure accuracy of the equipment, OSHA recommends following the manufacturers’ instructions.
“The atmosphere of a confined space should be analyzed using equipment of sufficient sensitivity and specificity to identify and evaluate any hazardous atmospheres that may exist or arise”, OSHA says. “Evaluation and interpretation of these data, and development of the entry procedure, should be done by, or reviewed by, a technically qualified professional (e.g., OSHA consultation service, or certified industrial hygienist, registered safety engineer, certified safety professional, certified marine chemist, etc.) based on evaluation of all serious hazards.”
Stratification of gases is another factor you will need to account for. Gases have different weights compared to the normal atmosphere and therefor can reside at the top, middle or bottom of a confined space. That’s why it’s important to take air samples at the top, middle and bottom of the confined space to identify different concentrations of gases and vapors. OSHA recommends testing the area around the worker, namely four feet in the direction of travel and to each side.
Minimum response time is also important– the time needed for the monitor to draw a sample and for the sensor to react to the gases, if present. Pumped monitors draw air at different flows, but you’ll usually want to account for 2-3 seconds per foot of tubing to get the sample to the detector. Depending on the sensors reaction time you’ll need to add an additional 15-20 seconds for gas stabilization time..
Another approach is using a diffusion-based monitor and lowering the entire monitor into the confined space – assuming it is a vertical entry. This brings a cost savings, as diffusion monitors are typical more affordable than pumped monitors.
It’s also time-saving, as there’s no need to wait for the pump to draw a sample. However, the user loses the ability to see the readings while doing the samples and often must scroll through menus to see what the readings were after the monitor is lifted out of the confined space. This approach is not recommended by most safety professionals and gas detection manufactures. It requires an experienced and knowledgeable user who understands both how to recover readings and what decisions to take.
A third approach includes Bluetooth wireless technology. A user can use a diffusion-based monitor, as mentioned in the second approach. However, instead of waiting to get the unit back to see the readings, a Bluetooth signal can send immediate readings back to a mobile phone/display held by the user. This approach can deliver the fastest results; however, it will come with a higher price tag than the first two. Bluetooth monitors are slightly more expensive than non-Bluetooth monitors. However, the true additional cost comes with the need of a mobile phone/display. While this is a new method for many, the value behind can’t be denied.
Once monitoring is finished, the entry permit needs to be completed. However, the confined space should be continuously monitored throughout the work being done. Conditions in a confined space can change rapidly, due to the work being done or other potential hazards like unexpected gas leaks.
Remember that each confined space has its own set of challenges, hazards and risks, so it must be appropriately assessed before any job is being done.
Let's Connect!
Sign up to receive exclusive communications from Honeywell including product updates, technical information, new offerings, events and news, surveys, special offers, and related topics via telephone, email, and other forms of electronic communication.
Copyright © 2025 Honeywell International Inc
Maximum File Size
Maximum Files Exceeded
Due to inactivity you will be logged out in 000 seconds.
Maximum File Size
Maximum Files Exceeded
You cannot access this page as this product is not available in your country.