-
Global
-
Africa
-
Asia Pacific
-
Europe
-
Latin America
-
Middle East
-
North America
- |
- Partners
- |
-
Currency:Localize your Content
You can set your preferred currency for this account.
Choose a Currency
Currency- CHOOSE YOUR CURRENCY
Update Currency
Changing Currency will cause your current cart to be deleted. Click OK to proceed.
To Keep your current cart, click CLOSE and then save your cart before changing currency.
-
Select Account
Switching accounts will update the product catalog available to you. When switching accounts, your current cart will not move to the new account you select. Your current cart will be available if you log back into this account again.
Account# Account Name City Zip/Post Code CANCELPROCEEDMy Account
-
Support
- View All Productivity Solutions
- Warranties
- Patents
- Global Locations
- Technical Support
- Discontinued Products
- Quality Program and Environmental Compliance
- Return Material Authorization (RMA)
- Legal Documents
- Product Certification
- Software Downloads
- Cyber Security Notifications
- Case Studies and Success Stories
- View All Sensing Solutions
- Sales Contact Form
- Technical Support
- Certificates
- eCOM Portal
- Distributor Inventory
- Return Material Authorization (Test & Measurement)
- Return Material Authorization (Citytech)
- Return Material Authorization (EnviteC)
- Legal Documents
- Intelligent Life Care
- Return Material Authorization (ILC)
-
Global
-
Africa
-
Asia Pacific
-
Europe
-
Latin America
-
Middle East
-
North America
- |
- Partners
- |
You are browsing the product catalog for
You are viewing the overview and resources for
- News & Events
- Featured stories
- Harness the Power of Real-time Asset Monitoring Programs
Harness the Power of Real-time Asset Monitoring Programs
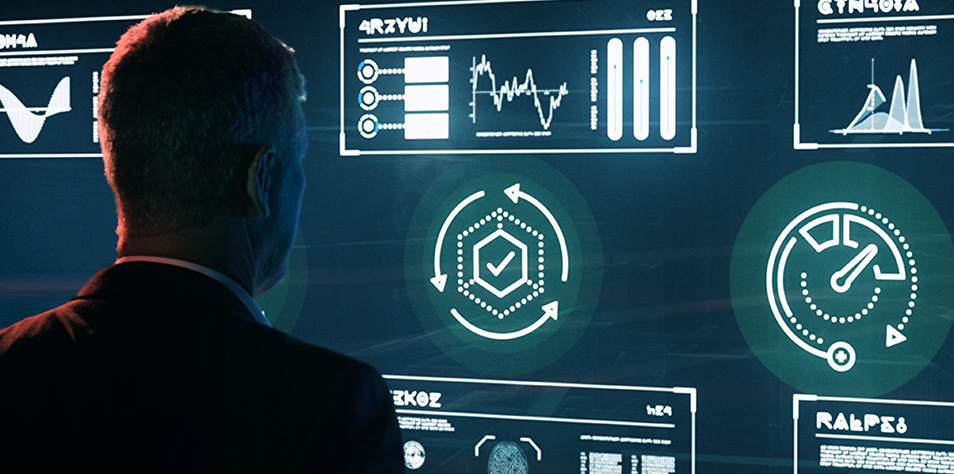
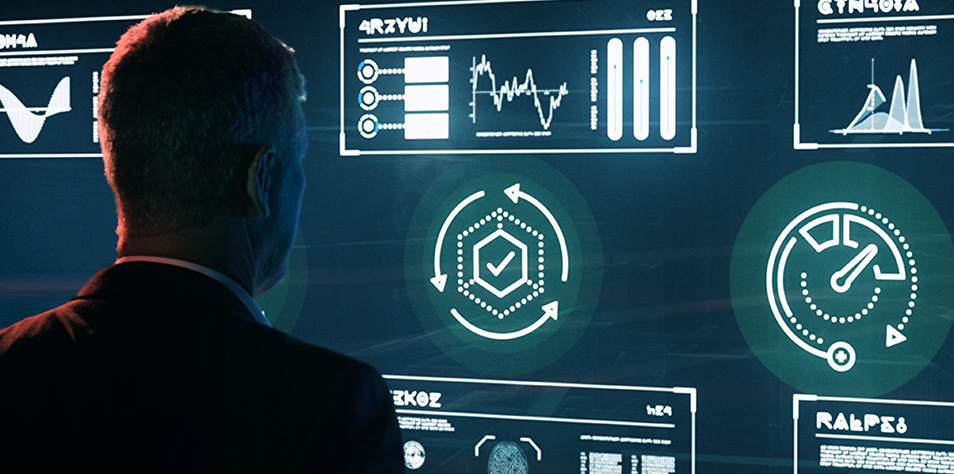
Harness the Power of Real-time Asset Monitoring Programs
William Leet
December 7, 2020
Real-time asset monitoring programs — or the ability to connect machinery and warehouse automation systems via the industrial internet of things (IIoT) technologies — allow distribution center (DC) operators to reduce unplanned downtime, increase throughput, and maximize facility utilization. Effective implementation of these programs helps to reduce e-commerce order fulfillment complexities.
Compared to other industries, the distribution and fulfillment (D&F) sector is relatively new to the concept of connecting assets. For example, in the maintenance and energy sector, IIoT-driven predictive maintenance programs have delivered a 10:1 return on investment (ROI).[1] While IIoT benefits are well-known in other industries, only 2 percent of executives identified supply chain performance as a focus of their digital strategies.[2] However, that may soon change, as 70 percent of material handling executives consider investments in IIoT technologies (aka Industry 4.0) a top priority.[3]
Understanding the True Cost of Downtime
Although many DC operators are beginning to recognize the potential of IIoT to increase their operational efficiency, most underestimate the true cost of unplanned downtime. Consider the following industry statistics:
- 90 percent of companies say their top priorities are durability, reliability and uptime.[4]
- 80 percent of businesses are unable to accurately estimate their downtime rates.[5]
- Many underestimate downtime costs by 200–300 percent.[6]
When you really stop to consider the implications, downtime creates a domino effect of issues in the DC — from depleted inventories, lost production and missed customer service level agreements (SLAs) to recovery costs, equipment stress and wasted labor resources — not to mention the potential for losing customer loyalty and weakening your brand reputation.
Predictive Maintenance Programs Prove Their Value
In a 2010 U.S. Department of Energy (DOE) study of operations, maintenance and energy professionals, IIoT-driven predictive maintenance programs were proven to improve processes and reduce operational costs significantly:
- 25–30% reduction in maintenance costs
- 70–75% elimination of equipment breakdowns
- 35–40% decrease in downtime
- 20–25% increase in production[7]
Performance improvements of this magnitude should appeal to DC operators and enterprise managers who recognize the need to fundamentally shift how they run their fulfillment operations.
From Control System Data to Condition Sensors
Leading retailers are implementing pilot programs that tap into the vast amounts of available data from machine control systems where hundreds of thousands of data points can be extracted. Software and analytics tools are needed to filter out the noise and deliver historical trends and actionable insights.
By itself, this step can provide tremendous value and address a variety of performance issues:
- Resolve conveyor faults that create repetitive jams.
- Uncover scanner timing and read rate issues to prevent unnecessary recirculation.
- Log the duration of downtime in pick stations, merges, transfers and recirculation loops.
But by adding temperature and vibration sensors, DC operators can implement a true real-time asset monitoring program — one that’s capable of providing deeper insights into system performance and even predicting equipment and system failures before they occur. In this scenario, smart analytics software utilize machine-learning algorithms and artificial intelligence (AI) to detect and track deviations from performance baselines. Operators then receive alerts when parameters exceed defined temperature and vibration thresholds.
Download our infographic, Implementing a Real-time DC Asset Monitoring Program, to learn more about harnessing the power of IIoT in your DC.
To subscribe to our blog and receive exclusive communications and updates from Honeywell Intelligrated, click here.
Source
_____________________
[1] https://www.energy.gov/sites/prod/files/2013/10/f3/omguide_complete.pdf
[2] Enis Gezgin, Xin Huang, Prakash Samal and Ildefonso Silva, “Digital transformation: Raising supply-chain performance to new levels,” McKinsey and Company, November 2017, https://www.mckinsey.com/business-functions/operations/our-insights/digital-transformation-raising-supply-chain-performance-to-new-levels (accessed March 5, 2020).
[3] Subu Narayanan and Michael Coxon, “It’s the last IT/OT mile that matters in avoiding Industry 4.0’s pilot purgatory,” October 8, 2018, https://www.mckinsey.com/business-functions/operations/our-insights/operations-blog/its-the-last-it-ot-mile-that-matters-in-avoiding-industry-40s-pilot-purgatory (accessed March 5, 2020).
[4] Bridget McCrea, “Annual Warehouse and Distribution Center Automation Survey: More automation, please,” Modern Materials Handling, May 15, 2019, https://www.mmh.com/article/annual_warehouse_and_distribution_center_automation_survey_more_automation (accessed March 5, 2020).
[5] Graham Immerman, “The Real Cost of Downtime in Manufacturing,” MachineMetrics, May 8, 2018, https://www.machinemetrics.com/blog/the-real-cost-of-downtime-in-manufacturing (accessed March 5, 2020).
[6] Industry Insights, “True Cost of Factory Downtime: How Downtime Affects Productivity,” Simutech, https://www.simutechmultimedia.com/the-true-cost-of-downtime-what-you-dont-know-about-how-downtime-affects-your-productivity (accessed March 5, 2020).
[7] https://www.energy.gov/sites/prod/files/2013/10/f3/omguide_complete.pdf
Let's Connect!
Sign up to receive exclusive communications from Honeywell including product updates, technical information, new offerings, events and news, surveys, special offers, and related topics via telephone, email, and other forms of electronic communication.
Copyright © 2025 Honeywell International Inc
Maximum File Size
Maximum Files Exceeded
Due to inactivity you will be logged out in 000 seconds.
Maximum File Size
Maximum Files Exceeded
You cannot access this page as this product is not available in your country.