-
Global
-
Africa
-
Asia Pacific
-
Europe
-
Latin America
-
Middle East
-
North America
- |
- Partners
- |
-
Currency:Localize your Content
You can set your preferred currency for this account.
Choose a Currency
Currency- CHOOSE YOUR CURRENCY
Update Currency
Changing Currency will cause your current cart to be deleted. Click OK to proceed.
To Keep your current cart, click CLOSE and then save your cart before changing currency.
-
Select Account
Switching accounts will update the product catalog available to you. When switching accounts, your current cart will not move to the new account you select. Your current cart will be available if you log back into this account again.
Account# Account Name City Zip/Post Code CANCELPROCEEDMy Account
-
Support
- View All Productivity Solutions
- Warranties
- Patents
- Global Locations
- Technical Support
- Discontinued Products
- Quality Program and Environmental Compliance
- Return Material Authorization (RMA)
- Legal Documents
- Product Certification
- Software Downloads
- Cyber Security Notifications
- Case Studies and Success Stories
- View All Sensing Solutions
- Sales Contact Form
- Technical Support
- Certificates
- eCOM Portal
- Distributor Inventory
- Return Material Authorization (Test & Measurement)
- Return Material Authorization (Citytech)
- Return Material Authorization (EnviteC)
- Legal Documents
- Intelligent Life Care
- Return Material Authorization (ILC)
-
Global
-
Africa
-
Asia Pacific
-
Europe
-
Latin America
-
Middle East
-
North America
- |
- Partners
- |
You are browsing the product catalog for
You are viewing the overview and resources for
- News & Events
- Featured stories
- Market Shifts Drive Demand for Automated Sortation
Market Shifts Drive Demand for Automated Sortation
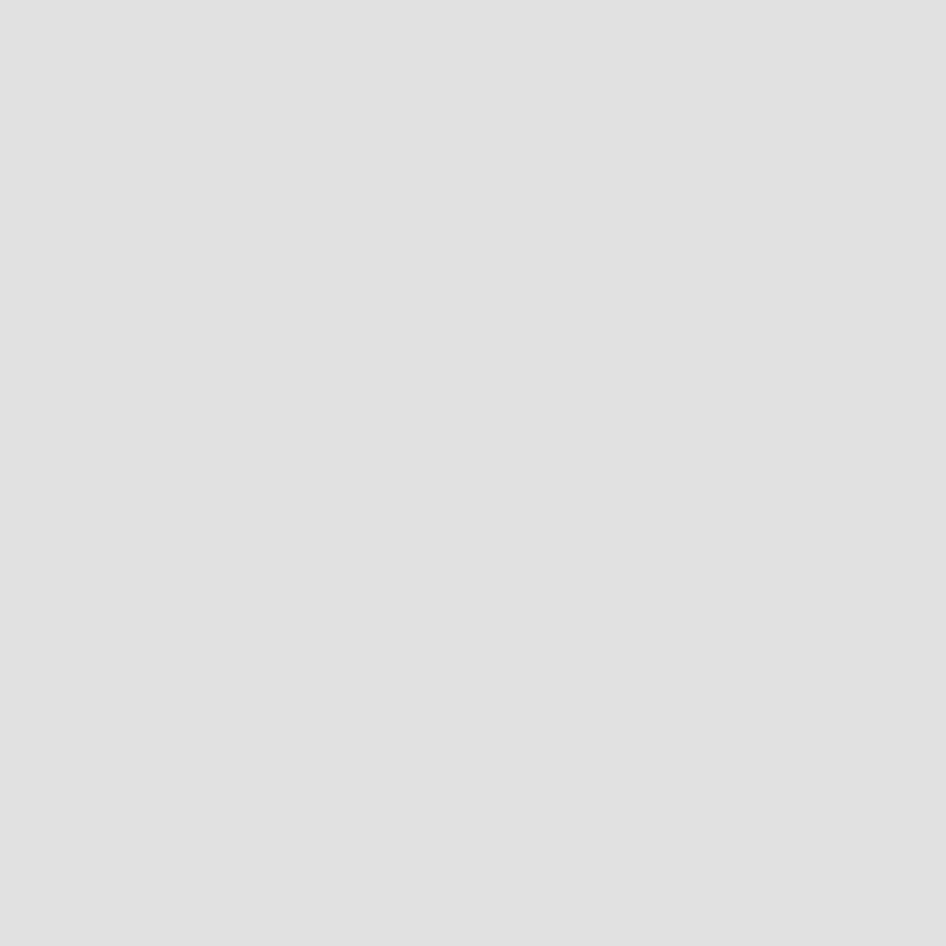
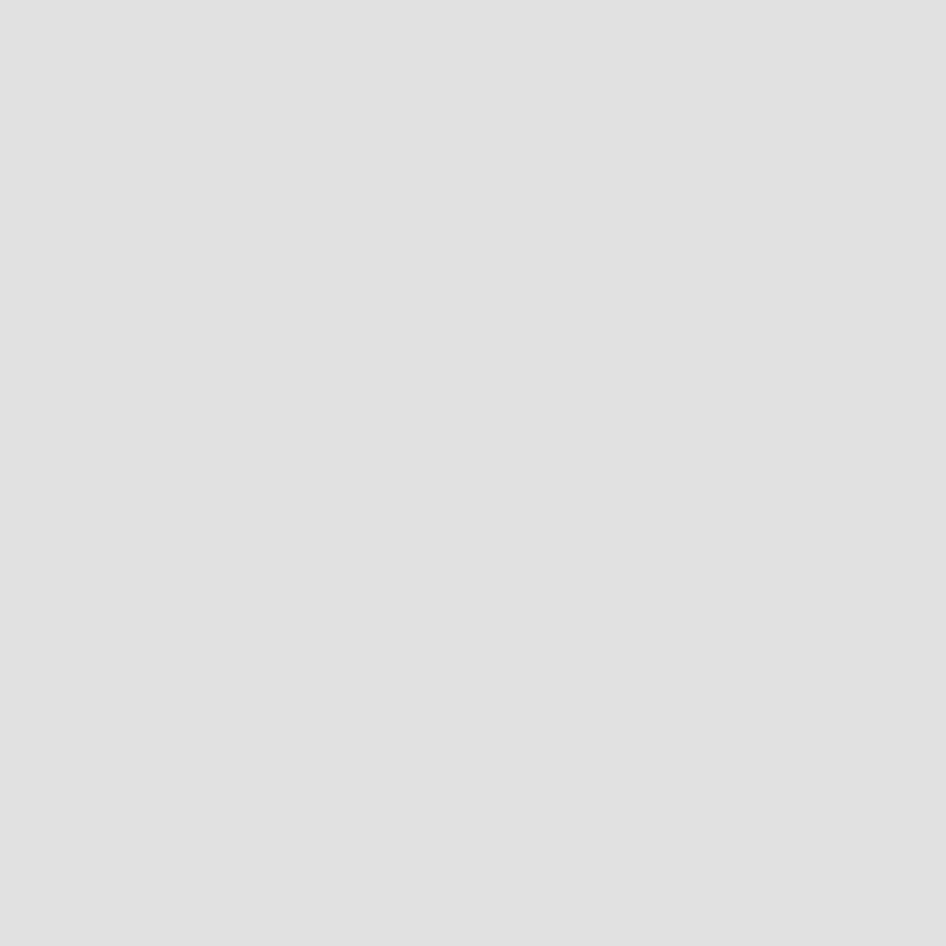
Market Shifts Drive Demand for Automated Sortation
This blog is the first in a series of three for DCs needing to expand sortation capacity to keep up with the growing demands of e-commerce.
Not long ago, brick-and-mortar stores dominated the retail landscape, attracting flocks of shoppers seeking everything from apparel and cosmetics to electronics and hardware. Within this environment, DCs typically sorted a case just once.
However, in today’s e-commerce world defined by individual, direct-to-consumer orders, this sortation burden can multiply into more than 100 sorts per case. As a result, the need to sort quickly and accurately has dramatically increased market demand for automated sortation technologies.
Traditional supply chain process
The journey of products from warehouses, through the supply chain, and ultimately to consumers at traditional storefronts used to be a fairly straightforward process. For example:
- A retail store running low on staplers places a replenishment order with the corporate DC.
- The DC ships a full case of staplers to a retail store.
- Store personnel put the staplers on a shelf.
- A customer arrives at the store, walks to the appropriate aisle, and selects a stapler from the shelf.
- The customer purchases the item and departs with it.
E-commerce is changing the game
Today, the shopping process a customer used to perform at retail stores — walking the aisles, selecting items, and getting them home — now falls to the supply chain. This also means a significant increase in the number of handling processes (including automated sorts) required at the distribution center. Instead of shipping an entire case to a retail store, the DC must ship single units individually to each consumer. This new process takes place in the following steps:
- An order for a stapler (likely one of multiple brands, styles, colors and options) is received by an online retailer.
- An associate at the DC picks the stapler and transfers it from the pick zone via conveyor.
- The stapler — along with hundreds of thousands of other individual picks — arrives at a sortation point, where it is transported and diverted to an order consolidation or pack-out area.
- Once packed, the ordered stapler is sorted again, this time by outbound destination.
- After leaving the facility, the order may go through several more sorts at local carrier and regional destination hubs through the last-mile carrier.
Other considerations
Further complicating the situation is the limited available labor to manually handle e-commerce’s increased order volumes, as well as rising transportation and freight costs, and customers’ expectations for free shipping.
Add in the need for DCs to store a broader assortment of products than ever before to satisfy the expectations of customers, and it becomes evident that floor space is at a premium. DC operators must find ways to maximize the number of chutes in a fixed amount of space in order to increase order consolidation and outbound sortation potential.
The end game of sortation also changes as the smaller order quantities of e-commerce dictate a greater focus on sorting items to containers, rather than dock doors, to accommodate new sortation strategies like zone skipping.
Automation is key to staying competitive
With so much of the e-commerce customer experience depending on accurate, efficient order fulfillment and fast, free delivery, businesses must invest in DC operations to keep up — while remaining both competitive and profitable. As a result, the demand for automated sortation solutions to help consolidate, separate and route the proliferation of individual orders at maximum throughput rates is booming — a trend that’s likely to continue for some time.
Find more information in our white paper, Buried By E-Commerce? Expand Sortation Capacity to Keep Up. And, Subscribe to our blog to watch for the next installment in this series, which will cover strategies for selecting the right automation solution.
To subscribe to our blog and receive exclusive communications and updates from Honeywell Intelligrated, click here.
Let's Connect!
Sign up to receive exclusive communications from Honeywell including product updates, technical information, new offerings, events and news, surveys, special offers, and related topics via telephone, email, and other forms of electronic communication.
Copyright © 2025 Honeywell International Inc
Maximum File Size
Maximum Files Exceeded
Due to inactivity you will be logged out in 000 seconds.
Maximum File Size
Maximum Files Exceeded
You cannot access this page as this product is not available in your country.