10 Questions Defining the Various DC Picking Workflows
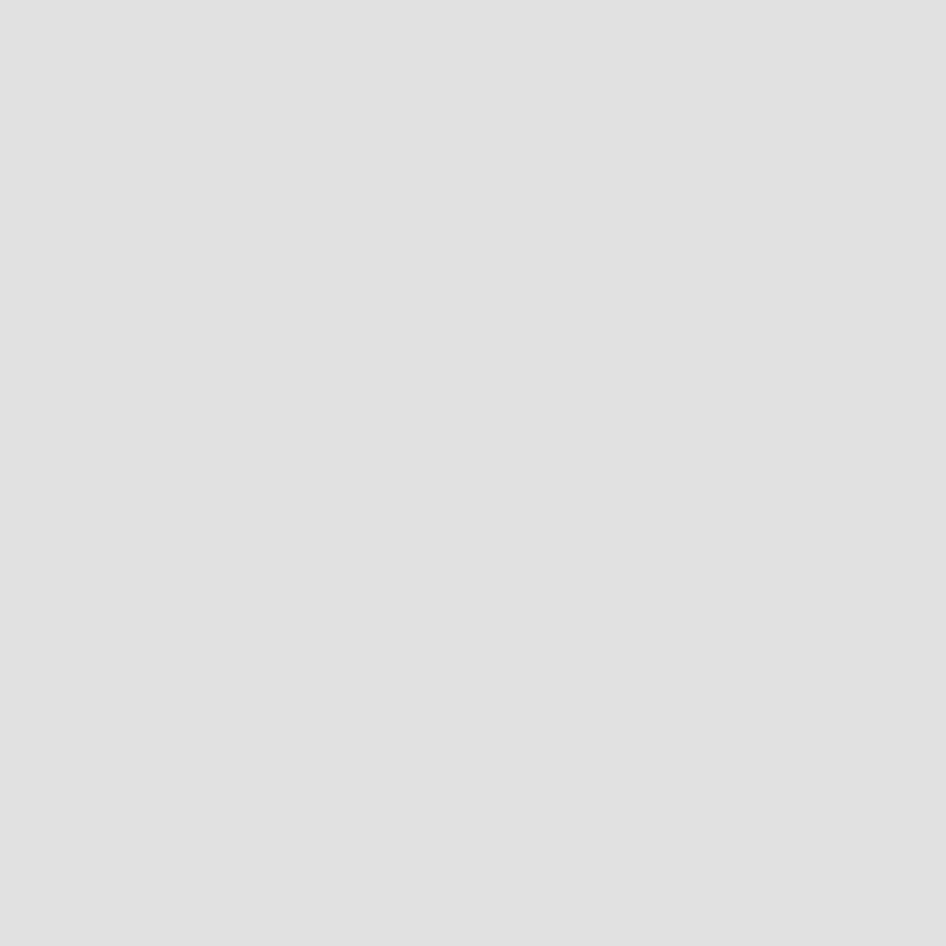
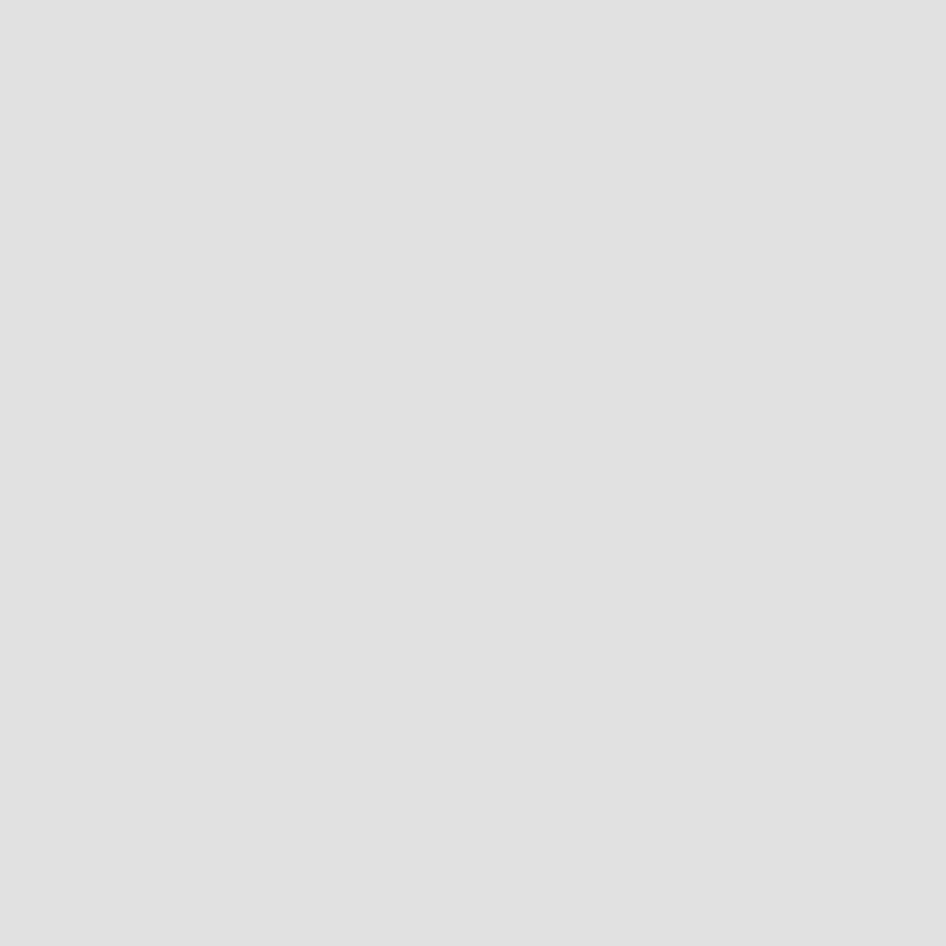
10 Questions Defining the Various DC Picking Workflows
Picking, more formally known as “order selection,” is the process of extracting goods from DC storage locations to fill orders from specific customers. The ability to quickly and accurately pick orders is the most labor-intensive, skill-intensive activity in the DC. The result is that it represents as much as 55%–60% of the typical DC’s operating expense. Because of these issues, picking is clearly the big issue for most operations and has significant impact on customer satisfaction levels. In this article, we will answer common questions about the various types of Picking workflow in the DC.
1. What determines the different types of picking methods and technology solutions?
There are a number of picking methods and technology solutions available. The methods for order picking vary greatly and define the method for order picking.
They include:
- Characteristics of the product being handled
- Total number of transactions
- Total number of orders
- Picks per order
- Quantity per pick
- Total number of SKUs
- Value-added processing activities such as kitting or private labeling
- Handling of piece-pick, case-pick or full-pallet loads
Often a combination of picking methods is needed to handle diverse product and order characteristics.
Some important things to understand and note about DC/warehouse operations are the types of picking methods being utilized. Are they doing full pallets (common in CPG), partial pallets, full cases, broken case and/or piece or each picking (usually single items from within the case pack level)?
Another important consideration is how many temperature zones are there? The three typical temperature zones are Freezer, Cooler (typically refrigerated temperatures for fresh foods) and Dry (ambient). These temperature zones determine the operational workflows. Naturally freezers present challenges to equipment and people and are typically more difficult than dry areas. Cooler and Dry are fairly similar in terms of people/equipment challenges.
2. What are the key objectives in picking?
Key objectives in order picking best practices include increased productivity, reduced cycle time and increased accuracy.
- Productivity. Productivity in order picking is measured by the pick rate. Piece pick operations usually measure the pick rate in pieces picked per hour, while case pick operations measure cases picked per hour. In pallet pick operations, the best measure is pallets picked per hour. Productivity includes the time it takes to physically travel to the item’s physical location, select and handle the item (or the total of the items on a given order) to be loaded on a pallet or packed in a tote or carton, and taken to the final destination location.
- Cycle Time. Cycle time is the amount of time it takes from order entry to shipping the order. Customers’ expectations for service levels vary, but inventory turn metrics, lean and just-in-time inventory practices as well as same-day shipment business models have put greater emphasis on reducing cycle times from days to hours or minutes.
- Accuracy. Regardless of DC operation, accuracy is always a key objective. Virtually every decision made in setting up a DC impacts accuracy. From product location and numbering scheme, slotting, pick face labeling, product labels and even lighting, all these elements of DC design impact picking accuracy. Technologies that aid in picking accuracy include voice picking systems, barcode scanning and imaging, and pick-to-light systems. Other major factors include employee training, strong accuracy tracking and accountability methodologies including audits and pay-for-performance incentives.
3. What is “Basic” order picking?
In the most basic order-picking method, product is slotted in fixed locations. An order selector typically picks one order at a time made up of one to potentially many items following a sequential process to the pick locations until the entire order is picked. The picking sequence is typically determined, optimized and managed by the WMS system and the picker is guided by the WMS process flow. The order picker will normally use some type of pallet jack, pick cart, tote or box into which items selected are put. This basic order picking method works well in operations with smaller total numbers of orders and higher number of picks per order. Operations with low picks per order may find the travel time excessive in this type of methodology.
4. What is batch picking/multi-ordering picking?
In batch picking, multiple orders are grouped into small batches. An order picker will pick all orders within the batch in one pass using a consolidated pick list. Usually the picker will use a multi-tiered picking cart maintaining a separate tote or carton on the cart for each order or pick to conveyor. Batch sizes usually run from 4 to 12 orders per batch depending on the average picks per order in that specific operation. Batch picking systems may use extensive logic programmed to consolidate orders with the same items. In operations with low picks per order, batch picking can greatly reduce travel time by allowing the picker to make additional picks while in the same area.
Picking multiple orders at the same time requires systems and procedures to prevent mixing of orders. In very busy operations, batch picking is often used in conjunction with zone picking and automated material handling equipment. In order to get maximum productivity in batch pick operations, orders must be accumulated in the system until there are enough similar picks to create the batches. This delay in processing may not be acceptable in same-day shipping operations.
5. What is “zone” picking?
Zone picking is the order picking version of the assembly line. In zone picking, the picking area is broken up into individual pick zones. Order pickers are assigned a specific zone, and only pick items within that zone. Orders are moved from one zone to the next as the picking from the previous zone is completed (also known as "pick-and-pass"). Usually, conveyor systems are used with totes, boxes or cartons to move orders from zone to zone. In zone picking it’s important to balance the number of picks from zone to zone, to maintain a consistent flow. Zones are usually sized to accommodate enough picks for one or two order pickers. Creating fast pick areas close to the conveyor is essential to achieving high productivity in zone picking. Zone picking is most effective in large operations with many SKUs, high total numbers of orders and low-to-moderate picks per order.
6. What is “wave” picking?
Wave picking is a variation on zone picking and batch picking, where rather than orders moving from one zone to the next for picking, all zones are picked at the same time and the items are later sorted and consolidated into individual orders/shipments. Wave picking is the quickest method (shortest cycle time) for picking multi-item orders. However, the sorting and consolidation process can be tricky. Operations with high total number of SKUs and moderate to high picks per order may benefit from wave picking. Wave picking may be used to isolate orders by specific carriers, routes or zones.
7. What is “piece” picking?
Piece picking, also known as broken case and Pick/Pack operations, describes systems where individual items, sometimes called “eaches,” are picked. Eaches are usually defined as the lowest-level SKU or smallest individual packaging unit. So an example of a piece pick unit level in a CPG DC operation might be the small, single-serve package of potato chips. The case level would be some multiple of the individual piece packages like 48 pieces in an over-pack unit. Piece pick operations usually have many SKUs (hundreds), smaller quantities per pick and shorter order fulfillment cycle times. E-commerce companies and repair parts distributors are good examples where you might find piece pick operations.
A common piece picking methodology is called “pick-to-tote”. This is especially common for operations that have many SKUs, but generally small amounts in each order. An example of typical operations that would use pick-to-tote applications would be chain drug stores, pharmacies, office products and tobacco retail outlets. Totes provide an extra level of protection for the items being shipped and are reused by these operations. Each tote typically has a unique barcode label or RFID license plate number. At the beginning of the pick process the tote barcode label or RFID tag is scanned to “induct” the tote into the system and automatically matches the order number with the items to be picked for that order to the tote. This serves as a closed-loop system that helps track product throughout the supply chain.
As with the general picking methods, the piece-picking technology and equipment used will also depend on a variety of factors.
Some of the technology and equipment used includes:
- Static Shelving. Common equipment for storage in very low-volume piece pick operations, static shelving is designed with depths from 12 ft to 24 ft. Product is either placed directly on the shelving or in corrugated, plastic or steel parts bins. Static shelving is economical and is a good method where there are few picks per SKU or where parts are very small. Picking technologies favored for static shelving are voice and barcode scanning.
- Flow rack. Flow rack, sometimes called gravity flow rack, is similar to static shelving with the exception that rather than shelves, there are racks tilted at an angle from back (higher) to front (lower) with small rollers on the racking. Product is stocked from the rear of the flow rack and picking is done from the face. Product can be stocked in cases, cartons or small totes or bins. As a carton or tote is emptied, it is removed from the rack and another one will roll into place. Carton flow rack is most useful where there is a very high number of picks per SKU. Picking technologies favored for flow rack are voice and barcode scanning.
- Carousels. Carousels are similar to equipment used by dry cleaners to store and retrieve clothing. They have horizontal racks hanging from them that can be configured to accommodate various size storage bins. Generally an operator will run 2 to 4 carousels at a time, avoiding the need for the operator to wait while one unit is turning. Carousel picking is usually performed in batches, with orders downloaded from the host system to the carousel software. Horizontal carousels are most common in picking operations with a very high number of orders, low to moderate picks per order and low to moderate picks per SKU. Horizontal carousels provide very high pick rates as well as high storage density. Picking technologies favored for carousels are voice and Pick-to-Light (PTL) systems. Barcode scanning with handheld computers can be used, but a wearable scanning solution such as a ring or hand-mounted scanner/imager used in conjunction with voice is more effective and more common.
- Barcode Scanners. Though very useful in increasing accuracy levels, barcode scanners in a fast-paced piece pick operation tend to become cumbersome and can significantly help reduce pick rates. The reason for this is the high amount of product handling required and the ergonomic penalties of having a scanner in the hand while picking. Scanners are better suited to case pick, pallet load, put-away and order checking operations and in selected picking situations where the actual speed required in the picking function is mitigated to some degree with travel times
- Voice-Directed Picking. Voice technology is very effective in both productivity and accuracy across all picking applications. Voice picking is unique in that it combines the speed of listening and talking without having to look at, read and interpret instructions on a piece of paper or display, working with your head up with visual contact on the point of work and having the hands free to accommodate all forms of ergonomic product handling. In short, voice has been proven in thousands of installations and varied applications to be the most productive and also most accurate of the picking processes. Some customers may have high-density picking operations using PTL. They often cite their preference for PTL saying that it is faster. This is not the point to address with PTL users when comparing voice. In fact, most of the older PTL systems have a limit as to how many people can work in one zone of the lights. This is a limiter on the total throughput of the system. With voice one can put as many people into a pick zone as can fit, which usually greatly exceeds the number of pickers a PTL system can support.
- Pick-to-Light (PTL). Pick-to light systems consist of a complex system of lights and sometimes LED displays mounted on the front-facing rack edge for each pick location. The system uses software to light the next pick and display the quantity to pick. The picker goes to the location, presses the off button on the light and picks the quantity shown on the display. Since a significant amount of hardware is required for each pick location, PTL systems are effectively static, inflexible systems, more costly to implement and maintain, and suffer from switch and light failures. They are almost only cost-justifiable where very high pick rates per a limited number of SKUs can be located in a densely packed, small area. Also, in batch picking, put-to-lights for placing items into the totes on a pick cart can be effective.
8. What is “case” picking?
Case picking operations tend to have less diversity in product characteristics than piece picking operations, with fewer SKUs and higher picks per SKU.
- Basic Case Picking. This is the most common method for case picking operations. Rather than product stored on static shelving, case pick operations have the product stored in slots in pallet racks or in bulk in fixed or temporary floor locations. The simplest picking method is to use a motorized pallet jack and pick cases out of slots and bulk floor locations. Voice picking and barcode scanning are the preferred technologies for productivity and accuracy.
- Zone/Batch/Wave Picking. All of these picking types can be used for case picking operations. This is typically done in pick-to-belt with automated sortation system configurations where cases are automatically transported, run through a barcode reader/diverter system and directed down conveyor spurs to pallet build locations. These pallet build areas are usually terminated near outbound dock doors for ease of loading. The process of building the pallets from the cases diverted down the spurs is also known as “line-loading.” Voice picking and barcode scanning are both used effectively in these scenarios. PTL is sometimes used, but less frequently.
Technologies commonly used in case picking include:
- Paper Lists. Believe it or not, there are many companies, from small mom-and-pop operations to Fortune 1000 companies, that still use paper pick lists or labels. Paper lists or the use of small adhesive-backed label sheets with item information printed on them can be surprisingly fast when used by a highly skilled picker. The downfall of paper systems is accuracy. This method tends to be the least accurate of all methods and is extremely difficult and costly to do real-time reconciliation for incomplete or short orders.
- Pallet Racks. Pallet racks are the most common storage system for case pick operations.
- Barcode Scanners. Barcode scanners are frequently used in case pick operations. Since the time to physically pick the product is higher in case pick operations, the time spent scanning tends to have less impact on productivity and gains in accuracy are substantial over paper-based processes and can outweigh a reduction in productivity.
- Flow Racks. Although flow rack rarely applies to case pick operations, in some operations pallet-flow rack or push-back rack can be useful.
- Voice-Directed Picking. Voice technology is very effective for case picking as product handling productivity and accuracy are enhanced with both hands free to lift typically heavier cases in a safe and ergonomic way. Also, having the picker’s head up at all times is a strong safety benefit particularly with motorized equipment like pallet jacks.
- Automated Conveyor and Sortation Systems. If using zone or wave picking, automated conveyor and sortation systems will likely be a part of the system. In case picking, you may use standard conveyors to transport individual cases or unit-load conveyors to transport pallets.
- Mobile Material Handling Equipment. As previously mentioned, motorized pallet jacks and man-up order pickers or turret trucks are the vehicles of choice for case pick operations.
9. What is “full-pallet” picking?
Full pallet picking is also known as unit-load picking. The systematic methods for full pallet picking are much simpler than either piece pick or case pick; however, the choices in storage equipment, storage configurations and types of lift trucks used are many and varied.
- Basic Pallet Picking. This is the most common method for full pallet picking. Orders are picked one at a time. The order picker will use some type of lift truck, retrieve the pallet load and stage it in a shipping area in a staging lane designated for that order, or just pick and load directly into an outbound trailer or container.
- Zone and Wave Picking. Pick zones can be used in wave picking for pallet picking operations. The storage area is broken into zones to eliminate multiple lift truck operators from picking in the same aisle. The lift truck operator may pick the pallet and deliver it directly to the designated staging lane or place it on a unit-load conveyor that will deliver it to the sorting/staging area.
- Tasking Interleaving. Task interleaving is a method used to combine picking (usually pallet picking) with other forklift applications like replenishment and put-away. Warehouse Management Systems (WMS) use logic to direct a lift truck operator to put away a pallet or conduct a replenishment of a pallet on a high rack location to a slot (floor location) enroute to the next pick or put-away. Often an inventory count or cycle-count can be interleaved with put-away, replenishment and picking applications. Task interleaving greatly helps reduce travel and helps to optimize labor and equipment flexibility and task response times.
Technologies commonly used in pallet picking include:
- Pallet Rack. There are numerous pallet rack configurations used in full pallet operations, from standard back-to-back single pallet depth configurations to double-deep rack, push-back rack, drive-in/drive-thru rack and flow rack.
- Automatic Storage & Retrieval Systems (ASRS). Unit-load ASRS, when combined with unit-load conveyors and sortation systems, can provide fully automatic pallet picking operations. And the ability to store product in racking up to 100 feet high gives excellent storage density. ASRS systems are used effectively in full pallet operations to defray labor costs. While extremely costly and complex mechanically, ASRS systems can be economical over longer payback periods.
- Automated Conveyor and Sortation Systems. Automated conveyor and sortation systems can be combined with ASRS units or used in conjunction with manual picking with lift trucks in zone/wave picking systems. Either the ASRS or the lift truck operator delivers the pallet load to the conveyor. The conveyor system then delivers the pallet to the shipping area, where it is either manually sorted by lift trucks into the designated staging lane, or a sortation system automatically sorts into a staging lane. Staging lanes can be equipped with automated or gravity-fed unit-load conveyors.
- Lift Trucks. The lift trucks used for pallet picking will depend upon the storage configuration.
10. What are the Honeywell solutions for the DC/warehouse picking workflows?
Honeywell is uniquely equipped to help you achieve logistical and operational excellence through smart end-to-end solutions. From identifying pain points to transforming distribution centers, our cutting-edge solutions when combined maximize operational potential and help optimize outcomes. They include the following:
- Voice. Voice picking is hands-free and eyes-free, so it helps increase accuracy and productivity through focused work activity. Voice can be deployed in any type of pick operation to include pallet picking, case picking and each picking to tote or carton. There are additional benefits with voice to include safety and ergonomic gains, training time reduction (very relevant for seasonal picking), employee satisfaction and the resulting retention and language barrier removal.
Honeywell’s voice-guided solutions have proven to help increase productivity by up to 35% and help increase accuracy to 99.99%+ in a variety of tasks throughout the warehouse. For example, in picking processes where workers follow a series of instructions for specific pick locations, products and quantities, these tools provide needed guidance and verification at every step. Voice is available in over 35 languages and has been proven to dramatically help reduce training and onboarding time, especially in peak seasons with highly transient workforces. - Wearable solutions. There are instances where scanning additional critical data is required and these are opportunities to deploy wearable scanners to be used with voice picking. A growing number of companies have turned to hands-free computing solutions to streamline operations and improve productivity. The Honeywell Mini Mobile Wearable solution provides a hands-free solution that helps provide increases in productivity and improved ergonomics over handheld devices.
- Barcode Scanning. Though very useful in increasing accuracy levels, barcode scanners in a fast-paced piece pick operation tend to become cumbersome and can significantly help reduce pick rates. The reason for this is the high amount of product handling required and the ergonomic penalties of having a scanner in the hand while picking. Scanners are better suited to case pick, pallet load, put-away and order checking operations and in selected picking situations where the actual speed required in the picking function is mitigated to some degree with travel times.
- Mobile computers that provide 1D and 2D imaging. Mobile computers are also used in pick operations and are best suited for low-volume, basic operating environments. If the workforce is expected to perform multiple operational processes such as picking, receiving, loading, etc. during a single shift, then it may be advantageous to equip them with voice-enabled multi-function (scan/key/voice) mobile computers so that a single device with a single supporting infrastructure (batteries, chargers, etc.) can be utilized.
Utilizing mobile computers with imagers to scan product and label information, as well as capture additional data, is more productive (~25%) and accurate (~50%) than paper/manual-based methods. It helps ensure quality control and vendor compliance, and quantity received information is captured in real-time. - Fixed and Mobile Printing and Media. As part of the picking process, destination labels are usually required to be applied to the finished container (pallet, tote, etc.). This can be accomplished by placing fixed printers throughout the facility so that the picker can retrieve them either before or after completing their pick task. These fixed printer stations can, however, become choke points in high-volume operations. Mobile printers can also be deployed, especially in operations such as Convenience and Drugstore DCs that require a shelf or pricing label be applied to each item picked, or in each picking where tote or carton labels are required.
- Automation. The use of automation and/or robotics is becoming increasingly relevant in DC operations. These technologies are currently typically deployed in very high-volume operations where the product being handled is very similar or standard in nature. If you are doing zone or wave picking, automated conveyor and sortation systems will likely be a part of the system. In case picking, you may see standard conveyors to transport individual cases or unit-load conveyors to transport pallets. This operation is often referred to as “pick-to-belt”.
- Automated Storage and Retrieval Systems (ASRS). When combined with unit-load conveyors and sortation systems, can provide fully automatic pallet-picking operations, and the ability to store product in racking up to 100 feet high gives excellent storage density. ASRS systems are used effectively in full pallet operations to defray labor costs. While extremely costly and complex mechanically, ASRS systems can be economical over longer payback periods.
- Motorized equipment. There is also an increase in the use of motorized equipment that allows the workers to remain in their pick zones and help reduces the travel time associated with conventional picking. Some of these processes involve the movement of pallets to each zone by motorized equipment and the worker will pick items from their zone to the pallet that then moves to the next zone. The use of voice technology for picking the items in the zone is a great complement to this technology. In some instances, the motorized equipment will arrive with a new empty container while the full container will be transported to the dock by motorized equipment.
At Honeywell, we have extensive experience in successfully solving complex problems for a variety of e-commerce and omnichannel businesses. We’re committed to solving your DC accuracy challenges through relentless innovation and a desire to deliver best-fit solutions. We provide access to the actionable insights and information you need to transform your business.
Our expert assessment teams will partner with you to understand your unique business requirements and identify where opportunities exist to optimize your workflows and increase efficiencies within today’s competitive retail climate.
Contact a Honeywell Solutions Expert today! Call 1-800-934-3163.