-
Global
-
Africa
-
Asia Pacific
-
Europe
-
Latin America
-
Middle East
-
North America
- |
- Partners
- |
-
Currency:Localize your Content
You can set your preferred currency for this account.
Choose a Currency
Currency- CHOOSE YOUR CURRENCY
Update Currency
Changing Currency will cause your current cart to be deleted. Click OK to proceed.
To Keep your current cart, click CLOSE and then save your cart before changing currency.
-
Select Account
Switching accounts will update the product catalog available to you. When switching accounts, your current cart will not move to the new account you select. Your current cart will be available if you log back into this account again.
Account# Account Name City Zip/Post Code CANCELPROCEEDMy Account
-
Support
- View All Productivity Solutions
- Warranties
- Patents
- Global Locations
- Technical Support
- Discontinued Products
- Quality Program and Environmental Compliance
- Return Material Authorization (RMA)
- Legal Documents
- Product Certification
- Software Downloads
- Cyber Security Notifications
- Case Studies and Success Stories
- View All Sensing Solutions
- Sales Contact Form
- Technical Support
- Certificates
- eCOM Portal
- Distributor Inventory
- Return Material Authorization (Test & Measurement)
- Return Material Authorization (Citytech)
- Return Material Authorization (EnviteC)
- Legal Documents
- Intelligent Life Care
- Return Material Authorization (ILC)
-
Global
-
Africa
-
Asia Pacific
-
Europe
-
Latin America
-
Middle East
-
North America
- |
- Partners
- |
You are browsing the product catalog for
You are viewing the overview and resources for
- News & Events
- Featured stories
- 6 Ways to Improve Warehouse Operations with Voice Technology
6 Ways to Improve Warehouse Operations with Voice Technology
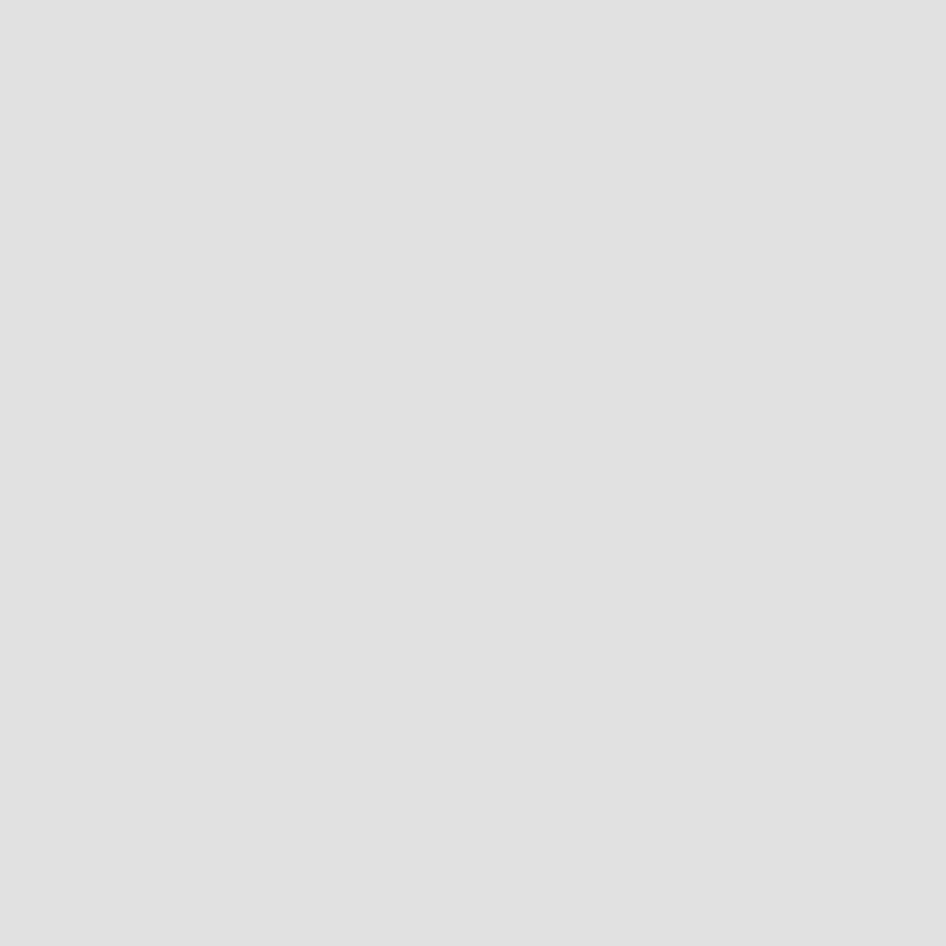
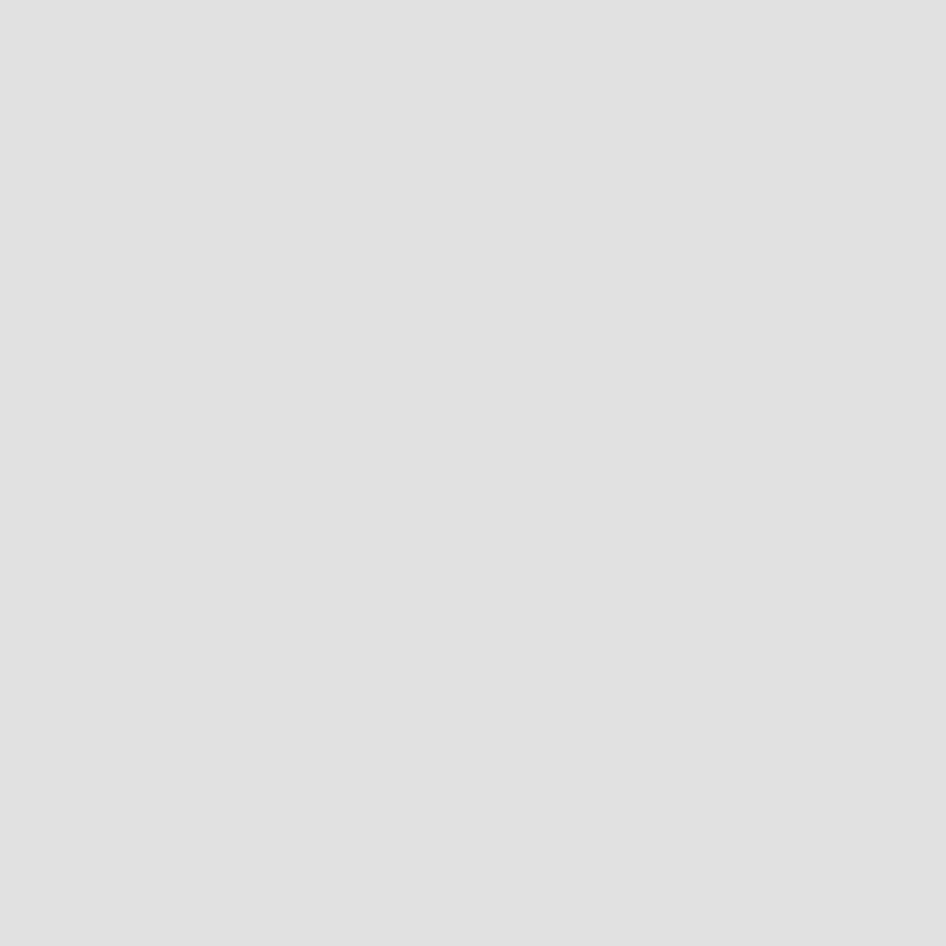
6 Ways to Improve Warehouse Operations with Voice Technology
Barry J. Ewell
March 2, 2021
Like a Swiss Army knife sporting multiple tools in a single package, optimizing warehouse operations by deploying voice technology improves warehouse processes and procedures in six different ways. That’s because voice-guided workflows free up mobile workers’ hands and eyes, allowing them to do their jobs safely and accurately in demanding distribution center (DC) and warehouse operations. Businesses that integrate voice into their basic warehouse operations achieve higher levels of productivity and profitability. Here’s how.
1. Guide Workers With Clear Directions in Their Language
Intuitive, voice-guided instruction cuts new employee training time in half, ensuring these associates begin working at much higher productivity and accuracy levels. Certain voice solutions incorporate speech-recognition capabilities that significantly reduce onboarding time. They also allow existing employees to be quickly cross- trained across a variety of operational functions.
Voice technology engineered to understand dozens of languages enables rapid training of a more diverse workforce, including temporary employees and non-native speakers. Solutions incorporating voice recognition software adapt to workers’ individual speech preferences; this minimizes the need to repeat spoken interactions, saving time and making work more engaging.
2. Seamlessly Integrate Voice with Your Processes
While there are many associate voice technologies with picking, voice-directed workflows can be deployed across multiple warehouse processes and procedures — including receiving, replenishment, shipping and maintenance/repairs. Further, voice software can integrate with a variety of host systems, including:
· Legacy, home-grown systems
· Warehouse execution systems (WES)
· Warehouse management software (WMS) platforms
· Enterprise resource planning (ERP) solutions (SAP S/4HANA in large organizations; SAP Business One or Microsoft Dynamics 365 for medium- and small-sized enterprises)
As directed by the overarching warehouse management system software, the voice system delivers easily understood instructions through a mobile worker’s wearable headset, directing them to the next location and assignment. Upon task completion, the worker speaks a verbal confirmation into the headset microphone. The voice software converts responses into data, then communicates it back to the host system to update inventory records in real time.
3. Collect and Analyze Worker Process Data
In addition to collecting and updating inventory information, certain voice systems incorporate automatic documentation and analytics capabilities. Ideal for optimizing warehouse operations by enhancing mobile workforce productivity, these solutions also verify process compliance.
Whether used alone or with a labor management system (LMS) or business information (BI) visualization tool, data gathered and analyzed via voice technology allows:
· Monitoring of real-time throughput and inventory movement
· Continuous process improvement by identifying activities or personnel in need of additional training
· Predictive analytics for better informed workflow decisions
4. Overcome Noisy and Tough Environments
Not all headsets are created equal; selected hardware must meet the demands of a given application and environment. In addition to reliable “text-to-speech” and “speech-to-text” software functionalities, headsets should include noise-suppression technology that ensures workers can hear commands, even in noisy, challenging conditions. Additional key features include directional microphones that consistently capture and relay a mobile worker’s voice, advanced software that integrates with the host system, and a rugged, wearable mobile device that interfaces with the voice system dependably.
5. Transform Equipment Inspections, Maintenance and Repairs
Maintenance technicians equipped with voice technology no longer have to rely on printed instruction manuals and checklists to complete service, inspection or repair procedures. Instead, with a voice-directed workflow, maintenance personnel are guided step-by-step through the required process, responding with a verbal confirmation upon completion of each task. The system automatically documents each action, ensuring strict compliance with required regulations and standard operating procedures (SOPs).
6. Improve Operations to Achieve Business Goals
Voice technology eliminates paper-based workflows and minimizes steps, thus optimizing warehouse operations and boosting organizational throughput, accuracy, safety and efficiency. With their hands and eyes free, mobile workers outfitted with voice systems can focus solely on their assigned tasks — whether that’s picking or replenishing products, shipping or receiving parcels and pallet loads, maintaining equipment, or learning a new process.
Contact a Honeywell Solutions Expert today! Call 1-800-934-3163.
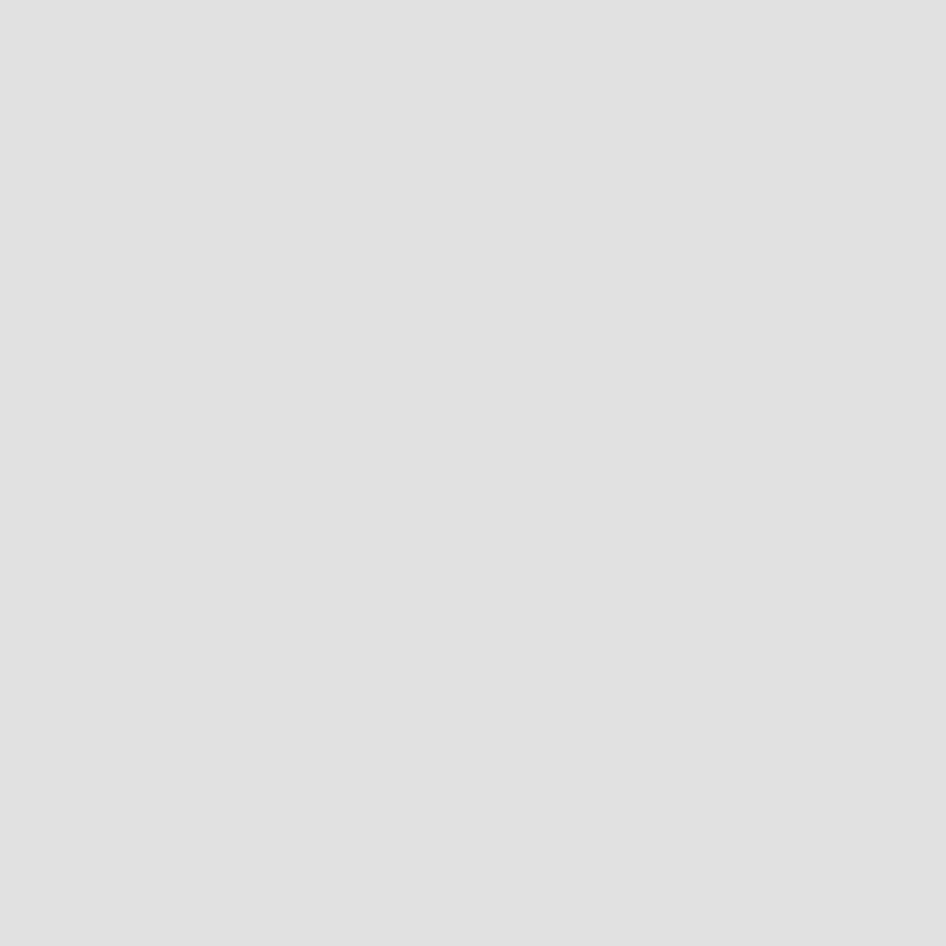
Barry J. Ewell is a Senior Content Marketing Communications Specialist for Honeywell Industrial Automation. He has been researching and writing on supply chain topics since 1991.
Let's Connect!
Sign up to receive exclusive communications from Honeywell including product updates, technical information, new offerings, events and news, surveys, special offers, and related topics via telephone, email, and other forms of electronic communication.
Copyright © 2025 Honeywell International Inc
Maximum File Size
Maximum Files Exceeded
Due to inactivity you will be logged out in 000 seconds.
Maximum File Size
Maximum Files Exceeded
You cannot access this page as this product is not available in your country.