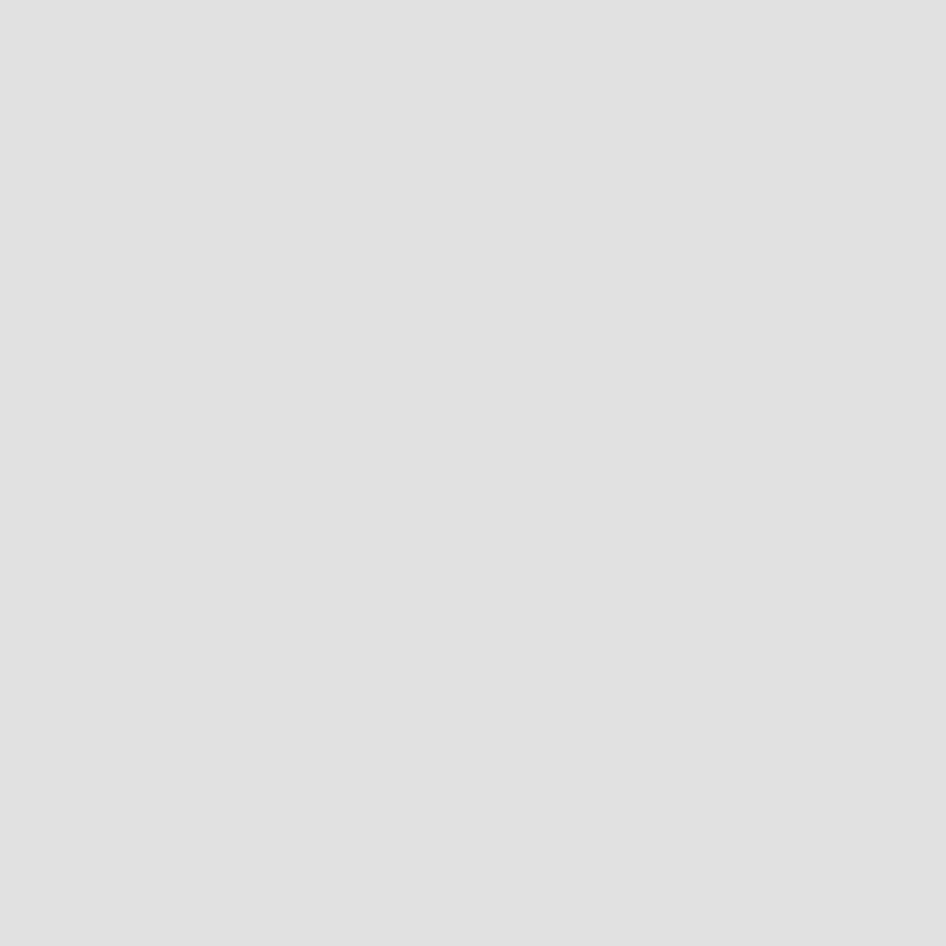
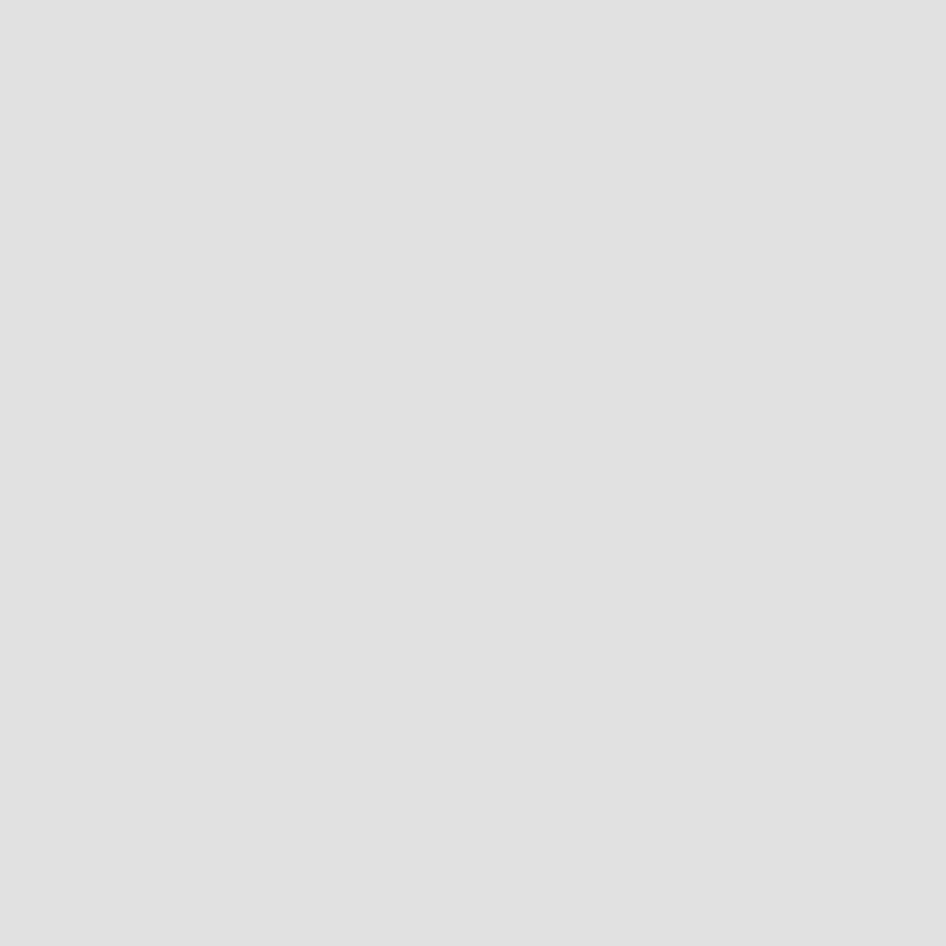
Honeywell PX940 Industrial Printer: 41 FAQs about ANSI Grading and Verification Support
The PX940 family of high-performance industrial printers with integrated label verification provides customers with error-free printing. The Honeywell PX940 is the first-of-its-kind industrial printer to include a barcode verifier in one device.
This is part-one of a three-part FAQ series to provide you an in-depth overview of the Honeywell PX940 printer to help understand barcode printers for your industrial printer needs. The series includes the following:
- Part 1: 41 FAQs about ANSI Grading and Verification Support
- Part 2: 25 FAQs about Printing Support, Service and Maintenance
- Part 3: 22 FAQs about Media, Ribbon Support and User Interface
In this article we will focus on answering 41 questions related to
The printer has been developed for customers that are subjected to fines levied for non-compliance to regulatory standards and additional costs triggered by corrective actions and returned shipments due to unreadable or unscannable barcodes. With integrated verification technology, barcodes are error-free and 100% accurate every time. Labels that do not meet a predetermined ANSI grades are retracted, voided and a new label is printed.
Some of the key benefits of the Honeywell PX940 include:
- Integrated Label Verification Technology provides customers with error-free printing and addresses fines, chargebacks, and lawsuits associated with poor/difficult-to-scan labels.
- Precision Printing with registration up to +/-0.2 mm addresses miniaturization driving printing on smaller labels.
- Operation Intelligence provides customers with predictive analytics and addresses printer health and maintenance, cost reduction and increased efficiency, historical data for audits and compliance with regulatory requirements.
- The PX940 consists of verification application software plus Edge Intelligence which provides customers with error-free printing, predictive analytics and cost savings of up to $15K per printer.
Honeywell PX940 ANSI Grading
- What is the difference between ISO 15415/15416 and read/no-read?
ISO 15415/15416 is a standard that describes how barcodes can be given a level of quality indicating how well the barcode can be scanned by a barcode scanner. This is also known as ANSI grading.
Read/no-read is a simpler version of verification which validates that the barcode is readable by most commercial barcode scanners.
- How does ANSI Grading (ISO 15415/15416) work in the printer?
For 1D barcodes, the printer will capture an image of the barcode and analyze 10 evenly distributed lines of the barcode. Parameters analyzed include contrast between black and white, whether the barcode is overheated or underheated, and whether any defects exist in the barcode. The final grade of the barcode is the average analysis of the 10 lines.
For 2D barcodes, similar parameters will be analyzed and graded accordingly, by creating a grid pattern over the barcode and analyzing it.
- I see ANSI grading listed in both numeric & alphabetic values, what is the difference?
The international standard specifies a numeric basis for expressing quality grades, however, both numeric & alphabetic characters are used interchangeably. Equivalence of numeric and alphabetic quality grades:
Numeric Grade
Alphabetic Grade
3.5 to 4.0
A
2.5 to <3.5
B
1.5 to <2.5
C
.5 to <0.5
D
0.0 to <0.5
F
- What is hardware aperture?
Hardware aperture defines the physical optical aperture of the verifier. As the verifier is not a camera, the aperture size is derived by a specific proprietary manufacturing procedure.
- What is software aperture?
Software aperture is an emulation of the effective aperture size used during verification.
- How is barcode size defined and what is barcode X dimension?
The size of a barcode is typically defined as ‘5 mil’, ’10 mil’, etc. which is referring to the X dimension of the barcode. The X dimension of the barcode is the size of the smallest element in the barcode.
- For 2D barcode the X dimension is the height and width of one module.
- For 1D barcode the X dimension is the width of the narrowest bar.
- How does the printer select which software aperture to use?
When printer is configured to automatic aperture size (recommended), the software aperture size is based on the barcode size that is under verification. This is the recommended aperture size for different barcode sizes as per ISO 15416:
X Dimension mm
Aperture Diameter mm
Reference Number
0.100 < X < 0.180
0.075
03
0.280 < X < 0.330
0.125
05
0.350 < X < 0.635
0.250
10
0.635 < X
0.500
20
- What does it mean to have a requirement of 2.8/05/660 for a label grading?
In this example, 2.8 is the overall grade of the barcode, 05 is the aperture size in mil, and 660 is the peak light wavelength in nanometers. The PX940V light source is 660nm laser diode and is controlled to fall on the center of the inspection area at an angle of 45 degrees to its plane.
- Can I select a different software aperture size?
- Example: At a lower software aperture value, the defect value will increase as the printer will see the barcode in higher focus and not necessarily the same way a scanner will see it.
- Note: If overriding the aperture size then all barcodes in the label will use that aperture size, independent of the barcode size verified.
Yes, as long the user knows which aperture to use and what the impact is on the verification. Typically, application standards will dictate if there is a specific aperture size needed, but most of the time the automatic selection is used.
Honeywell PX940 Verification Support
- How accurate are the verification results?
- Barcode verification is conforming to ISO/IEC 15146-2016 for Linear (1D) barcode verification.
- Barcode verification is conforming to ISO/IEC 15415-2011 for 2-Dimensional (2D) barcode verification.
- Is the verifier certified under ISO15426-1 and ISO15426-2?
Currently the verifier is not certified under these ISO standards, but this is being considered for future releases.
- Which languages are supporting the new verification function?
The PX940 supports all direct printing languages; Direct Protocol, IPL, DPL, and ZSim2. We also support verification in Fingerprint smart printing applications. C# does not support verification.
- Which barcode symbologies are supported for verification and read/no-read?
These 1D and 2D barcodes are supported by the verifier: Code39, Hibc39, Code128, Hibc128, ISBT128, Ean-8, Ean-13, Ean-128, UPC-A, UPC-E, Interleaved 2 of 5 (ITF-14) Datamatrix, ISBT Datamatrix.
- Do I need to use any special solvent and material to clean the verifier?
It is recommended to use a lint-free soft cloth that is soaked with isopropyl alcohol. Let the alcohol dry before using the verifier after cleaning.
- Will the PX940 print on small labels?
The PX940 has registration of +/-0.2 mm. The trend toward miniaturization requires printing on smaller and smaller labels. The PX940 will print accurately on small labels, edge to edge with little error tolerance. Suited for Transportation & Logistics, Pharmaceuticals & Healthcare, Shipping & Distribution Centers, Industrial Manufacturing, Automotive Parts Suppliers, and applications that are regulated and require high precision and error-free printing.
- What is the smallest barcode that can be printed and verified?
The smallest 1D barcode size supported is 10 mil (X dimension). The smallest 2D barcode size supported is 15 mil (X dimension). There is no upper limit to the size of barcode that can be graded.
- How many barcodes can I have on my label to be verified?
Maximum 32 barcodes are supported. More barcodes may slow down the printing.
- What is the maximum speed I can use for verification?
The maximum speed for verification and read/no-read is 8 ips (200mm/s) for 203 and 300 dpi. The maximum speed for 600 dpi is 6 ips (150mm/s).
- Is voiding of labels supported in all print modes?
Voiding is supported in all print modes. In peel off mode there may be certain media type or media length that could cause jam or get stuck if voiding.
- My barcode is still readable after voiding it, how do I make sure it is not readable?
There is a configuration to change the pattern to ‘Grid’ which will ensure the barcode cannot be read after voiding. Do note that with high heat settings the ribbon may break or cause media jam if using the ‘Grid’ pattern.
- I have read that the PX940 will automatically void good labels when voiding a failed label, why?
This is because the printer is ensuring the order of the labels is the same as what is sent to the printer. The user can change the printer configuration to “Non-Sequential Voiding” to only void the failed label, however, the labels may not be printed in the order they are sent. This is supported from FW version H10.15.017868 onwards.
- What is the maximum label length for voiding?
The maximum retract distance is 12 inches on demand mode and 6 inches on batch mode. There is no restriction in the firmware. If the customer is using labels that require longer retract then there may be issues with ribbon wrinkle or printing on the next label.
- Will there be any impact to the verification result if I pull the media?
Yes, the media should not be interfered with during printing or the result may be incorrect.
- Can I send barcodes as graphics print job?
No, only barcodes sent as printer commands are supported for verification. Graphics barcodes will be ignored.
- Will the verifier grade my pre-printed barcode?
No, only barcodes sent as printer language commands i are supported for verification. Pre-printed barcode will be ignored.
- Does the PX940 support verification of inverted barcodes (white on black)?
No, currently inverted barcodes cannot be graded by the verifier. If there is an inverted barcode in the label then the verifier will attempt to grade it and fail the barcode, and thus fail the entire label.
- My application requires a higher grade than recommended ISO standard, can I change it?
Yes, there is a ‘Passing Grade’ configuration that can be used to set the passing threshold.
- What does grade 3.5 mean on my label which has multiple barcodes?
The label grade is the lowest grade of any of the barcodes on the label. The grade for label as well as detailed information about each barcode grade can be viewed on the printer web page.
- Can the verifier support OCR and OCV (Optical Character Recognition and Verification)?
No, only barcode grading is supported.
- Can I do full image content verification on my labels?
No, only barcode grading is supported.
- Does the verifier check data content such as GS1?
The verifier will grade the quality of the barcode and make sure data content is the same as the one sent to the printer, however, it does not confirm GS1 data content.
- Can I choose which barcodes on my label should be graded?
No, the printer will grade all barcodes on the label that are within specification (symbology and size), unsupported barcodes will be ignored. The passing grade for all barcodes will be the same, by default 1.5 (C), as per ISO standard.
- Where can I find the result and image from my last printed label?
The latest report and image can be found on the printer internal web page, using a browser and the IP address of the printer.
- How can I export the verification results to my computer?
With FW version H10.15.017 or higher verification results can be exported in XML or CSV formats. Multiple options are available depending on customer requirements:
- Exported to a USB thumb drive using the front panel UI on the printer.
- Exported to a USB thumb drive automatically (XML only).
- Exported manually from the printer web page (CSV summary or XML individual report).
- Exported automatically via FTP (XML or CSV).
- Exported using Verifier Integration Interface (VII).
- Is the verification result data automatically deleted once the memory fills up?
No, the user must regularly delete the data manually from the printer web page and restart the printer. From FW version H10.15.017868 onwards, it is not required to restart the printer after deleting the data.
- How do I integrate this printer/verifier solution to my host software?
There will soon be an interface available to integrate the verification report and printer behavior to host software. This interface will be called Verifier Integration Interface (VII).
- When will the Verifier Integration Interface (VII) be available?
It has been available since August 2019.
- While printing label media in ladder mode and verifying 1D barcodes I am getting too many failures but the barcodes look perfect upon visual inspection?
- Can a rectangular Datamatrix be verified?
Yes
- Is PX940 able to verify 1D and 2D barcodes at all rotation?
Yes
- What is the minimum height of a barcode that can be verified?
1.2mm
This could be due to some unwanted media movement occurring when the media gap between labels rolls over the platen roller. This may affect the verifier system that results in low ANSI grading. The verification will improve by moving the ladder barcode more than 32 mm away from the trailing edge of the label, or by rotating the image 180 degrees.
Find out more about the high-performance Honeywell PX940 industrial printer with integrated label verification technology – and how it can help you eliminate the risk and costs of bad labels.
Contact Honeywell Solutions Experts today! Call 1-800-934-3163.