-
Global
-
Africa
-
Asia Pacific
-
Europe
-
Latin America
-
Middle East
-
North America
- |
- Partners
- |
-
Currency:Localize your Content
You can set your preferred currency for this account.
Choose a Currency
Currency- CHOOSE YOUR CURRENCY
Update Currency
Changing Currency will cause your current cart to be deleted. Click OK to proceed.
To Keep your current cart, click CLOSE and then save your cart before changing currency.
-
Select Account
Switching accounts will update the product catalog available to you. When switching accounts, your current cart will not move to the new account you select. Your current cart will be available if you log back into this account again.
Account# Account Name City Zip/Post Code CANCELPROCEEDMy Account
-
Support
- View All Productivity Solutions
- Warranties
- Patents
- Global Locations
- Technical Support
- Discontinued Products
- Quality Program and Environmental Compliance
- Return Material Authorization (RMA)
- Legal Documents
- Product Certification
- Software Downloads
- Cyber Security Notifications
- Case Studies and Success Stories
- View All Sensing Solutions
- Sales Contact Form
- Technical Support
- Certificates
- eCOM Portal
- Distributor Inventory
- Return Material Authorization (Test & Measurement)
- Return Material Authorization (Citytech)
- Return Material Authorization (EnviteC)
- Legal Documents
- Intelligent Life Care
- Return Material Authorization (ILC)
-
Global
-
Africa
-
Asia Pacific
-
Europe
-
Latin America
-
Middle East
-
North America
- |
- Partners
- |
You are browsing the product catalog for
You are viewing the overview and resources for
- News & Events
- Featured stories
- Honeywell Operational Intelligence Configuration Analytics Module Enhances Worker Insights and Efficiencies
Honeywell Operational Intelligence Configuration Analytics Module Enhances Worker Insights and Efficiencies
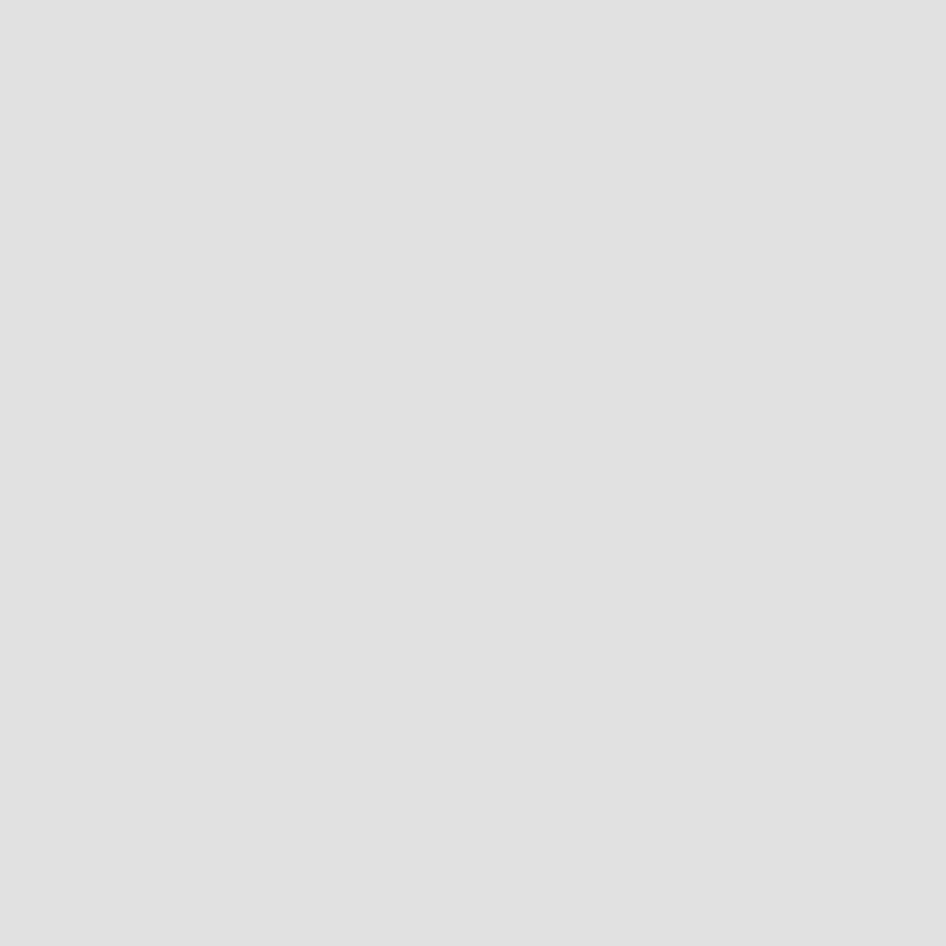
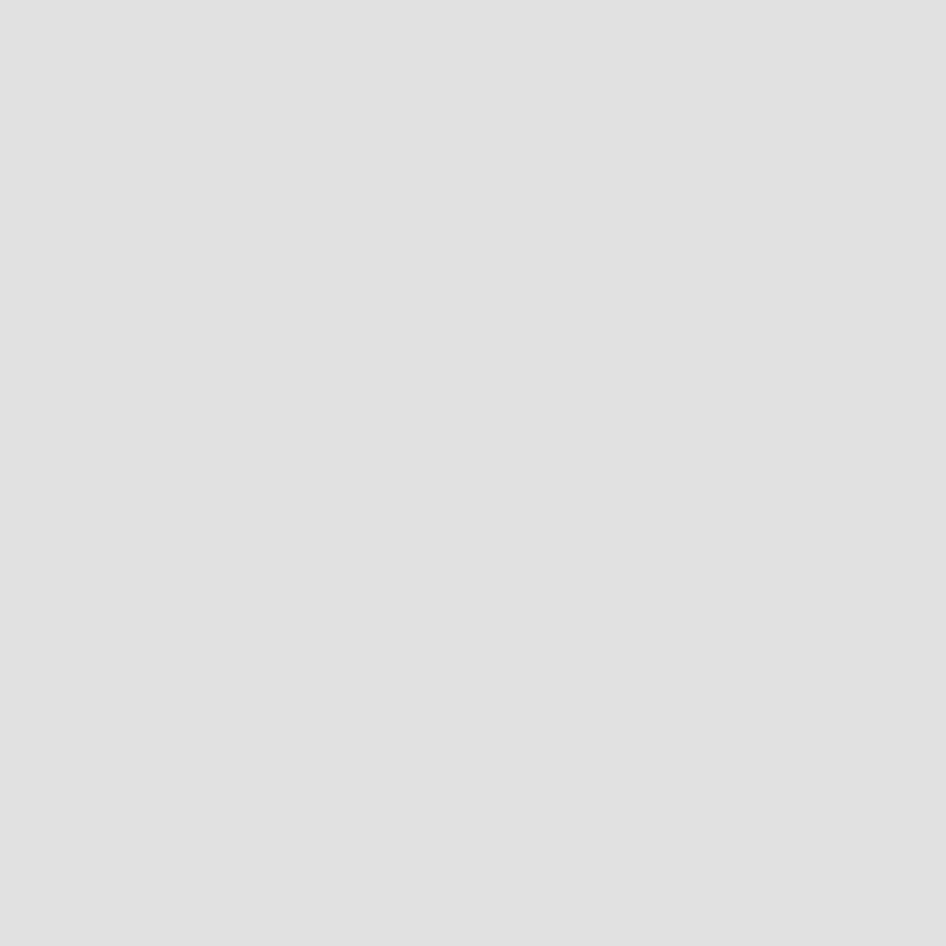
Honeywell Operational Intelligence Configuration Analytics Module Enhances Worker Insights and Efficiencies
Barry J. Ewell
February 5, 2020
This is a four-part series looking at how Honeywell is revolutionizing IT asset and service management with Operational Intelligence. Operational Intelligence includes four modules to give you a robust tool to manage and optimize assets across your locations throughout the operational asset lifecycle. These include: 1) Service Management, 2) Performance Management, 3) Configuration Management, and 4) Worker Performance. Part 4 will introduce the Worker Performance module.
Across the supply chain, organizations deploy fleets of mobile devices made up of assets from multiple manufacturers – ruggedized mobile computers, tablets, barcode scanners, and printers. Each device comes with its own operating system, software, contracts, agreements, and repair processes that must be carefully managed. Many of these devices can collect rich telemetry and event data that can be used to provide actionable insights into how devices are used, how to decrease operational costs, and how to improve productivity. Sadly, organizations are challenged in accessing these insights because they are using separate tools and aggregating the information with spreadsheets and in-house developed tools.
Operational Intelligence Overview
Honeywell Operational Intelligence solves these needs and problems by providing IT and site leaders and services providers a centralized, cloud-based platform to manage the complete lifecycle of their assets. Operational Intelligence aggregates lifecycle and workflow information into a single flexible tool to capture data, enforce processes, and provide visibility across the entire device workflow for your heterogeneous environment. Operational Intelligence is also capable of communicating with Honeywell devices to gather deep metric and telemetry data; provide software, configuration, OS, and firmware updates to the devices; and track indoor device location.
Operational Intelligence is a powerful analysis software engine that provides dashboards to support your troubleshooting efforts. At Honeywell, we believe in the power of intelligence and design products to give you more of it. Over the last several years, Honeywell has been systematically adding powerful “self-analyzing” toolsets to all of our hardware products. These embedded tools are capable of methodically capturing hundreds of performance data points from our devices as they are being used in your operations. When this data is compiled and analyzed, it opens amazing insights into many problems common to AIDC technology users.
Operational Intelligence includes four modules to give you a robust tool to manage and optimize assets across your locations throughout the operational asset lifecycle. These include:
- Service Management: As a vendor-agnostic solution, systematically standardize, manage, and optimize the process of servicing your IT assets.
- Performance Management: Track, analyze, and report on the operational performance of your IT assets. Remotely download software and configurations.
- Configuration Management: Reduce time spent on individual device updates and security risks by keeping devices automatically updated.
- Worker Performance: Analyze worker performance and workflow efficiencies by tracking device and application use.
A Closer Look at Worker Performance Module
Operational Intelligence analyzes worker performance and workflow efficiencies by tracking device and application use. With the Worker Performance module, you gain access to:
- Workforce Insights. Monitor, compare, and score your workforce through device usage and productivity to identify opportunities for continuous improvement.
- Worker Time Studies. Gain real-time metrics for each step of your job workflow to identify bottlenecks and create opportunities for process improvement.
- AI-Based Optimization. Machine learning on IT asset usage patterns to optimize performance.
Some of the module highlights include:
- Automatically collects device data and associates it to individual workers
- Data analysis tools for measuring worker behavior
- Supports creating worker time studies
- Artificial Intelligence–based analysis of processes and worker productivity
Workforce time studies drive workflow efficiency
Operational Intelligence allows your organization to collect a constant stream of device data that provides full visibility into workflow patterns. The main object of time study is to determine the proper time required to complete the job. Because the sample size can include every device, it makes root cause analysis easier and more accurate than sparse measurements and the potential for continuous improvement is immense. You can take worker skills into consideration, from veterans to new hires, and look for opportunities to improve process and provide one-on-one training across the team.
Accurate data leads to increased worker efficiency because workers are asked to follow correct methods, use proper tools, and eliminate wasteful motions. It helps in simplifying existing operations by laying the best sequence of essential operations, which leads to economy in labor and a reduction in fatigue.
AI-based optimization for continuous improvement
Operational Intelligence machine learning provides critical information to help managers make more informed business decisions. For example, machine learning helps with:
- Predictive Maintenance. Helps in the creation of highly efficient predictive maintenance plans. Following such predictive maintenance plans will minimize the chances of unexpected failures, thereby reducing unnecessary preventive maintenance activities.
- Workforce Planning. Machine learning can analyze warehouse processes and optimize the sending, receiving, storing, picking, and management of individual products.
Workforce insights guide solutions to everyday needs
Looking for bottlenecks is a key ingredient to creating new efficiencies in your operations. A powerful tool for finding hidden slowdowns in your systems is to analyze your workforce’s location as they travel during the day picking orders and replenishing inventory. This is not a search for how much time your workers are in the breakroom, but rather a study of time and motion. Have you inadvertently created artificial traffic jams in your own operations? Operational Intelligence is the perfect tool to give you that intelligence.
Honeywell mobile computers have the unique ability to transmit location information both indoors and outdoors while they are being used throughout the day. The Operational Intelligence software engine captures that information in real-time and provides both dashboards and views of the data with eye-opening discoveries of where your workers are at any moment in time and how they traveled there. It’s similar in concept to a Real-Time Location System (RTLS) without the extra expense and support of yet another unique set of hardware infrastructure.
With Operational Intelligence locationing, a zone mapping procedure is first completed that creates a virtual grid of your facilities travel areas that detects when a Honeywell mobile computer has entered. Typically mapping these small zones in a large warehouse requires an hour walking the facility with a Honeywell mobile computer running a simple mapping agent. Once the zones have been uniquely identified, it is as simple as letting your workforce do what they normally do each day processing your customer’s orders, loading and unloading trucks, and replenishing your inventory.
The value of this approach to data collection is that there are no limits to the combinations of events you can explore and analyze. For example, the following is a sample list of questions you can now get answers to with Operational Intelligence that likely have been mysteries to you in the past.
- Which zones in my facility do my workers spend the most time in? You can even explore this question down to certain worker types and even individual workers. For example, I want to compare my picking forklift operators versus replenish forklift operators.
- Where are my traffic jams throughout the day? Which zones or grouping of zones show multiple workers in close proximity at the same time? Should we duplicate certain SKU locations in different areas because I can now see how many forklifts are trying to get to the same area at the same time.
- When I look at time, are my workers focused in one area of my facilities at one time and in other areas during other hours? For example, I want to see a heat map of where my people are every 15 minutes throughout the day.
- Warehouse slotting issues. By looking at how many zones each worker is traveling per transaction, you will get powerful insight into the efficiency of your inventory locations as it relates to worker travel.
- Seasonality impacts on your workloads and workflows. Since Honeywell Operational Intelligence is running all the time, you can easily analyze seasonal impacts on your processes and workers.
- Accident, damaged inventory, and injury investigations. While these events are rare as they should be, it is always a priority to look for the cause of issues when they do arise. By using Operational Intelligence to maintain zone location information history, you can get new information about the location and travel direction of workers at the time of any adverse event.
- A common problem with handheld mobile computers is workers losing them somewhere in your facility. Because Operational Intelligence is tracking each device’s location as it is being used, it is easy to know the location that the device is currently reporting or the location it was in when it last communicated on your network.
The simplicity of the Operational Intelligence approach to gathering insights is that you are already collecting data with the equipment in relation to barcode scanning. You enable the Operational Intelligence software to collect data, you know where your workers are, and the answers to your questions are revealed.
Conclusion
Honeywell Operational Intelligence is a cloud-based platform to manage the complete lifecycle of your assets. Operational Intelligence aggregates lifecycle and workflow information into a single, flexible tool to capture data, enforce processes, and provide visibility across the entire device workflow for your heterogeneous environment. Operational Intelligence is also capable of communicating with Honeywell devices to gather deep metric and telemetry data; provide software, configuration, OS, and firmware updates to the devices; and track indoor device location.
Operational Intelligence is a powerful analysis software engine that provides dashboards to support your troubleshooting efforts. At Honeywell, we believe in the power of intelligence and design products to give you more of it. That’s why we have been systematically adding powerful “self-analyzing” toolsets to all of our hardware products. These embedded tools we call “Edge Intelligence” are capable of methodically capturing hundreds of performance data points from our devices as they are being used in your operations. When this data is compiled and analyzed, it opens amazing insights into many problems common to AIDC technology users.
Operational Intelligence delivers results that have been previously unattainable with any one solution. These include:
- Assign assets to unique departments and locations for accountability.
- Receive real-time status updates on assets returned for repair to reduce help desk status calls.
- Define self-service checklists to follow prior to RMA issuance to reduce NFF returns and create accountability.
- Simplify the RMA process by consolidating and standardizing the lifecycle management processes by digitizing your service and repair workflow, ensuring global consistency and simplifying the process for all employees.
- Control corporate shipping methods through automated integration to understand and reduce shipping costs.
- Minimize size of spare pools, reducing upfront capital expenditure.
- Properly allocate devices to locations and departments based on usage to improve productivity.
- Track connected mobile devices in operation and unconnected mobile devices through their service repair workflow and back into operations or spare pools to reduce lost devices.
- Reduce wasteful spend on unnecessary equipment purchases by analyzing device utilization and alerting supervisors to underutilized devices that could be relocated.
- Receive device lifecycle analytics to make informed decisions to refresh devices, spot reoccurring device issues, and identify individual problem devices.
- Track and locate devices to minimize lost devices.
- Minimize productivity loss with real-time notifications for printer jams and out-of-media and ink issues.
- Increase device uptime and availability by providing predictive notifications about pending maintenance needs or consumable replacements such as batteries, labels, printheads, and more.
- Track dropped and high-impact events on the devices to understand the care and use of the devices.
- Understand battery usage to drive behavior changes to extend the lifespan of batteries.
- Receive recommendations and make informed decisions regarding battery replacements based on health.
- Device OS and firmware update capabilities and versioning tracking so you can have visibility into security vulnerabilities and can patch devices to enforce compliance and mitigate risk.
- Integrated dashboards, KPIs, alerts, and notifications to provide device usage and productivity degradation events to improve utilization and productivity.
If you want to learn how Operational Intelligence can help you better manage your mobile assets, contact Honeywell today at https://www.honeywellaidc.com/solutions/workflow/operational-intelligence.
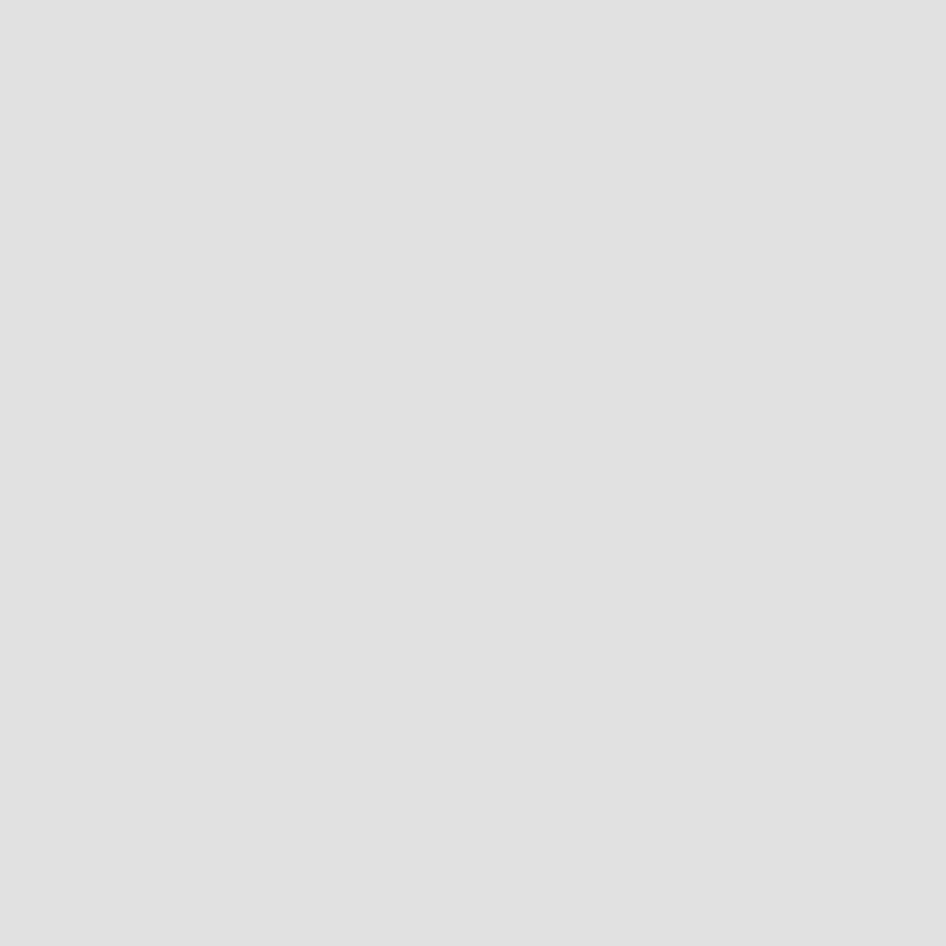
Barry J. Ewell is a Senior Content Marketing Communications Specialist for Honeywell Industrial Automation. He has been researching and writing on supply chain topics since 1991.
Let's Connect!
Sign up to receive exclusive communications from Honeywell including product updates, technical information, new offerings, events and news, surveys, special offers, and related topics via telephone, email, and other forms of electronic communication.
Copyright © 2025 Honeywell International Inc
Maximum File Size
Maximum Files Exceeded
Due to inactivity you will be logged out in 000 seconds.
Maximum File Size
Maximum Files Exceeded
You cannot access this page as this product is not available in your country.