-
Global
-
Africa
-
Asia Pacific
-
Europe
-
Latin America
-
Middle East
-
North America
- |
- Partners
- |
-
Currency:Localize your Content
You can set your preferred currency for this account.
Choose a Currency
Currency- CHOOSE YOUR CURRENCY
Update Currency
Changing Currency will cause your current cart to be deleted. Click OK to proceed.
To Keep your current cart, click CLOSE and then save your cart before changing currency.
-
Select Account
Switching accounts will update the product catalog available to you. When switching accounts, your current cart will not move to the new account you select. Your current cart will be available if you log back into this account again.
Account# Account Name City Zip/Post Code CANCELPROCEEDMy Account
-
Support
- View All Productivity Solutions
- Warranties
- Patents
- Global Locations
- Technical Support
- Discontinued Products
- Quality Program and Environmental Compliance
- Return Material Authorization (RMA)
- Legal Documents
- Product Certification
- Software Downloads
- Cyber Security Notifications
- Case Studies and Success Stories
- View All Sensing Solutions
- Sales Contact Form
- Technical Support
- Certificates
- eCOM Portal
- Distributor Inventory
- Return Material Authorization (Test & Measurement)
- Return Material Authorization (Citytech)
- Return Material Authorization (EnviteC)
- Legal Documents
- Intelligent Life Care
- Return Material Authorization (ILC)
-
Global
-
Africa
-
Asia Pacific
-
Europe
-
Latin America
-
Middle East
-
North America
- |
- Partners
- |
You are browsing the product catalog for
You are viewing the overview and resources for
- News & Events
- Featured stories
- Unload Fully and Autonomously With Less Product Damage | Honeywell Intelligrated
Unload Fully and Autonomously With Less Product Damage
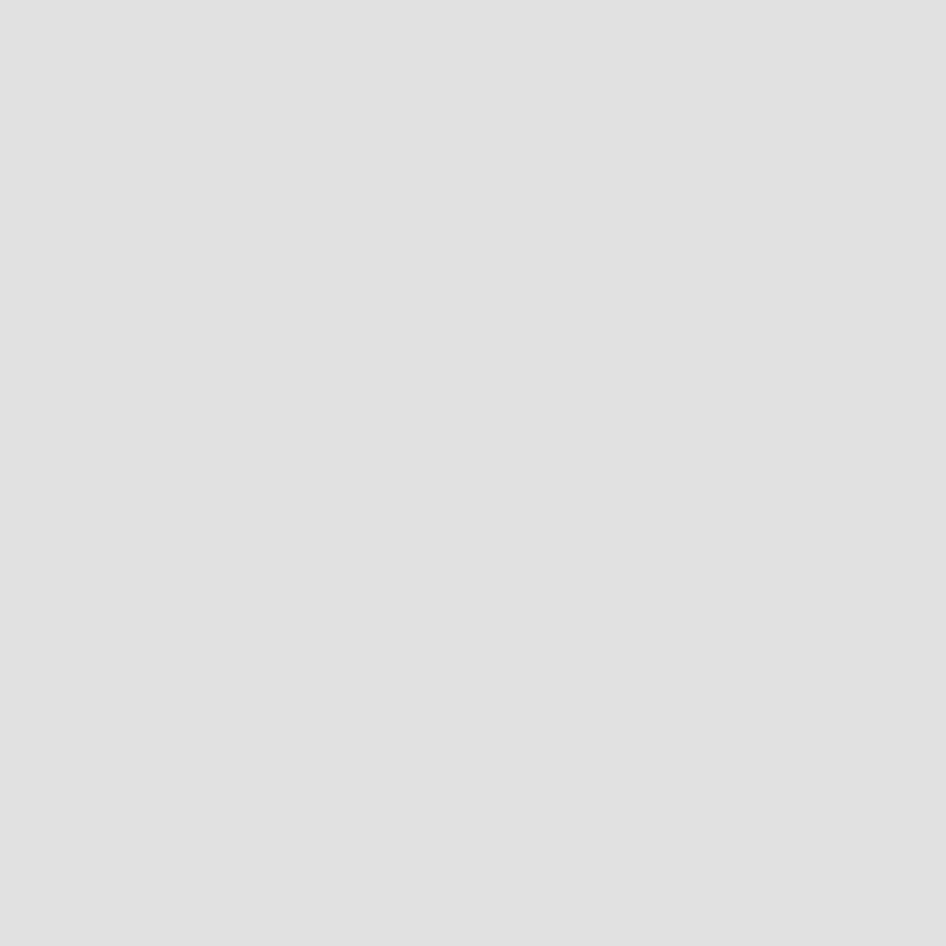
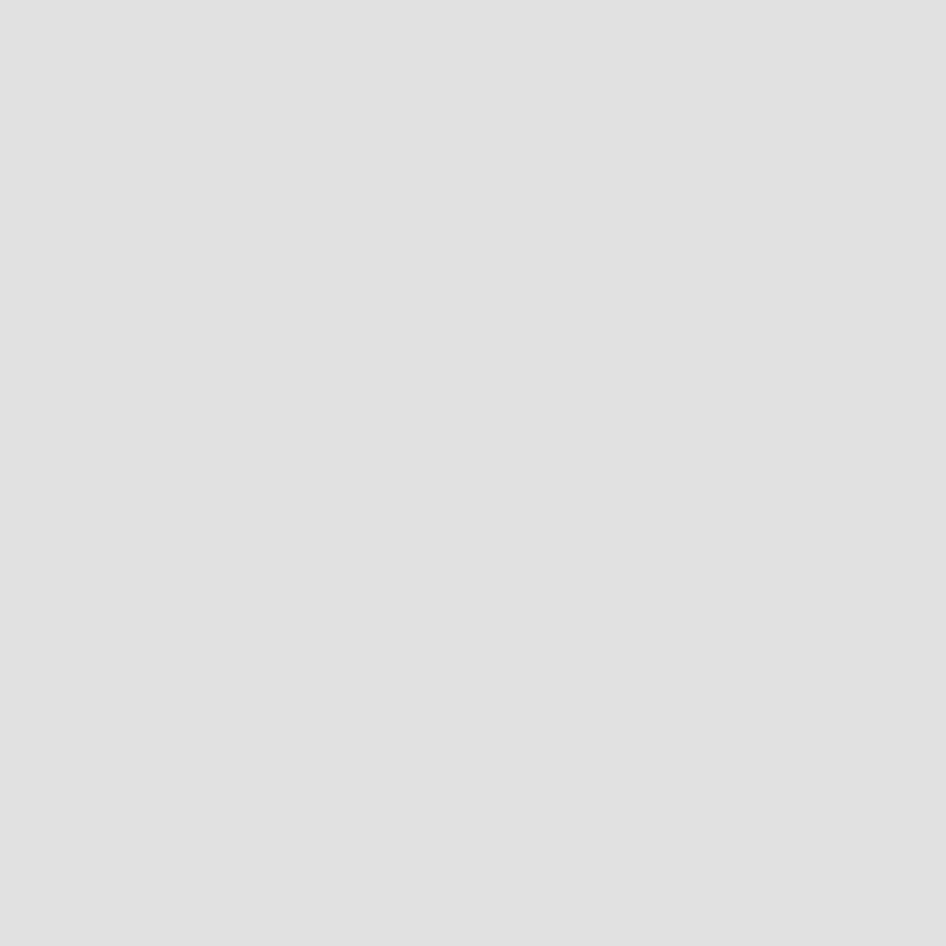
Unload Fully and Autonomously With Less Product Damage | Honeywell Intelligrated
Matt Wicks
August 10, 2020
Next-generation robotic unloaders from Honeywell Intelligrated can do more than just minimize delays. Trailers can be unloaded fully autonomously, sending boxes, polybags and jiffy bags downstream in a semi-singulated flow. The robot’s efficiency can reduce your dock labor needs by up to 80%, and might even allow you to free up valuable space by using fewer loading bays.
Here’s how it works:
Using a combination of a vacuum arm and a conveyor sweep system, these robots are capable of handling diverse case sizes and weights, even from trailers that haven’t been loaded with robots in mind. The machine can handle cases from 1 to 75 pounds, and product dimensions as small as a box of tissues or as large as a washing machine. This range is designed to accommodate the variety of sizes, shapes and quantities typically found in today’s e-commerce operations.
But the innovations don’t stop there.
What makes these robots truly revolutionary is a cutting-edge electronic “brain.” Next-generation robotic unloaders are among the first to benefit from the Honeywell Universal Robotics Controller (HURC), which combines high-speed processing, improved vision and machine learning-based decision making with advanced motion planning. This system also offers full connectivity, allowing robotic unloaders to incorporate advanced machine learning and use data from other robots to improve their perception and decision making.
Depending on case size and operational specifications, HURC enables each robot to unload over 1,900 cases per hour — more than double the rate of manual processes. Even at this speed, the same system also enables the robot to handle packages with greater care. The articulated nose conveyor positions itself to minimize drop distance. The system’s unloading aggressiveness can also be customized for each application to ensure customers receive merchandise intact.
Robust operating algorithms, an integrated unscrambler and dynamic side guides minimize the chances of a jam and keep product flowing, while automated exception detection alerts operators to handle unexpected pallets. In the event of fallen or missed packages, the robotic unloader’s nose conveyor automatically adjusts height and angle to sweep them up with ease; no operator involvement is required.
This fully autonomous performance means there’s no need for an operator to remain on standby or direct the machine. Operators can spend that time overseeing as many as four additional robotic unloaders or performing other tasks. And thanks to standard industrial controls and a simple machine design, these employees don’t need advanced skill sets.
To learn more about the technical capabilities of the robotic unloader, as well as the labor-relieving benefits it can offer your operation, download our Robotic Unloader brochure.
To subscribe to our blog and receive exclusive communications and updates from Honeywell Intelligrated, click here.
Let's Connect!
Sign up to receive exclusive communications from Honeywell including product updates, technical information, new offerings, events and news, surveys, special offers, and related topics via telephone, email, and other forms of electronic communication.
Copyright © 2025 Honeywell International Inc
Maximum File Size
Maximum Files Exceeded
Due to inactivity you will be logged out in 000 seconds.
Maximum File Size
Maximum Files Exceeded
You cannot access this page as this product is not available in your country.