-
Global
-
Africa
-
Asia Pacific
-
Europe
-
Latin America
-
Middle East
-
North America
- |
- Partners
- |
-
Currency:Localize your Content
You can set your preferred currency for this account.
Choose a Currency
Currency- CHOOSE YOUR CURRENCY
Update Currency
Changing Currency will cause your current cart to be deleted. Click OK to proceed.
To Keep your current cart, click CLOSE and then save your cart before changing currency.
-
Select Account
Switching accounts will update the product catalog available to you. When switching accounts, your current cart will not move to the new account you select. Your current cart will be available if you log back into this account again.
Account# Account Name City Zip/Post Code CANCELPROCEEDMy Account
-
Support
- View All Productivity Solutions
- Warranties
- Patents
- Global Locations
- Technical Support
- Discontinued Products
- Quality Program and Environmental Compliance
- Return Material Authorization (RMA)
- Legal Documents
- Product Certification
- Software Downloads
- Cyber Security Notifications
- Case Studies and Success Stories
- View All Sensing Solutions
- Sales Contact Form
- Technical Support
- Certificates
- eCOM Portal
- Distributor Inventory
- Return Material Authorization (Test & Measurement)
- Return Material Authorization (Citytech)
- Return Material Authorization (EnviteC)
- Legal Documents
- Intelligent Life Care
- Return Material Authorization (ILC)
-
Global
-
Africa
-
Asia Pacific
-
Europe
-
Latin America
-
Middle East
-
North America
- |
- Partners
- |
You are browsing the product catalog for
You are viewing the overview and resources for
- News & Events
- Featured stories
- How Label Verification Helps Avoid Costly Fines and Chargebacks Due to Defective Labels
How Label Verification Helps Avoid Costly Fines and Chargebacks Due to Defective Labels
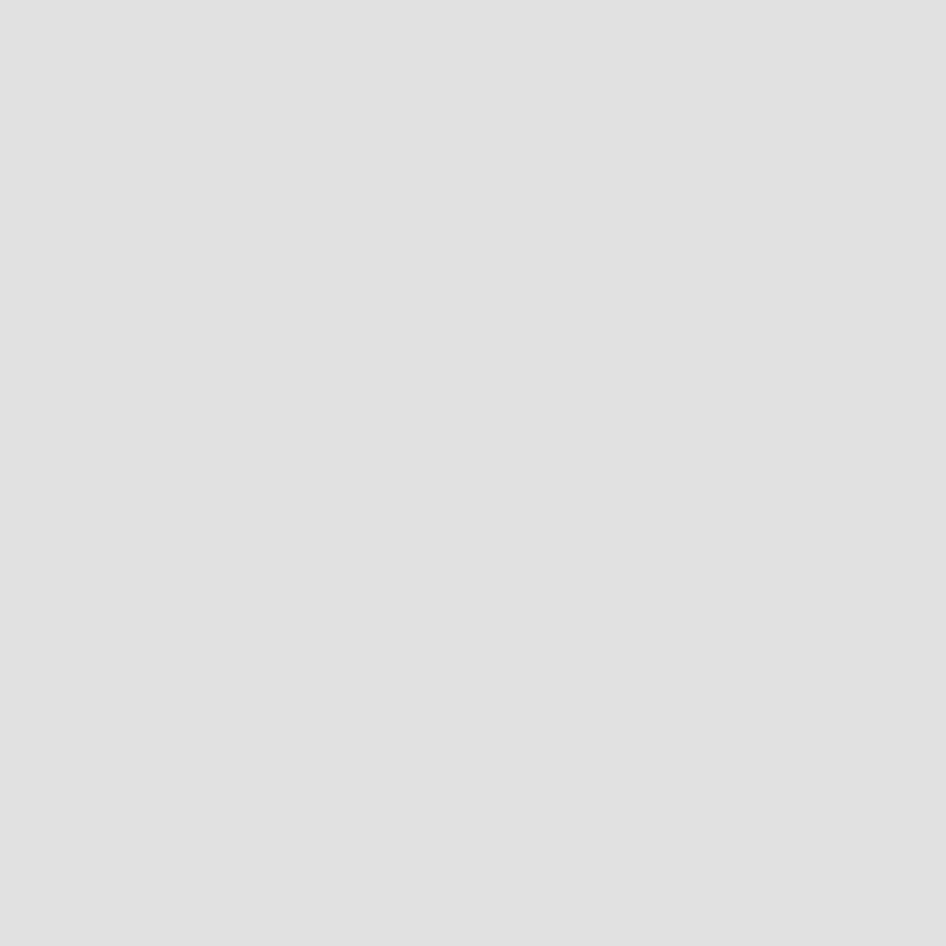
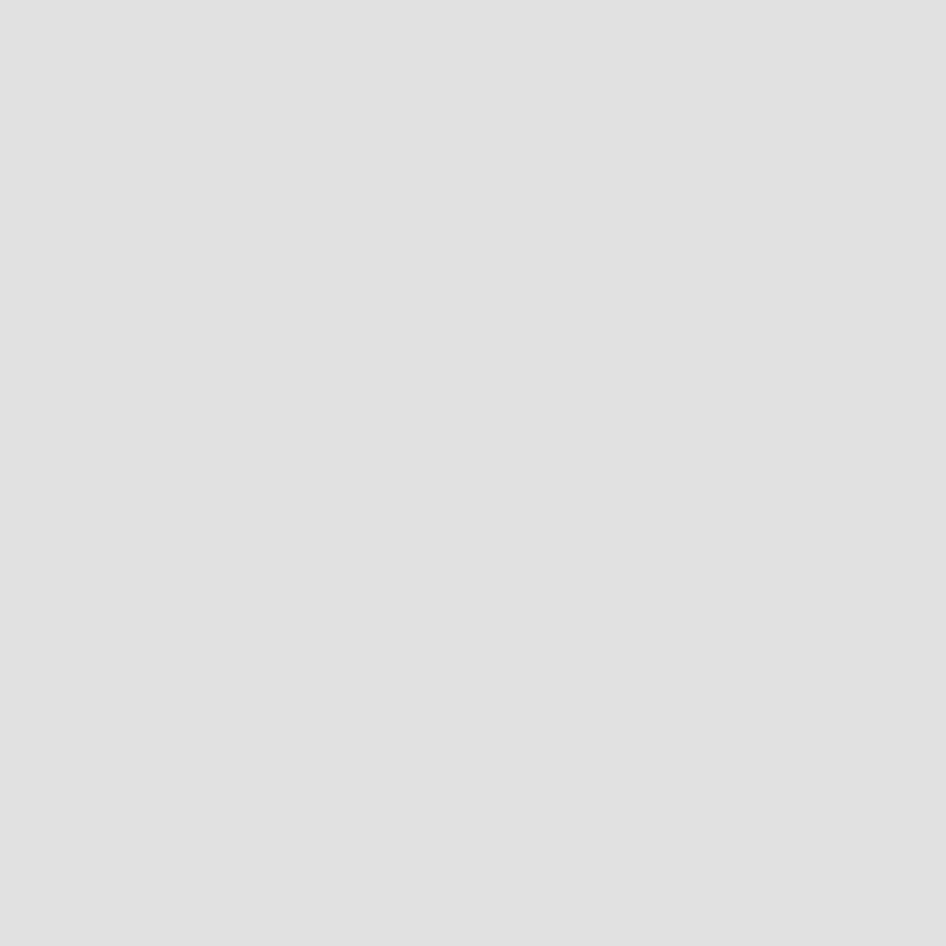
How Label Verification Helps Avoid Costly Fines and Chargebacks Due to Defective Labels
Barry J. Ewell
August 11, 2020
Printing of faulty barcode labels that are not scannable can have a devastating downstream effect on your business. The most common causes of unreadable barcodes include low contrast, quiet zone violations, improper reading position, print or mark inconsistency and damage/distortion. These issues are frequently the result of incorrect printer settings, printhead damage, or wrinkled ribbons. Any of these can make the barcode too dark or too light and/or produce voids on the label.
Readability of a barcode is defined by how well a barcode reader can decode the data in the symbol. While a code may look perfectly fine to the human eye, even simple inconsistences mean loss of readability.
A faulty barcode has a ripple effect on the entire supply chain. At a minimum, barcodes that can’t be scanned will need to be entered by the worker manually. This simple act brings with it the increased risk of data errors and costly mis-shipments or shipment delays – and customer frustration. This can result in slow/stop production and cost companies and their customers thousands of dollars in decreased throughput, manual rework and fines.
Real Costs of Faulty Barcodes
When a customer receives a shipment with unscannable/bad barcodes, customers can and do levy severe consequences on the supplier/shipper. They can include:
- Costly Fines. Having the wrong/damaged barcode on a shipment can cost the shipper fines that can mount very quickly.For example, retailers like Walmart have detailed requirements for on barcode label design/placement. Non-compliance can cost the shipper $5,000 for the second infraction which can double with each infraction.1 Retailers invest heavily in technology to help optimize business efficiency using barcodes. If the supplier does not have the complete information in the barcode, retailer systems can come to a screeching halt.
Certain industries such as automotive, pharmaceutical, and aerospace have compliance regulatory requirements around barcoding and levy fines for non-compliance.
- Chargebacks and Refused Shipments. Unscannable UCC-128 labels and misplaced labels are among the leading causes for chargebacks and refused shipments. Consequences like these can easily cost the supplier up to 10% of their revenue. Such fines are levied to help the retailer recoup their costs associated with re-labeling.For this reason, it is imperative that shippers put in place procedures and equipment that will verify barcode readability on products and shipments before they enter the supply chain. If the shipper can’t verify that the barcode was scannable when it left their facility, they are liable to pay the chargeback fees.
- Manual Entry and Delayed Shipment Fees.For customers who do accept shipments with faulty barcodes, shippers can still be penalized with fees for manual barcode entry and/or late fees for delayed shipments.
- Product Safety. Many industries such as pharmaceutical, medical devices, automotive, and food/beverage use barcodes for tracking and tracing. Barcodes are critical in these industries in cases where there are product recalls. Barcodes improve visibility into:
- Product movement and inventory management to make sure the correct product was shipped to the correct warehouse and/or retailer at the correct time.
- Food safety for consumers by tracking production and expiration dates.
- Providing retailers with the ability to track the product from receiving it through to the sale.
- Business Reputation. How many poor quality/unreadable barcodes will it take before it will affect the reputation of your company? Companies make decisions every day to stop doing business with shippers who repeatedly deliver product/shipments with bad and unscannable barcodes.
How Integrated Barcode Verification Ensures 100% Accuracy, Every Time
Today, technology is changing every aspect of the supply chain. Honeywell has changed the landscape of barcode printing with the introduction of the Honeywell PX940 high-performance industrial printer with integrated label verification.
Developed for companies that are subjected to fines levied for non-compliance to regulatory shipments due to unreadable barcodes, the PX940 series takes industrial printing to a new level of accuracy and simplicity. It provides customers with error-free precision printing, increasing production efficiency and reducing operational costs.
Find out more about the high-performance Honeywell PX940 industrial printer with integrated label verification technology – and how it can help you eliminate the risk and costs of bad labels.
Contact Honeywell Solutions Expert today! Call 1-800-934-3163.
1TB&P: Wal-Mart to impose stiff fines against suppliers around merchandising errors
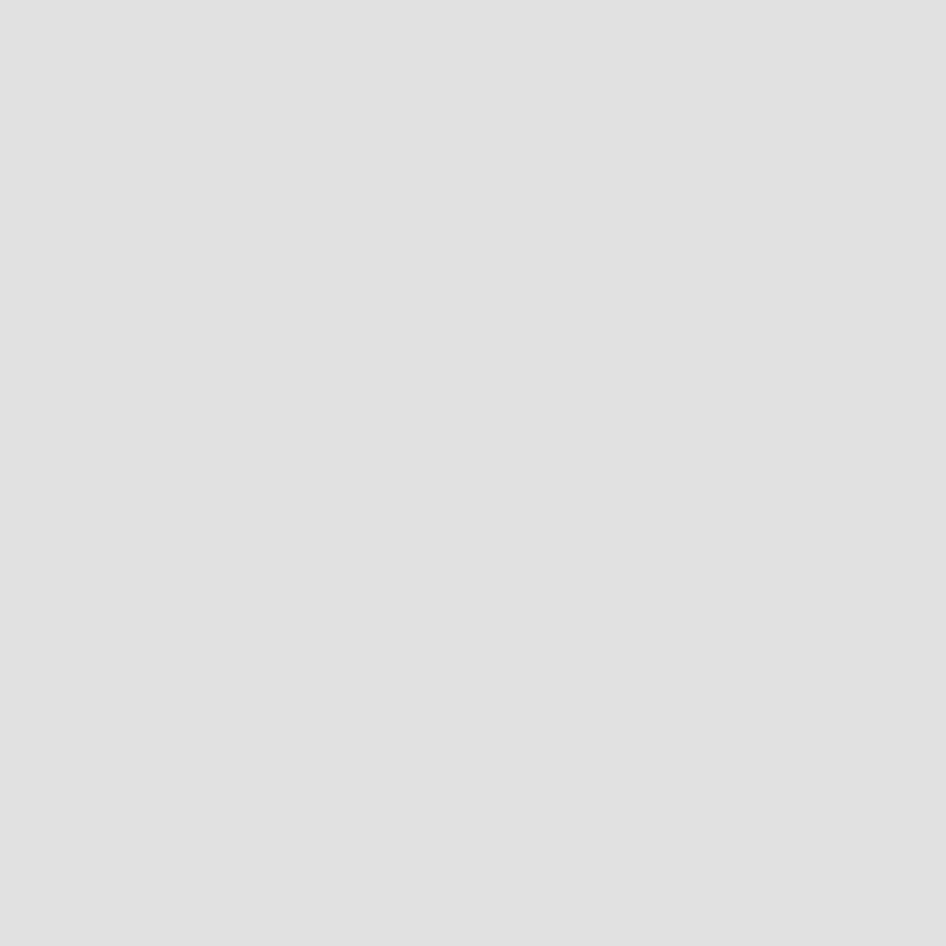
Barry J. Ewell is a Senior Content Marketing Communications Specialist for Honeywell Industrial Automation. He has been researching and writing on supply chain topics since 1991.
Let's Connect!
Sign up to receive exclusive communications from Honeywell including product updates, technical information, new offerings, events and news, surveys, special offers, and related topics via telephone, email, and other forms of electronic communication.
Copyright © 2025 Honeywell International Inc
Maximum File Size
Maximum Files Exceeded
Due to inactivity you will be logged out in 000 seconds.
Maximum File Size
Maximum Files Exceeded
You cannot access this page as this product is not available in your country.