-
Global
-
Africa
-
Asia Pacific
-
Europe
-
Latin America
-
Middle East
-
North America
- |
- Partners
- |
-
Currency:Localize your Content
You can set your preferred currency for this account.
Choose a Currency
Currency- CHOOSE YOUR CURRENCY
Update Currency
Changing Currency will cause your current cart to be deleted. Click OK to proceed.
To Keep your current cart, click CLOSE and then save your cart before changing currency.
-
Select Account
Switching accounts will update the product catalog available to you. When switching accounts, your current cart will not move to the new account you select. Your current cart will be available if you log back into this account again.
Account# Account Name City Zip/Post Code CANCELPROCEEDMy Account
-
Support
- View All Productivity Solutions
- Warranties
- Patents
- Global Locations
- Technical Support
- Discontinued Products
- Quality Program and Environmental Compliance
- Return Material Authorization (RMA)
- Legal Documents
- Product Certification
- Software Downloads
- Cyber Security Notifications
- Case Studies and Success Stories
- View All Sensing Solutions
- Sales Contact Form
- Technical Support
- Certificates
- eCOM Portal
- Distributor Inventory
- Return Material Authorization (Test & Measurement)
- Return Material Authorization (Citytech)
- Return Material Authorization (EnviteC)
- Legal Documents
- Intelligent Life Care
- Return Material Authorization (ILC)
-
Global
-
Africa
-
Asia Pacific
-
Europe
-
Latin America
-
Middle East
-
North America
- |
- Partners
- |
You are browsing the product catalog for
You are viewing the overview and resources for
- News & Events
- Featured stories
- Personal Protective Equipment
- Electrical Safety Training-Enough to Prevent Arc Flash Injuries?
Electrical Safety Training-Enough to Prevent Arc Flash Injuries?
Electrical Safety Training-Enough to Prevent Arc Flash Injuries?
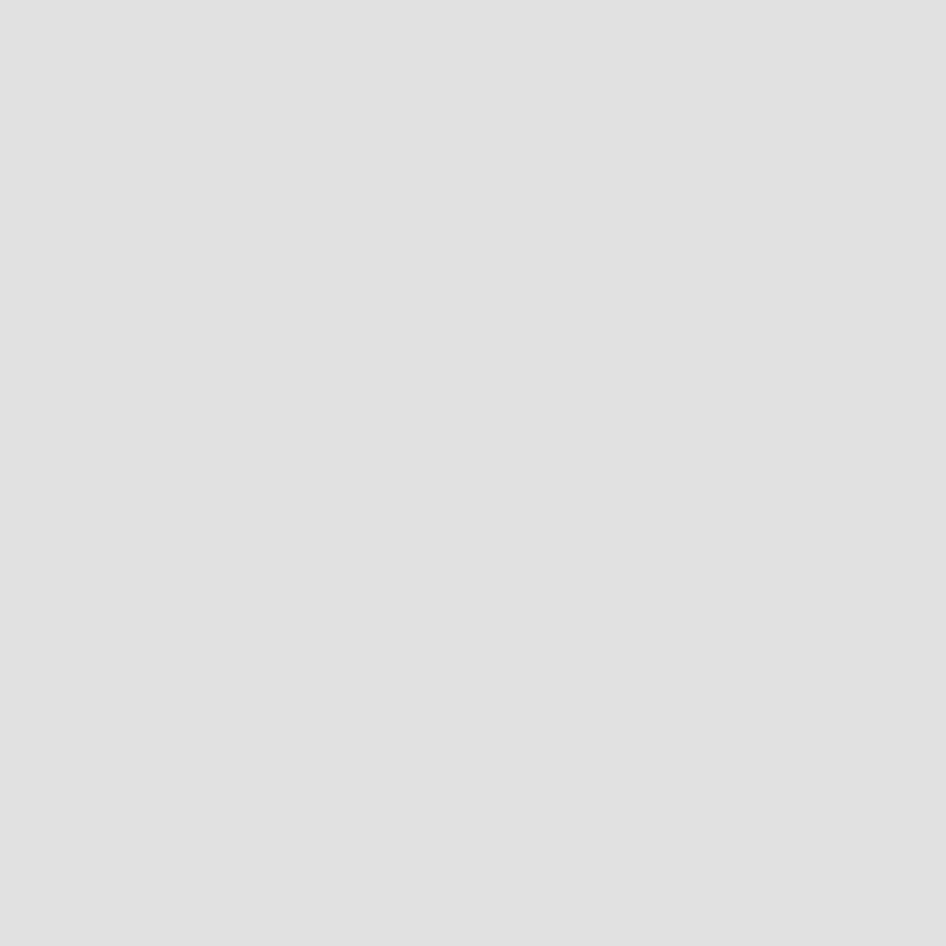
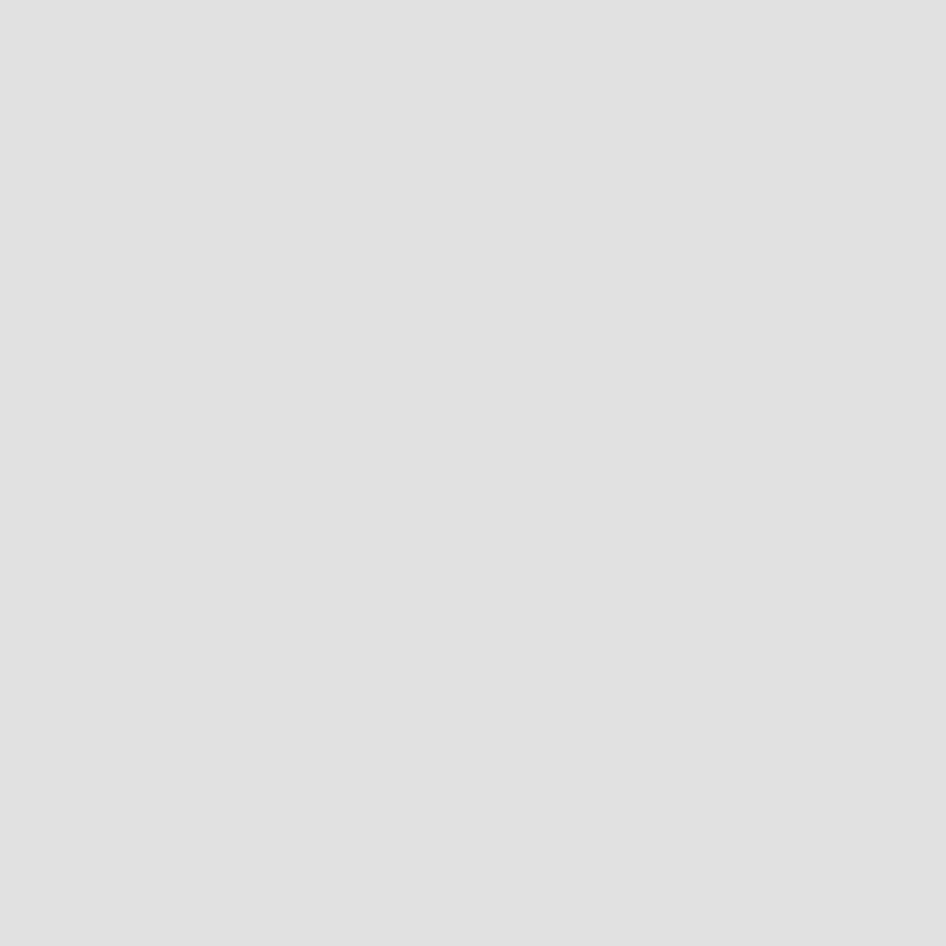
Alexandra Serban
May 29, 2019
Electricity, what an invention, right? As grateful as we may be for its discovery, we’re also in awe of its powerful destructive ability.
In 2017, exposure to electric current was the sixth most common type of workplace fatality.
Electric shock and burns from contact with live parts are an all-too-common source of injury for anyone whose job involves designing, reviewing or installing electrical systems, including safety managers and inspectors.
And despite popular misconception that arc flash incidents are rare, each year, 2,000 workers are admitted to burn centers for treatment of severe arc flash burns. These fraction-of-a-second fireballs can cause severe damage, including potential blindness or deafness and other hidden deadly injuries such as internal bleeding.
The root cause? Unsafe human procedures – especially mishandling or inadvertent contact with energized equipment and tools. Therefore, educating employees facing a high risk of electrical accident on recognizing the dangers is paramount when it comes to preserving people’s physical integrity.
What to teach workers
Released in September 2017, the NFPA 70E, is the accepted standard for safe electrical work conditions. It is a voluntary national consensus standard, meaning it is not enforced by OSHA, yet OSHA may refer to it when it comes to violations of certain OSHA standards.
It mandates that, before any training program, a hazard/risk evaluation procedure should be performed. Its role is to assess whether an electrical safe work condition can be established through lockout/tagout (LOTO) procedures, energy control procedures and temporary protective grounding equipment. De-energizing and lockout/tagout procedures are the easiest first steps in preventing the release of unexpected hazardous energy and all employees must be well-versed with them.
If de-energizing is not possible, employees need to be trained to work around electrical hazards, as part of an overall Electrical Safety Program.
Employee electrical safety training is split in two: for “qualified” and for unqualified” workers. Each category of workers should be able to recognize electrical hazards and what type of tasks they can perform, as a result of this type of training.
As defined in the 2015 NFPA 70E, a qualified person is“…one who has demonstrated skill and knowledge related to the construction and operation of electrical equipment and installations and has received safety training to identify and avoid the hazards involved.”
Qualified workers are expected to master the following:
1. How to differentiate energized from non-energized parts
2. The voltage of exposed electrical conductors
3. Safe practices to prevent electrical exposure
4. Selecting the proper PPE for the job
5. Work practices related to equipment
6. Emergency procedures and first aid practices
7. How to perform hazard/risk assessment
8. How to establish flash protection boundaries
They are also required to demonstrate skills and knowledge for a specific electrical task.
On the other hand, “unqualified” workers who don’t have direct contact with exposed electrical equipment will only receive training related to the nature of electricity and sources of injury.
Additionally, OSHA requires “qualified” employees be taught the skills and techniques to identify exposed live parts from others, as well as how to determine their nominal voltage and clearance distance. According to OSHA’s 29 CFR 1910.335(a)(1)(i), employee training should also include information on PPE use and selection.
Why is this important?
In an overwhelming number of scenarios, arc flash injuries could have been prevented by simply turning off the power. Furthermore, due to the high-risk and unpredictable nature of their activity, employees must understand the serious consequences of not following basic safety procedures.
The power of know-how and PPE
Fortunately, there are a lot of guiding materials and procedures to reduce electrical risk. Processes such as issuing hot work permits are one solution. Getting a hot work permit when using spark-producing power tools will reduce the risk of starting a fire in area with flammable or combustible materials. Establishing a preventative maintenance program for electrical materials is also helpful in making sure electrical assets are always safe and reliable.
Arc-flash PPE comes in last on the list, but remains critical in any arc flash safety strategy. Apart from defining the extraordinary circumstances for “working live”, and setting strict electrical safety limits on voltage exposures, NFPA 70E also guides workers in their PPE selection.
What PPE is required for arc flash?
How do we ensure our PPE matches high-voltage emergencies?
According to NFPA 70E-2018 , arc flash protective equipment categorizes PPE based on its ability to absorb the incident’s thermal energy level. This usually takes the form of a short and very hot blast, so, the fabrics used in arc-flash PPE should be flame-resistant.
There are four arc-flash PPE categories – each reflects a specific amount of energy expressed in calories per centimeter squared. (between 1.2 cal/cm2 - 12 cal/cm2 and greater than 12 cal/cm2).
Source: osha.gov
However, the power of any PPE lies in its constant and correct use. You need to equip employees with the appropriate tools and protections, but also with the knowledge and desire to use them properly.
This is where comprehensive electrical safety training plays a monumentally important role.
Let's Connect!
Sign up to receive exclusive communications from Honeywell including product updates, technical information, new offerings, events and news, surveys, special offers, and related topics via telephone, email, and other forms of electronic communication.
Copyright © 2025 Honeywell International Inc
Maximum File Size
Maximum Files Exceeded
Due to inactivity you will be logged out in 000 seconds.
Maximum File Size
Maximum Files Exceeded
You cannot access this page as this product is not available in your country.