-
Global
-
Africa
-
Asia Pacific
-
Europe
-
Latin America
-
Middle East
-
North America
- |
- Partners
- |
-
Currency:Localize your Content
You can set your preferred currency for this account.
Choose a Currency
Currency- CHOOSE YOUR CURRENCY
Update Currency
Changing Currency will cause your current cart to be deleted. Click OK to proceed.
To Keep your current cart, click CLOSE and then save your cart before changing currency.
-
Select Account
Switching accounts will update the product catalog available to you. When switching accounts, your current cart will not move to the new account you select. Your current cart will be available if you log back into this account again.
Account# Account Name City Zip/Post Code CANCELPROCEEDMy Account
-
Support
- View All Productivity Solutions
- Warranties
- Patents
- Global Locations
- Technical Support
- Discontinued Products
- Quality Program and Environmental Compliance
- Return Material Authorization (RMA)
- Legal Documents
- Product Certification
- Software Downloads
- Cyber Security Notifications
- Case Studies and Success Stories
-
Global
-
Africa
-
Asia Pacific
-
Europe
-
Latin America
-
Middle East
-
North America
- |
- Partners
- |
You are browsing the product catalog for
You are viewing the overview and resources for
- News & Events
- Featured stories
- Resources and Ideas to Inspire Higher Efficiency Levels
Resources and Ideas to Inspire Higher Efficiency Levels
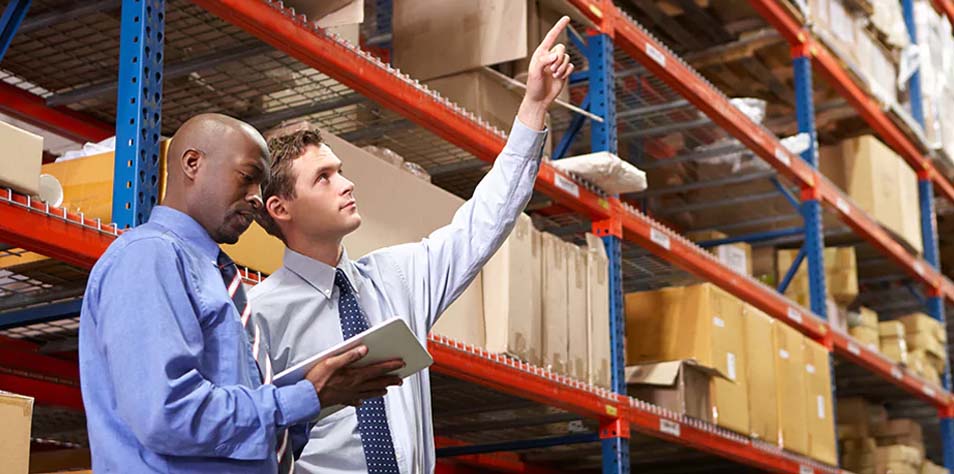
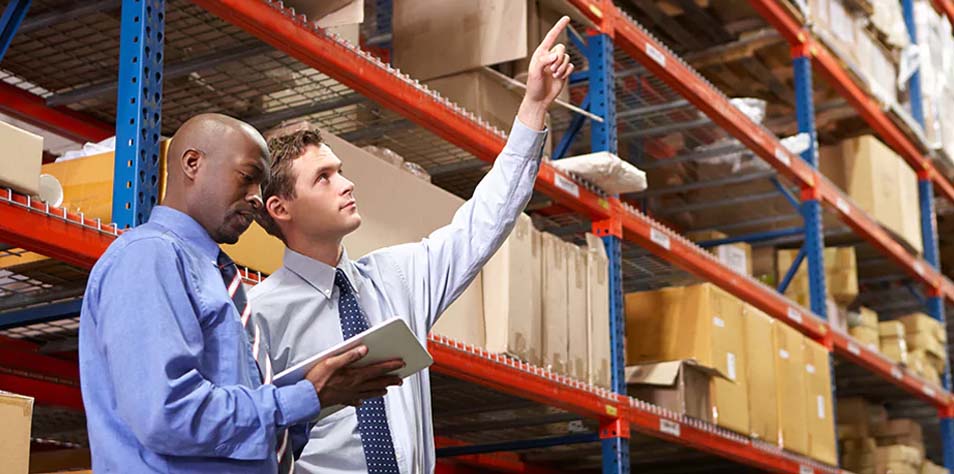
Resources and Ideas to Inspire Higher Efficiency Levels
Doug Fukushima
September 30, 2020
This post is part 7 in a series of 10 different approaches to addressing the common challenges faced by distribution centers (DCs) across a broad range of industries without investing in automation.
The sixth blog in this 10-part series exploring ways to enhance operational efficiency without investing in automation offered a selection of solutions to address the little impediments that might be big productivity barriers. In this post, we’re taking a look at different idea sources for measures that can inspire greater efficiency.
Step 7: Raise the Bar
Today you noted — again — that the metrics in a specific area or department haven’t hit their target. It’s time to head out onto the floor to observe and inquire. Watch the associates performing tasks, then ask them why they’re doing what they do. Most of the time the response will be: “Because we’ve always done it this way.”
That’s your cue to re-evaluate the status quo. As part of the investigation, don’t neglect to ask associates for feedback and ideas. As the people who do the work every day, they are a tremendous (and often overlooked) resource for ideas about ways to work smarter.
Other efficiency improvement ideas can come from industry sources, such as those offered by the many associations and conventions focused on the warehousing, supply chain and materials handling fields. Equipment suppliers, distributors and trade publications also regularly share insights into the steps other operations have taken to boost productivity.
Finally, consider incentivizing a little friendly competition among associates to seek out and suggest ideas for streamlining processes with specific rewards, or tie productivity to performance-based pay raises or bonuses. Posting an individual team’s accuracy and throughput statistics can inspire greater participation. Benchmarking employee performance by individual, team, shift, department or other criteria with labor management systems (LMS) can also help identify opportunities for better efficiency and areas that would benefit from additional training.
To learn more about the other nine steps, download the latest Honeywell Intelligrated white paper, 10 Steps to Improve Operational Efficiency: Addressing Common Order Fulfillment Challenges Without Investing in Automation. Stay tuned for the eighth step in this series: “Conduct Process Reviews.”
To subscribe to our blog and receive exclusive communications and updates from Honeywell Intelligrated, click here.
Let's Connect!
Sign up to receive exclusive communications from Honeywell including product updates, technical information, new offerings, events and news, surveys, special offers, and related topics via telephone, email, and other forms of electronic communication.
Copyright © 2025 Honeywell International Inc
Maximum File Size
Maximum Files Exceeded
Due to inactivity you will be logged out in 000 seconds.
Maximum File Size
Maximum Files Exceeded
You cannot access this page as this product is not available in your country.