-
Global
-
Africa
-
Asia Pacific
-
Europe
-
Latin America
-
Middle East
-
North America
- |
- Partners
- |
-
Currency:Localize your Content
You can set your preferred currency for this account.
Choose a Currency
Currency- CHOOSE YOUR CURRENCY
Update Currency
Changing Currency will cause your current cart to be deleted. Click OK to proceed.
To Keep your current cart, click CLOSE and then save your cart before changing currency.
-
Select Account
Switching accounts will update the product catalog available to you. When switching accounts, your current cart will not move to the new account you select. Your current cart will be available if you log back into this account again.
Account# Account Name City Zip/Post Code CANCELPROCEEDMy Account
-
Support
- View All Productivity Solutions
- Warranties
- Patents
- Global Locations
- Technical Support
- Discontinued Products
- Quality Program and Environmental Compliance
- Return Material Authorization (RMA)
- Legal Documents
- Product Certification
- Software Downloads
- Cyber Security Notifications
- Case Studies and Success Stories
- View All Sensing Solutions
- Sales Contact Form
- Technical Support
- Certificates
- eCOM Portal
- Distributor Inventory
- Return Material Authorization (Test & Measurement)
- Return Material Authorization (Citytech)
- Return Material Authorization (EnviteC)
- Legal Documents
- Intelligent Life Care
- Return Material Authorization (ILC)
-
Global
-
Africa
-
Asia Pacific
-
Europe
-
Latin America
-
Middle East
-
North America
- |
- Partners
- |
You are browsing the product catalog for
You are viewing the overview and resources for
- News & Events
- Featured stories
- Honeywell Voice Takes a Huge Leap Forward With Voice-Enabled Maintenance and Inspection Checklists
Honeywell Voice Takes a Huge Leap Forward With Voice-Enabled Maintenance and Inspection Checklists
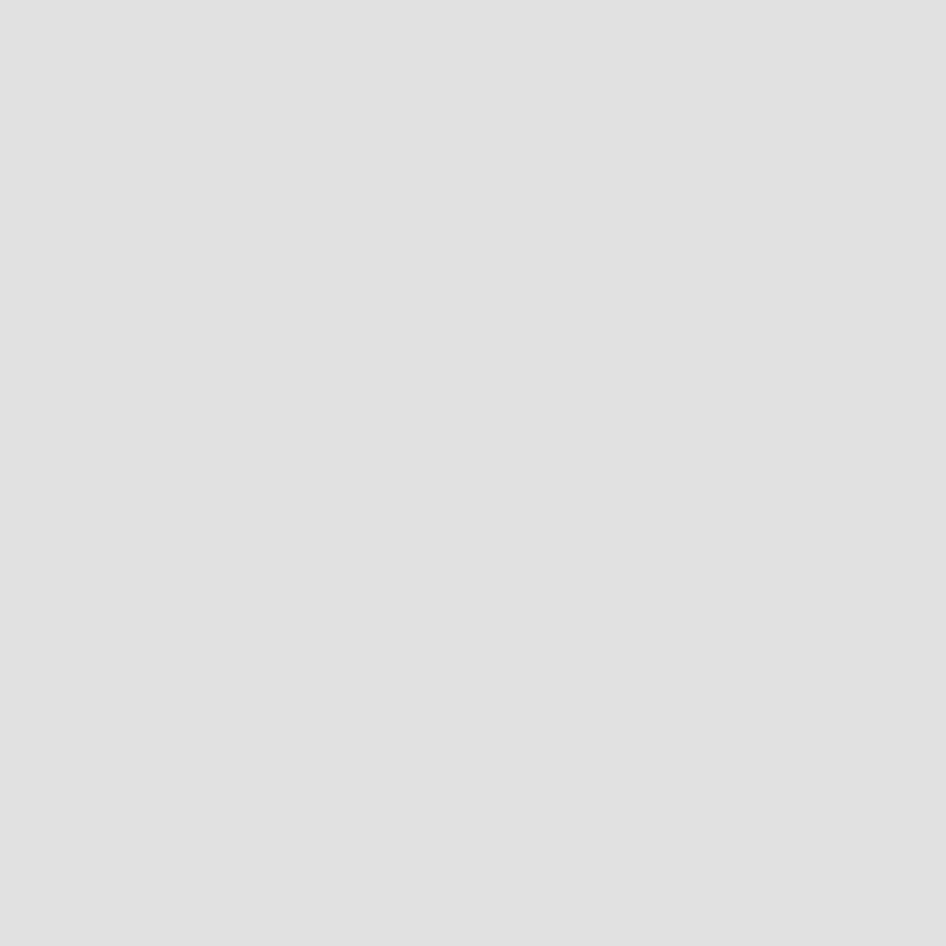
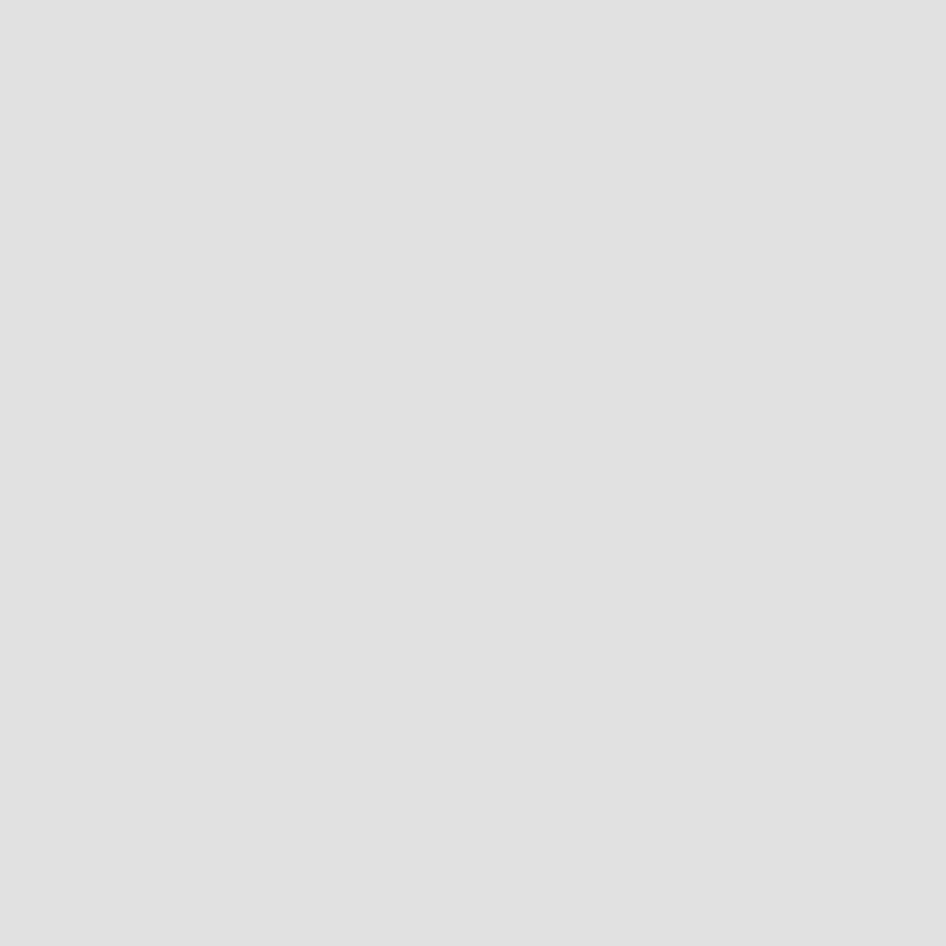
Honeywell Voice Takes a Huge Leap Forward With Voice-Enabled Maintenance and Inspection Checklists
Barry J. Ewell
November 22, 2019
Checklists, work orders, audits, work cards, and other complex processes are an essential part of almost every industry. It’s a traditional system where instructions are read and followed, discrepancies and measurements recorded, and at the end of the procedure certain steps may be signed off on as verification of accomplishment. We are taking checklists that have been created for paper or digital applications and voice-enabling them by turning them into commands the operator can hear and engage with.
Honeywell Voice for Maintenance and Inspection comprises voice-directed work technology for technicians, auditors, operators, and individuals tasked with completing a wide variety of reviews on vehicles, machinery, engines, and more in a host of environments. Rather than recording findings on paper and manually entering them into a database, the interaction between technicians and the system is carried out by voice while the system is updated automatically. With a voice-directed, hands-free and eyes-free inspection process, workers eliminate skipped steps, make fewer errors, are more productive, and have higher job satisfaction. The voice-directed solution eliminates the post-inspection manual data entry process and facilitates compliance with various inspection processes.
Here is an example of how Honeywell Voice Maintenance and Inspection is used for Aviation MRO facilities for repair and overhaul of Auxiliary Power Units (APUs), engines, and avionics. The technician wears a wireless headset and a voice-enabled mobile computing device. Through the company's wireless network, the technician is connected to Honeywell Voice and the company’s in-house ERP/EAM records system.
For example, an APU is received in the shop and the first task is an incoming inspection. The system once activated directs the technician by voice command through the incoming inspection checklist and allows for hands-free, eyes-free voice data entry. The system captures all information through spoken commands. The technician responds to work instructions with answers such as Yes, No, and Check, provides measurements when the task requires, and recognizes completion of steps.
Using Honeywell Voice for Maintenance and Inspection cuts down on the outdated back-and-forth data entry and look-up time on a laptop, handheld device, or paper forms by speaking commands and verbally inputting data findings directly into your system via a headset with a microphone, while performing the inspection task. The benefits we have seen across industries include:
- Streamlined documentation – by completing observations and findings documentation while performing the actual task.
- Process improvement – through the use of best-in-class processes and actionable operational insights.
- Faster training and new technician onboarding – with easy-to-follow documentation and inspection processes for existing and new technician training.
- Enhanced compliance – with strict adherence to standard operating procedures (SOPs) to ensure standardized processes through consistent technician behavior.
- Improved safety – by enabling hands-free, eyes-free operations at the point of inspection.
- Greater technician retention – by providing an intuitive solution that motivates and enables technicians to be more productive and increases employee satisfaction.
Honeywell Voice can be deployed to a myriad of hardware devices including:
- Honeywell Android™-based CT40 and CT60 built on the Mobility Edge™ platform
- Third-party Android or Apple® iOS devices (e.g., ruggedized, consumer-grade), allowing you to leverage your existing device investments
- Honeywell Voice integrated Talkman series (e.g., A500, A700 and A700X series, headsets, and peripherals)
- PCs connecting to Bluetooth® headsets (e.g., SRX series) for 10 meter (30 feet) connectivity
Managers have a real-time view of each operator, work in process, and work completed. They have the ability to become granular in their review. For example, if there is a portion of an inspection that normally takes 2 minutes and the operator is taking less than 30 seconds, that could be a red flag that the operator is doing a less-than-adequate job or needs more training on the process. In other cases, the test might call for 9-minute test. If the test was completed in less than the required time, the technician did not perform the test properly.
With voice-enabled checklists, you can:
- Multiple list selection. Create multiple list selections where the operator can choose from different responses such as yes, no, pass/fail, damage, normal, or whatever response is desired.
- Conditional, if/then statements. Create conditional, if/then statements – for example, if something has damage in a previous step, the operator could be instructed to take a photograph of the damage.
- Voice notes. Provide options for the operator to include additional information at different points in the inspection. For example, if the operator notices damage to lug nuts, they could say “Lug nuts are rusted and stripped.” A transcript of the notes will be logged in the system. The transcribed voice note information can then be passed on to a supervisor for review or a repair work order to fix the damage.
We have worked with companies throughout the world to develop applications for:
Aviation
The application is providing aviation customers with better documentation, greater compliance, and consistent processes. A leading aerospace manufacturer realized a 30% reduction in production data entry-cycle time and significant gains in accuracy levels by implementing Honeywell Voice. The following are examples of how Honeywell Voice for Maintenance and Inspection is being used in aviation:
- Engine MRO. Honeywell Voice help streamline off-wing repair to restore aircraft engines to designed operational condition.
- Heavy maintenance. Honeywell Voice help streamline inspection of airframe components, comprehensive structural inspection, and overhaul of aircraft.
- Component MRO. Honeywell Voice enable regular aircraft inspection and maintenance checks to ensure flight-worthiness.
- Line maintenance. Honeywell Voice support the execution of component MRO for APU, Avionics, wheels and brakes, communication equipment, flight controls, etc.
See video examples and watch technician feedback.
Lufthansa Technik AG
Truck Fleets
The application is providing trucking fleet customers with improved compliance documentation, process consistency, and streamlined record keeping. A leading fleet leasing and management company projects a reduction in total asset inspection time by almost 25% with Honeywell Voice and will use the increased available technician time to broaden its inspection offerings as a market differentiator. They also improved quality by 3%, which has accounted for a reduction in unplanned maintenance across their fleet. The following are examples of how Honeywell Voice for Maintenance and Inspection is being used in truck fleets:
- Regulatory compliance and preventive maintenance. Honeywell Voice enable fleet owners and lessors to optimize the maintenance of power units and trailers and are supportive of the most common regulatory requirements and preventive maintenance checklists.
- Repairs. Honeywell Voice help the documentation process for repairs of power units and trailers, on an as-needed basis, including the capture of parts replaced and new parts ordered.
- Aftermarket services. Help ensure SOP checklists are fully adhered to with Honeywell Voice when performing retrofits with additional parts or components.
Watch the video to see how Penske Truck Leasing, a leader in truck fleet maintenance and leasing, keeps its fleet of more than 270,000 vehicles running smoothly with assistance from Honeywell Voice.
Automotive Fleets
The application is providing automotive fleet customers with automotive inspection, consistent processes, and improved technician retention. A national car maintenance service organization with high technician turnover needed to increase technician adherence to standard procedures and documentation processes to help ensure accurate billing. They discovered our voice solution would provide standardization and management visibility needed to support growth initiatives across a growing number of locations. Automotive fleets have experienced the ability to:
- Provide process consistency. Honeywell Voice ensure your technicians follow a consistent step-by-step standard operating procedure (SOP) across multiple locations, ensuring that your inspection processes are properly supported and meet all necessary requirements.
- Onboard new technicians rapidly. Honeywell Voice help you retain and onboard new technicians quickly. The easy-to-follow voice commands guide each technician through each step of the standard processes and reduce the need to interact with complex technology alternatives. Your technicians will show greater confidence and be proud to use exciting voice technology from Honeywell.
Logistics Inspection and Assembly
The application is providing logistics inspection and assembly companies step-by-step process guidance, increasing throughput and reducing training time. Many of these customers are already experiencing the benefits of Honeywell Voice in their distribution centers. With the Maintenance and Inspection offering, the proven value of Honeywell Voice can be extended into additional, non-picking workflows. The expansion into other workflows can:
- Reduce training time for new technicians or workflows. As employees and assets change, training becomes more important. Through step-by-step voice guidance, technicians require less training and no shadowing. These improvements help you better utilize your workforce and improve efficiency during change.
- Train users for their task, not a data entry GUI. By queuing results and integrating directly with host systems, Honeywell Voice Maintenance and Inspection reduces the training required to interact with your chosen system of record. Technicians will no longer waste time navigating screens, but will focus on the work required, resulting in reduced process time and increased throughput.
See video examples and watch technician feedback.
Oil and Gas Industry
The application provides oil and gas companies the ability to collect valuable data, improve training, and enhance safety via hands-free, eyes-free inspections. In the oil and gas field, elevated risk of injury and fatality has been attributed to workers new to the industry. Honeywell Voice Maintenance and Inspection provides users with not only a safer, hands-free, eyes-free experience, but also a standardized approach to onsite training. Experience the ability to:
- Improve field work safety. Oil and gas work presents many safety challenges. Workers are required to not only navigate heights in their environment, but also avoid potentially explosive situations. By allowing workers to focus on the task at hand, Honeywell Voice improves safety.
- Improve training. By standardizing operations and directing a user step-by-step through a process, Honeywell Voice eliminates shortcuts during training. Workers are onboarded faster and trained more thoroughly.
Utility Field Workers
The application provides utility field workers a hands-free option for improved safety, data entry directly from the field, and process steps from one location. Experience the ability to:
- Increase field work safety. Field inspections rely on technicians to utilize their hands and eyes to remain safe while navigating their environment. By removing common data collection tools such as paper and pen or tablet forms, Honeywell Voice dramatically improves utility inspection safety.
- Eliminate redundant data entry. Network connectivity and host system software may not always be available in the field. Honeywell Voice Maintenance and Inspection captures, queues, and transmits data when a network becomes available. This functionality prevents technicians from being interrupted and completely eliminates the need to re-enter data once an inspection is completed in the field.
Healthcare
The application provides healthcare companies the ability to eliminate transposition errors, improve quality, and provide step-by-step guidance. For example:
- Reduce errors. Errors in healthcare can have significant consequences. Through standardization and elimination of transposition, process execution and data collection errors are reduced.
- Step-by-step guidance. Ensure equipment and processes critical to human health and well-being are maintained and executed properly. By providing users one step at a time, they are more focused and unlikely to miss steps or stray from established standardized methods.
- Optimized for healthcare. By providing hands-free, voice-enabled process guidance and data collection at the point of care, staff can maintain cleanliness best practices, while reducing documentation overhead.
Case Studies of Honeywell Voice for Maintenance and Inspection Checklists
The following are just a couple examples of businesses throughout the world who have incorporated Honeywell Voice for Maintenance and Inspection checklists.
Penske Truck Leasing
Who and what: Penske Truck Leasing Co., L.P., headquartered in Reading, Pennsylvania, is a partnership of Penske Corporation, Penske Automotive Group, and Mitsui & Co., Ltd. A leading global transportation services provider, Penske operates more than 266,000 vehicles and serves customers from more than 1,000 locations in North America, South America, Europe, Australia, and Asia.
Penske was seeking a solution to:
- Improve accuracy and consistency
- Reduce and eliminate paperwork
- Ensure documentation and compliance with regulations
Solution: Penske chose from Honeywell Voice, through partner Voiteq.
The system is in use across Penske's expansive network of truck fleet maintenance facilities in North America and taps into a robust, high-speed Aruba indoor and outdoor Wi-Fi network; uses rugged mobile tablet devices for maintenance technicians; and supplements those devices with an innovative voice-directed preventive maintenance system.
The system provides voice prompts via a headset to direct maintenance technicians through a preventive maintenance (PM) inspection. It is the foundation of Penske's proprietary PM process, providing the ability to tailor inspections to the specific vehicle, its age, specifications, and technologies now and in the future. Here’s the full circle of how the system works:
- A driver comes into a Penske Truck Leasing location and goes to a kiosk to log in truck information and request a repair or service.
- From there, the service manager receives the request and schedules the service.
- The technician puts on their Talkman or SRX series headset and is guided through the PM task, while the service manager can monitor the entire process on a tablet in real time.
- All of the data from the PM is recorded in real time as the technician works.
The solution has improved accuracy and consistency while reducing and eliminating paperwork and ensuring documentation and compliance with regulations. With the solution, workers make fewer errors, have higher job satisfaction rates, and are more productive.
In the first two-year period, Penske moved from about 82% PM quality to 89% as a company, but just last year alone, it moved four points, which meant 60,000 less unscheduled shop visits for their customers and service departments.
See the Penske Truck Leasing video.
Lufthansa Technik
Who and what: Lufthansa Technik APU Services facility in Hamburg, Germany. Technicians needed to work in teams on engine induction. One technician would inspect the engine and verbally pass the information on to another technician who either wrote it on a clipboard or entered it into a computer. The clipboard data would later have to be input into the computer, opening up many possible avenues for mistakes.
Solution: Lufthansa Technik chose Honeywell Voice to service Pratt & Whitney APS 3200 APUs. With the Honeywell application, a technician is guided through the induction process through interaction with a headset that is connected via Bluetooth to a wireless mobile computer on his belt, which automatically transmits the information to the company’s server. When performing the incoming inspection, the technician can now work hands- and eyes-free of distractions and can concentrate on the specific task at hand. The process continues through inspection and disassembly of the engine.
The system has saved hundreds of hours of technician time while improving quality and productivity. It has freed technicians from time-consuming and burdensome written documentation, which previously took up around 50% of their working hours.
See the Lufthansa Technik video.
U.S. Air Force – Warner Robins Air Logistics Center
Who and what: U.S. Air Force – Warner Robins Air Logistics Center. Maintenance and inspections of mission-critical assets (from aircraft to ground-based vehicles) require the use of well-defined checklists to be followed by maintenance technicians and detailed documentation of services performed for recordkeeping. This process is beset with inefficiencies. It requires the technicians working in these hands-busy, eyes-busy environments to enter their observations and findings as a separate step from the actual visual and manual asset inspections.
Solution: Honeywell’s voice-directed solution enables technicians to elevate their documentation and compliance to levels never before attainable by providing step-by-step verbal instructions while capturing observation data in a hands-free, eyes-free mode. Technicians listen to checklist instructions and capture their observations by simply speaking their responses.
It eliminates outdated back-and-forth manual data entry and look-up time on a laptop, handheld device, or paper forms. The solution also ensures that the technicians strictly adhere to the standard operating procedure for a given type of asset. The data captured is automatically transferred to any DoD EAM/back-end system for recordkeeping. Some results included:
- Reduced training time for new employees
- Increased accuracy and quality of service
- Reduced maintenance costs and turnaround time
Conclusion
Click here for more information about Honeywell Voice for Maintenance and Inspection, Honeywell’s voice-directed work technology for inspection technicians.
Our expert assessment teams will partner with you to understand your unique business requirements and identify where opportunities exist to optimize your workflows and increase efficiencies within today’s competitive climate.
At Honeywell, we work with thousands of distribution centers of all sizes, across a wide variety of industries worldwide. We bring a deep foundational understanding of the businesses we serve, backed with expert research and data that identifies the real, specific needs of today’s DC.
With over 130 years of on-the-ground experience, Honeywell is uniquely equipped to help you solve the problems that your business faces every day, see improved results, and be a trusted partner to help you reach and exceed your predetermined goals.
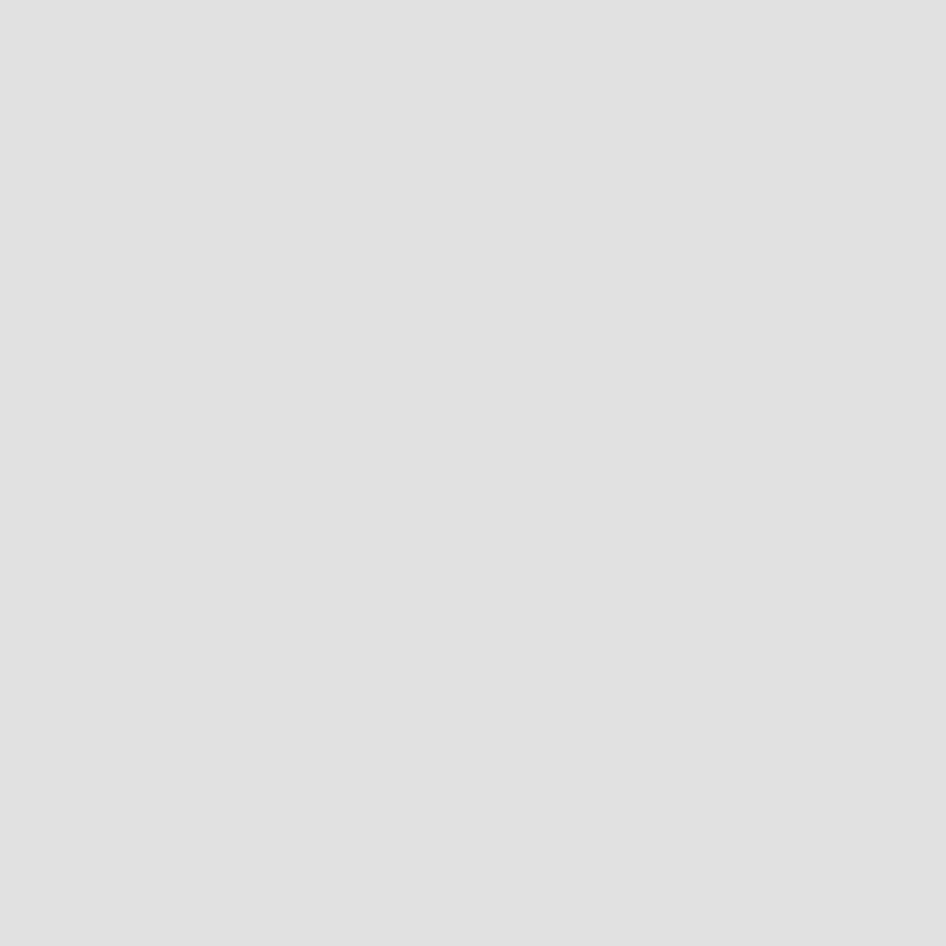
Barry J. Ewell is a Senior Content Marketing Communications Specialist for Honeywell Industrial Automation. He has been researching and writing on supply chain topics since 1991.
Let's Connect!
Sign up to receive exclusive communications from Honeywell including product updates, technical information, new offerings, events and news, surveys, special offers, and related topics via telephone, email, and other forms of electronic communication.
Copyright © 2025 Honeywell International Inc
Maximum File Size
Maximum Files Exceeded
Due to inactivity you will be logged out in 000 seconds.
Maximum File Size
Maximum Files Exceeded
You cannot access this page as this product is not available in your country.